比亞迪“刀片電池”通過結(jié)構(gòu)創(chuàng)新,在成組時(shí)可以跳過“模組”,大幅提高了體積利用率,最終達(dá)成在同樣的空間內(nèi)裝入更多電芯的設(shè)計(jì)目標(biāo)。相較傳統(tǒng)的有模組電池包,“刀片電池”的體積利用率提升了50%以上!
集微網(wǎng)消息,3月29日,備受關(guān)注的比亞迪刀片電池正式揭開面紗。當(dāng)日,比亞迪舉行線上發(fā)布會,首次對外公布了“刀片電池”順利通過“針刺試驗(yàn)”的完整測試視頻。同時(shí)宣布首款搭載“刀片電池”的產(chǎn)品將是旗下全新的C級轎車--漢EV,其綜合工況下的續(xù)航里程達(dá)到605公里,百公里加速3.9秒。
何為“刀片電池”呢?目前新能源車的兩種主流電池,一種是磷酸鐵鋰電池,另一種是三元鋰電池。從材料來說,“刀片電池”也屬主流類型中的一類:磷酸鐵鋰電池,因?yàn)槠渫庑伍L度較長,厚度較薄而因此得名。
隨著用戶對電動車的續(xù)航能力的要求逐漸提升,而在車身底部空間有限的情況下,傳統(tǒng)技術(shù)中的電池組技術(shù)都降低了電池包體內(nèi)部空間的利用率,導(dǎo)致電池包中單體電池的體積之和與包體體積的比值過低,能量密度無法滿足用戶對電動車的續(xù)航能力的需求,其也逐漸成為制約電動車發(fā)展的重要因素。
另外,目前電池包的組裝過程繁瑣、組裝工序復(fù)雜,需要先組裝成電池模組,再將電池模組安裝在包體內(nèi),增加了人力、物力等成本。同時(shí)因需要多次組裝工序,在電池包的組裝過程中,不良率提高、多次組裝增加了電池包出現(xiàn)松動、安裝不牢固的可能性,對電池包的品質(zhì)造成不良影響,并且電池包的穩(wěn)定性下降、可靠性降低。
在這種技術(shù)背景下,“刀片電池”應(yīng)用而生,比亞迪在19年6月21日申請了一項(xiàng)名為“電池包、電動車和儲能裝置”的發(fā)明專利(申請?zhí)枺?01910542987.2),申請人為比亞迪股份有限公司。
根據(jù)目前公開的專利資料,讓我們一起來看看這項(xiàng)“刀片電池”技術(shù)吧。
如上圖所示為傳統(tǒng)技術(shù)中電池包的組成結(jié)構(gòu),電池包10的包體200多由寬度方向橫梁500、長度方向橫梁600分割成多個(gè)電池模組400的安裝區(qū)域。電池模組包括依次排列的多個(gè)單體電池,單體電池排列形成電池陣列,在電池陣列外部設(shè)置有端梁和側(cè)梁,同時(shí)包含端梁和側(cè)梁圍成的容納電池陣列空間。端梁和側(cè)梁通過螺釘或者通過拉桿等其他連接件連接,來對電池陣列進(jìn)行固定。
但是由于螺釘?shù)冉Y(jié)構(gòu)固定在寬度方向橫梁上,浪費(fèi)了空間,同時(shí)因?yàn)榧尤肓寺葆數(shù)冗B接接件,不但增加了產(chǎn)品整體的重量,而且降低了能量密度,使得電池包整體體積的利用率下降。
如上圖為該專利中的“刀片電池”包的剖視圖,可以看到多個(gè)單體電池100設(shè)于包體200內(nèi),包體是用于容納多個(gè)單體電池100的外殼,由托盤210和上蓋220組成,托盤和上蓋構(gòu)造出多個(gè)單體電池的容納空間,因此單體電池可以容納在托盤中,并由上蓋封蓋。
首先我們說說這樣布置的優(yōu)點(diǎn),通過限定單體電池的體積之和與電池包的體積的比例,即將V1/V2≥55%,可以提高電池包的空間利用率,在電池包內(nèi)可以布置更多的單體電池。即在單位空間內(nèi)布置更多的能量提供結(jié)構(gòu),由此可以提高能量密度,從而在不擴(kuò)大占用空間的情況下提高續(xù)航能力。同時(shí)在組裝電池包的過程中,降低成本,并且提高品質(zhì)和電池包的可靠性。
從圖中也可以看到,電池本體的長度遠(yuǎn)大于其寬度,并且在電池包內(nèi)沿第一方向布置,沿第二方向排列,長單體排列并放置在電池包中,形成體積利用率在55%以上的電池包,提高了空間利用率,提高能量密度和使用該電池包的電動車?yán)m(xù)航能力。
從下圖的爆炸圖中可以更加清楚的看到其結(jié)構(gòu)構(gòu)成。
單體電池100的長度延伸在電池包10的整個(gè)寬度方向B上,即沿電池包的寬度方向B,單體電池由包體200一側(cè)延伸到另一側(cè),單體電池的長度在電池包的寬度方向B上進(jìn)行填充。由于包體在方向B上無法放置兩個(gè)及以上的單體電池,因此單體電池的長度方向上的兩端可以配合于方向B上相對的兩側(cè)壁,例如進(jìn)行包體的固定。
由此看來,包體內(nèi)部無需寬度方向橫梁和長度方向橫梁,直接通過連接的單體電池承擔(dān)中間梁的作用,極大的簡化了包體的結(jié)構(gòu),且減少了中間梁占用的空間以及單體電池的安裝結(jié)構(gòu)占用的空間,從而進(jìn)一步提高空間利用率,以進(jìn)一步提高續(xù)航能力。
最后我們來看看這個(gè)電池包應(yīng)用在實(shí)際的車輛上時(shí)的場景吧。
如上圖所示為該電池包應(yīng)用于實(shí)際車輛上的渲染圖,電池包體200可以包括與車身配合連接的車用托盤210,形成與車身配合容納并承載單體電池100的結(jié)構(gòu),這個(gè)車用托盤用于容納并安裝單體電池。當(dāng)單體電池安裝到車用托盤中后,該車用托盤可以通過緊固件安裝到車身上,例如懸掛在電動車的底盤上,并起到容納和承重作用。
我們知道在電動車的開發(fā)中,對于單體電池的電壓要求是事先確定好的,這使得單體電池的體積成定值在使用相同化學(xué)體系材料的基礎(chǔ)時(shí),其單體電池中所容納的材料量是一定的。因此,通過設(shè)計(jì)電池本體的長度L和寬度H的比值,可在一定體積下使電池包進(jìn)行合理的扁長化。
這樣一方面利于在電池包內(nèi)的整體排布、提高電池包的空間利用率、擴(kuò)大電池包的能量密度,同時(shí)進(jìn)而增強(qiáng)電池包的續(xù)航能力,另一方面能夠保證單體電池具有足夠大的散熱面積,能夠及時(shí)將內(nèi)部的熱量傳導(dǎo)至外部,防止熱量在內(nèi)聚集,從而匹配較高的能量密度,支持續(xù)航能力的提升。
以上就是比亞迪的“刀片電池”技術(shù),比亞迪“刀片電池”通過結(jié)構(gòu)創(chuàng)新,在成組時(shí)可以跳過“模組”,大幅提高了體積利用率,最終達(dá)成在同樣的空間內(nèi)裝入更多電芯的設(shè)計(jì)目標(biāo)。相較傳統(tǒng)的有模組電池包,“刀片電池”的體積利用率提升了50%以上!在大幅提升系統(tǒng)質(zhì)量能量密度以及體積能量密度的同時(shí),也使得電池系統(tǒng)的復(fù)雜度大幅下降,由此也帶來了更高的產(chǎn)品穩(wěn)定性和更低的故障率,給消費(fèi)者帶來了兼具高安全以及高品質(zhì)的新能源汽車!
-
比亞迪
+關(guān)注
關(guān)注
19文章
2311瀏覽量
54204 -
電池
+關(guān)注
關(guān)注
84文章
10590瀏覽量
129966
發(fā)布評論請先 登錄
相關(guān)推薦
比亞迪2025年將推出新一代刀片電池
蘋果與比亞迪曾秘密合作研發(fā)刀片電池技術(shù)
蘋果與比亞迪共同研發(fā)長續(xù)航電池技術(shù)
比亞迪第二代刀片電池研發(fā)創(chuàng)新,能量密度攀升至190Wh/kg
比亞迪發(fā)布全新刀片電池雙層大巴底盤,即將進(jìn)駐倫敦
刀片電池創(chuàng)新技術(shù)引領(lǐng)的能源革命速銳得揭秘比亞迪海豹核心數(shù)據(jù)
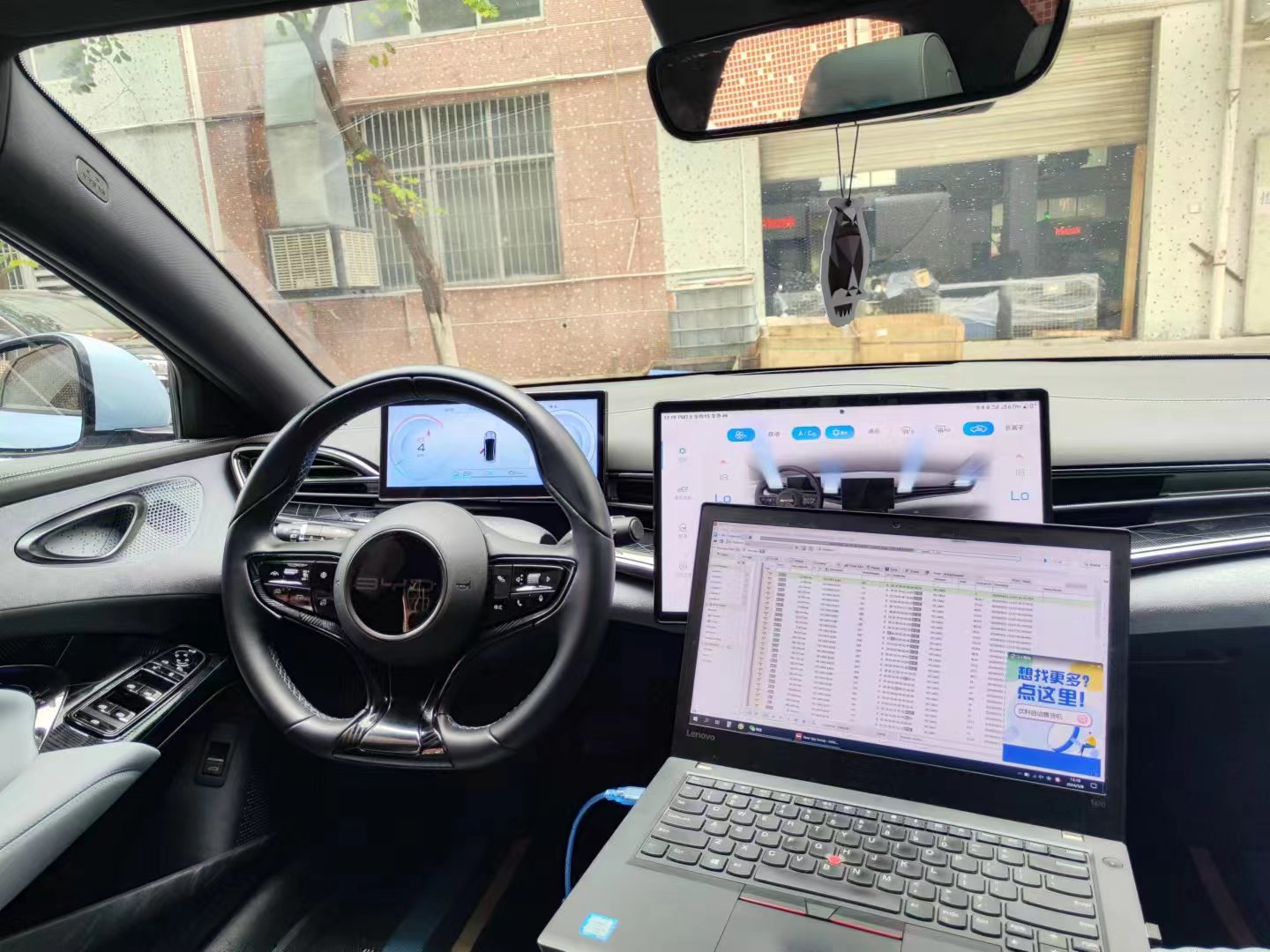
蔚來子品牌被曝引入比亞迪刀片電池
刀片電池和三元鋰電池對比
磷酸鋰電池就是刀片電池嗎
刀片電池的原理、特點(diǎn)及其在電動汽車領(lǐng)域的應(yīng)用前景
比亞迪取得電池外殼專利
比亞迪取得電池和電池包專利
比亞迪斬獲百億大單:再創(chuàng)行業(yè)新紀(jì)錄
激光焊接機(jī)焊接剃須刀片的技術(shù)工藝
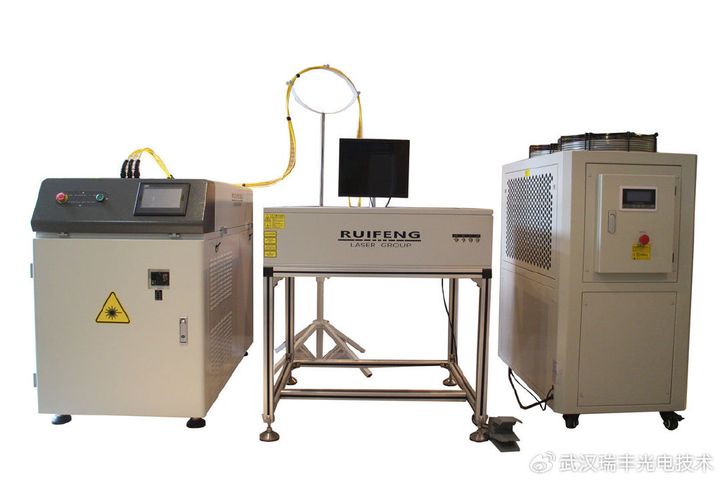
評論