本文主要簡單介紹探討接觸孔工藝制造流程。以55nm接觸控工藝為切入點進(jìn)行簡單介紹。
在集成電路制造領(lǐng)域,工藝流程主要涵蓋前段工藝(Front End of Line,F(xiàn)EOL)與后段工藝(Back End of Line,BEOL)。前段工藝主要用于制作晶體管,而后段工藝則專注于實現(xiàn)晶體管之間的金屬布線互連。其中,接觸孔工藝作為前后段工藝銜接的關(guān)鍵環(huán)節(jié),其作用是連接晶體管有源區(qū)與第一金屬層。在大規(guī)模生產(chǎn)的成套工藝流程里,接觸孔工藝一旦出現(xiàn)缺陷,常常會成為影響良率的關(guān)鍵因素。在該工藝模塊中,接觸電阻(Contact Resistance,Rc)和套刻對準(zhǔn)(Overlay)是需要重點關(guān)注的兩個核心部分。
電路信號的傳輸速度取決于電阻與電容的乘積,因此,在接觸孔工藝中,降低接觸電阻成為了一個至關(guān)重要的問題。針對這一問題,主要可從接觸孔材料、接觸孔關(guān)鍵尺寸等方面展開考量。
接觸孔工藝簡介
在接觸孔材料方面,用金屬鎳硅化物替代以往的金屬鈷硅化物,能夠獲得更小的接觸電阻;采用金屬鎢替換之前的金屬鋁作為接觸孔的填充材料,不僅可擁有更強的抗電遷移能力,還能實現(xiàn)更小的電阻率以及更高的臺階覆蓋率;在不影響填充能力的前提下,減小具有高阻特性的黏合層 Ti/TiN 的厚度,同樣可以達(dá)到降低電阻的目的。
在接觸孔關(guān)鍵尺寸方面,隨著技術(shù)節(jié)點逐漸縮小,多晶硅到接觸孔的距離越來越短。減小接觸孔的關(guān)鍵尺寸,有助于減少多晶硅和接觸孔之間橋聯(lián)的問題,然而,關(guān)鍵尺寸的減小會致使接觸孔與多晶硅及有源區(qū)的接觸面積變小,進(jìn)而增加接觸電阻。與此同時,降低層間介質(zhì)的厚度也有助于降低電阻。所以,需要探尋合適的工藝窗口,以平衡這些因素之間的關(guān)系。光刻工藝中的套刻對準(zhǔn)步驟,對接觸孔工藝有著較大的影響,尤其是在靜態(tài)隨機存取存儲器(Static Random - Access Memory,SRAM)區(qū)域。靜態(tài)隨機存取存儲器依靠提高晶體管密度來增加緩存容量,其設(shè)計可不遵循最小設(shè)計規(guī)則,這給工藝帶來了極大的挑戰(zhàn)。在靜態(tài)隨機存取存儲器區(qū)域,當(dāng)接觸孔與柵極套刻對準(zhǔn)時,若出現(xiàn)較大偏差,就容易導(dǎo)致接觸孔和柵極之間發(fā)生橋聯(lián)短路,進(jìn)而使器件失效。當(dāng)接觸孔與有源區(qū)套刻對準(zhǔn)時,部分有源區(qū)上的接觸孔與有源區(qū)重疊,一旦產(chǎn)生對準(zhǔn)偏差,在后續(xù)刻蝕過程中就會刻蝕掉一部分淺溝槽隔離(STI)上的氧化物,從而增加漏電,加大器件功耗。
接觸孔工藝流程
55nm 接觸孔工藝選用金屬鎢作為填充材料,在器件與第一層金屬之間采用介質(zhì)材料,以此形成層間介質(zhì)層(Inter - Layer Dielectric,ILD),從而實現(xiàn)電性隔離,并降低金屬與襯底之間的寄生電容。55nm 接觸孔工藝的具體步驟如下:
清洗:
在進(jìn)行化學(xué)氣相沉積(Chemical Vapour Deposition,CVD)之前,需對晶圓表面進(jìn)行清洗,以確保其表面潔凈。
沉積具有拉應(yīng)力的氮化物層:
如下圖所示,利用化學(xué)氣相沉積法沉積一層氮化物,這層氮化物既作為后續(xù)刻蝕接觸孔的刻蝕停止層,同時還能引入應(yīng)力。在早期工藝中,對器件的工作速率要求相對較低,所以在這一步驟采用的是氧化物加氮化物的組合,主要目的是實現(xiàn)電性隔離。加入氧化層,一方面是將其作為刻蝕停止層;另一方面是因為氮化物與硅襯底的晶格常數(shù)和熱膨脹系數(shù)不匹配,氮化物與硅直接接觸會產(chǎn)生較大應(yīng)力,容易致使硅襯底出現(xiàn)裂紋、大量位錯或缺陷。因此,需要在襯底上生長一層氧化物,以緩解氮化物與硅襯底之間的應(yīng)力。隨著技術(shù)節(jié)點不斷縮小,對 <100> 晶向的硅片施加拉應(yīng)力,能夠顯著提升其溝道的電子遷移率,進(jìn)而提高器件的驅(qū)動電流。所以,在這一步驟中去除了氧化物,以充分發(fā)揮氮化物的應(yīng)力作用,通過精準(zhǔn)控制沉積工藝的各項指標(biāo)來調(diào)控應(yīng)力大小,有效提升 NMOS 器件的工作速率。
生長具有拉應(yīng)力的氮化物
沉積磷硅玻璃:
如下圖所示,運用高密度等離子體化學(xué)氣相沉積工藝(High Density Plasma Chemical Vapour Deposition,HDPCVD)沉積磷硅玻璃(PSG),將其作為第一層層間介質(zhì)層。磷硅玻璃是在未摻雜硅酸鹽玻璃(Undoped Silicate Glass,USG)中摻磷形成的,它能夠有效吸收固定離子(主要為 Na)并阻擋水汽。在該步驟中,主要從間隙填充能力(Gap Fill)、等離子體損傷、薄膜均勻性這三個方面對高密度等離子體化學(xué)氣相沉積工藝進(jìn)行優(yōu)化。
生長磷硅玻璃層
沉積 TEOS:
如下圖所示,采用等離子體增強化學(xué)氣相沉積(PECVD)工藝生長正硅酸乙酯(TEOS),將其作為第二層層間介質(zhì)層。為解決高密度等離子體化學(xué)氣相沉積工藝中等離子體密度過大、薄膜均勻性欠佳、沉積時間過長的問題,55nm 工藝采用 PSG + TEOS 的組合作為層間介質(zhì)。
生長正硅酸乙酯層
CMP:
如下圖所示,借助化學(xué)機械研磨(Chemical Mechanical Polishing,CMP)來調(diào)整層間介質(zhì)層的高度,實現(xiàn)表面平坦化。在研磨氧化物的過程中,主要通過調(diào)節(jié)研磨時間來達(dá)到指定的介質(zhì)層高度,最后清洗去除表面的研磨液。
化學(xué)機械研磨調(diào)整高度
沉積氧化物:
如下圖所示,利用等離子體增強化學(xué)氣相沉積形成一層氧化物,該氧化物可作為光刻的抗反射涂層,以減少反射,降低駐波效應(yīng),同時還能修復(fù)化學(xué)機械研磨工藝對表面造成的損傷。
生成等離子體增強的氧化物
光刻:
如下圖所示,通過光刻膠旋涂、前烘、對準(zhǔn)與曝光、后烘、顯影、堅膜等一系列步驟,將掩模上的圖形轉(zhuǎn)移到光刻膠上。非接觸孔區(qū)域保留光刻膠,接觸孔區(qū)域的光刻膠則通過顯影去除,后續(xù)將通過刻蝕工藝形成接觸孔。
光刻形成接觸孔圖案
刻蝕、清洗:
如下圖所示,采用 CF?等氣體形成的等離子體轟擊晶圓,去除無光刻膠覆蓋區(qū)域的介質(zhì)層,形成高深寬比的接觸孔。在形成接觸孔后,通過干法刻蝕和濕法刻蝕去除光刻膠和抗反射涂層,隨后將晶圓放入清洗槽中清洗,最后在物理氣相沉積(Physical Vapor Deposition,PVD)金屬前,用氬離子濺射去除表面的氧化物。
刻蝕形成接觸控圖案
沉積黏合層(Glue Layer,GL):
如下圖所示,利用物理氣相沉積工藝濺射沉積 Ti 和 TiN 層。Ti/TiN 層主要有兩方面作用:一方面,由于鎢與氧化物的黏附性較差,如果直接將鎢填充進(jìn)氧化物,形成的介質(zhì)層中鎢層極易脫落,因此需要 Ti/TiN 作為黏附層,防止鎢層脫落;另一方面,Ti/TiN 層作為阻擋層,能夠有效防止鎢擴(kuò)散至器件有源區(qū)內(nèi),對器件性能造成損害。
沉積Ti/TiN層
沉積鎢層:
如下圖所示,采用化學(xué)氣相沉積工藝沉積金屬鎢,填充接觸孔。這個過程主要分為兩步,第一步是利用六氟化鎢(WF?)、硅烷(SiH?)和乙硼烷(B?H?)在一定溫度和壓力下反應(yīng)沉積一層鎢籽晶層,第二步是利用六氟化鎢(WF?)和氫氣(H?)沉積大量的鎢。
沉積鎢層
CMP:
如下圖所示,利用化學(xué)機械研磨去除表面多余的鎢層和 Ti/TiN 層,防止鎢殘留導(dǎo)致不同區(qū)域的接觸孔短路,同時也使表面平坦化。正硅酸乙酯層是化學(xué)機械研磨的停止層,考慮到工藝的容忍度,當(dāng)終點檢測器檢測到正硅酸乙酯的成分時,會再進(jìn)行一定時間的研磨,確保鎢沒有殘留。
-
檢測器
+關(guān)注
關(guān)注
1文章
878瀏覽量
47940 -
工藝
+關(guān)注
關(guān)注
4文章
626瀏覽量
29023
原文標(biāo)題:接觸孔工藝簡介
文章出處:【微信號:bdtdsj,微信公眾號:中科院半導(dǎo)體所】歡迎添加關(guān)注!文章轉(zhuǎn)載請注明出處。
發(fā)布評論請先 登錄
相關(guān)推薦
PCB線路板的Via hole塞孔工藝
PCB導(dǎo)電孔塞孔工藝及原因詳解
PCB線路板導(dǎo)電孔塞孔工藝的實現(xiàn)
點鍍盲孔填充工藝流程簡介
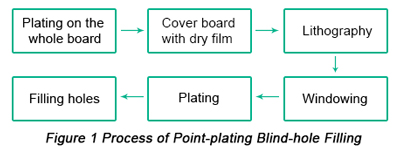
PCB設(shè)計的導(dǎo)電孔塞孔工藝解析
Via hole塞孔工藝全面解析
通孔回流焊工藝原理_通孔回流焊接工藝的優(yōu)缺點
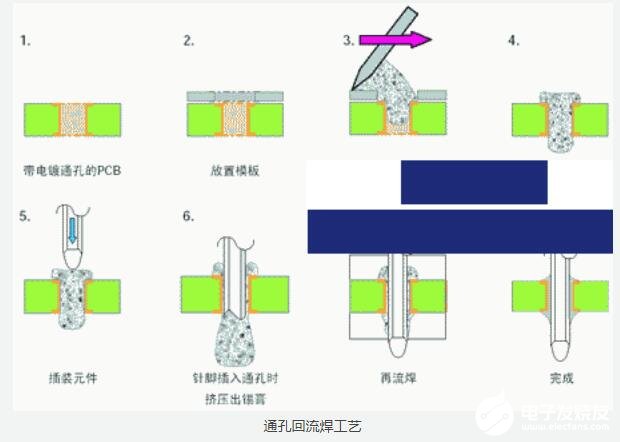
何時使用通孔技術(shù)工藝?
PCB導(dǎo)電孔塞孔工藝的實現(xiàn)
PCB線路板導(dǎo)電孔塞孔工藝的實現(xiàn)
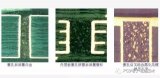
互連/接觸/通孔/填充分別代表了什么
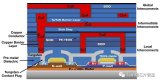
評論