高功率應(yīng)用需要高功率密度和可靠的功率半導(dǎo)體,且成本合理。分立器件降低了解決方案的總成本,但在重負(fù)載循環(huán)期間必須承受高熱要求。為了滿足這些要求,功率半導(dǎo)體應(yīng)具有較低的總損耗,使用標(biāo)準(zhǔn)封裝中最大的芯片,并具有良好的冷卻系統(tǒng)。
通過直接銅鍵合 (DCB) 安裝在水冷散熱器上的分立器件是設(shè)計(jì)工程師可用的一種解決方案,假設(shè)分立器件可以像表面貼裝器件 (SMD) 一樣安裝。
TO 247PLUS分立式封裝的回流焊
TO-247PLUS是一種理想的封裝,可以容納高功率密度解決方案所需的大型芯片[1]。為了最大限度地提高其熱性能,需要從器件芯片到冷卻系統(tǒng)具有低熱阻。一種解決方案是通過DCB將封裝背面焊接到水冷散熱器上。作為推薦用于波峰焊的標(biāo)準(zhǔn)通孔器件 (THD),對(duì)封裝進(jìn)行了改進(jìn),以承受回流焊工藝。TO-247PLUS封裝的改進(jìn)版本是根據(jù)JEDEC J-STD-020E標(biāo)準(zhǔn)設(shè)計(jì)和認(rèn)證的。
仿真結(jié)果:不同DCB材料對(duì)系統(tǒng)熱阻的影響
在TO-247PLUS SMD封裝的開發(fā)過程中進(jìn)行了多次仿真。這些仿真中考慮的器件使用可放入TO247PLUS封裝的最大芯片尺寸。要了解使用可回流焊接TO-247PLUS的優(yōu)勢(shì),必須首先驗(yàn)證整個(gè)系統(tǒng)的熱阻。
在對(duì)組裝在DCB上的器件進(jìn)行可靠性測(cè)試之前,使用有限元法(FEM)軟件Ansys進(jìn)行了熱仿真。它們首次表明了系統(tǒng)對(duì)不同類型DCB材料的熱性能。為了簡(jiǎn)化 DUT 模型,省略了布線,因?yàn)榉抡娴闹攸c(diǎn)是結(jié)點(diǎn)到環(huán)境的熱流。DCB使用兩個(gè)銅層和鋁2O3層間陶瓷材料。該模型使用的三層材料厚度分別為 0.3 mm Cu、0.38 mm Al2O 3, 和 0.3 mm Cu。DUT 用 80 μm SAC 合金焊接到頂部 Cu DCB 層,而 DCB 的底部銅焊接到銅基板上。然后將仿真結(jié)果與實(shí)際值進(jìn)行比較。圖 1 說明了仿真系統(tǒng)。
圖片由Bodo's Power Systems提供 [PDF]
然后,根據(jù)芯片加熱至150°C20秒以達(dá)到芯片、DCB和基板之間的靜態(tài)熱量分布后的冷卻曲線確定熱阻。使用不同尺寸和厚度的DCB銅進(jìn)行了進(jìn)一步的測(cè)試。焊接質(zhì)量也被考慮在內(nèi),以了解其對(duì)系統(tǒng)整體熱阻的影響。表 1 總結(jié)了模擬的 R 釷(J-A) 適用于不同的DCB材料。
- 表 1. 不同DCB材料和裝配工藝的模擬Rth(j-a)摘要。*
參數(shù) | R | 差值 [%] |
---|---|---|
DCB尺寸:- 20 x 23 毫米DCB銅厚度:- 0.3 毫米焊料空洞:0%焊料:- 80 μm SAC 合金 | 0.292 | 參考 |
DCB尺寸:- 28 x 32 毫米 | 0.288 | -1.4 |
DCB銅厚度:- 0.2 毫米 | 0.294 | 0.7 |
單焊料空隙:- 10% | 0.323 | 10.3 |
銀燒結(jié):- 25 μm 厚 | 0.280 | -4.1 |
增加DCB尺寸可以降低系統(tǒng)熱阻,而減小DCB的銅厚度可以增加R 釷(J-A) .一個(gè)關(guān)鍵參數(shù)是單個(gè)焊料空隙,在該空隙下,R 顯著增加 釷(J-A) 被看見了。為了提高 DUT、DCB 和基板之間連接的強(qiáng)度和質(zhì)量,以及整體熱性能,應(yīng)考慮使用銀燒結(jié)而不是焊接工藝。
逆變器應(yīng)用中的熱性能
為了評(píng)估 TO 247PLUS SMD 封裝的熱性能,在逆變器應(yīng)用中進(jìn)行了大電流測(cè)試。DUT 組裝在 DCB 中,并在與應(yīng)用相關(guān)的條件下進(jìn)行測(cè)試。這些評(píng)估中使用的測(cè)試樣品是 750 V/ 200 A EDT2 IGBT 與 TO-247PLUS SMD 封裝的 200 A EmCon3 二極管共同封裝,專為主逆變器系統(tǒng)而設(shè)計(jì),特別是在建筑、商用和農(nóng)用車輛 (CAV) 應(yīng)用中。EDT2 IGBT技術(shù)具有微圖案溝槽場(chǎng)截止,可顯著降低導(dǎo)通和關(guān)斷開關(guān)損耗,并針對(duì)10 kHz范圍內(nèi)的開關(guān)頻率進(jìn)行了優(yōu)化。圖 2 描繪了安裝在底板上的 DCB 中 DUT 的測(cè)試組件。
兩個(gè)器件在 B6 配置中并聯(lián)連接,總共有 12 個(gè)測(cè)試樣品。所有 DUT 均回流焊接到 DCB 上,并安裝到水冷基板上。負(fù)載為永磁電機(jī)。熱電偶用于監(jiān)測(cè)設(shè)備溫度、底板和進(jìn)水口/出水口。該逆變器的母線電壓設(shè)置為310 V,而水溫設(shè)置為27°C。
熱測(cè)試涉及最惡劣條件下的應(yīng)用情況。在低開關(guān)頻率下,逆變器在其每個(gè)相段上工作,以在較長(zhǎng)時(shí)間內(nèi)傳導(dǎo)高峰值電流。如果冷卻設(shè)計(jì)不合適,IGBT/二極管將被加熱,可能加熱到超過芯片的溫度。
圖3顯示了一個(gè)示例電流波形,相當(dāng)于鎖定在4 kHz的轉(zhuǎn)子。電機(jī)的轉(zhuǎn)子鎖可與短路測(cè)試相媲美。測(cè)得的逆變器輸出峰峰值電流為1092 A,產(chǎn)生315 A RMS電流。這基本上是無功電流,因?yàn)樗窃诳蛰d下運(yùn)行的,輸出頻率非常低,為 1 Hz。當(dāng)逆變器負(fù)載約500 A至1000 A一段時(shí)間時(shí),測(cè)量測(cè)試設(shè)備的最高溫度。
* 圖3. 逆變器的峰峰值輸出電流波形。圖片由Bodo's Power Systems提供 [PDF]*
表2列出了工作頻率為10 kHz的逆變器對(duì)應(yīng)的負(fù)載電流和持續(xù)時(shí)間。在 986 A 的峰峰值電流(對(duì)應(yīng)于 284 A 的 RMS 電流)下,持續(xù) 24 秒會(huì)將 DUT 加熱到最高溫度 112°C。 考慮到工作開關(guān)頻率為4 kHz的逆變器,表3列出了轉(zhuǎn)子鎖定條件下的等效負(fù)載電流和持續(xù)時(shí)間。在 1092 A pk-pk 電流(對(duì)應(yīng)于 315 A 的 RMS 電流)下,持續(xù)時(shí)間為 1 分鐘會(huì)將 DUT 加熱到最高溫度 105°C。 所有由此產(chǎn)生的 DUT 最高溫度均在器件 175°C 的最大允許工作結(jié)溫范圍內(nèi)。
* 表 2. 在10 kHz的開關(guān)頻率下,DUT的最大溫度相當(dāng)于轉(zhuǎn)子鎖定操作。*
兩個(gè)并聯(lián)組件的 200 A 負(fù)載測(cè)試 – 10 kHz |
---|
pk-pk 電流 [A] |
520 |
600 |
824 |
986 |
* 表 3. 最大 DUT 溫度相當(dāng)于開關(guān)頻率為 4kHz 時(shí)轉(zhuǎn)子鎖定操作。*
兩個(gè)并聯(lián)組件的 200 A 負(fù)載測(cè)試 – 4 kHz |
---|
pk-pk 電流 [A] |
540 |
712 |
920 |
1092 |
總結(jié)
TO-247PLUS SMD 是理想的分立式封裝,適用于要求高功率密度和可靠功率半導(dǎo)體且成本合理的高要求應(yīng)用。該封裝能夠回流焊接到 DCB,而不會(huì)產(chǎn)生分層。這最大限度地減少了從器件芯片到 DCB 基板的熱阻。熱仿真表明,單次焊接空洞對(duì)整個(gè)系統(tǒng)的熱性能影響巨大,而銀燒結(jié)可以大大提高系統(tǒng)的導(dǎo)熱性。應(yīng)用測(cè)試證實(shí),EDT2 IGBT與EmCon3二極管共同封裝,采用TO 247PLUS SMD封裝,滿足CAV等高功率應(yīng)用的要求。轉(zhuǎn)子鎖定測(cè)試與系統(tǒng)短路測(cè)試相當(dāng),導(dǎo)致設(shè)備在最大允許工作結(jié)溫內(nèi)運(yùn)行。
-
芯片
+關(guān)注
關(guān)注
455文章
50818瀏覽量
423727 -
封裝
+關(guān)注
關(guān)注
126文章
7905瀏覽量
142971 -
散熱器
+關(guān)注
關(guān)注
2文章
1056瀏覽量
37561 -
功率半導(dǎo)體
+關(guān)注
關(guān)注
22文章
1156瀏覽量
42983
發(fā)布評(píng)論請(qǐng)先 登錄
相關(guān)推薦
簡(jiǎn)述分立式整流器的整流原理
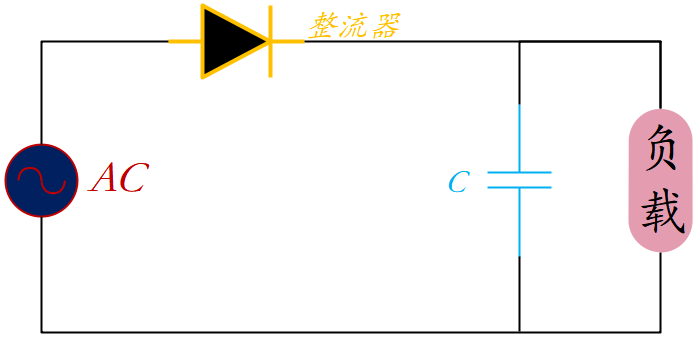
英飛凌推出全新車規(guī)級(jí)750 V EDT2 IGBT,適用于分立式牽引逆變器
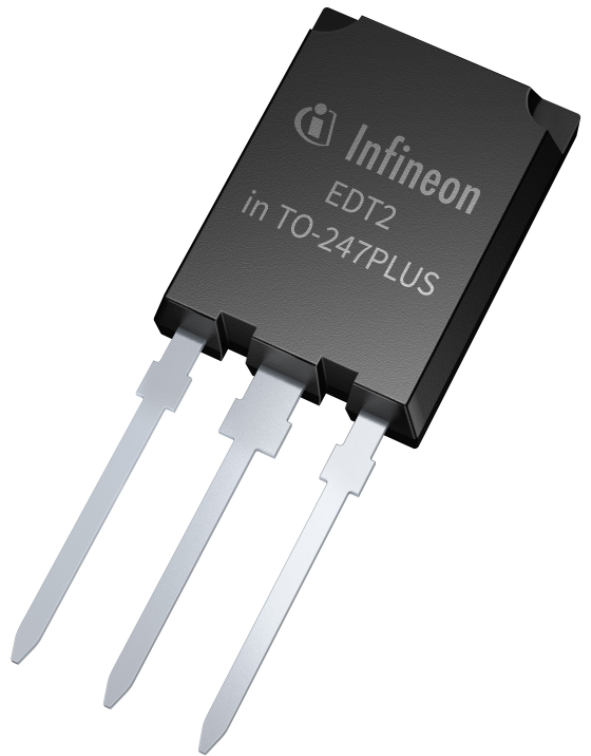
PowerLab筆記:進(jìn)行分立式設(shè)計(jì)的方法
AM437x離散功率簡(jiǎn)化型分立式電源解決方案包括BOM及框圖
低成本LCD偏置電源分立式解決方案
集成與分立式低電壓電機(jī)驅(qū)動(dòng)解決方案的主要差異
支持多種汽車應(yīng)用的微控制器分立式電源設(shè)計(jì)
分立式逆變器的挑戰(zhàn)
集成壓控振蕩器的寬帶鎖相環(huán)真的能取代分立式解決方案嗎?
如何進(jìn)行分立式設(shè)計(jì)?
英飛凌推出額定電流高達(dá)120A的新型TO-247PLUS封裝
英飛凌推出面向高能效電源應(yīng)用的第七代分立式650V TRENCHSTOP IGBTs H7新品
集成壓控振蕩器的寬帶鎖相環(huán)能取代分立式解決方案嗎
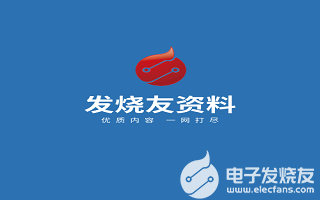
評(píng)論