以2010年為肇始,中國動力電池產(chǎn)業(yè)駛?cè)肓?0年增長快車道,10年來,產(chǎn)業(yè)鏈經(jīng)歷了萌動、躁熱、瘋狂、驟冷、回暖、洗牌、理性、豐滿。
10年來,中國動力電池產(chǎn)業(yè)從破土的幼苗,到羽翼豐滿,臂膀壯碩,并開始走向世界舞臺中央,成為全球電動化的主角。
回望十年路,預(yù)見新征途。在新舊十年轉(zhuǎn)換之際,高工鋰電發(fā)起“中國動力電池十年回望”系列策劃,通過專題、專訪、口述等形式回望產(chǎn)業(yè)發(fā)展得與失,勾勒新十年產(chǎn)業(yè)圖景。
動力電池制造正在進(jìn)入大規(guī)模生產(chǎn)的導(dǎo)入期,從全球看,到2025年將實現(xiàn)1000GWh的制造能力。這對于整個生產(chǎn)制造環(huán)節(jié)提出了更高的要求,包括大規(guī)模制造的要求、對于智能化的要求。
而真正的大規(guī)模制造不是空中樓閣,而是能夠通過切實可行的方式來提升制造效率、品質(zhì),并降低成本。
“基于科學(xué)認(rèn)識電池的制造是解決質(zhì)量、效率、成本的關(guān)鍵;而標(biāo)準(zhǔn)化是產(chǎn)業(yè)的基礎(chǔ),基于標(biāo)準(zhǔn)化行業(yè)有30%以上的降本空間。同時,動力電池制造技術(shù)必須與材料、原理深度融合?!边@是吉陽智能董事長陽如坤給出的判斷。
他認(rèn)為,產(chǎn)業(yè)從導(dǎo)入期進(jìn)入快速成長期,動力電池在中國很快會成為萬億產(chǎn)業(yè),制造難度和規(guī)模大于半導(dǎo)體產(chǎn)業(yè),動力電池制造規(guī)?;⒅悄芑D(zhuǎn)型迫在眉睫。
動力電池制造能力評估指標(biāo)主要有電池制造合格率、材料利用率、人工成本率、WH制造成本、安全指標(biāo)、能耗指數(shù)、運轉(zhuǎn)可靠性等,其中電池制造合格率、材料利用率是關(guān)注重點。
在陽如坤看來,就企業(yè)層面來說,產(chǎn)業(yè)鏈企業(yè)需在電池設(shè)計、制造工藝、生產(chǎn)管理、質(zhì)量管理等不同階段規(guī)范操作,同時采用的電池材料、電池結(jié)構(gòu)沒有明顯缺陷,并且制程工藝的制程能力需大于1.33(合格率大于99.38%)等。
產(chǎn)能需具備規(guī)?;瘲l件,單線產(chǎn)能達(dá)2-4GWh,并且電池制造合格率應(yīng)不低于96%, 材料利用率不低于95%。
不過,動力電池大規(guī)模制造目前依然面臨諸多難點與挑戰(zhàn),這其中既有企業(yè)自身層面的基礎(chǔ)問題、機理不清晰,認(rèn)識不夠、努力不夠等內(nèi)部因素,也有動力電池制造因素眾多,產(chǎn)業(yè)標(biāo)準(zhǔn)不一等外部阻礙。
四大難點
在陽如坤看來,阻礙動力電池規(guī)模制造的最大難點是,基礎(chǔ)問題、機理不清晰,且沒有定量化,因素眾多、系統(tǒng)復(fù)雜,且難以準(zhǔn)確量化。
一是,電池研究中的機理核心問題量化。包括表界面反應(yīng)、SEI膜、結(jié)構(gòu)演化、離子/電子運輸、電荷轉(zhuǎn)移、電壓調(diào)控、應(yīng)力演化等機理問題,通過熱力學(xué)、動力學(xué)、耦合效應(yīng)、尺度效應(yīng)等維度做到量化,而非停留在概念。
二是,動力電池制造過程中安全機理、設(shè)計的結(jié)構(gòu)與尺度、制造模型與數(shù)字化機理三大領(lǐng)域依然存在諸多難點。
其中,安全機理涉及熱失控機理與抑制,鋰枝晶產(chǎn)生、抑制及消除,制造安全管控和使用監(jiān)控、使用安全管理等,如鋰枝晶生長會刺穿隔膜導(dǎo)致短路,死鋰導(dǎo)致電池衰減等。
三是,電池材料制造控制面臨的難題。三元正極材料特性壓實密度大、硬脆;負(fù)極尤其硅碳負(fù)極膨脹20-30%,對電池的影響十分大,還有濕度控制、制造精度、時間控制、材料化學(xué)浸潤、材料物理浸潤及機械設(shè)備浸潤等。
四是,制造安全管控難,包括制造精度、毛刺控制、水份、粉塵、連接制造、極片保護(hù)、極片膨脹制造問題待解。
總結(jié)來說,規(guī)模制造的難點體現(xiàn)在缺乏完整定量理論支撐,只有定性描述,試驗驗證建立科學(xué)經(jīng)驗、規(guī)律,并且制造質(zhì)量要求高、尺寸規(guī)格多,以及安全問題錯綜復(fù)雜等等。
并同時保證來料數(shù)字化及過程數(shù)字化,確保液體、粉體的量、雜質(zhì)、狀態(tài)在線檢測、監(jiān)控,建立漿料、極片、材料的數(shù)字化模型。
三大挑戰(zhàn)
陽如坤定義的痛點是,本該做好,而我們沒能做好,包括認(rèn)識不夠、努力不夠,最終未能達(dá)到目標(biāo)。
當(dāng)前動力電池大規(guī)模制造依然面臨諸多挑戰(zhàn),他認(rèn)為集中在標(biāo)準(zhǔn)化、質(zhì)量及成本等多領(lǐng)域。
其一,標(biāo)準(zhǔn)化,也是大規(guī)模制造的基礎(chǔ)。其程度決定了產(chǎn)品的成本及質(zhì)量合格率,主要涉及領(lǐng)域包括尺寸規(guī)格標(biāo)準(zhǔn)、制造工藝過程、材料標(biāo)準(zhǔn)化等。
當(dāng)前電芯尺寸種類繁多,不同電池類型規(guī)格不一。而對尺寸類型、尺寸數(shù)量、接口等標(biāo)準(zhǔn)化后,不僅可提升合格率,成本有望下降20-30%等。
其二,車規(guī)級動力電池制造質(zhì)量缺失。陽如坤認(rèn)為,動力電池的制造合格率,是動力電池企業(yè)生存的關(guān)鍵,不僅關(guān)系到制造企業(yè)的成本,更關(guān)系到動力電池的安全。
當(dāng)前全球動力電池制造合格率依然處于B級水平,CPK處于1.0到1.33之間,制程會隱含變異和安全隱患,需采用更嚴(yán)格篩選檢測標(biāo)準(zhǔn),需應(yīng)用各種資源及方法將其提升為A級。
目標(biāo)是車規(guī)級動力電池制造標(biāo)準(zhǔn)要求CPK水平做到2.0及以上,保證生產(chǎn)出來的電池都能實現(xiàn)裝車。
其三,裝備野蠻生長。整個新型工藝裝備產(chǎn)生的過程,包括工藝研究、指標(biāo)驗證、樣機開發(fā)、量產(chǎn)制造,目前依然沒有一個統(tǒng)一平臺規(guī)劃整個制造過程。
為此,陽如坤建議設(shè)立一個統(tǒng)一的工藝平臺,并重點圍繞極片制造工藝及裝備研發(fā)平臺、電芯制造工藝與裝備研發(fā)平臺、模組PACK制造工藝與裝備研發(fā)平臺、電池回收工藝與裝備研發(fā)平臺、智能制造體系平臺及固態(tài)電池工藝與裝備平臺等六大領(lǐng)域展開。
他強調(diào),電池制造未來是一個萬億級的巨大產(chǎn)業(yè),裝備應(yīng)當(dāng)?shù)玫匠浞种匾暋⒆鳛楠毩a(chǎn)業(yè)、系統(tǒng)規(guī)劃。
此外還存在用戶的強勢與商業(yè)模式等問題,如電池結(jié)構(gòu)與尺寸過度滿足主機廠要求,導(dǎo)致性能與規(guī)格的失衡。
應(yīng)對策略
陽如坤表示,基于科學(xué)認(rèn)識電池的的制造是解決質(zhì)量、效率、成本的關(guān)鍵,而標(biāo)準(zhǔn)化是產(chǎn)業(yè)的基礎(chǔ),動力電池行業(yè)標(biāo)準(zhǔn)化有30%以上的降本價值空間,同時制造技術(shù)必須與材料、原理深度融合。
而制造及裝備主導(dǎo)的質(zhì)量與成本主要體現(xiàn)在精度合格率、制造安全性及效率成本三大領(lǐng)域。如通過高速化、工序一體化及統(tǒng)計質(zhì)量控制等,F(xiàn)PY合格率目標(biāo)99%,材料利用率97%等,在效率成本上,單機設(shè)備產(chǎn)能1GWh,分段一體化到整線一體化。
圍繞加強制造機理研究、數(shù)字化機理模型、制造及裝備主導(dǎo)的質(zhì)量與成本分析等領(lǐng)域提出了相應(yīng)的應(yīng)對策略。
其一,搞清制造機理及研究數(shù)字化機理模型。過去普遍靠排比試驗確定設(shè)計、制造參數(shù),多次優(yōu)化,達(dá)到逼近真實的情況,存在的問題是耗時長、精確度不夠等。
而基于大數(shù)據(jù)深度學(xué)習(xí)方法建立機理模型,通過大數(shù)據(jù)分析、仿真、優(yōu)化等途徑找出理論值,實現(xiàn)一次性驗證完成,縮短時間,并有效的提升生產(chǎn)效率。
其二,大規(guī)模電池制造結(jié)構(gòu)上,復(fù)合式疊片原理實現(xiàn)高速、不會重片、隔膜、極片不會褶皺。
其三,電芯規(guī)格標(biāo)準(zhǔn)化,通過減少品種、技術(shù)優(yōu)化、性能提升等方式,實現(xiàn)平均材料成本、固定成本攤銷大幅下降。
此外,電芯規(guī)格標(biāo)準(zhǔn)化也能給產(chǎn)業(yè)帶來紅利,當(dāng)前動力電池產(chǎn)能每增加1倍,成本約降低15%。按照這個節(jié)奏初略估算,未來3年總成本可下降30%以上。
其四,構(gòu)建鋰電智能工廠,打造動力電池大數(shù)據(jù)分析與閉環(huán),實現(xiàn)設(shè)備、物料、系統(tǒng)互聯(lián)互通,并設(shè)置大于3500個質(zhì)量數(shù)據(jù)監(jiān)控點,基于二維碼ID(Barcode)雙向追溯系統(tǒng)。
制造主導(dǎo)了動力電池質(zhì)量、安全提升、盈利提升。目前電芯核心制造工序控制指標(biāo)約20個,假設(shè)單工序合格率99.38%,則整體合格率88.3%,核心工序CPK大于1.33。
若單工序合格率提升0.57%,則相應(yīng)的整體合格率達(dá)到99%,核心工序CPK大于1.67。此外,提升電池生產(chǎn)合格率、材料利用率可有效提升動力電池的利潤空間。
-
動力電池
+關(guān)注
關(guān)注
113文章
4534瀏覽量
77654
原文標(biāo)題:十年對話 | 陽如坤:動力電池大規(guī)模制造痛點與難點
文章出處:【微信號:weixin-gg-lb,微信公眾號:高工鋰電】歡迎添加關(guān)注!文章轉(zhuǎn)載請注明出處。
發(fā)布評論請先 登錄
相關(guān)推薦
動力電池自動點焊機:賦能綠色能源,引領(lǐng)智能制造新篇章
動力電池阻抗分析
【干貨】新能源汽車動力電池詳解
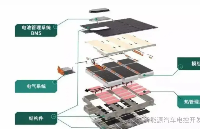
溫度是如何對動力電池的性能造成影響?
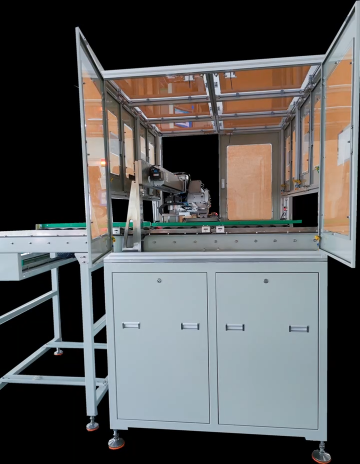
倍加福推出UC-18GS超聲波傳感器,賦能動力電池制造提能增效
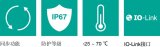
動力電池電壓一般是多少
動力電池和儲能電池的區(qū)別 儲能電池與動力電池電芯有區(qū)別嗎
臨沂臨工新能源科技動力電池PACK項目首臺動力電池下線儀式舉行
動力電池結(jié)構(gòu)與原理介紹
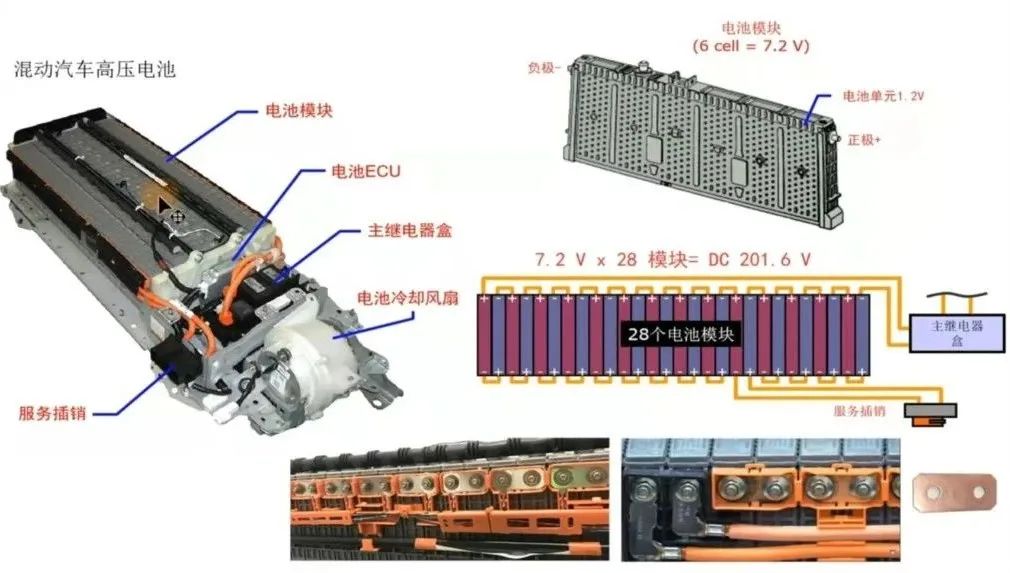
評論