陳力 楊曉鋒 于大全
(廈門(mén)大學(xué)電子科學(xué)與技術(shù)學(xué)院 廈門(mén)云天半導(dǎo)體科技有限公司)
摘要:
近年來(lái),隨著5G、可穿戴設(shè)備、智能手機(jī)、汽車(chē)電子、人工智能等新興領(lǐng)域蓬勃興起,集成電路應(yīng)用正向著多元化應(yīng)用方向發(fā)展,先進(jìn)三維封裝技術(shù)也逐漸成為實(shí)現(xiàn)電子產(chǎn)品小型化、輕質(zhì)化、多功能化的重要手段。玻璃通孔(TGV)互連技術(shù)具有高頻電學(xué)特性?xún)?yōu)異、成本低、工藝流程簡(jiǎn)單、機(jī)械穩(wěn)定性強(qiáng)等應(yīng)用優(yōu)勢(shì),在射頻器件、微機(jī)電系統(tǒng)(MEMS)封裝、光電系統(tǒng)集成等領(lǐng)域具有廣泛的應(yīng)用前景。綜述了國(guó)內(nèi)外高密度玻璃通孔制作、金屬填充、表面高密度布線(xiàn)的研究進(jìn)展,對(duì)玻璃通孔技術(shù)特點(diǎn)及其應(yīng)用進(jìn)行了總結(jié)。
1引言
隨著智能手機(jī)、物聯(lián)網(wǎng)、汽車(chē)電子、高性能計(jì)算、5G、人工智能等新興領(lǐng)域的蓬勃發(fā)展,隨之出現(xiàn)的各種新的應(yīng)用對(duì)先進(jìn)封裝提出更高的要求。硅基轉(zhuǎn)接板2.5D集成技術(shù)作為先進(jìn)系統(tǒng)集成技術(shù),近年來(lái)得到了迅猛的發(fā)展。但硅基轉(zhuǎn)接板存在兩個(gè)主要問(wèn)題:1)成本高,硅通孔(TSV)制作采用硅刻蝕工藝,隨后硅通孔需要氧化絕緣層、薄晶圓的拿持等技術(shù);2)電學(xué)性能差,硅材料屬于半導(dǎo)體材料,傳輸線(xiàn)在傳輸信號(hào)時(shí),信號(hào)與襯底材料有較強(qiáng)的電磁耦合效應(yīng),襯底中產(chǎn)生渦流現(xiàn)象,造成信號(hào)完整性較差(插損、串?dāng)_等)[1]。作為一種可能替代硅基轉(zhuǎn)接板的材料,玻璃通孔(TGV)轉(zhuǎn)接板因其眾多優(yōu)勢(shì)正在成為國(guó)內(nèi)外半導(dǎo)體企業(yè)和科研院所的研究熱點(diǎn)[2-5]。
與硅基轉(zhuǎn)接板相比,玻璃轉(zhuǎn)接板的優(yōu)勢(shì)主要體現(xiàn)在以下幾個(gè)方面。
1)低成本:受益于大尺寸超薄面板玻璃易于獲取,以及不需要沉積絕緣層,玻璃轉(zhuǎn)接板的制作成本大約只有硅基轉(zhuǎn)接板的1/8;2)優(yōu)良的高頻電學(xué)特性:玻璃材料是一種絕緣體材料,介電常數(shù)只有硅材料的1/3左右,損耗因子比硅材料低2~3個(gè)數(shù)量級(jí),使得襯底損耗和寄生效應(yīng)大大減小,可以有效提高傳輸信號(hào)的完整性;3)大尺寸超薄玻璃襯底易于獲?。嚎祵帯⑿裣踝右约靶ぬ氐炔A?a target="_blank">廠商可以量產(chǎn)超大尺寸(大于2 m×2 m)和超?。ㄐ∮?0 μm)的面板玻璃以及超薄柔性玻璃材料;4)工藝流程簡(jiǎn)單:不需要在襯底表面及TGV內(nèi)壁沉積絕緣層,且超薄轉(zhuǎn)接板不需要二次減薄;5)機(jī)械穩(wěn)定性強(qiáng):當(dāng)轉(zhuǎn)接板厚度小于100 μm時(shí),翹曲依然較?。?)應(yīng)用領(lǐng)域廣泛:除了在高頻領(lǐng)域有良好應(yīng)用前景之外,透明、氣密性好、耐腐蝕等性能優(yōu)點(diǎn)使玻璃通孔在光電系統(tǒng)集成領(lǐng)域[6]、MEMS封裝領(lǐng)域有巨大的應(yīng)用前景。
目前玻璃轉(zhuǎn)接板技術(shù)已得到了國(guó)內(nèi)外的廣泛關(guān)注,大批科研人員針對(duì)TGV玻璃轉(zhuǎn)接板開(kāi)展了大量的相關(guān)工藝技術(shù)[3-5]、器件集成技術(shù)的研究工作,如高密度TGV制作、TGV的金屬填充、表面高密度金屬布線(xiàn),玻璃基集成波導(dǎo)、芯片間光互聯(lián)、濾波器、射頻模塊等[6-8]。本文對(duì)TGV成孔技術(shù)、TGV金屬填充技術(shù)、TGV高密度布線(xiàn)技術(shù)的國(guó)內(nèi)外研究現(xiàn)狀進(jìn)行了綜述。
2玻璃通孔成孔技術(shù)
制約玻璃通孔技術(shù)發(fā)展的主要困難之一就是玻璃通孔成孔技術(shù),需要滿(mǎn)足高速、高精度、窄節(jié)距、側(cè)壁光滑、垂直度好以及低成本等一系列要求。多年以來(lái),許多研究工作都在致力于研發(fā)低成本、快速可規(guī)?;慨a(chǎn)的成孔技術(shù)。下面將簡(jiǎn)要介紹近年來(lái)常用的玻璃通孔成孔技術(shù),同時(shí)分析其優(yōu)缺點(diǎn)。
2.1噴砂法
首先需要在玻璃基板上制作一層復(fù)合掩模,然后以制備的復(fù)合掩模為基礎(chǔ),采用干粉噴砂工藝對(duì)玻璃晶片進(jìn)行蝕刻[9-11]??紤]到蝕刻效率和寬高比,可在玻璃晶片的一側(cè)先蝕刻一次;隨后,在玻璃晶片的另一側(cè)也采用上述同樣的工藝步驟進(jìn)行蝕刻。在兩次噴砂蝕刻過(guò)程中,必須保證對(duì)中形成完整的通孔。通過(guò)噴砂法制作的玻璃通孔結(jié)構(gòu)如圖1所示。從圖1可以明顯看出,噴砂法制作的通孔非常粗糙;該方法只能制作孔徑較大(>200 μm)、間距較大的玻璃通孔;該工藝中使用的沙粒直徑為20~50 μm,如此大的顆粒會(huì)對(duì)玻璃表面以及孔的側(cè)壁造成封裝系統(tǒng)無(wú)法接受的損傷。
2.2光敏玻璃法
通過(guò)紫外線(xiàn)照射定義圖形,光敏玻璃中摻雜有一定濃度的三價(jià)鈰離子(Ce 3+)和銀離子(Ag +),經(jīng)過(guò)一定波長(zhǎng)的紫外線(xiàn)曝光后,三價(jià)鈰離子釋放一個(gè)電子變成四價(jià)的鈰離子(Ce 4+),銀離子與釋放的電子結(jié)合形成銀原子,該區(qū)域形成變性區(qū),主要反應(yīng)式如下:
曝光后再經(jīng)過(guò)后續(xù)的高溫?zé)Y(jié)工藝,經(jīng)過(guò)紫外光照射的區(qū)域材料屬性轉(zhuǎn)變?yōu)樘沾刹牧?,最后通過(guò)氫氟酸腐蝕去除陶瓷材料。詳細(xì)工藝流程如圖2所示?;诠饷舨AУ腡GV制作方法,其優(yōu)勢(shì)在于采用高刻蝕速率的濕法腐蝕實(shí)現(xiàn)各向異性刻蝕,可獲得高密度、高深寬比的TGV。圖3為該工藝制作的TGV陣列顯微圖像。但是該技術(shù)也存在兩個(gè)問(wèn)題:1)價(jià)格昂貴,包括光敏玻璃本身的材料價(jià)格和工藝制程價(jià)格;2)對(duì)于不同尺寸的圖形,尤其是盲孔或者盲槽的刻蝕,由于腐蝕速率不同,會(huì)造成圖形定義精度差別較大[12-13];同時(shí),由于需要高溫處理,會(huì)造成玻璃在半固化狀態(tài)下移動(dòng),造成結(jié)構(gòu)偏移。
2.3聚焦放電法
聚焦放電主要包括兩個(gè)步驟:1)將玻璃放在兩個(gè)電極之間,通過(guò)控制放電對(duì)玻璃局部區(qū)域進(jìn)行放電熔融;2)通過(guò)焦耳熱使玻璃內(nèi)部產(chǎn)生高應(yīng)力,引起內(nèi)部高壓和介電擊穿。圖4表示聚焦放電制作TGV的示意圖。上述步驟可以在不到1 μs的時(shí)間內(nèi)就完成100~500 μm厚的玻璃通孔制備。該方法可以制備最小孔徑為20 μm、深寬比5~8的玻璃通孔。且聚焦放電產(chǎn)生玻璃通孔的方法可以制備多種類(lèi)型的玻璃,如石英、鈉鈣玻璃、無(wú)堿玻璃、含堿玻璃[14]。圖5為聚焦放電制作的TGV陣列,從圖中可以看出,該方法能夠制作均勻性較好、沒(méi)有裂紋的高密度通孔;但是從玻璃通孔的切片結(jié)果來(lái)看,通孔的形狀不是很垂直。
2.4等離子體刻蝕法
用等離子刻蝕法在石英玻璃上制作玻璃通孔步驟如下:1)在石英上蒸發(fā)沉積了一層鋁層作為刻蝕硬掩模;2)通過(guò)光刻的方法暴露出玻璃表面需要光刻的位置;3)用氯氣或者三氯化硼腐蝕暴露的鋁層,用氧氣等離子體去除玻璃表面的光刻膠;4)利用全氟環(huán)丁烷/氬氣等離子體蝕刻石英以形成TGV [15]。其簡(jiǎn)要步驟如圖6所示。
等離子體法刻蝕TGV可以并行進(jìn)行,同時(shí)進(jìn)行大面積TGV刻蝕,且側(cè)壁粗糙度小(<150 nm),側(cè)壁無(wú)損傷,擁有良好的可靠性保證。但是等離子刻蝕TGV?的方法也還存在許多缺點(diǎn)。截至目前,阻礙干法刻蝕成孔大范圍應(yīng)用的的難點(diǎn)主要有:1)工藝復(fù)雜;2)成本高;3)刻蝕速率慢,速率小于?1 μm/min。
2.5激光燒蝕法
激光燒蝕TGV制作是利用激光的能量將玻璃燒蝕以形成玻璃通孔。激光燒蝕所使用激光器主要包括飛秒激光、皮秒激光、納秒準(zhǔn)分子激光器和CO 2激光器等。喬治亞理工學(xué)院研究人員分別采用CO 2激光和準(zhǔn)分子激光在玻璃上制作的通孔如圖7和圖8所示[16]。CO 2激光屬于“熱激光”,其通過(guò)局部燒蝕玻璃材料形成TGV。但利用該種激光制備的TGV側(cè)壁裂紋較多(熱應(yīng)力問(wèn)題)。準(zhǔn)分子激光器屬于“冷激光”,其燒蝕形成的TGV孔壁基本上沒(méi)有裂紋出現(xiàn),但是孔壁的粗糙度略大(4~5 μm),且成孔效率較低。
2.6電化學(xué)放電加工法
電化學(xué)放電加工法是一種將電火花加工(EDM)和電解加工(ECM)相結(jié)合的新型低成本玻璃微加工方法。該方法通過(guò)電解液的電化學(xué)放電和化學(xué)腐蝕產(chǎn)生的熱熔作用,將材料從基板中去除。電化學(xué)加工的電解槽由一個(gè)堿性電解質(zhì)溶液(氫氧化鉀、氫氧化鈉等)和兩個(gè)電極組成,工具電極和對(duì)電極分別連接到電源的正、負(fù)端子上。當(dāng)兩個(gè)電極之間施加電位差時(shí),在工具電極周?chē)捎跉馀莸木劢Y(jié)而形成一層薄薄的氫氣膜,該氣體膜將工具電極與周?chē)碾娊庖和耆綦x。當(dāng)電位差進(jìn)一步增大時(shí),上述氫氣膜破裂,產(chǎn)生電化學(xué)放電,將玻璃融化并移除。該方法不僅工藝簡(jiǎn)單,且對(duì)設(shè)備要求較低,能快速加工出TGV。但是,截至目前該方法只能加工出孔徑大于300 μm且上開(kāi)口大于下開(kāi)口的錐形玻璃通孔,這也大大限制了該方法的應(yīng)用范圍[17-19]。圖9為電化學(xué)放電法制備TGV裝置。
2.7激光誘導(dǎo)刻蝕法
通過(guò)脈沖激光誘導(dǎo)玻璃產(chǎn)生連續(xù)的變性區(qū),相比未變性區(qū)域的玻璃,變性玻璃在氫氟酸中刻蝕速率較快,基于這一現(xiàn)象可以在玻璃上制作通孔/盲孔。德國(guó)LPKF公司率先用該技術(shù)實(shí)現(xiàn)了玻璃通孔制備[20],該公司將該方法分為兩步:1)使用皮秒激光在玻璃上產(chǎn)生變性區(qū)域;2)將激光處理過(guò)的玻璃放到氫氟酸溶液中進(jìn)行刻蝕。國(guó)內(nèi),廈門(mén)云天半導(dǎo)體科技有限公司也利用激光誘導(dǎo)變性技術(shù)實(shí)現(xiàn)了低成本、高效率、高均勻性玻璃通孔/盲孔制作[21],其簡(jiǎn)要步驟如圖10所示。
光學(xué)顯微鏡圖像如圖11所示,該方法可以在50~500 μm厚的玻璃上形成孔徑大于20 μm的玻璃通孔/盲孔。該技術(shù)的優(yōu)點(diǎn)如下:1)成孔質(zhì)量均勻,一致性好,無(wú)裂紋;2)成孔速率快,可達(dá)到290 TGV/s [21];3)TGV形貌可調(diào),由于刻蝕的各向異性,可以通過(guò)調(diào)節(jié)激光參數(shù)來(lái)控制TGV的垂直度和形貌。綜合比較各種玻璃通孔制造技術(shù),激光誘導(dǎo)刻蝕法具有低成本優(yōu)勢(shì),有大規(guī)模應(yīng)用前景。
與傳統(tǒng)的平面集成技術(shù)相比,玻璃通孔技術(shù)能夠?qū)崿F(xiàn)垂直互連,從而將集成空間擴(kuò)展到了第三維度,顯著提升了空間的利用率。TGV成孔技術(shù)是目前玻璃通孔技術(shù)的難點(diǎn)之一,已報(bào)道有多種TGV成孔方法,如噴砂法、光敏玻璃法、聚焦放電法、等離子刻蝕法、激光燒蝕、電化學(xué)、激光誘導(dǎo)刻蝕法。本節(jié)詳細(xì)介紹了以上幾種TGV成孔方法,比較了不同制作方法的優(yōu)缺點(diǎn),最后的總結(jié)如表1所示。
3玻璃通孔填孔技術(shù)
除TGV成孔技術(shù)外,限制玻璃通孔應(yīng)用的另一個(gè)技術(shù)難點(diǎn)是高質(zhì)量的金屬填充。與TSV不同,TGV孔徑較大,且多為通孔,電鍍時(shí)間長(zhǎng)、成本高;另一方面,與硅材料不同,由于玻璃表面平滑,與常用金屬(如Cu)的黏附性較差,容易造成玻璃襯底與金屬層之間的分層現(xiàn)象,導(dǎo)致金屬層卷曲甚至脫落等現(xiàn)象。
3.1 TGV金屬實(shí)孔填充
類(lèi)似硅通孔的金屬填充方案可以應(yīng)用在TGV金屬填充中。首先,制作TGV盲孔;其次,通過(guò)物理氣相沉積(PVD)的方法在TGV盲孔內(nèi)部沉積種子層;再次,自底向上電鍍,實(shí)現(xiàn)TGV的無(wú)縫填充;最后,通過(guò)臨時(shí)鍵合,背面研磨、化學(xué)機(jī)械拋光(CMP)露銅,解鍵合,形成TGV金屬填實(shí)轉(zhuǎn)接板[22-24]。圖12為采用上述TGV填孔方案的工藝流程,包括:玻璃盲孔制備,TGV銅填實(shí),銅覆蓋層去除過(guò)程,頂部重布線(xiàn)層(RDL)(TR1)過(guò)程,臨時(shí)鍵合,研磨減薄露銅,底部RDL(BR1)制備,解鍵合等工藝過(guò)程。
另外一個(gè)將TGV填實(shí)的方案是使用金屬導(dǎo)電膠進(jìn)行TGV填實(shí)[17]。利用金屬導(dǎo)電膠的優(yōu)點(diǎn)是固化后導(dǎo)電通孔的熱膨脹系數(shù)可以調(diào)節(jié),使其接近基材,避免了因CTE不匹配造成的失效。通過(guò)對(duì)銅導(dǎo)電膠填充工藝的優(yōu)化,實(shí)現(xiàn)了間距為130 μm、孔徑為50 μm的TGV金屬化。Cu導(dǎo)電膠填充后的TGV孔如圖13所示。研究表明,采用銅導(dǎo)電膠填充后的TGV電導(dǎo)率約為1.6~1.9 (Ω·m 2 ) -1。該方法工藝簡(jiǎn)單,且能夠在一定程度上降低TGV金屬化成本。但是,部分導(dǎo)電膠,特別是銅導(dǎo)電膠的電性能比較差,這也阻礙了該方法在高頻電子器件或電子系統(tǒng)上的應(yīng)用。
3.2 TGV孔內(nèi)電鍍薄層
除TGV電鍍填實(shí)外,TGV也可采用通孔內(nèi)電鍍薄層方案實(shí)現(xiàn)電學(xué)連接。研究表明,在電性能方面,薄層電鍍與實(shí)心電鍍的插入損耗差別較小。采用薄層電鍍方案的優(yōu)勢(shì)是在保證電學(xué)性能的同時(shí)可以有效減小電鍍時(shí)間和電鍍成本。通常電鍍填孔需要沉積金屬粘附層如鈦(Ti)、鉻(Cr)等,種子層Cu,然后進(jìn)行電鍍。旭硝子公司的研究結(jié)果顯示Cr層與ENA 1玻璃的粘附性最好(347.8 mN),大于硅與鎢化鈦(TiW)金屬層間的244.1 mN。清華大學(xué)研究了關(guān)于在康寧公司的玻璃上濺射不同種類(lèi) (TiW、Ti、Cr、Cu)、不同厚度(50 nm、100 nm、150 nm)金屬材料以及不同玻璃表面粗糙度的對(duì)比實(shí)驗(yàn),并進(jìn)行了劃痕測(cè)試。研究表明,在進(jìn)行的實(shí)驗(yàn)中,50 nm的TiW在粗糙度為4.4 nm的玻璃襯底上黏附性最強(qiáng)[23]。
但是,對(duì)于高深寬比通孔來(lái)說(shuō),物理氣相沉積的設(shè)備和工藝過(guò)于昂貴。因此,近年來(lái)研發(fā)人員在開(kāi)發(fā)采用化鍍Cu種子層的低成本TGV填充方案,然后再通過(guò)半加成法(SAP)在光刻膠圖形上電鍍出Cu線(xiàn)路。由于玻璃與金屬Cu之間熱膨脹系數(shù)不同(玻璃為3×10 -6 /K,Cu為17×10 -6 /K),化學(xué)結(jié)構(gòu)存在明顯差異,并且玻璃具有非常光滑的表面,導(dǎo)致玻璃與化鍍Cu之間的黏附力差,需要特殊的處理來(lái)提高結(jié)合力。美國(guó)安美特公司報(bào)道了金屬氧化物黏附增強(qiáng)方法[25-26],通過(guò)把玻璃基板浸入化學(xué)藥液,覆蓋納米厚度的金屬氧化物助黏膠形成黏附層提高化鍍Cu層的黏附力,9 nm厚度黏附層圖片如圖14所示。當(dāng)黏附層的厚度增加至5~20 nm時(shí),Cu與玻璃之間的剝離強(qiáng)度達(dá)到6 N/cm以上。但是,截至目前通過(guò)黏附層提高結(jié)合力的機(jī)理尚不清楚,可能原因是由于黏附層納米尺度的機(jī)械釘扎作用以及化學(xué)反應(yīng)結(jié)合共同作用的結(jié)果[24]。此外,喬治亞理工學(xué)院研發(fā)人員將環(huán)氧聚合物干膜貼在玻璃表面,提高化鍍Cu與玻璃之間的結(jié)合力[27-28]。在薄玻璃襯底上層壓介質(zhì)層,在增強(qiáng)玻璃襯底機(jī)械強(qiáng)度的同時(shí),可以作為表面RDL的黏附層,增強(qiáng)抗剝離強(qiáng)度。采用該方案得到的結(jié)果如圖15所示。該方案存在的主要問(wèn)題是增加了工藝,表面聚合物膜需要通過(guò)激光或干法刻蝕,而且由于孔內(nèi)沒(méi)有聚合物涂敷,在可靠性方面可能存在失效風(fēng)險(xiǎn)。為了進(jìn)一步簡(jiǎn)化工藝,ONITAKE等開(kāi)發(fā)了基于254 nm光波的紫外光清洗后直接化鍍Cu工藝[29]。紫外光清洗技術(shù)是利用有機(jī)化合物的光敏氧化作用去除黏附在材料表面的有機(jī)物質(zhì),碳?xì)浠衔镂漳芰亢蠓纸獬呻x子、游離態(tài)原子、受激分子和中子,經(jīng)過(guò)清洗后的材料表面可以達(dá)到原子級(jí)清潔度。測(cè)試結(jié)果顯示Cu與玻璃之間的剝離強(qiáng)度為3.5 N/cm。
4玻璃通孔高密度布線(xiàn)
4.1線(xiàn)路轉(zhuǎn)移(CTT)和光敏介質(zhì)嵌入(PTE)
相對(duì)于有機(jī)襯底而言,玻璃表面的粗糙度小,所以在玻璃上可以進(jìn)行高密度布線(xiàn)。佐治亞理工對(duì)玻璃轉(zhuǎn)接板高密度布線(xiàn)做了很多研究。由于半加成工藝法在線(xiàn)寬小于5 μm的時(shí)候會(huì)面臨許多挑戰(zhàn),例如在窄間距內(nèi)刻蝕種子層容易對(duì)銅走線(xiàn)造成損傷且窄間距里的種子層殘留易造成漏電。劉富漢等開(kāi)發(fā)了CTT和PTE技術(shù)[30]。CTT主要包括兩個(gè)過(guò)程。1)精細(xì)RDL線(xiàn)預(yù)制。每一RDL層可以在可移動(dòng)載體上單獨(dú)制造一層薄導(dǎo)電層,并在轉(zhuǎn)移到基板上之前測(cè)試或檢查細(xì)線(xiàn)成品率。精細(xì)線(xiàn)路的形成采用細(xì)線(xiàn)光刻和電解鍍銅的方法,并且以薄銅箔作為鍍層的種子層。工藝流程如圖16(a)所示。2) RDL層集成到基板上。RDL層被制造出來(lái)后,它們?cè)谑褂脽釅汉系耐瑫r(shí)被轉(zhuǎn)移到核心層的兩邊,該步驟如圖16(b)所示。
PTE工藝可分為兩個(gè)不同的步驟:1)在光敏電介質(zhì)層中形成精細(xì)的溝槽;2)金屬化,包括種子層沉積、電鍍和表面除銅。PTE詳細(xì)工藝流程如圖17所示。首先刻蝕基板下側(cè)銅箔,并使用真空壓膜機(jī)在基板上側(cè)壓合感光膜,在光刻圖案化后下一步是種子層沉積,采用物理氣相沉積(PVD)分別沉積Ti和Cu作為阻擋層和種子層,接著采用電鍍工藝填充溝槽,溝槽填充完后,使用化學(xué)腐蝕劑刻蝕掉上表面的銅從而露出線(xiàn)路。如圖18所示,劉富漢等使用CTT和PTE兩種方法分別達(dá)到了RDL 1.5 μm和2 μm的線(xiàn)寬線(xiàn)距。
4.2多層RDL的2.5D玻璃轉(zhuǎn)接板技術(shù)
喬治亞理工學(xué)院的LU等研究了多層RDL的2.5D玻璃轉(zhuǎn)接板技術(shù),實(shí)現(xiàn)了面板級(jí)光刻后1.5~5 μm的線(xiàn)條溝槽制備,并提出改進(jìn)式半加成工藝法(SAP)達(dá)到了5 μm以下低成本的線(xiàn)寬制作工藝[31],即用旋轉(zhuǎn)金剛刀取代昂貴的CMP對(duì)層間RDL表面平坦化,進(jìn)而做到低成本多層RDL堆疊。其工藝步驟如圖19所示。首先在第一層RDL的基礎(chǔ)上進(jìn)行壓膜,然后通過(guò)顯影制作通孔并暴露出第一層RDL的銅焊盤(pán),接著進(jìn)行種子層濺射。濺射完成后,將高分辨率的光刻薄膜層壓在基板上側(cè)并進(jìn)行高精度的曝光、顯影。完成上述步驟后,采用電鍍工藝填充通孔并用旋轉(zhuǎn)金剛刀進(jìn)行表面平坦化,最后去除光刻薄膜并完成種子層刻蝕。通過(guò)上述工藝得到的多層RDL堆疊結(jié)果如圖20所示。
5玻璃通孔技術(shù)的應(yīng)用
與硅基轉(zhuǎn)接板相比,玻璃通孔轉(zhuǎn)接板具有更為優(yōu)良的電學(xué)特性和材料特性,因此具有廣泛的應(yīng)用前景。下面對(duì)玻璃通孔轉(zhuǎn)接板的幾個(gè)典型應(yīng)用進(jìn)行綜述。
5.1玻璃基板的三維集成無(wú)源元件
玻璃基板具有優(yōu)異的高頻電學(xué)性能,因此被廣泛應(yīng)用于集成無(wú)源元件(IPD)之中。2010年,喬治亞理工的封裝中心率先完成了
基于TGV的濾波器設(shè)計(jì)與制作,并與相同的硅基電感對(duì)比,其中的電感結(jié)構(gòu)采用TGV互連形成了高Q值的三維(3D)螺旋電感,展現(xiàn)了玻璃材料的優(yōu)良電學(xué)特性[32]。2017年,日月光集團(tuán)(ASE)的研究人員在玻璃基板上實(shí)現(xiàn)了面板級(jí)的IPD制作工藝,通過(guò)該工藝,成功在408 mm×512 mm的長(zhǎng)方形玻璃基板上制作IPD,如圖21所示,該方案板材翹曲可控制在1 mm以?xún)?nèi),并且無(wú)明顯的結(jié)構(gòu)剝落/分層現(xiàn)象[33],該方案進(jìn)一步降低了IPD制作的成本。
2017年ASE的LEE等采用玻璃通孔制作3D電感,并利用晶圓級(jí)集成工藝的優(yōu)勢(shì),將射頻ASIC模塊與玻璃IPD模塊集成,形成晶圓級(jí)芯片封裝(WLCSP)[34]。該工藝從TGV金屬化和充填工藝開(kāi)始,然后進(jìn)行標(biāo)準(zhǔn)的晶圓級(jí)IPD工藝來(lái)完成前端結(jié)構(gòu)。正面結(jié)構(gòu)由電容器、RDL和凸點(diǎn)下金屬(UBM)組成,然后將晶圓送到裝配工廠進(jìn)行晶圓級(jí)裝配。裝配完成后,再經(jīng)過(guò)背面加工,形成3D電感和焊球焊盤(pán)。背面工藝包括玻璃晶片減薄、背面RDL和鈍化工藝。最后是制作錫球和切割以形成WLCSP。最終得到如圖22所示的芯片。
玻璃通孔技術(shù)不僅可以用于制作TGV,還可以在玻璃上制作空腔,進(jìn)而為芯片的封裝提供一種名為嵌入式玻璃扇出(eGFO)的新方案。2017年喬治亞理工的3D系統(tǒng)封裝研究中心率先實(shí)現(xiàn)了用于高I/O密度和高頻多芯片集成的玻璃面板扇出(GFO)封裝。該技術(shù)在70 μm厚、大小為300 mm×300 mm的玻璃面板上完成26個(gè)芯片的扇出封裝,并有效控制芯片偏移和翹曲[35]。2020年廈門(mén)云天半導(dǎo)體科技公司采用嵌入式玻璃扇出技術(shù)開(kāi)發(fā)了77 GHz汽車(chē)?yán)走_(dá)芯片的封裝,并在此基礎(chǔ)上提出了一種高電性能的天線(xiàn)封裝(AiP)方案[36]。該方案具體工藝流程如圖23所示。在厚度為180 μm的玻璃晶片中,先采用激光誘導(dǎo)玻璃變性和化學(xué)腐蝕工藝形成玻璃空腔,然后將175 μm高的芯片放入玻璃空腔中。通過(guò)復(fù)合材料將芯片與玻璃之間的縫隙填壓而不產(chǎn)生空隙,同時(shí)保護(hù)芯片的背面。對(duì)晶圓的頂面進(jìn)行剝離,形成銅RDL,最后進(jìn)行后續(xù)線(xiàn)路制作、球柵陣列(BGA)制作以及晶圓切片,最終得到如圖24所示的芯片。
2020年喬治亞理工的TUMMALA等首次在100 μm的玻璃基板上實(shí)現(xiàn)了在n257頻段(26.5~29.5 GHz)的芯片嵌入毫米波天線(xiàn)集成模塊,該方案的工藝流程如圖25所示,首先在玻璃上制作2.5 mm×1.77 mm的空腔,然后將芯片放入其中并完成后續(xù)線(xiàn)路制作,從而得到應(yīng)用于n257頻段的毫米波天線(xiàn)[37];相比于倒裝芯片嵌入技術(shù),該方案具有更低的信號(hào)損耗。
5.3基于玻璃通孔的微機(jī)電系統(tǒng)封裝
玻璃轉(zhuǎn)接板相比于硅轉(zhuǎn)接板具有一系列的優(yōu)勢(shì),因此它也被廣泛應(yīng)用于MEMS封裝中,2013年,LEE等利用玻璃通孔技術(shù)實(shí)現(xiàn)射頻MEMS器件的晶圓級(jí)封裝,采用電鍍方案實(shí)現(xiàn)通孔的完全填充,通過(guò)該方案制作的射頻MEMS器件在20 GHz時(shí)具有0.197 dB的低插入損耗和20.032 dB的高返回?fù)p耗,在40 GHz以?xún)?nèi)具有穩(wěn)定的射頻性能[38]。2016年,廈門(mén)大學(xué)的馬盛林等提出了一種基于TGV轉(zhuǎn)接板的慣性MEMS器件晶圓級(jí)封裝方案。在400 μm厚的玻璃基板上制作TGV通孔,后續(xù)金屬化則采用濺射Al的方案,最終實(shí)現(xiàn)了一個(gè)MEMS加速計(jì)的封裝制作[39];工藝加工結(jié)果如圖26所示。2018年,LAAKSO等創(chuàng)造性地使用磁輔助組裝的方式來(lái)填充玻璃通孔,并且將該技術(shù)應(yīng)用于MEMS器件的封裝中,如圖27所示。
通過(guò)該方法填充的TGV具有低電阻、高集成密度的特點(diǎn),同時(shí)能夠有效改善金屬與玻璃間不匹配的問(wèn)題[40]。
5.4基于TGV工藝的集成天線(xiàn)
廈門(mén)大學(xué)的張淼等基于先進(jìn)封裝及微納制造技術(shù)制備了高頻波導(dǎo)縫隙天線(xiàn)[41],創(chuàng)新性地引入TGV加工波導(dǎo)縫隙天線(xiàn)。首先采用激光誘導(dǎo)刻蝕制備波導(dǎo)縫隙陣列天線(xiàn)玻璃襯底,通過(guò)激光在玻璃上誘導(dǎo)產(chǎn)生連續(xù)的變性區(qū),后將變性后玻璃在稀釋氫氟酸中進(jìn)行刻蝕,由于激光作用處的玻璃在氫氟酸中刻蝕速率較快,所以玻璃會(huì)成塊脫落從而形成目標(biāo)通孔結(jié)構(gòu)。最終刻蝕后的玻璃通孔精度為±5 μm,遠(yuǎn)遠(yuǎn)高于傳統(tǒng)機(jī)加工的精度。其次,采用物理氣相沉積對(duì)每層波導(dǎo)縫隙陣列天線(xiàn)玻璃襯底濺射銅層,經(jīng)過(guò)氧等離子體清洗以徹底清除焊盤(pán)表面的有機(jī)物等顆粒,并使晶圓表面產(chǎn)生一定粗糙度,為種子層的良好附著創(chuàng)造條件。清洗后的晶圓在烤箱150 ℃下烘烤60 min徹底去除水汽。然后在磁控濺射設(shè)備中,晶圓表面濺射一層厚度約為5 μm的銅層。最后,采用金屬焊料鍵合技術(shù)將5片晶圓鍵合。用刮刀以及絲網(wǎng)將約10 μm厚度的錫焊料印刷到晶圓表面,然后在鍵合機(jī)的真空腔室中以240 ℃的溫度加熱,以40 N的壓力壓合5 min使焊料融化或相互擴(kuò)散以達(dá)到鍵合的目的。其工藝流程如圖28所示。通過(guò)以上加工工藝得到的高能太赫茲天線(xiàn)如圖29所示。
HWANGBO等設(shè)計(jì)了一種緊湊、高功率高效的TGV-集成天線(xiàn)[42],其原理如圖30所示,并將其應(yīng)用于3D系統(tǒng)封裝(SiP)中的V波段(40~75 GHz)無(wú)線(xiàn)平面內(nèi)芯片到芯片(C2C)通信。其設(shè)計(jì)步驟如圖31所示。首先在玻璃基板上制作TGV,并進(jìn)行玻璃清洗。在基板干燥后,將30 nm的鈦(Ti)濺射在玻璃基板的正面作為附著層,然后進(jìn)行光刻膠干膜的壓膜和光刻,接著采用濺射法制備Ti/Cu/Ti (30 nm/2 μm/30 nm)金屬層作為傳輸線(xiàn),對(duì)位于玻璃基板底部的圓盤(pán)濺射另一層Ti,并采用相類(lèi)似的工藝沉積底部的Ti/Cu/Ti(30 nm/2 μm/30 nm)金屬層,最后完成去膠和種子層刻蝕。
5.5多層玻璃基板
隨著5G時(shí)代的到來(lái),各種設(shè)備廠商對(duì)電子器件的性能提出了更高要求,這也推動(dòng)著電子器件的封裝技術(shù)從傳統(tǒng)的2D封裝往2.5D甚至3D的方向發(fā)展。然而2.5D和3D封裝都存在熱膨脹系數(shù)不匹配的問(wèn)題,2018年IWAI等使用導(dǎo)電膠填充玻璃通孔,從而實(shí)現(xiàn)多層玻璃基板堆疊,在回流過(guò)程中,通過(guò)該方案制作的多層玻璃基板的翹曲比傳統(tǒng)有機(jī)基板要小,通過(guò)該技術(shù)可以實(shí)現(xiàn)高密度布線(xiàn),同時(shí)具有較高的可靠性[43]。2019年,IWAI等在多層玻璃基板技術(shù)的基礎(chǔ)上完成了一個(gè)多芯片封裝的結(jié)構(gòu)[44],其工藝流程如圖32所示。首先用激光誘導(dǎo)玻璃變性和濕法刻蝕技術(shù)在玻璃上形成TGV,并制作種子層;其次,使用半加法工藝制作布線(xiàn)圖案;再次,用激光在干燥的樹(shù)脂層壓膜上制作通孔并進(jìn)行絲網(wǎng)印刷工藝;之后,將單層基片疊放在一起,然后用真空熱壓機(jī)將導(dǎo)電漿料和干膜熔化;最后將多個(gè)芯片對(duì)齊安裝。通過(guò)以上工藝制作的多芯片模塊如圖33所示。
5.6基于玻璃基板的硅光集成技術(shù)
玻璃轉(zhuǎn)接板除了應(yīng)用于電子封裝領(lǐng)域,在光電領(lǐng)域也有廣泛應(yīng)用。2010年,IZM聯(lián)合肖特公司發(fā)布了面板玻璃轉(zhuǎn)接板的制作樣品,并在上方集成了一個(gè)4通道的雙向光電收發(fā)模塊,單通道的傳輸速率為10 Gbit/s,功耗僅有592 mW [45]。2015年,研究者第一次在光電基板(EOCB)上實(shí)現(xiàn)了對(duì)平面多模玻璃基波導(dǎo)和球形反光鏡的集成,為解決將來(lái)超級(jí)計(jì)算機(jī)和數(shù)據(jù)存儲(chǔ)網(wǎng)絡(luò)的需求打下基礎(chǔ)[46]。圖34、35分別為IZM的應(yīng)用于光電領(lǐng)域的玻璃轉(zhuǎn)接板樣品以及EOCB疊層設(shè)計(jì)示意圖。
6結(jié)論
隨著半導(dǎo)體行業(yè)的飛速發(fā)展,半導(dǎo)體器件逐漸朝著高頻、大功率、小尺寸的方向發(fā)展。玻璃通孔互連技術(shù)具有突出的電學(xué)性能和良好的力學(xué)、光學(xué)性能,在先進(jìn)封裝和無(wú)源器件制造等領(lǐng)域具有巨大的應(yīng)用潛力,近年來(lái)得到了突破性的發(fā)展。本文綜述了國(guó)內(nèi)外TGV成孔技術(shù)和進(jìn)展,主要包括噴砂法、光敏玻璃法、聚焦放電法、等離子刻蝕、激光燒蝕、電化學(xué)放電法和激光誘導(dǎo)玻璃變性法,并對(duì)比了以上幾種技術(shù)的優(yōu)缺點(diǎn);總結(jié)了幾種高可靠性通孔金屬填充技術(shù)以及高深寬比高密度布線(xiàn)技術(shù);最后總結(jié)了玻璃通孔技術(shù)的應(yīng)用進(jìn)展,說(shuō)明玻璃通孔技術(shù)在2.5D/3D封裝和高頻、高性能、低成本電子器件等重要領(lǐng)域上具有廣泛的應(yīng)用前景。
審核編輯:黃飛
-
等離子
+關(guān)注
關(guān)注
2文章
236瀏覽量
29931 -
光刻
+關(guān)注
關(guān)注
8文章
321瀏覽量
30164 -
顯微鏡
+關(guān)注
關(guān)注
0文章
563瀏覽量
23035 -
射頻器件
+關(guān)注
關(guān)注
7文章
125瀏覽量
25548
原文標(biāo)題:玻璃通孔技術(shù)研究進(jìn)展
文章出處:【微信號(hào):深圳市賽姆烯金科技有限公司,微信公眾號(hào):深圳市賽姆烯金科技有限公司】歡迎添加關(guān)注!文章轉(zhuǎn)載請(qǐng)注明出處。
發(fā)布評(píng)論請(qǐng)先 登錄
相關(guān)推薦
新型銅互連方法—電化學(xué)機(jī)械拋光技術(shù)研究進(jìn)展
室內(nèi)顆粒物的來(lái)源、健康效應(yīng)及分布運(yùn)動(dòng)研究進(jìn)展
薄膜鋰電池的研究進(jìn)展
傳感器EMC的重要性與研究進(jìn)展
太赫茲量子級(jí)聯(lián)激光器等THz源的工作原理及其研究進(jìn)展
中孔分子篩研究進(jìn)展
中藥提取技術(shù)的研究進(jìn)展
廢舊鎳氫電池回收處理技術(shù)研究進(jìn)展
物聯(lián)網(wǎng)隱私保護(hù)研究進(jìn)展
電動(dòng)汽車(chē)無(wú)線(xiàn)充電技術(shù)的研究進(jìn)展_高大威
農(nóng)業(yè)機(jī)械自動(dòng)導(dǎo)航技術(shù)研究進(jìn)展
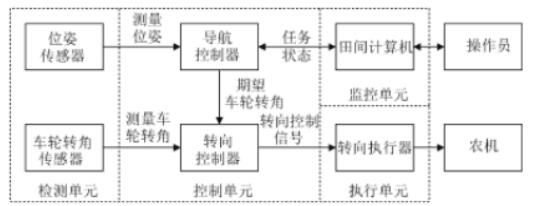
量子計(jì)算關(guān)鍵技術(shù)研究進(jìn)展
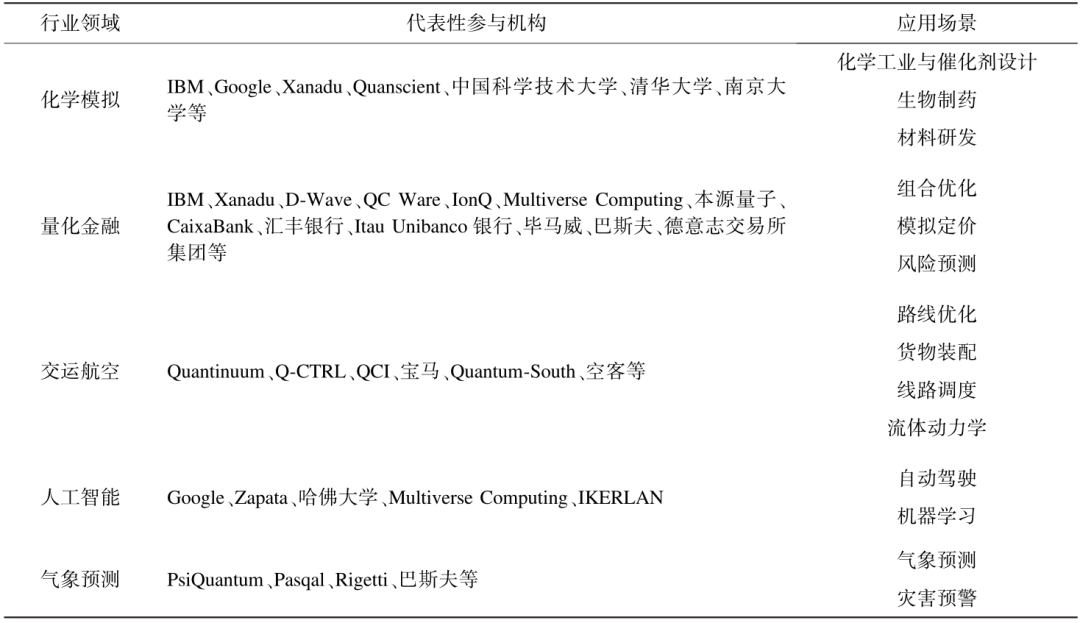
先進(jìn)激光雷達(dá)探測(cè)技術(shù)研究進(jìn)展
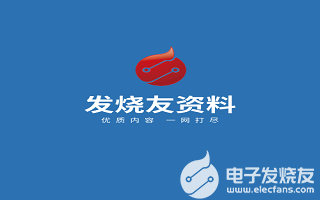
評(píng)論