晶片級封裝(WLP)用單獨的焊點將集成電路(IC)與印刷電路板(PCB)連接在一起。IC面朝下安裝,這種技術(shù)不需要任何綁定線或引線,有別于其他球珊陣列、引腳封裝和壓層CSP封裝技術(shù),是IC與PCB之間電感最小的封裝形式,這也是它最主要的優(yōu)點。另外,這種封裝大大縮小了封裝尺寸,縮短了制造周期,并增強了熱傳導(dǎo)特性。
本文描述了Maxim WLP的PCB布局和安裝流程,注意,這里給出的只是基本的PCB布板設(shè)計和安裝指南,并不保證用戶最終產(chǎn)品的可靠性,用戶還需要對其最終產(chǎn)品的使用壽命和可靠性進(jìn)行驗證。
封裝結(jié)構(gòu)
Maxim封裝圖WLP焊點的相互連接是在硅晶片的基板上構(gòu)建起來的,晶片電路的表面覆蓋了一層BCB (Benzocyclobutene)樹脂薄膜,這層薄膜可以減緩?fù)裹c的機械應(yīng)力,并為裸片表層提供電氣隔離。過孔成像在BCB膜上,與IC綁定焊盤提供電氣連接。UBM層(焊點下的金屬化層)覆蓋在過孔上方,BCB層的另一個作用是焊料掩膜,定義回流焊球的直徑和位置。目前封裝I/O的設(shè)計包含2至55個可焊接點,如圖1所示。標(biāo)準(zhǔn)的焊點合金是易于溶解的Sn63Pb37、“高鉛含量”Pb95Sn5和“無鉛”Sn96.5Ag3Cu0.5,單個WLP焊點的結(jié)構(gòu)如圖2所示,元件背面是裸露的硅片,帶有一個光刻的引腳1標(biāo)記和標(biāo)示碼。雙金屬層分區(qū)工藝(RDL)允許從外圍綁定盤移至其他凸點矩陣模板。
圖1. 通用的2焊點CSP、55焊點倒裝芯片、4 x 4 UCSP?
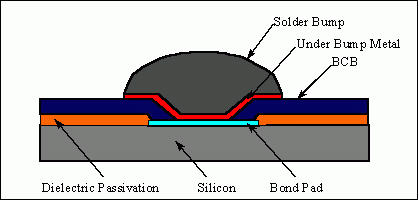
圖2. 通用WLP結(jié)構(gòu)圖
WLP載帶
WLP采用卷帶(T&R)形式包裝,卷帶規(guī)格符合EIA-481和EIA-746&747標(biāo)準(zhǔn)。圖3給出了典型的卷帶結(jié)構(gòu),所有Maxim的倒裝芯片和CSP器件采用浮凸載帶包裝,帶有壓封膠粘(PSA)封帶,卷軸為7英寸或13英寸。也可以根據(jù)用戶需求提供Surftape?或Surftape-Lite?卷帶及其他尺寸的卷軸。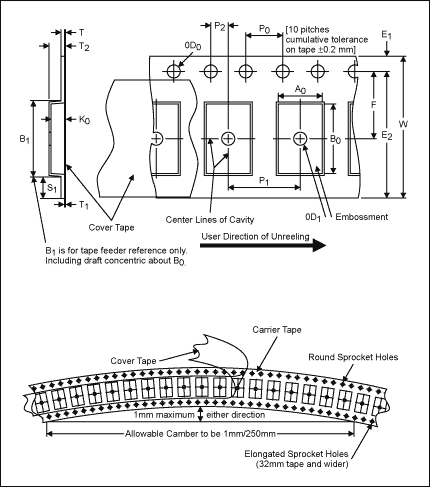
圖3. 典型WLP載帶結(jié)構(gòu)
焊球在卷帶內(nèi)面朝下放置,卷帶的每個包裝內(nèi)引腳1的位置保持一致。封帶的總剝離強度在0.1N至1.0N (10gf至102gf標(biāo)定刻度)。
PCB布局
PCB設(shè)計需要符合IPC-A-600和IPC-6012A標(biāo)準(zhǔn),標(biāo)準(zhǔn)的FR4 (Tg = 120°C至150°C)覆銅層壓板可能適用于峰值溫度達(dá)240°C的全部回流焊流程;對于峰值溫度在240°C至270°C范圍的回流焊工藝,建議使用高性能FR4或BT層壓板(Tg = 170°C值185°C)。對于Maxim的焊點合金材料,無電鍍鎳浸金(ENIG)是PCB銅基板焊盤表面拋光的首選電鍍處理方法(在最小100微英寸/最大300微英寸厚度的Ni上覆蓋最小3微英寸/最大20微英寸厚度的Au),銅焊盤上也可以使用有機表面保護(hù)(OSP)層。對于所有球柵陣列封裝的焊點,非焊錫掩膜法(NSMD)焊盤優(yōu)于焊錫掩膜法(SMD)焊盤。焊盤之間建議使用焊盤掩膜法,利用焊盤掩膜設(shè)計清空0.002"至0.003"的焊盤邊緣。采用層疊焊點回流(易溶的Sn-Pb和無鉛)處理時,焊盤尺寸通常比最大焊點直徑小20至25%,保證焊接深度達(dá)到最大元件焊點高度。采用非層疊焊點回流(高鉛含量)處理時,焊盤尺寸通常比最大焊點孔徑大0.002"至0.004",對于焊點沉浸度和可接受度可以利用X射線檢查。對于“高鉛含量”焊盤設(shè)計的唯一例外是Maxim的2焊點CSP封裝(圖1),對于這種封裝形式,建議使用1:1最大焊點孔徑的焊盤,以防止回流焊時由于管芯的傾斜造成焊點的連接?;迥0蹇梢允菆A形的或方形的,焊盤和連線應(yīng)該對稱排列,以避免回流焊中產(chǎn)生偏離中心的拉力。為防止虛焊,每個NSMD焊盤應(yīng)該由一條線連接,引線寬度不要超出所連接的NSMD焊盤孔徑的1/2。
應(yīng)謹(jǐn)慎選擇WLP元件在PCB上的位置,如果相鄰元件具有較高的封裝外形,則會遮蔽WLP封裝,避免潛在的錯誤連接。
PCB安裝流程
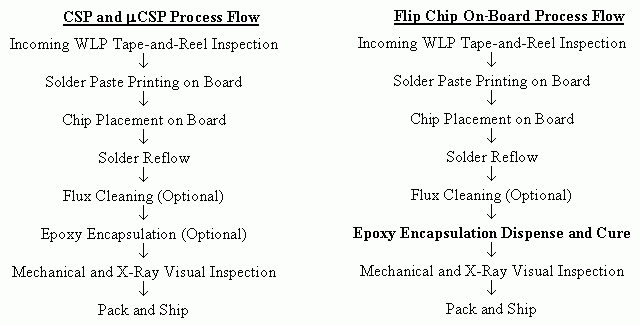
焊膏印刷工藝
焊膏印刷是與PCB裝配產(chǎn)出率相關(guān)的最重要的工藝。必須檢查焊膏厚度、焊盤覆蓋百分比和與焊盤的對準(zhǔn)精度。- 選擇焊膏:應(yīng)使用第3類(錫球尺寸為25至45微米)或第四類(20至38微米)的錫膏,選擇哪一類取決于模板開孔的尺寸。建議使用低鹵化物含量(< 100ppm)和免清洗的、J-STD-004指定的ROL0/REL0樹脂助焊劑,可以省去回流裝配后的清洗工作。
- 制作模板:使用激光切割不銹鋼箔片加電拋光技術(shù)或鎳金屬電鑄成形的制作工藝。鎳電鑄成形工藝雖然比較昂貴,但是對于從超小的開孔進(jìn)行焊膏沉積的過程最具可重復(fù)性。這種方法還有一個優(yōu)點,可以形成任何用戶所需要的厚度。具有梯形截面的模板開口有助于焊膏的釋放。
- 焊錫模板開口設(shè)計:對于激光切割SS使用縱橫比為≥ 0.75的孔徑;對于鎳金屬電鑄成形,使用縱橫比為≥ 0.66的孔徑,方圓形(25微米角徑)開口有助于焊膏沉積的重復(fù)性??讖娇v橫比定義為孔徑開口面積除以孔徑邊緣的面積。也可以使用偏離基板焊盤的X、Y坐標(biāo)軸,使每個焊點的粘貼沉積度最強,焊點之間的影響最小,如圖4、圖5所示。
- 焊錫模板的厚度:焊錫模板的厚度應(yīng)該不超過焊點的高度,必須達(dá)到實際孔徑設(shè)計所對應(yīng)的縱橫比的要求。在采用混合技術(shù)的PCB裝配中,如果這些模板要求與其他SMT元件的要求相沖突,可以使用符合IPC-7525設(shè)計標(biāo)準(zhǔn)的低一級的模板工藝或雙印刷模板工藝。
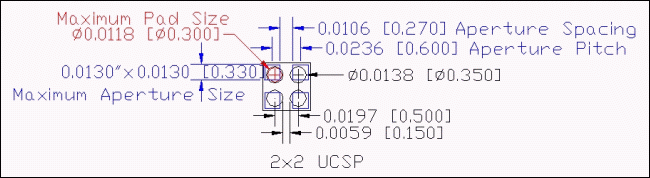
圖4. 2 x 2 UCSP孔徑焊點的模板設(shè)計范例
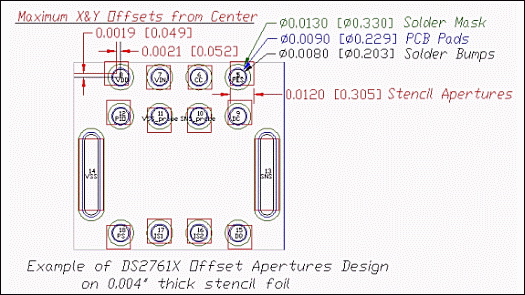
圖5. DS2761X倒裝芯片孔徑焊點的模板設(shè)計范例
元件的放置
Maxim的所有WLP硅片均采用真空吸頭從載帶包裝中取出,并貼放到PCB上,這一過程使用標(biāo)準(zhǔn)的自動精確定位IC拾取/貼放機完成,在4σ下的貼放精度≤ 0.050mm。拾取/貼放系統(tǒng)需要一個固定的卷帶送料器。使用機械中心定位方案的系統(tǒng)是不可取的,因為它極有可能損壞硅封裝。- 拾取/貼放系統(tǒng)的貼放精度依賴于它使用的是封裝外形中心與球柵陣列中心的視覺定位技術(shù)。排列精度要求較低時,封裝外形中心對準(zhǔn)可以用于高速貼放;球柵陣列中心排列能夠在貼放速率較低時實現(xiàn)最大的對準(zhǔn)精度。封裝外形對準(zhǔn)與球柵陣列對準(zhǔn)的中心位置座標(biāo)X、Y最大可相差±0.035mm。
- 焊點貼放位置與PCB焊盤中心的最大允許偏移在X、Y方向均為±0.100mm,這樣可以保證回流過程的沉浸力使焊點自動對準(zhǔn)中心。
- 所有硅裸片封裝的接觸力應(yīng)該控制在≤ 2牛頓(204gf)以內(nèi)。精確的分布力度應(yīng)該周期性地利用經(jīng)過校準(zhǔn)的測壓表進(jìn)行測試。
- 需要使用2D X射線測量并驗證貼放精度。
焊膏回流
Maxim的WLP符合工業(yè)標(biāo)準(zhǔn)回流焊處理流程,我們選擇氮惰性氣體下的回流焊接。- 推薦使用壓迫氣體對流回流爐,這樣可以控制整個過程中的熱傳導(dǎo)率。
- WLP焊點能夠經(jīng)受三個標(biāo)準(zhǔn)回流焊周期。
- 推薦使用2D X射線或3D X射線分層攝影法作為回流焊之后取樣檢驗,檢查焊結(jié)短路、焊錫不足、漏焊和潛在開路等問題。-00
- 易溶解的Sn-Pb焊膏回流到易溶解的Sn-Pb或“高鉛含量”焊點的WLP:標(biāo)稱峰值溫度是220°C ±15°C,高于183°C熔點溫度的持續(xù)時間是60 ±15秒,由機械裝置內(nèi)部的熱電偶測量和驗證回流爐的溫度特性。典型的易溶Sn-Pb焊膏回流焊溫度曲線如圖6所示。峰值溫度上限建議用于易溶Sn-Pb焊膏回流到“高鉛含量”焊點的WLP中,以增強焊點接口處金屬間的綁定層。
圖6. 易溶焊膏的典型溫度特性曲線
- “無鉛”焊膏回流焊:標(biāo)稱峰值溫度為250°C ±10°C,高于217°C至221°C熔點溫度的時間是60 ±15秒,由機械裝置內(nèi)部的熱電偶測量和驗證回流爐的溫度特性。對于Sn96.5Ag3.5和SnAg(2-4)Cu(0.5-0.8)合金的典型“無鉛”焊膏回流焊溫度曲線如圖7所示。
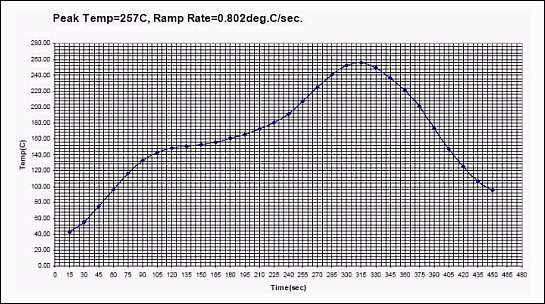
圖7. Sn96.5Ag3.5和Sn-Ag-Cu“無鉛”焊膏的典型溫度特性曲線
元件更換
WLP的更換方法與典型的球柵陣列(BGA)更換方法相同。- 使用局部加熱取走WLP元件,加熱溫度曲線與最初的回流溫度曲線類似,使用對流熱氣體噴嘴和底部預(yù)熱的方法。
- 當(dāng)噴嘴溫度超過焊點熔點時,使用塑膠鑷子或者真空工具取走有缺陷的元件。
- 必須使用溫度可控的烙鐵除去焊盤上的殘留錫料。
- 將凝膠狀助焊劑涂到焊盤上。
- 用真空拾取工具拾起新元件并利用視覺定位貼放夾具將其精確地放置在電路板上。
- 用相同的對流熱氣體噴嘴和底部預(yù)熱的方法對元件進(jìn)行回流焊接,采用最初的回流溫度曲線。
環(huán)氧包封(板上安裝倒裝芯片所必需的)
為了提高焊點連接的機械強度,加速熱循環(huán)(ATC)能力,可以在安裝了的CSP電路增加環(huán)氧填充和/或Glob-Top包封,使測試可靠性比沒有環(huán)氧包封的元件提高10倍。這種“包封效應(yīng)”可以提高芯片與基板之間環(huán)氧粘合劑的機械連接機制的性能。環(huán)氧包封還為潮濕的環(huán)境以及化學(xué)污染提供了一層物理屏障。另外,環(huán)氧填充還可以阻止焊膏在相鄰焊點之間蔓延,Glob-Top環(huán)氧層可以防護(hù)WLP的邊緣和背面硅層的機械連接處不被損壞。材質(zhì)的考慮
- 固化環(huán)氧劑的線性擴充系數(shù)(CTE)與焊接點、Sn63Pb37 (21ppm/°C) - Pb95Sn5 (29ppm/°C)、65%至70%硅填充料一致。
- 較高的玻璃化轉(zhuǎn)變溫度(Tg)改善了所有產(chǎn)品保存期內(nèi)的溫度需求(最小固化環(huán)氧Tg ≥ 基板Tg; FR4 = 120°C至135°C, BT/強化FR4 = 170°C至185°C)。
- 支持BCB鈍化和LPI焊錫掩膜。
- 低Ionics, 總鹵化物低于100ppm。
- 低粘連性、快速回流率,回流能力可達(dá)到50mm (2mil)最小間隙尺寸。
- 低扭曲度,低收縮率。
- 低吸潮性。
可接受的視覺核查標(biāo)準(zhǔn)
- 環(huán)氧填充材料必須連續(xù)地環(huán)繞整個管芯的四周構(gòu)成一個正倒角,不允許有空隙。這個正倒角與管芯的底層邊沿有一個最小連接高度,連接高度不要超出管芯頂層邊沿。另外,倒角必須為正的潤濕角,使管芯邊沿與外界隔離。
- 環(huán)氧表層從視覺上必須保持均勻,沒有間隙和針孔。
- 環(huán)氧層不要粘接到任何裝配電氣插頭的表面。
- 可以利用垂直掃描聲波顯微鏡(C-SAM)成像作為填充空隙檢測的分析方法,如圖9、圖10所示。
- 測量液化環(huán)氧分布重量的增加可作為監(jiān)視SPC的簡單方法。
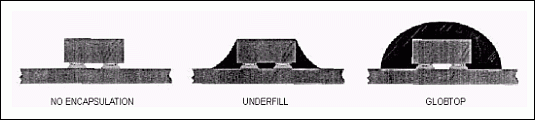
圖8. 環(huán)氧包封選項
圖9. 垂直掃描聲波顯微鏡(C-SAM)成像的例子
圖10. 垂直掃描聲波顯微鏡(C-SAM)成像的例子
包裝與運輸
為了防止損壞WLP元件,包裝與運輸WLP裝配部件時必需小心,尤其是在不使用環(huán)氧包封安裝WLP元件的情況下。必需評估并嚴(yán)格遵守裝有WLP元件的PCB包裝規(guī)格。UCSP是Maxim Integrated Products, Inc.的商標(biāo)。
評論