摘 要:隨著半導(dǎo)體功率器件的使用環(huán)境和性能要求越來越高,器件散熱能力要求也隨之提高。器件散熱問題導(dǎo)致的失效占了總失效的一半以上,而雙面散熱封裝是提高器件散熱能力的有效途徑之一。因此,本文針對大功率模塊的雙面散熱封裝,利用有限元計算的仿真手段進(jìn)行了模塊整體的熱設(shè)計與特性研究。首先,分析了熱對流系數(shù)對模塊最高溫度的影響; 其次,對比分析了單雙面散熱以及不同形狀散熱片對散熱的影響; 另外,對比分析不同焊料及金屬厚度對散熱的影響; 最后,對優(yōu)化模型進(jìn)行了熱應(yīng)力分析,從而完成模塊的熱設(shè)計與熱管理。研究結(jié)果對雙面封裝的熱設(shè)計具有一定參考意義。
關(guān)鍵詞:功率器件; 雙面散熱; 溫度; 熱應(yīng)力; 形變
關(guān)鍵詞:功率器件; 雙面散熱; 溫度; 熱應(yīng)力; 形變;
1引言
目前,大功率器件尤其是第三代半導(dǎo)體功率器件的主要問題仍然是熱引起的失效問題,其70%以上的失效是由于熱引起的。因此,散熱也是大功率器件發(fā)展中一直研究和優(yōu)化的熱點。在器件封裝中,由于封裝材料不同,其封裝材料的熱膨脹系數(shù)的差異,導(dǎo)致器件出現(xiàn)不同程度的形變和熱應(yīng)力積累,最終導(dǎo)致如焊線脫離、焊料分層、塑封體開裂分層等失效問題; 另外,溫度的升高也會降低器件的性能,帶來電流的載荷能力和柵壓影響等問題。
大功率模塊的封裝形式主要還是以單面封裝為主,許多研究者為此做了多方面研究,推動了功率器件的發(fā)展。但是,隨著對器件散熱能力要求的提高,特別是第三代半導(dǎo)體極高的功率密度,單面散熱封裝有著一定的局限性。因此,雙面散熱封裝應(yīng)運而生,其散熱能力將提升30% ~ 50%。Brinkfeldt等人通過計算仿真對比了一款SiC模塊,相同條件下,單面封裝的最高溫度為141 ℃,而雙面封裝為119 ℃。寧圃奇等人則通過針刺型散熱片來進(jìn)一步提高雙面散熱封裝的散熱能力。Cova等人通過試驗和仿真,極大優(yōu)化了雙面散熱模塊的散熱能力,使芯片溫度在80 ℃以下。陸國權(quán)等人研究了雙面SiC模塊應(yīng)力緩沖層形狀、厚度和焊層面積對模塊各層材料的受力與變形的影響規(guī)律。美國弗吉利亞理工大學(xué)通過優(yōu)化模塊布局,研制了高溫、大功率SiC結(jié)晶型場效應(yīng)晶體管功率模塊。美國北卡州立大學(xué)將驅(qū)動芯片集成到功率模塊內(nèi)部,實現(xiàn)了開關(guān)頻率高達(dá)3. 38 MHz的SiC功率模塊。美國田納西大學(xué)和橡樹林國家實驗室,針對電動汽車應(yīng)用,研究了集成水冷、雙面散熱的SiC功率模塊。日本豐田公司采用雙面散熱封裝技術(shù),研制了高功率密度的SiC車用電機控制器。雖然許多學(xué)者對雙面散熱封裝模塊進(jìn)行了一些研究,但是其研究還略顯匱乏,有待全面而深入的持續(xù)研究。而在散熱特性的研究上,仿真計算無疑擁有著較大的經(jīng)濟和時間成本優(yōu)勢。
本文對一款SiC雙面散熱封裝模塊,利用熱仿真對模塊的整體熱設(shè)計進(jìn)行了全面仿真分析。首先分析了熱對流系數(shù)對模塊最高溫度的影響; 其次對比分析了單雙面散熱特性以及不同形狀散熱片對散熱的影響; 另外,對比分析不同焊料及金屬厚度對散熱的影響; 最后,對優(yōu)化模型進(jìn)行了熱應(yīng)力分析。本文的研究結(jié)果對雙面封裝的熱設(shè)計具有重要的參考意義。
1仿真模型
本文中,以雙面散熱模塊為研究對象,圖1為計算模型的結(jié)構(gòu)示意圖。如圖所示,上下兩層為直接覆銅陶瓷(DBC,Direct Bonding Copper) 基板,通過芯片與墊塊相連,實現(xiàn)整體的電氣互聯(lián)。模型的尺寸為39 mm × 33 mm,母排尺寸為18 mm × 10 mm,引腳尺寸為16 mm × 1 mm。金屬氧化物半導(dǎo)體場效應(yīng)晶體管(MOSFET) 的芯片尺寸為:5. 46 mm × 4. 37 mm,而DBC基板陶瓷層厚度為0. 63 mm,其他部件如焊料和墊塊初步尺寸為5. 46 mm × 4. 37 mm,本文將對這些參數(shù)做出優(yōu)化。
有限元計算過程中,模型各部分的溫度分布并不均勻,溫差較大,同時形變差異也不相同。因此,對應(yīng)力應(yīng)變變化劇烈的焊料層、芯片、墊塊和DBC基板相對應(yīng)的銅層周圍進(jìn)行局部細(xì)化的網(wǎng)格劃分,采用矩形映射單元,以提高計算精度。模型采用0. 2 mm的網(wǎng)格間距劃分網(wǎng)格,網(wǎng)格總數(shù)量為622430,焊料層、芯 片、墊 塊 和DBC基板相對應(yīng)的銅層的網(wǎng)格數(shù)為172050。
當(dāng)物體內(nèi)的溫度分布只依賴于一個空間坐標(biāo),且溫度分布不隨時間而變時,熱量只沿溫度降低的一個方向傳遞,稱為一維定態(tài)熱傳導(dǎo),導(dǎo)熱現(xiàn)象的規(guī)律被總結(jié)為傅里葉定律[13]。此時的熱傳導(dǎo)可用式(1) 描述:
φ= -λAdt/dx (1)
式中:φ為熱量;A為垂直于熱流方向的截面積;dt/dx為溫度t在x方向的變化率;λ為導(dǎo)熱系數(shù); 負(fù)號表示熱傳遞方向指向溫度降低的方向。
對流換熱過程所傳遞的能量,可用牛頓冷卻方程來計算,其數(shù)學(xué)式(2) 為:
φ=hcA(tw-tf) (2)
式中:hc為換熱系數(shù),表示單位面積溫差為1 ℃時所傳遞的熱量;A為固體壁面換熱面積;tf為流體溫度;tw為固體壁面溫度。其中對流換熱系數(shù)hc在熱傳導(dǎo)過程中尤為重要,其大小反映對流換熱的強弱,物理意義是: 當(dāng)流體與固體表面之間的溫度差為1 K時,1 m × 1 m壁面面積在每秒所能傳遞的熱量。
本文對應(yīng)力場有限元模型計算做出以下簡化:
1) 忽略自蔓延薄膜燃燒過程中可能產(chǎn)生的斷裂和自蔓延薄膜內(nèi)的納米層的熔化流動情況,不考慮流動以及溫度變化導(dǎo)致的自蔓延薄膜物性參數(shù)的改變;
2) 本模型主要分析焊料層應(yīng)力應(yīng)變的變化,不考慮焊料的流動和形狀的改變,同時不考慮焊料的密度、楊氏模量和泊松比等物性參數(shù)隨溫度的改變;
3) 假設(shè)芯片和DBC基板互連之前平整無翹曲,不考慮硅片和基板材料的各向異性。
表1給出了模塊各部分材料屬性參數(shù)。
2結(jié)果與分析
本文中模型利用ANSYS /Workbench有限元仿真軟件進(jìn)行溫度與熱應(yīng)力仿真計算,并做出以下假設(shè):
環(huán)境溫度設(shè)為22 ℃;
芯片的發(fā)熱為有效熱源;
器件各焊料均無空洞等缺陷且焊接良好;
散熱器的散熱面有效熱對流系數(shù)為1000 W/(m2·K) ,其余與空氣發(fā)生熱量交換的等效熱對流系數(shù)為5 W/(m2·K)。
2.1確定網(wǎng)格密度
一般情況下,過大的網(wǎng)格密度會影響計算精度,造成結(jié)果的誤差分析,而過小的網(wǎng)格密度則會消耗巨大的計算資源,效率低下。因此,為了提高模型的計算精度,同時節(jié)省計算資源,提高效率,本文利用“路徑法”首先確定了所計算模型的網(wǎng)格密度,對比不同網(wǎng)格密度下距離特定點不同距離的應(yīng)力分布,即以某一應(yīng)力集中點為基準(zhǔn)點,將基準(zhǔn)點外5 mm距離線段劃分成50段,從外往應(yīng)力基準(zhǔn)點開始對比其應(yīng)力分布。如圖2所示,本文分別比較了0. 1 mm、0. 2 mm和0. 4 mm的網(wǎng)格密度下特定點的應(yīng)力分布,可以看到,0. 4 mm的應(yīng)力值和0. 1 mm、0. 2 mm的應(yīng)力值有較大的差別,而0. 1 mm、0. 2 mm的應(yīng)力值基本相同。因此,本文采用0. 2 mm的網(wǎng)格密度。
2.2單雙面散熱對比
雙面封裝所帶來最直觀的優(yōu)勢是可以采用雙面散熱,其具有更多的換熱面積,使單位時間內(nèi)通過傳熱面積的熱量增多,溫度下降更明顯。如圖3所示,在熱對流系數(shù)為1000 W/(m2·K) 環(huán)境下,模擬計算單、雙面封裝的溫度場,由圖可知,單面封裝的最高結(jié)溫為153. 34 ℃,雙面封裝的最高結(jié)溫為95. 95 ℃,雙面封裝的最高結(jié)溫比單面封裝的最高結(jié)溫減少57 ℃,散熱能力提高37. 4%。雙面封裝所帶來的優(yōu)勢不僅僅是熱對流換熱面積的增大,同時熱傳導(dǎo)面積也有增大,可以看到雙面封裝熱傳導(dǎo)面積的增加最直觀的效果就是為器件提供了多一條豎直方向散熱途徑。
另外,本文分析了熱對流系數(shù)對封裝散熱的影響。選用帶有雙面散熱器模型,熱對流系數(shù)與模型結(jié)溫( 最高溫度點) 的關(guān)系如圖4所示。從圖中可知,在熱對流系數(shù)初始增加階段,結(jié)溫急劇下降。在對流系數(shù)150 W/(m2·K) 以上時,溫度下降趨勢變緩,說明熱對流的增大,對溫度的影響效果已經(jīng)不大。因 此,在器件散熱方面,除了熱對流系數(shù)的影響,特別是在熱對流系數(shù)影響緩慢的階段,對其他散熱影響因素的優(yōu)化顯得尤為重要,所以本文在下面部分對散熱器、基板、焊料等進(jìn)行了仿真優(yōu)化。
2.3不同散熱器的對比
針對市面較為常見的針式與肋片式兩種散熱器進(jìn)行比較,基于本實驗的模型與環(huán)境探討最佳散熱器效果。
2.3.1肋片式散熱器
肋片式散熱器具有加工相對簡單的優(yōu)勢,肋片可以做得更薄,可通過提高散熱片密度增加散熱面積,從而有效地提高散熱能力。因此在對比不同散熱器的同時,也探究了相同厚度不同翅數(shù)的散熱器對器件散熱的影響。在本實驗中分析了3個不同翅數(shù)的散熱器,其翅數(shù)分別為19、25、30。計算結(jié)果如圖5所 示,從左到右散熱器翅數(shù)分別為19、25、30的散熱模型,其最大結(jié)溫分別為100. 38 ℃、95. 95 ℃以及93. 779 ℃,從19片的翅數(shù)增至25片時,最大結(jié)溫可降低4. 41%,而從25片翅數(shù)增至30片時,最大結(jié)溫僅降低2. 26%。這說明當(dāng)散熱器的片數(shù)密度過密時并不利于散熱。
2.3.2針式散熱器
針式散熱器相對肋片式散熱器加工較難,但在相同尺寸下針式散熱器的傳熱面積更大,在理論上同等尺寸的針式散熱器的散熱效果會更佳。同樣在本實驗中也做出3個同直徑不同針數(shù)的散熱器的散熱效果對比。如圖6所示,從左到右散熱器的pin針排數(shù)分別為19、25、30的散熱模型,其最大結(jié)溫分別為121. 69 ℃、108. 52 ℃以及103. 85 ℃,隨著pin針數(shù)量的增加,傳熱面積隨之增加。當(dāng)散熱器pin針的排數(shù)由19增加至25時,最大結(jié)溫下降10. 8%。當(dāng)散熱器pin針的排數(shù)由25增加至30時,最高結(jié)溫下降4. 3%,針式散熱器與肋片式散熱器具有相同的性質(zhì),當(dāng)散熱pin針過密時會使散熱器的散熱能力下降。
通過兩種散熱器結(jié)果分析對比可知( 如圖5、圖6) ,在同樣的溫度環(huán)境下,針式散熱器的溫度計算結(jié)果會比肋片式散熱器的溫度計算結(jié)果偏高,故基于本實驗該模型與溫度環(huán)境是用肋片式的散熱器效果更佳。
2.4不同基板材料的熱散熱性能對比
陶瓷基板因擁有著優(yōu)良的電絕緣性、高導(dǎo)熱性以及優(yōu)異的附著強度而廣泛應(yīng)用于電子半導(dǎo)體器件當(dāng)中,而本實驗中的器件中陶瓷基板直接與散熱器連接,在整個器件當(dāng)中,陶瓷基板不僅起到載流作用,同時也是散熱的重要結(jié)構(gòu)之一,陶瓷基板直接將芯片的熱量傳給散熱器,減少熱量經(jīng)過途徑,減少熱阻,使器件能夠及時散熱。然而不同的陶瓷基板的陶瓷材料不同,其導(dǎo)熱性能也差異較大。以下將比較市面常用的Al2O3、AlN、Si3N4這三種陶瓷基板材料性能。由 于BeO是有毒物質(zhì),在工業(yè)上無法廣泛應(yīng)用,所以并不對其做出比較。
從表2中可知導(dǎo)熱性能最佳為AlN陶瓷基板,而熱膨脹系數(shù)最小為Si3N4陶瓷基板,同時該材料的基板也是綜合性能最佳的,但成本偏高,而Al2O3陶瓷基板工藝較為成熟,成本較低。以這3種陶瓷基板為變量,探究其對器件散熱的影響,計算結(jié)果如圖7。
從左到右分別為Al2O3、AlN、Si3N4這3種陶瓷基板的計算模型,其中溫度計算結(jié)果最高的是Al2O3陶瓷基板,其最高結(jié)溫為137. 05 ℃,最低的是AlN陶瓷基板,其最高結(jié)溫為95. 95 ℃,需要特殊說明的是由于Si3N4材料的力學(xué)性能較好,所以該陶瓷基板成品的陶瓷厚度只有其他基板的一半,以此來提高基板的散熱能力,正如計算結(jié)果圖7所示,其最高結(jié)溫與AlN相差僅有3 ℃。
2.5不同銀漿厚度對器件最高結(jié)溫的影響
在本實驗中的器件有著三層納米銀漿,分別連接著下基板、芯片、鉬片緩沖層、上基板,如圖1所示。在器件的制樣中采用的是納米銀漿焊料,故本實驗計算同樣采用納米銀,將納米銀漿厚度作為自變量,最高結(jié)溫作為因變量,厚度范圍在0. 01 ~ 0. 1 mm,結(jié)果如表3所列。
隨著銀漿厚度的減小,器件的最高結(jié)溫整體趨勢也在緩慢地下降,但效果并不明顯,可以發(fā)現(xiàn)0. 1 mm的銀漿厚度與0. 01 mm銀漿厚度的器件最高結(jié)溫相差不超過2 ℃,由熱量在內(nèi)部熱傳導(dǎo)時的熱阻公式(3) 來描述:
R=L /(λA) (3)
式中:R為熱阻;L為銀漿厚度;λ為導(dǎo)熱系數(shù);A為銀漿面積。當(dāng)銀漿厚度增加,熱阻變大,溫度隨之上升,但由于銀漿相對器件整體的熱阻過小,并無法使溫度波動太大,當(dāng)銀漿厚度為0. 01 mm時,R0. 01僅為0. 004 K/W。綜上銀漿厚度對器件的最高結(jié)溫影響很小,無法作為器件對銀漿厚度選擇的重要依據(jù),銀漿厚度除了對器件溫度有影響之外,對連接物體的應(yīng)力同樣也有影響。
2.6熱應(yīng)力分析
2.6.1不同銀漿厚度對熱應(yīng)力的影響
銀漿厚度對器件的最高結(jié)溫的影響并不明顯,然而對銀漿的連接物體應(yīng)力的影響尚未明確,需要進(jìn)一步仿真計算。為排除其他因素對連接物體的熱應(yīng)力計算結(jié)果分析造成影響,在計算前對模型進(jìn)行簡化,使誤差減少。本次計算的銀漿同樣采用納米銀漿,銀漿厚度范圍仍在0. 01 ~ 0. 1 mm。為簡化計算,假設(shè)器件處于150 ℃的高溫環(huán)境下。
將納米銀漿厚度作為自變量,其他重點關(guān)注部位的熱應(yīng)力作為因變量,計算結(jié)果如表4所示。
從表4可以看出,銀漿厚度對芯片、基板連接部位的應(yīng)力影響較大,而對基板非連接部位的應(yīng)力計算結(jié)果并不影響,這說明了該模型基板非連接部位與銀漿厚度的無關(guān)性,從而可以減少計算結(jié)果所帶來的誤差,保證計算數(shù)據(jù)的嚴(yán)謹(jǐn)性。而重點關(guān)注的連接部位的應(yīng)力則是隨銀漿厚度的增加而減少,結(jié)果如圖8所 示。上、下基板的連接部位的應(yīng)力隨銀漿厚度增大而減小的趨勢比較緩慢,芯片與銀漿兩個部位的應(yīng)力下降幅度最為明顯。當(dāng)銀漿厚度從0. 01 mm增至0. 1mm時,芯片與銀漿的最大等效應(yīng)力分別可下降56%和64%,這充分說明銀漿厚度對應(yīng)力的影響比較大。同時,銀漿厚度對器件整體形變的影響可以忽略不計。
綜上所述,銀漿厚度對應(yīng)力的影響可成為器件選擇銀漿厚度的重要依據(jù)。理論上銀漿厚度在實驗計算的范圍當(dāng)中選取0. 1 mm可達(dá)到最佳優(yōu)化效果,但考慮芯片的厚度以及爬漿過高會導(dǎo)致短路,綜合器件的制樣情況最終選取0. 08 mm的銀漿厚度。
2.6.2金屬墊塊結(jié)構(gòu)對熱應(yīng)力的影響
銀漿厚度對器件的最高結(jié)溫的影響并不明顯,然而對銀漿的連接物體應(yīng)力的影響尚未明確,需要進(jìn)一步仿真計算。為排除其他因素對連接物體的熱應(yīng)力計算結(jié)果分析造成影響,在計算前對模型進(jìn)行簡化,使誤差減少。本次計算的銀漿同樣采用納米銀漿,銀漿厚度范圍仍在0. 01 ~ 0. 1 mm。為簡化計算,假設(shè)器件處于150 ℃的高溫環(huán)境下。
器件可通過雙面封裝增加散熱通道與換熱面積,有效提高散熱效率,使器件向更高功率與密度的方向發(fā)展,但同時雙面封裝結(jié)構(gòu)必須承受更高的熱應(yīng)力。因此在雙面封裝結(jié)構(gòu)中采用鉬、鎢等金屬墊塊作為緩沖層結(jié)構(gòu)代替鍵合引線,優(yōu)化結(jié)構(gòu)應(yīng)力。本實驗通過無緩沖層、單層緩沖層、雙層緩沖層3個模型去探究緩沖層對應(yīng)力的影響,模型結(jié)構(gòu)見圖9,從左到右分別為無緩沖層、單層緩沖層、雙層緩沖層3個模型,其中無緩沖層模型與雙緩沖層模型都是上下對稱結(jié)構(gòu)。
為避免其他因素造成對熱應(yīng)力計算結(jié)果的影響,對這3個模型進(jìn)行簡化。采用芯片發(fā)熱的穩(wěn)態(tài)結(jié)果作為器件的溫度計算條件,溫度條件計算所得結(jié)果:無金屬緩沖層模型計算得最高結(jié)溫為79. 36 ℃,單金屬緩沖層模型計算得最高結(jié)溫為90. 5 ℃,而雙金屬緩沖層模型計算得最高結(jié)溫為108. 18 ℃。
雙層金屬墊塊模型的整體形變?nèi)鐖D10所示,上下基板拱起的趨勢較大,而器件的上下對稱面位置形變量較小。該變形勢必會對起連接作用的銀漿造成較大的拉應(yīng)力,當(dāng)器件的芯片越靠近陶瓷基板,芯片也會受到較大的應(yīng)力,當(dāng)芯片處于對稱面,這時芯片的熱應(yīng)力越會較小,銀漿與芯片的計算結(jié)果見表5。
圖?11給出了無金屬墊塊結(jié)構(gòu)、單層金屬墊塊結(jié)構(gòu)和雙層金屬墊塊結(jié)構(gòu)與芯片或金屬墊塊接觸的DBC銅層接觸面的應(yīng)力分布情況。其中圖11(a) 為無金屬墊塊結(jié)構(gòu)的基板銅層應(yīng)力分布,圖11(b) 為雙層金屬墊塊結(jié)構(gòu)的基板銅層應(yīng)力分布,由于無金屬層和雙金屬層的模型結(jié)構(gòu)是上下對稱的,所以上下基板銅層接觸面的應(yīng)力情況是一致的; 圖11(c) 為單金屬墊塊上銅層應(yīng)力分布圖,即為與芯片接觸的銅層應(yīng)力分布,圖11(d) 為單金屬墊塊下銅層應(yīng)力分布圖,即為與金屬墊塊接觸的銅層應(yīng)力分布,因為單金屬層的模型結(jié)構(gòu)并不對稱,所以上下基板的應(yīng)力情況并不一致。
從圖11中可以看到,無金屬墊塊的基板接觸面銅層最大等效應(yīng)力為98. 819 MPa,雙金屬墊塊的基板接觸面銅層最大等效應(yīng)力為80. 767 MPa。結(jié)合上述有無金屬墊塊模型溫度變化情況,雙金屬墊塊結(jié)構(gòu)的溫度條件比無金屬墊塊結(jié)構(gòu)高36. 3%,但其基板接觸面銅層的熱應(yīng)力結(jié)果卻比無緩沖層結(jié)構(gòu)低18. 3%。
單金屬層的上、下基板接觸面銅層最大等效應(yīng)力分別為109. 23 MPa、69. 51 MPa,這兩者數(shù)值相差較大,這是芯片與鉬片兩者的熱膨脹系數(shù)、溫度差異等原因所造成的。與非對稱結(jié)構(gòu)相比較,上下對稱結(jié)構(gòu)的熱應(yīng)力實現(xiàn)相互抵消,使得器件整體應(yīng)力偏小,然而由于器件電氣線路等原因是無法實現(xiàn)完全對稱結(jié)構(gòu)的,但該結(jié)構(gòu)具有優(yōu)化器件應(yīng)力的指導(dǎo)意義。
LED燈珠受芯片波長、熒光膠配比及均勻度的影響,不僅僅是不同批次、甚至同批次封裝的燈珠特殊顯色指數(shù)R9分布都會存在較大的波動。在LED燈珠色容差、壓降、亮度、Ra等光電參數(shù)一致性很高的情況下,特殊顯色指數(shù)R9的差異會影響顏色一致性,差異值取決于不同照明、背光產(chǎn)品的要求。普通照明產(chǎn)品如對顏色一致性有要求,在保證其他參數(shù)一致性的基礎(chǔ)上,特殊顯色指數(shù)R9的差值范圍應(yīng)該保持在15以內(nèi),對顏色一致性要求較高的商照或者背光產(chǎn)品,R9的差異建議不要超過10。所以對于R9的標(biāo)準(zhǔn)不應(yīng)僅限于R9大于0,應(yīng)根據(jù)產(chǎn)品應(yīng)用的實際效果對R9的范圍進(jìn)行界定。
3結(jié)論
本文主要研究的是SiC雙面封裝模塊的散熱能力提升及其熱應(yīng)力優(yōu)化,對于模塊的散熱,旨在通過提高模塊的熱對流系數(shù)、散熱器模型的優(yōu)化以及器件材料的選擇等種種方法以降低器件的芯片結(jié)溫,在器件熱應(yīng)力方面,針對應(yīng)力集中現(xiàn)象比較嚴(yán)重的焊料層,以及器件緩沖層金屬結(jié)構(gòu)進(jìn)行優(yōu)化,從而使器件的應(yīng)力有所下降。本文研究結(jié)論主要有:
(1) 基于本器件的計算環(huán)境,熱對流系數(shù)為1000 W/(m2·K) 是一個較大的值,雖肋片式散熱器換熱比針式散熱器差,但在導(dǎo)熱方面肋片式效果更佳,故在本研究中肋片式散熱器效果更好。
(2) 對于基板材料的選擇,無論是從散熱還是應(yīng)力上,做薄后的Si3N4基板是最佳的選擇,但考慮成本問題,AlN基板也能滿足散熱和應(yīng)力要求。
(3) 在探究銀漿厚度對應(yīng)力的影響中,發(fā)現(xiàn)隨銀漿厚度增加,與銀漿接觸部位包括銀漿的應(yīng)力值都有所下降,綜合考慮爬漿導(dǎo)致芯片短路,故最終選取銀漿厚度為0. 08 mm為佳。
(4) 對于金屬層結(jié)構(gòu)的優(yōu)化,發(fā)現(xiàn)當(dāng)器件的整體結(jié)構(gòu)上下對稱時,可減少基板18. 3%的熱應(yīng)力,上下對稱結(jié)構(gòu)可使部分的內(nèi)應(yīng)力相互抵消,從而減少應(yīng)力。
通過本文對功率器件熱設(shè)計的研究優(yōu)化,進(jìn)而提高功率器件的可靠性,但是在散熱器與應(yīng)力研究上可以更深入??傮w上,本文為功率器件的熱設(shè)計提供了一定的參考,具有一定的指導(dǎo)作用。
來源:《中國照明電器》期刊-第2期
作者:楊 寧1,2 ,詹洪桂2 ,謝健興2 ,王冠玉2 ,陳曉儀2 ,張 超2
1. 華南理工大學(xué)機械與汽車工程學(xué)院
2. 佛山市國星光電股份有限公司
-
模塊
+關(guān)注
關(guān)注
7文章
2707瀏覽量
47476 -
材料
+關(guān)注
關(guān)注
3文章
1228瀏覽量
27291
發(fā)布評論請先 登錄
相關(guān)推薦
Tips:大功率電源PCB繪制注意事項
一種氮化硼納米片增強的高導(dǎo)熱復(fù)合材料
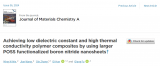
高導(dǎo)熱高絕緣低介電材料 | 氮化硼散熱膜
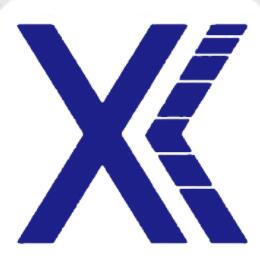
導(dǎo)熱界面材料對降低接觸熱阻的影響分析
IGBT主動散熱和被動散熱 | 氮化硼高導(dǎo)熱絕緣片
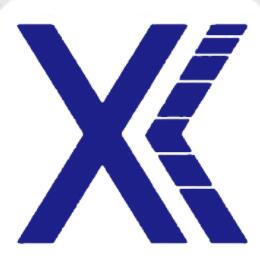
散熱第一步是導(dǎo)熱
5G芯片超薄絕緣導(dǎo)熱透波氮化硼散熱片
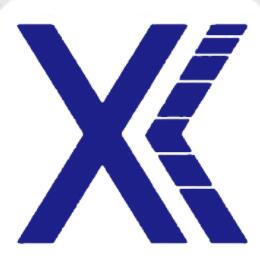
二維氮化硼高效聲子橋效應(yīng)讓快充不再過熱
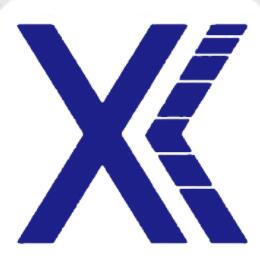
5G通信散熱的VC及絕緣導(dǎo)熱透波氮化硼材料
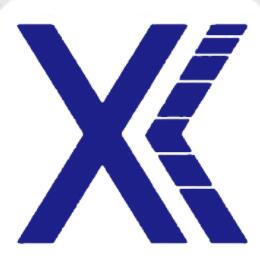
導(dǎo)熱吸波材料在光模塊的應(yīng)用
高導(dǎo)熱絕緣透波超薄氮化硼均熱膜
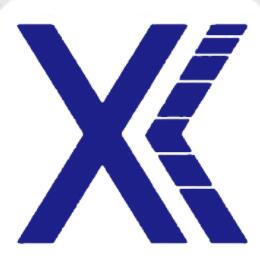
評論