一、引言
在競爭日益激烈的現(xiàn)代制造業(yè)中,注塑成型機作為核心生產設備,其高效運行和精細管理對企業(yè)的生存與發(fā)展至關重要。然而,眾多工廠在注塑成型機的管理上,面臨數據采集、傳輸、遠程監(jiān)控等一系列難題,嚴重阻礙了企業(yè)的數字化與智能化升級進程。深控技術研發(fā)的 “不需要點表的工業(yè)網關” 為這些問題提供了全面且創(chuàng)新的解決方案,助力工廠實現(xiàn)注塑成型機的全方位高效管理。
二、工廠現(xiàn)存問題
數據采集難題
傳統(tǒng)點表方式繁瑣:傳統(tǒng)的數據采集高度依賴詳細的點表配置,確定每個數據點的采集參數和規(guī)則需耗費大量人力與時間,效率低下且易出錯。
設備兼容性差:不同品牌和型號的注塑成型機接口和協(xié)議差異大,導致數據采集設備難以兼容多種設備,極大增加了數據采集的復雜性與成本。
數據傳輸問題
網絡不穩(wěn)定:工廠內部復雜的網絡環(huán)境存在信號干擾、網絡擁堵等問題,致使數據傳輸時經常出現(xiàn)丟包、延遲現(xiàn)象,嚴重影響數據的實時性與準確性。
傳輸安全隱患:數據傳輸過程面臨網絡攻擊、數據泄露等風險,傳統(tǒng)傳輸方式缺乏有效的加密和認證機制,無法保障數據安全。
遠程監(jiān)控困境
監(jiān)控界面不友好:現(xiàn)有的遠程監(jiān)控系統(tǒng)界面復雜、操作繁瑣,管理人員難以及時獲取關鍵信息,影響監(jiān)控效率與決策及時性。
缺乏智能預警功能:無法實時監(jiān)測注塑成型機的異常狀態(tài)并進行智能預警,設備故障不能及時發(fā)現(xiàn)和處理,增加了停機時間與生產損失。
工藝管理困境
工藝參數記錄困難:難以精確記錄和追溯注塑成型過程中的各項工藝參數,導致工藝優(yōu)化缺乏數據支持。
工藝一致性難以保證:不同批次生產中,工藝參數難以保持一致,影響產品質量穩(wěn)定性。
設備維護與模具保護難題
設備維護不及時:缺乏對設備運行狀態(tài)的實時監(jiān)測,無法提前預測設備故障,導致設備維護不及時,增加維修成本。
模具保護不到位:無法實時監(jiān)測模具的使用情況和狀態(tài),模具在生產過程中易出現(xiàn)損壞,影響生產進度和產品質量。
生產進度管理問題
信息不透明:管理人員難以實時掌握生產進度,無法及時發(fā)現(xiàn)生產過程中的延誤和瓶頸。
生產計劃調整困難:缺乏實時數據支持,生產計劃難以根據實際生產情況進行及時調整。
深圳市深控信息技術有限公司
三、深控技術 “不需要點表的工業(yè)網關” 解決方案
不需要點表的數據采集
深控技術的工業(yè)網關運用先進的自適應技術,能自動識別和采集注塑成型機的各類數據,無需繁瑣的點表配置。這不僅簡化了數據采集流程,降低了部署成本和時間,還提升了數據采集的準確性與穩(wěn)定性。
高效穩(wěn)定的數據傳輸
多網絡接入:支持多種網絡接入方式,如以太網、4G/5G 等,可根據工廠實際網絡環(huán)境靈活選擇,確保數據傳輸的穩(wěn)定性與可靠性。
安全加密傳輸:采用先進的加密算法和認證機制,對傳輸的數據進行加密處理,防止數據泄露與篡改,保障數據傳輸安全。
便捷智能的遠程監(jiān)控
可視化監(jiān)控界面:提供簡潔直觀的可視化監(jiān)控界面,以圖形化方式展示注塑成型機的運行狀態(tài)、生產數據等信息,管理人員可輕松獲取所需信息,快速做出決策。
智能預警功能:內置智能算法,實時監(jiān)測注塑成型機的運行參數,當發(fā)現(xiàn)異常情況時,及時通過短信、郵件等方式發(fā)送預警信息,提醒管理人員及時處理,減少設備故障與生產損失。
全面的工藝管理
工藝參數實時記錄:精確記錄注塑成型過程中的各項工藝參數,如溫度、壓力、速度等,為工藝優(yōu)化提供詳實的數據支持。
工藝一致性控制:通過對歷史工藝數據的分析和比對,幫助企業(yè)實現(xiàn)工藝參數的標準化和一致性控制,提高產品質量穩(wěn)定性。
設備維護與模具保護
設備狀態(tài)實時監(jiān)測:實時監(jiān)測注塑成型機的關鍵部件運行狀態(tài),通過數據分析預測設備故障,提前制定維護計劃,實現(xiàn)預防性維護,降低設備維修成本。
模具狀態(tài)監(jiān)測與保護:實時監(jiān)測模具的開合模次數、溫度、壓力等參數,及時發(fā)現(xiàn)模具的異常情況,采取相應的保護措施,延長模具使用壽命,保障生產順利進行。
精準的生產進度管理
實時生產進度跟蹤:通過對注塑成型機的生產數據進行實時采集和分析,管理人員可以實時掌握每臺設備的生產進度,及時發(fā)現(xiàn)生產過程中的延誤和瓶頸。
生產計劃智能調整:根據實時生產數據,系統(tǒng)自動分析生產進度與計劃的偏差,為生產計劃的調整提供科學依據,實現(xiàn)生產計劃的智能優(yōu)化。
四、客戶案例
案例一:[公司名稱 A]
客戶背景:[公司名稱 A] 是一家大型注塑制品生產企業(yè),擁有數十臺不同品牌和型號的注塑成型機。此前,數據采集依賴人工記錄,監(jiān)控靠現(xiàn)場巡查,工藝管理缺乏數據支持,設備維護不及時,生產進度管理混亂。
解決方案實施:部署深控技術 “不需要點表的工業(yè)網關”,實現(xiàn)了對所有注塑成型機的數據自動采集和實時傳輸。利用可視化監(jiān)控界面,管理人員能實時掌握設備運行狀態(tài)、工藝參數和生產進度。智能預警功能及時發(fā)現(xiàn)并處理了多次設備異常和工藝偏差情況。通過對設備狀態(tài)的實時監(jiān)測,提前進行設備維護,模具保護措施有效降低了模具損壞率。
實施效果:生產效率提高了 20%,設備故障率降低了 30%,產品不良率降低了 15%,人工成本顯著降低,生產進度管理更加精準,企業(yè)競爭力大幅提升。
案例二:[公司名稱 B]
客戶背景:[公司名稱 B] 是一家專注于精密注塑模具制造的企業(yè),對注塑成型機的生產質量和工藝參數要求極高。但因數據采集和傳輸問題,工藝管理粗放,設備維護滯后,生產進度難以把控。
解決方案實施:采用深控技術的工業(yè)網關,解決了數據采集和傳輸難題。通過對工藝參數的實時記錄和分析,實現(xiàn)了工藝的優(yōu)化和一致性控制。設備狀態(tài)監(jiān)測系統(tǒng)提前發(fā)現(xiàn)設備潛在故障,模具保護機制有效延長了模具壽命。生產進度管理系統(tǒng)讓管理人員能實時調整生產計劃。
實施效果:產品不良率降低了 20%,設備維修成本降低了 25%,模具更換次數減少了 30%,生產效率提高了 18%,生產計劃的執(zhí)行準確率達到 95% 以上。
案例三:[公司名稱 C]
客戶背景:[公司名稱 C] 是一家新興的注塑產品制造企業(yè),工廠規(guī)模較小,預算有限,但對數字化轉型需求迫切。傳統(tǒng)方案成本高、實施難度大,工藝管理、設備維護和生產進度管理缺乏有效手段。
解決方案實施:深控技術的 “不需要點表的工業(yè)網關” 以其簡單易用、成本低廉的優(yōu)勢,為 [公司名稱 C] 提供了高性價比的解決方案。實現(xiàn)了注塑成型機的遠程監(jiān)控和管理,工藝管理得到加強,設備維護更加科學,生產進度一目了然。
實施效果:企業(yè)以較低成本實現(xiàn)數字化轉型,生產效率提高了 15%,設備故障率降低了 20%,產品質量得到顯著提升,生產管理更加高效有序,為企業(yè)快速發(fā)展奠定了基礎。
五、結論
深控技術研發(fā)的 “不需要點表的工業(yè)網關” 為注塑成型機的物聯(lián)網應用帶來了全方位的革新。通過解決數據采集、傳輸、遠程監(jiān)控等問題,以及實現(xiàn)工藝管理、設備維護、模具保護、生產進度管理等功能,幫助工廠實現(xiàn)了生產過程的數字化、智能化管理。以上客戶案例充分證明了該解決方案的卓越成效,為注塑行業(yè)的數字化轉型提供了有力的支持與成功范例。
審核編輯 黃宇
-
物聯(lián)網
+關注
關注
2909文章
44743瀏覽量
374528 -
數據采集
+關注
關注
39文章
6160瀏覽量
113761 -
網關
+關注
關注
9文章
4524瀏覽量
51218
發(fā)布評論請先 登錄
相關推薦
機械加工行業(yè)數據采集物聯(lián)網解決方案 —— 基于深控技術研發(fā)的不需要點表的工業(yè)網關
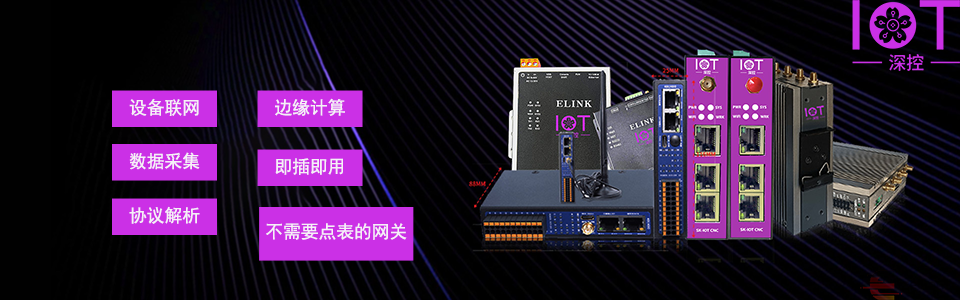
深控技術研發(fā)的 “不需要點表的工業(yè)網關” 在 CNC 采集方面的應用
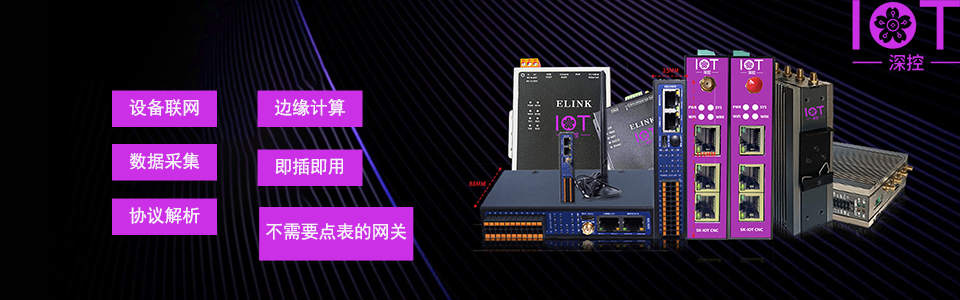
深控技術 “不需要點表的工業(yè)網關” 在機械加工中的解決方案及實施案例
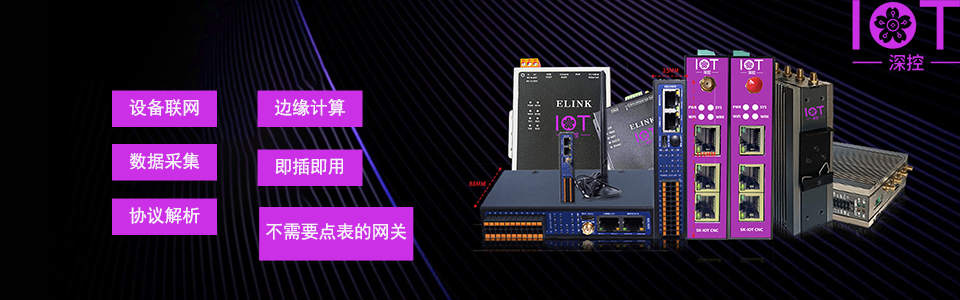
基于 “不需要點表的工業(yè)網關” 的工業(yè)自動化設備遠程監(jiān)控解決方案
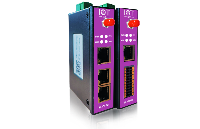
“不需要點表的工業(yè)網關”如何實現(xiàn)松下FPG-C32T2H數據采集和遠程維護的物聯(lián)網解決方案
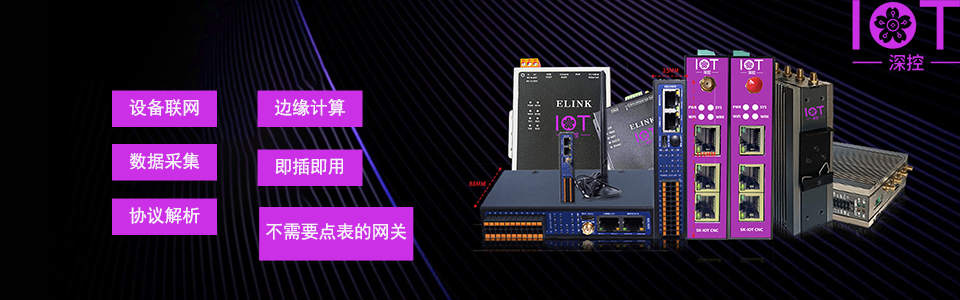
評論