芯片封裝隨著制程的越來越先進(jìn),其生產(chǎn)制造工藝也開始從宏觀制程轉(zhuǎn)向微縮制程,量產(chǎn)工藝也越來越半導(dǎo)體制程化。
而在2D平面封裝越來越難以適應(yīng)更大的帶寬傳輸容量,以及更高的互聯(lián)速度性能要求時(shí)。2.5D3D獨(dú)立立體封裝,以及2.5D3D混和的3.5D封裝,以及高速銅互聯(lián)技術(shù),成為了行業(yè)的主流研究方向。
玻璃基板在3D封裝中的重要性源自其獨(dú)特的物理和化學(xué)特性,這些特性使其在先進(jìn)封裝技術(shù)中具有顯著的優(yōu)勢。
以下是玻璃基板在3D封裝中的關(guān)鍵重要性:
1. 尺寸穩(wěn)定性
低熱膨脹系數(shù):玻璃基板的熱膨脹系數(shù)(CTE)通常低于硅(Si)或有機(jī)基板,這意味著在高溫制造和操作過程中,玻璃基板的尺寸變化較小,減少了熱應(yīng)力和變形,提高了封裝的可靠性。
2. 平面度和均勻性
優(yōu)異的平面度:玻璃基板可以提供非常高的平面度和均勻性,這對于多層堆疊和微米級精度的對準(zhǔn)至關(guān)重要。高平面度支持更高密度的互連和更好的電氣性能。
3. 電氣性能
介電常數(shù)低:玻璃具有較低的介電常數(shù),這有助于減少信號傳輸中的損耗,提升高頻性能,尤其在高速數(shù)據(jù)傳輸和射頻應(yīng)用中。
絕緣性能:玻璃基板的絕緣性能優(yōu)于有機(jī)基板,提供更好的電氣隔離,減少漏電流。
4. 光學(xué)特性
透明性:對于需要透光的應(yīng)用,如光學(xué)傳感器或光通信器件,玻璃的透明特性允許光在封裝內(nèi)自由傳輸,減少光學(xué)損失。
5. 耐化學(xué)性
化學(xué)穩(wěn)定性:玻璃對各種化學(xué)物質(zhì)具有較高的耐受性,這在封裝過程中或在惡劣環(huán)境中使用時(shí)非常重要,延長封裝的壽命。
6. 機(jī)械強(qiáng)度
機(jī)械性能:雖然玻璃在傳統(tǒng)上被認(rèn)為易碎,但現(xiàn)代玻璃基板通過特殊處理(如化學(xué)強(qiáng)化)可以獲得增強(qiáng)的機(jī)械強(qiáng)度,適合于需要機(jī)械穩(wěn)定性的應(yīng)用。
7. 環(huán)境適應(yīng)性
抗?jié)裥院湍蜔嵝裕翰AЩ鍖Νh(huán)境條件的變化,如濕度和溫度變化,表現(xiàn)出較好的穩(wěn)定性,減少封裝的劣化風(fēng)險(xiǎn)。
應(yīng)用優(yōu)勢
多芯片模塊(MCM)和系統(tǒng)級封裝(SiP):玻璃基板可以承載多個(gè)芯片或組件,提供更高的集成度和性能。
3D堆疊:玻璃的物理特性使其在3D堆疊技術(shù)中成為理想的選擇,支持更高密度的互連和更復(fù)雜的封裝結(jié)構(gòu)。
光電子集成:在光通信和光學(xué)傳感器封裝中,玻璃基板的透明性和低損耗特性使其成為首選材料。
挑戰(zhàn)
成本和制造復(fù)雜性:雖然玻璃基板在性能上優(yōu)于傳統(tǒng)基板,但其生產(chǎn)成本較高,且需要專門的制造設(shè)備和工藝。
加工難度:玻璃的加工,如鉆孔、切割等,需要先進(jìn)的技術(shù)以保持精度和不損壞基板。
玻璃基板在3D封裝中的應(yīng)用正在逐漸增長,因?yàn)槠淠芴峁┑男阅芴嵘谖磥?a target="_blank">電子產(chǎn)品的微型化、多功能化和高性能需求中變得越來越重要。隨著技術(shù)進(jìn)步和成本優(yōu)化,玻璃基板的應(yīng)用前景將更加廣闊。
硅基板和玻璃基板在3D封裝中的應(yīng)用對比
硅基板和玻璃基板在3D封裝和其他半導(dǎo)體應(yīng)用中各有其優(yōu)缺點(diǎn)。以下是對比分析了這兩種材料在關(guān)鍵特性上的異同:
1. 熱膨脹系數(shù) (CTE)
硅基板:硅的熱膨脹系數(shù)約為2.6 ppm/°C,較高,導(dǎo)致在高溫下容易產(chǎn)生熱應(yīng)力。
玻璃基板:玻璃基板(如硼硅酸鹽玻璃)的熱膨脹系數(shù)通常低于1 ppm/°C,比硅小得多,提供更好的尺寸穩(wěn)定性。
2. 平面度和均勻性
硅基板:硅晶圓通常具有非常高的平面度,但可能在制造過程中出現(xiàn)微小的翹曲。
玻璃基板:玻璃的平面度可以更優(yōu),尤其是經(jīng)過拋光的玻璃基板,提供更好的平面度和均勻性。
3. 電氣性能
硅基板:硅本身是半導(dǎo)體材料,具有較高的介電常數(shù),可能會增加信號傳輸?shù)膿p耗。
玻璃基板:玻璃具有低介電常數(shù)(比如3.8 vs.硅的11.7),減少電氣信號的損耗,適用于高頻應(yīng)用。
4. 光學(xué)特性
硅基板:硅對可見光不透明,但在紅外光范圍內(nèi)有透光性。
玻璃基板:大多數(shù)玻璃是透明的,適用于光學(xué)通信和傳感應(yīng)用。
5. 化學(xué)穩(wěn)定性
硅基板:硅在某些化學(xué)環(huán)境中較為穩(wěn)定,但不耐強(qiáng)酸如HF。
玻璃基板:玻璃通常對化學(xué)物質(zhì)有更高的耐受性,特別是對于酸和堿。
6. 機(jī)械強(qiáng)度
硅基板:硅晶圓雖然堅(jiān)硬,但脆性較大,在加工過程中容易破損。
玻璃基板:通過化學(xué)強(qiáng)化處理,玻璃可以獲得較高的機(jī)械強(qiáng)度,雖然仍比硅脆,但更適合一些需要機(jī)械穩(wěn)定性的應(yīng)用。
7. 加工工藝
硅基板:加工工藝成熟,適合半導(dǎo)體制造,如CMP(化學(xué)機(jī)械拋光)和TSV(硅通孔)。
玻璃基板:加工相對復(fù)雜,特別是在形成通孔(TGV)或精密加工時(shí),但技術(shù)也在不斷進(jìn)步。
8. 成本
硅基板:由于生產(chǎn)規(guī)模大且工藝成熟,成本相對較低。
玻璃基板:初始成本較高,因?yàn)橹圃旃に嚭驮O(shè)備的要求更高,但隨著技術(shù)進(jìn)步和大規(guī)模生產(chǎn),成本也在降低。
應(yīng)用場景
硅基板:廣泛用于傳統(tǒng)的IC制造、MEMS、和TSV技術(shù),因?yàn)樗募庸すに囈呀?jīng)高度優(yōu)化。
玻璃基板:在高頻通信、光電子、3D封裝、和需要高平面度和低熱膨脹的應(yīng)用中越來越受歡迎。
總結(jié)
優(yōu)勢:
硅基板:加工工藝成熟,成本效益高,廣泛應(yīng)用于半導(dǎo)體領(lǐng)域。
玻璃基板:優(yōu)異的電氣性能、光學(xué)透明性、尺寸穩(wěn)定性,特別適合新興的高性能和多功能封裝需求。
挑戰(zhàn):
硅基板:在高頻應(yīng)用中可能存在信號損耗,更高的熱膨脹系數(shù)在3D堆疊時(shí)可能導(dǎo)致問題。
玻璃基板:成本較高,加工難度大,目前的市場普及度不如硅基板。
隨著3D封裝技術(shù)的發(fā)展和對高性能、多功能集成的需求增加,玻璃基板的應(yīng)用場景可能會進(jìn)一步擴(kuò)大,但硅基板仍將在許多應(yīng)用中保持其重要地位。
玻璃基板預(yù)埋蝕刻工藝
玻璃蝕刻工藝是一種用于在玻璃表面創(chuàng)建復(fù)雜圖案、紋理或透明度變化的方法,廣泛應(yīng)用于裝飾、光學(xué)器件制造、微流控設(shè)備、半導(dǎo)體工業(yè)等領(lǐng)域。以下是對玻璃蝕刻工藝的詳細(xì)介紹:
工藝類型
濕法蝕刻:
化學(xué)蝕刻:
酸蝕刻:最常見的方法使用氫氟酸(HF)或其混合物(如HF和硝酸)來蝕刻玻璃。氫氟酸能夠與玻璃中的SiO?反應(yīng),形成可溶性氟硅酸鹽。
掩模技術(shù):使用光刻膠或金屬膜作為掩模,通過光刻技術(shù)在玻璃上形成圖案,然后進(jìn)行蝕刻。
干法蝕刻:
等離子體蝕刻(PE):使用等離子體,如氟化物等離子體(CF?,SF?),通過反應(yīng)性離子蝕刻(RIE)或深反應(yīng)性離子蝕刻(DRIE)來蝕刻玻璃。
激光蝕刻:利用激光能量進(jìn)行局部熔化或蒸發(fā)玻璃,適用于高精度圖案或通孔的制造。
濕法蝕刻詳細(xì)步驟
玻璃清洗:
使用溶劑和酸洗去除玻璃表面的污染物和油脂。
掩模制作:
光刻:在玻璃上涂布光刻膠,通過光掩模曝光和顯影形成圖案。
金屬掩模:也可以通過濺射或蒸發(fā)沉積金屬膜,然后通過光刻或激光刻蝕金屬形成圖案。
蝕刻:
準(zhǔn)備蝕刻溶液:氫氟酸常以5-40%的濃度使用,具體濃度依據(jù)蝕刻速度和所需深度調(diào)整。
浸泡或噴涂:將玻璃放入蝕刻溶液中或用蝕刻溶液噴涂玻璃表面,控制時(shí)間來達(dá)到所需的蝕刻深度。
去除掩模:
使用適當(dāng)?shù)娜軇ㄈ绫蚬饪棠z去除劑)或酸去除光刻膠或金屬掩模。
后處理:
用去離子水或高純度水多次清洗玻璃,去除所有蝕刻溶液殘留。
干燥,通常用氮?dú)獯蹈伞?/p>
干法蝕刻詳細(xì)步驟
玻璃清洗:
與濕法蝕刻相同,確保玻璃表面潔凈。
掩模制作:
采用與濕法蝕刻類似的光刻技術(shù)或直接使用金屬掩模。
等離子體蝕刻:
設(shè)備設(shè)置:將玻璃放入等離子體蝕刻機(jī)中,設(shè)置好氣體(如CF?或SF?)、壓力、功率和時(shí)間。
蝕刻:通過等離子體的物理和化學(xué)作用蝕刻玻璃。
掩模去除:
使用化學(xué)方法或等離子清洗去除掩模。
后處理:
清洗和干燥玻璃。
關(guān)鍵點(diǎn)
蝕刻速率控制:根據(jù)需要的深度和精度,精確控制蝕刻時(shí)間、溶液濃度或等離子體參數(shù)。
圖案精確度:掩模的質(zhì)量和蝕刻的均勻性決定了最終圖案的精確度。
安全性:特別是濕法蝕刻使用氫氟酸時(shí),必須嚴(yán)格遵守安全操作規(guī)程,保護(hù)操作人員和環(huán)境。
環(huán)境影響:處理蝕刻廢液時(shí)需進(jìn)行中和處理,防止污染。
成本和效率:濕法蝕刻成本較低但可能對環(huán)境影響大;干法蝕刻更環(huán)保但設(shè)備成本高。
玻璃蝕刻工藝需要根據(jù)應(yīng)用場景選擇合適的方法,以達(dá)到所需的工藝效果。
玻璃基板TGV工藝
玻璃基板TGV(Through Glass Via)工藝涉及多個(gè)復(fù)雜的步驟,每一步都需要精細(xì)的控制以保證最終產(chǎn)品的性能和可靠性。
以下是對TGV工藝更詳細(xì)的步驟描述:
1. 玻璃基板準(zhǔn)備
材料選擇:選用高純度、低熱膨脹系數(shù)的玻璃,如硼硅酸鹽玻璃或熔融石英。
清洗:
使用超聲波清洗去除表面污垢。
化學(xué)清洗(如酸洗)去除金屬離子和有機(jī)物。
用去離子水多次漂洗以確保潔凈度。
2. 通孔形成
激光鉆孔:
選擇激光類型:常用飛秒激光或皮秒激光,因?yàn)樗鼈兡芴峁└呔?,減少熱效應(yīng)。
參數(shù)設(shè)置:控制激光能量、脈沖頻率、光束聚焦等,以獲得理想的通孔深寬比和表面質(zhì)量。
多次掃描:可能需要多次激光掃描以達(dá)到所需的深度。
干法蝕刻(如DRIE):
設(shè)備準(zhǔn)備:設(shè)置等離子體蝕刻機(jī)。
掩模制作:使用光刻技術(shù)在玻璃上制作掩模圖案。
蝕刻過程:通過交替進(jìn)行的離子轟擊和聚合物沉積,逐層蝕刻玻璃直到形成通孔。
3. 通孔壁處理
清洗:
用溶劑或化學(xué)清洗劑去除通孔內(nèi)任何殘留的碎屑或污染物。
使用等離子清洗進(jìn)一步清潔通孔壁。
活化:
通過化學(xué)浸泡(如稀酸溶液)或等離子處理激活通孔壁,增強(qiáng)后續(xù)金屬層的附著力。
4. 種子層沉積
濺射:
靶材選擇:常用鈦或鉻。
濺射條件:控制功率、氣壓和濺射時(shí)間,形成均勻的薄種子層。
化學(xué)鍍:
配制鍍液:如使用硫酸-氟化氫酸溶液進(jìn)行鈦的化學(xué)鍍。
控制溫度和pH:以確保鍍層均勻。
5. 導(dǎo)電層沉積
電鍍:
鍍液準(zhǔn)備:配置高純度銅電鍍液。
電鍍條件:設(shè)置電流密度、溫度、pH值等參數(shù)以填充通孔。
電鍍時(shí)間:根據(jù)通孔深度和直徑調(diào)整時(shí)間,確保充分填充。
化學(xué)鍍銅:
使用還原劑:如甲醛或氫硼化鈉進(jìn)行銅的無電沉積。
鍍液管理:控制溶液的穩(wěn)定性和純度。
6. 表面處理
平坦化:
化學(xué)機(jī)械拋光(CMP):去除多余的金屬并平整表面。
清洗:去除任何殘留的化學(xué)物質(zhì)。
7. 保護(hù)層和鈍化
沉積鈍化層:
使用PECVD(等離子增強(qiáng)化學(xué)氣相沉積)沉積SiO?或Si?N?。
也可以使用濺射或蒸發(fā)方法沉積金屬氧化物或聚合物層。
測試和驗(yàn)證:
導(dǎo)電性測試:檢查通孔的電導(dǎo)通性。
可靠性測試:如溫度循環(huán)測試,確保通孔在不同環(huán)境下的性能。
關(guān)鍵控制點(diǎn)
精確的激光或蝕刻控制以確保通孔一致性。
嚴(yán)格的清潔和活化過程以增強(qiáng)粘附力。
鍍層均勻性和完整性,避免空洞或不連續(xù)。
熱管理以防止玻璃應(yīng)力裂紋。
每個(gè)步驟都涉及到詳細(xì)的參數(shù)控制和質(zhì)量檢測,以確保TGV工藝的高效和高質(zhì)量執(zhí)行。
玻璃基板銅互聯(lián)再布線層工藝流程和參數(shù)
玻璃基板銅互聯(lián)再布線層工藝是制造高性能電子器件的關(guān)鍵技術(shù)之一,涉及一系列精密的加工步驟和嚴(yán)格的工藝參數(shù)控制。以下是該工藝的詳細(xì)流程和相關(guān)參數(shù)的全面介紹。
工藝流程
1. 表面處理
目的:在玻璃基板上制備一層反向應(yīng)力層,如氮化硅、碳化硅或氮化鈦,以提高后續(xù)金屬層與基板的結(jié)合力。
材料選擇:應(yīng)考慮材料在電鍍過程中是否與銅產(chǎn)生不良反應(yīng)。
2. 光刻膠涂布
方法:通過懸涂或噴涂在反向應(yīng)力層上涂布光刻膠。
參數(shù):光刻膠的厚度影響曝光和顯影效果,通常在幾微米到十幾微米之間。
3. 曝光和顯影
過程:形成帶有溝槽的光刻膠圖案。
參數(shù)控制:
曝光劑量:根據(jù)光刻膠的靈敏度和分辨率要求,一般在幾十到幾百毫焦耳每平方厘米。
顯影時(shí)間:幾十秒到幾分鐘,顯影溫度控制在20-30攝氏度。
4. 種子層制備
方法:采用磁控濺射在光刻膠溝槽中制備金屬種子層(如鈦、鉻、銅或它們的共濺射層)。
厚度:通常在200-500nm,影響后續(xù)電鍍過程的質(zhì)量。
5. 電鍍銅
過程:在種子層上電鍍一層厚銅。
參數(shù):
厚度:一般在3.6-5微米。
電鍍條件:電流密度0.1-1安培每平方分米,溫度20-30攝氏度。
6. 去除光刻膠
方法:使用剝離劑去除光刻膠,形成高精度銅走線。
注意事項(xiàng):避免對銅走線造成損害。
7. 表面處理和檢測
步驟:清洗、干燥及檢測,包括尺寸測量、導(dǎo)電性測試和外觀檢查,確保產(chǎn)品質(zhì)量。
工藝參數(shù)
光刻膠厚度:影響曝光和顯影效果。
曝光劑量:決定圖案的精確度。
顯影時(shí)間:控制圖案的形成。
種子層厚度:影響電鍍質(zhì)量的基礎(chǔ)。
電鍍銅厚度:決定銅走線的性能。
溫度和時(shí)間控制:貫穿整個(gè)工藝過程,確保穩(wěn)定性和產(chǎn)品質(zhì)量。
玻璃基板銅互聯(lián)再布線層工藝的復(fù)雜性和精細(xì)性要求對每個(gè)步驟的工藝參數(shù)進(jìn)行嚴(yán)格控制。通過優(yōu)化這些參數(shù),可以生產(chǎn)出高質(zhì)量的銅互聯(lián)再布線層,滿足高性能電子器件的需求。同時(shí),材料的兼容性、環(huán)境控制、設(shè)備精度以及持續(xù)的工藝優(yōu)化都至關(guān)重要。此外,中間檢測和質(zhì)量控制也是確保生產(chǎn)高質(zhì)量產(chǎn)品的關(guān)鍵步驟。
玻璃基板銅互聯(lián)再布線層電鍍銅工藝
電鍍銅工藝是一種常見的表面處理技術(shù),用于在金屬或非金屬基材上沉積一層銅鍍層,以提高其導(dǎo)電性、耐腐蝕性或裝飾效果。以下是電鍍銅工藝的一些關(guān)鍵細(xì)節(jié):
工藝流程
預(yù)處理:
清洗:去除基材表面的污垢、油脂和氧化物,通常使用溶劑、酸洗或超聲波清洗。
活化:通過化學(xué)或電化學(xué)手段活化基材表面,以改善鍍層的附著力,常用硫酸或鹽酸。
鍍液配制:
電鍍銅溶液的選擇取決于所需的鍍層特性。常見的鍍液包括:
硫酸銅鍍液:適用于一般電鍍,經(jīng)濟(jì)且操作簡便。
氰化鍍液:用于需要高光潔度和均勻性的應(yīng)用,但由于其毒性現(xiàn)已較少使用。
焦磷酸鹽鍍液:適用于需要精確控制鍍層厚度的場合。
檸檬酸鹽鍍液:提供良好的覆蓋能力,特別適合不規(guī)則表面的鍍覆。
鍍液的pH值、溫度、銅離子濃度和添加劑(如光亮劑、整平劑)都需要嚴(yán)格控制。
電鍍過程:
電流密度:根據(jù)基材和所需鍍層厚度調(diào)整,通常在0.1到1 A/dm2之間。
電鍍時(shí)間:控制鍍層厚度,時(shí)間從幾分鐘到幾小時(shí)不等。
溫度:通常在20-30攝氏度之間,確保鍍液穩(wěn)定和鍍層質(zhì)量。
后處理:
漂洗:用清水或去離子水徹底清洗以去除殘留的化學(xué)物質(zhì)。
干燥:避免水斑形成,可以使用熱風(fēng)或真空干燥。
封閉或鈍化:可能需要進(jìn)行后續(xù)處理以增強(qiáng)耐腐蝕性或光亮度。
工藝細(xì)節(jié)
鍍層質(zhì)量:
鍍層應(yīng)均勻、光亮、無孔隙,具有良好的導(dǎo)電性和較高的耐腐蝕性。
控制鍍液成分和電鍍參數(shù)是關(guān)鍵。
覆蓋性:
特別是在復(fù)雜形狀的基材上,要確保鍍液能夠均勻覆蓋所有表面。
電鍍效率:
通過調(diào)整添加劑或電流密度來優(yōu)化電鍍效率,減少能耗。
環(huán)境和安全:
電鍍過程中需要考慮環(huán)境影響,特別是廢水處理和化學(xué)品管理,以符合環(huán)保要求。
維護(hù):
定期檢測和調(diào)整鍍液成分,防止污染和鍍液老化,確保鍍層的一致性。
電鍍銅工藝雖然看似簡單,但其細(xì)節(jié)管理決定了最終產(chǎn)品的質(zhì)量。每個(gè)步驟需要精確控制,從預(yù)處理到后處理,每一環(huán)節(jié)都對鍍層性能有直接影響。掌握這些細(xì)節(jié),可以大大提升產(chǎn)品的功能性和外觀質(zhì)量。
玻璃基板銅互聯(lián)再布線層電鍍金工藝
電鍍金工藝是一種高端的表面處理技術(shù),用于增強(qiáng)材料的抗腐蝕能力、提高導(dǎo)電性、或者為產(chǎn)品增添高檔的美觀外觀。電鍍金工藝涉及到多種類型的金鍍層,如硬金、軟金、純金等,每種都有其獨(dú)特的用途和特性。以下是電鍍金工藝的詳細(xì)步驟和關(guān)鍵細(xì)節(jié):
工藝流程
預(yù)處理:
清洗:用溶劑、堿液或酸液清洗基材,去除油脂、氧化物等污染物。
活化:常用稀酸(如鹽酸)浸泡基材,激活表面以增強(qiáng)金鍍層的附著力。
除鈍:如果基材表面有鈍化層,可能需要用除鈍劑進(jìn)行處理。
鍍液準(zhǔn)備:
金鍍液:常用的金鍍液包括:
氰化金鍍液:提供高純度的金鍍層,但由于其毒性,使用受到限制。
無氰金鍍液:如磷酸鹽體系或硫酸鹽體系,更環(huán)保,逐漸成為主流。
酸性金鍍液:用于硬金鍍層,耐磨性高。
pH值、溫度、金濃度:根據(jù)具體鍍液體系調(diào)整,通常pH在4-7之間,溫度在30-60攝氏度。
添加劑:包括光亮劑、整平劑等,控制金鍍層的外觀和性能。
電鍍過程:
電流密度:一般在0.5到5 A/dm2之間,具體取決于鍍層厚度和硬度要求。
鍍層厚度:從幾微米到幾十微米不等,根據(jù)應(yīng)用場景選擇。
時(shí)間控制:根據(jù)所需鍍層厚度調(diào)整電鍍時(shí)間,通常幾分鐘到幾十分鐘。
后處理:
漂洗:用去離子水多級漂洗,去除鍍液殘留。
干燥:熱風(fēng)、真空或自然風(fēng)干,防止水斑。
鈍化或封閉:某些應(yīng)用下可能需要進(jìn)一步處理以增強(qiáng)耐腐蝕性或光亮度。
關(guān)鍵細(xì)節(jié)
鍍層質(zhì)量:
鍍層應(yīng)光亮、均勻、無氣孔,具有良好的導(dǎo)電性和耐腐蝕性。
鍍液的純度和穩(wěn)定性直接影響鍍層質(zhì)量。
鍍層硬度:
通過選擇合適的鍍液(如酸性金鍍液)可以得到硬金鍍層,提高耐磨性。
軟金鍍層用于需要高導(dǎo)電性和延展性的場合。
覆蓋性:
確保金鍍液能均勻覆蓋復(fù)雜形狀的基材,必要時(shí)使用輔助電極或特殊夾具。
環(huán)保和安全:
由于金的毒性和昂貴性,特別是氰化物使用,需嚴(yán)格控制廢液排放,符合環(huán)保標(biāo)準(zhǔn)。
成本控制:
金價(jià)昂貴,電鍍金過程中需要精確控制鍍層厚度,避免浪費(fèi)。
維護(hù):
定期檢測鍍液成分和性能,調(diào)整添加劑以維持鍍層的一致性和質(zhì)量。
電鍍金工藝要求高精度和高質(zhì)量控制,涉及到的每個(gè)步驟都需嚴(yán)謹(jǐn)操作。通過優(yōu)化預(yù)處理、電鍍參數(shù)和后處理,可以獲得高品質(zhì)的金鍍層,廣泛應(yīng)用于電子、首飾、裝飾等領(lǐng)域。
金電鍍液配制
金鍍液種類根據(jù)其化學(xué)成分、使用場景和鍍層特性可以分為多種類型。以下是一些常見的金鍍液分類:
1. 氰化金鍍液
成分:含有氰化鉀(KCN)或氰化鈉(NaCN)作為絡(luò)合劑,金以氰化金鉀(KAu(CN)?)或氰化金鈉(NaAu(CN)?)形式存在。
特點(diǎn):
提供高純度和光亮度的金鍍層。
覆蓋性好,適用于復(fù)雜形狀的零件。
由于氰化物的毒性,現(xiàn)在的使用受到嚴(yán)格限制。
2. 無氰金鍍液
成分:使用非氰化物的絡(luò)合劑,如:
磷酸鹽體系:磷酸金鉀或磷酸金鈉,環(huán)保性較好。
硫酸鹽體系:硫酸金鉀或硫酸金鈉。
檸檬酸體系:檸檬酸金鉀或檸檬酸金鈉,適用于高覆蓋性需求。
特點(diǎn):
環(huán)保,減少毒性風(fēng)險(xiǎn)。
能提供與氰化金鍍液相媲美的鍍層質(zhì)量。
3. 酸性金鍍液
成分:主要是硫酸金(Au?SO?)或氯金酸(HAuCl?)。
特點(diǎn):
用于制作硬金鍍層,耐磨性高。
適合需要高硬度金鍍層的應(yīng)用,如電氣接觸點(diǎn)。
4. 軟金鍍液
成分:通?;诹姿猁}或檸檬酸體系,但調(diào)整參數(shù)以獲得較軟的金鍍層。
特點(diǎn):
提供良好的延展性和導(dǎo)電性。
用于需要高導(dǎo)電性和接插件的應(yīng)用。
5. 純金鍍液
成分:使用純金化合物,確保鍍層純度極高。
特點(diǎn):
用于需要極高純度金鍍層的場合,如高端電路板或藝術(shù)品。
6. 合金金鍍液
成分:金與其他金屬(如鎳、鈷、銀)形成合金。
特點(diǎn):
可以調(diào)整鍍層的硬度、耐磨性和顏色。
用于特殊應(yīng)用,如裝飾性鍍層或特定功能需求。
注意事項(xiàng)
環(huán)保和安全:選用無氰金鍍液可以降低環(huán)境和健康風(fēng)險(xiǎn)。
成本控制:金的價(jià)格高昂,鍍液的選擇和使用的控制對成本管理至關(guān)重要。
應(yīng)用適應(yīng)性:根據(jù)需要鍍層的特性(如硬度、導(dǎo)電性、顏色)選擇合適的鍍液。
金鍍液的選擇應(yīng)基于鍍層的特定需求、環(huán)境考慮以及經(jīng)濟(jì)效益。每個(gè)類型都有其最佳應(yīng)用場景,因此在實(shí)際應(yīng)用中選擇合適的金鍍液是關(guān)鍵。
玻璃基板銅互聯(lián)再布線層電鍍銀工藝
電鍍銀工藝是用于在各種基材上施加銀鍍層的一種表面處理技術(shù)。銀鍍層因其出色的導(dǎo)電性、反光性能和抗腐蝕性而廣泛應(yīng)用于電子、裝飾、鏡面等領(lǐng)域。以下是電鍍銀工藝的詳細(xì)流程和關(guān)鍵細(xì)節(jié):
工藝流程
預(yù)處理:
清洗:使用溶劑、堿液或超聲波清洗去除基材表面的油脂、污垢和氧化層。
活化:通常用稀酸(如硫酸或鹽酸)浸泡以激活基材表面,增強(qiáng)銀與基材的結(jié)合力。
除鈍:若基材表面有鈍化層,需要使用除鈍劑進(jìn)行處理。
鍍液準(zhǔn)備:
銀鍍液:常見類型包括:
氰化銀鍍液:提供高質(zhì)量的鍍層,但由于毒性問題,應(yīng)用受到限制。
無氰銀鍍液:如硫代硫酸鹽體系、氨銀體系,更環(huán)保,逐漸取代氰化鍍液。
參數(shù)調(diào)整:
pH值:通常在8.5到10之間,具體根據(jù)鍍液體系調(diào)整。
溫度:一般在20-40攝氏度,有助于鍍層的均勻性和光亮度。
銀離子濃度:保持適當(dāng)濃度以確保鍍層質(zhì)量。
添加劑:包括光亮劑、整平劑等,控制鍍層的外觀和性能。
電鍍過程:
電流密度:一般在0.5到5 A/dm2之間,根據(jù)鍍層厚度和硬度要求調(diào)整。
鍍層厚度:從幾微米到幾十微米,視具體應(yīng)用而定。
時(shí)間控制:從幾分鐘到幾十分鐘,根據(jù)所需鍍層厚度和鍍液效率。
后處理:
漂洗:用去離子水多次漂洗,徹底去除殘留鍍液。
干燥:可以用熱風(fēng)、真空或自然干燥,避免水斑。
鈍化或封閉:可能需要進(jìn)行后處理以增強(qiáng)耐腐蝕性或改進(jìn)外觀。
關(guān)鍵細(xì)節(jié)
鍍層質(zhì)量:
鍍層應(yīng)具備良好的均勻性、光亮度和導(dǎo)電性。
鍍液的穩(wěn)定性和純度直接影響鍍層質(zhì)量。
覆蓋性:
確保銀鍍液能覆蓋所有基材表面,特別是在復(fù)雜形狀的零件上。
硬度和耐磨性:
銀鍍層相對較軟,可以通過添加硬化劑或后處理來提高耐磨性能。
環(huán)保和安全:
由于銀的毒性和高成本,需嚴(yán)格控制廢液處理,符合環(huán)保標(biāo)準(zhǔn)。
成本管理:
銀價(jià)較高,需精確控制鍍層厚度,避免不必要的浪費(fèi)。
維護(hù):
定期檢查和調(diào)整鍍液成分,確保鍍層的一致性。
電鍍銀工藝要求精細(xì)的工藝控制和管理,以確保鍍層的高質(zhì)量和功能性。通過優(yōu)化預(yù)處理、電鍍參數(shù)和后處理步驟,可以獲得具有優(yōu)異性能的銀鍍層。銀鍍層的應(yīng)用范圍從電子元件到裝飾品,涵蓋許多領(lǐng)域,但需要注意的是,銀在空氣中容易氧化,因此在某些應(yīng)用中可能需要額外的保護(hù)措施。
銀電鍍液配制
銀鍍液根據(jù)其成分和應(yīng)用目的,可以分為多種類型。這里介紹幾種常見的銀鍍液種類:
1. 氰化銀鍍液
成分:主要包括氰化鉀(KCN)或氰化鈉(NaCN)和硝酸銀(AgNO?)或氰化銀(AgCN)。
特點(diǎn):
提供高純度、高光亮度的銀鍍層。
可控制的鍍層厚度,覆蓋性能好。
由于氰化物的毒性,現(xiàn)在使用受到嚴(yán)格限制或已被替代。
2. 無氰銀鍍液
成分:包括非氰化物的絡(luò)合劑,如硫代硫酸鹽(如硫代硫酸鈉)、氨(NH?)、或有機(jī)酸(如檸檬酸、酒石酸)。
類型:
硫代硫酸銀鍍液:環(huán)保,適合大規(guī)模生產(chǎn),鍍層質(zhì)量好。
氨銀鍍液:用于細(xì)致的電子組件鍍層,提供光亮鍍層。
有機(jī)酸銀鍍液:如檸檬酸銀鍍液,適用于需要高覆蓋性的場合。
特點(diǎn):
環(huán)保,減少對環(huán)境和操作人員的危害。
能提供與氰化銀鍍液類似的鍍層質(zhì)量。
3. 酸性銀鍍液
成分:主要是硫酸銀(Ag?SO?)或硝酸銀(AgNO?)。
特點(diǎn):
適用于需要高硬度銀鍍層的場合,如電接觸點(diǎn)。
鍍層可能不如無氰銀鍍液光亮,但耐磨性更好。
4. 光亮銀鍍液
成分:除了基礎(chǔ)鍍液成分外,還添加了光亮劑、整平劑等添加劑。
特點(diǎn):
專門用于需要高光亮度和裝飾效果的應(yīng)用。
光亮劑的選擇和濃度對鍍層的光亮度影響很大。
5. 化學(xué)鍍銀液
成分:使用還原劑(如甲醛或氫硼化鈉)在沒有外部電源的情況下進(jìn)行銀的化學(xué)沉積。
特點(diǎn):
適用于非導(dǎo)電材料的鍍銀,如塑料。
不需要電源,電鍍過程更簡單。
注意事項(xiàng)
環(huán)境影響:選擇無氰銀鍍液以減少對環(huán)境的危害。
成本:銀的價(jià)格較高,選擇合適的鍍液類型可以幫助控制成本。
應(yīng)用適應(yīng)性:根據(jù)應(yīng)用場景選擇合適的銀鍍液。例如,電子元件可能需要高導(dǎo)電性,而裝飾品可能更注重光亮度。
每種銀鍍液都有其獨(dú)特的優(yōu)勢和應(yīng)用范圍,選擇時(shí)需要考慮最終產(chǎn)品的要求、環(huán)保因素以及操作的安全性。
玻璃基板銅互聯(lián)再布線層真空鍍銅工藝
玻璃基板銅互聯(lián)再布線層真空鍍銅工藝是一種高精度、高潔凈度的金屬沉積方法,通常用于制造高性能電子器件,如LED、半導(dǎo)體封裝等。以下是詳細(xì)的玻璃基板真空鍍銅工藝流程和關(guān)鍵點(diǎn):
工藝流程
預(yù)處理:
清洗:玻璃基板首先需要通過溶劑清洗、超聲波清洗、去離子水沖洗等步驟去除表面的污垢和油脂。
干燥:使用高純度氮?dú)饣蚋稍锟諝獯蹈苫澹乐谷魏嗡只蛭廴疚餁埩簟?/p>
真空系統(tǒng)準(zhǔn)備:
抽真空:將真空鍍膜設(shè)備內(nèi)的壓力降低到10^-6 Torr或更低,以確保高純度環(huán)境。
基板裝載:將清洗后的玻璃基板安裝到真空室內(nèi)的基板夾具上。
鍍膜過程:
蒸發(fā)鍍銅:
電阻加熱:通過電阻加熱蒸發(fā)源中的銅材料,使其升華成氣態(tài)銅。
電子束蒸發(fā):使用電子束加熱銅源,使之在真空中蒸發(fā)。這種方法控制精度高,適用于厚度均勻的鍍層。
濺射鍍銅:
直流磁控濺射:使用直流電源在磁場下加速惰性氣體離子(通常是氬氣)轟擊銅靶材,從而在基板上沉積銅層。
冷卻和檢測:
冷卻:在真空環(huán)境中讓基板和鍍層自然冷卻,防止熱應(yīng)力引起的鍍層剝離。
檢測:使用光學(xué)顯微鏡、橢偏儀、四探針測量等方法檢查鍍層厚度、均勻性和導(dǎo)電性。
關(guān)鍵點(diǎn)
潔凈度:
真空鍍膜要求設(shè)備和環(huán)境的超高潔凈度,以防止任何雜質(zhì)混入鍍層。
鍍層控制:
精確控制蒸發(fā)或?yàn)R射的速率,確保鍍層厚度和均勻性。鍍層厚度可以從納米到微米級別,具體根據(jù)應(yīng)用需求調(diào)整。
真空環(huán)境:
高真空環(huán)境不僅防止氧化,更能確保鍍膜的純度和粘附力。
材料選擇:
銅的純度直接影響鍍層的導(dǎo)電性和質(zhì)量,因此選擇高純度銅靶材或蒸發(fā)源材料是關(guān)鍵。
溫度管理:
控制基板和蒸發(fā)源的溫度,防止由于熱應(yīng)力導(dǎo)致的鍍層脫落或變形。
覆蓋性:
確保鍍層能均勻覆蓋玻璃基板的每一個(gè)部分,特別是在有凹凸或復(fù)雜結(jié)構(gòu)的區(qū)域。
玻璃基板銅互聯(lián)再布線層真空鍍銅工藝是一種復(fù)雜的技術(shù),涉及多方面的控制和管理。通過嚴(yán)格的預(yù)處理、精確的鍍膜控制和后處理檢測,可以獲得高質(zhì)量、均勻、導(dǎo)電性能優(yōu)良的銅鍍層。這種工藝在電子工業(yè)中具有廣泛的應(yīng)用前景,特別是在高精度要求的電子器件制造中。
玻璃基板銅互聯(lián)再布線層真空鍍銅工藝的成功實(shí)施依賴于幾個(gè)關(guān)鍵點(diǎn)和對靶材的精心準(zhǔn)備。
關(guān)鍵點(diǎn)
潔凈度:
玻璃基板和整個(gè)鍍膜過程環(huán)境的潔凈度至關(guān)重要。任何污染物都會影響鍍層的質(zhì)量和性能。
真空度:
高真空環(huán)境(通常要求達(dá)到10^-6 Torr或更低)是保證鍍膜純度、防止氧化和獲得良好粘附力的基礎(chǔ)。
鍍層均勻性:
通過精確控制濺射或蒸發(fā)的參數(shù)(如電流、氣壓、時(shí)間),確保銅層在基板上均勻沉積。
基板溫度控制:
控制基板溫度以避免由于熱應(yīng)力導(dǎo)致的鍍層剝離或變形。通常需保持在一定溫度范圍內(nèi)以優(yōu)化鍍層質(zhì)量。
覆蓋性:
對于有復(fù)雜結(jié)構(gòu)的玻璃基板,確保銅層能覆蓋到所有必要的表面是關(guān)鍵,可能需要調(diào)整基板角度或使用額外的濺射源。
鍍層厚度:
根據(jù)應(yīng)用需求,控制鍍層厚度,以達(dá)到所需的導(dǎo)電性、耐腐蝕性和機(jī)械性能。
沉積速率:
調(diào)整濺射或蒸發(fā)的速率,以在保持高質(zhì)量的情況下提高生產(chǎn)效率。
靶材準(zhǔn)備
材料純度:
使用高純度銅靶材(通常99.99%或更高純度),以保證鍍層的高導(dǎo)電性和低雜質(zhì)含量。
靶材的尺寸和形態(tài):
靶材需要加工成符合設(shè)備要求的形狀和尺寸,確保其在濺射過程中能提供穩(wěn)定的鍍層。
靶材的表面處理:
靶材表面可能需要進(jìn)行拋光或打磨處理,以去除表面的氧化層和雜質(zhì),提高濺射效率。
靶材的背板結(jié)合:
為了提高靶材的使用效率和熱管理,靶材可能需要綁定到銅背板上。無氧銅背板常用,因?yàn)樗哂休^高的導(dǎo)熱性和導(dǎo)電性。
靶材的固定:
確保靶材牢固地固定在濺射源上,以防止在高能粒子轟擊下移動(dòng)或脫落。
靶材的老化和預(yù)濺射:
在正式鍍膜前,對新靶材進(jìn)行預(yù)濺射,移除表面的氧化層和穩(wěn)定濺射過程,確保鍍層質(zhì)量一致。
靶材的維護(hù):
定期檢查靶材使用情況,及時(shí)更換或清潔,以保持鍍膜的穩(wěn)定性和質(zhì)量。
通過嚴(yán)格控制這些關(guān)鍵點(diǎn)和靶材準(zhǔn)備步驟,玻璃基板真空鍍銅工藝可以實(shí)現(xiàn)高質(zhì)量、均勻的銅鍍層,滿足高性能電子器件的需求。
玻璃基板種子層和保護(hù)層的制備
在玻璃基板銅互聯(lián)再布線層鍍銅工藝中,種子層和保護(hù)層是兩個(gè)關(guān)鍵步驟,分別用于確保鍍層與基板的良好結(jié)合和鍍層的長期穩(wěn)定性。以下是關(guān)于玻璃基板鍍銅的種子層與保護(hù)層工藝的詳細(xì)介紹:
種子層工藝
目的:
種子層主要用于增強(qiáng)銅層與玻璃基板的附著力,提供良好的電導(dǎo)通路徑,同時(shí)為后續(xù)的電鍍提供一個(gè)均勻的沉積基礎(chǔ)。
步驟:
清洗:
玻璃基板首先需要經(jīng)過徹底清洗,去除表面的任何污染物。
活化處理:
通常使用等離子清洗或化學(xué)活化方法,如稀酸浸泡,來活化基板表面,增強(qiáng)后續(xù)金屬層的粘附性。
金屬種子層的沉積:
方法:
濺射:最常用的是磁控濺射,使用金屬如鈦(Ti)、鉻(Cr)或者鉭(Ta)作為種子層材料,它們在真空中被濺射到玻璃基板上。
化學(xué)鍍:也可使用化學(xué)鍍方法在基板上沉積金屬種子層。
厚度:種子層通常很薄,幾十到幾百納米,具體厚度根據(jù)應(yīng)用要求和后續(xù)銅層的需要進(jìn)行控制。
種子層的均勻性:
確保種子層在基板上的均勻分布是關(guān)鍵,以防止電鍍時(shí)出現(xiàn)不均勻的銅沉積。
保護(hù)層工藝
目的:
保護(hù)層旨在防止銅層氧化,增強(qiáng)抗腐蝕性,延長產(chǎn)品使用壽命,并可能提供額外的功能如耐磨性或特定光學(xué)性能。
步驟:
銅層沉積完成:
在種子層上通過電鍍或進(jìn)一步的濺射方法沉積銅層達(dá)到所需厚度。
保護(hù)層材料選擇:
常見的保護(hù)層材料包括:
有機(jī)保護(hù)層:如環(huán)氧樹脂或聚合物涂層,提供良好的抗氧化性和機(jī)械保護(hù)。
金屬保護(hù)層:如鎳(Ni)、金(Au)或鈀(Pd),這些金屬不僅增強(qiáng)抗腐蝕性,還能提供良好的導(dǎo)電性。
氧化物或氮化物保護(hù)層:如SiO?或Si?N?,提供耐腐蝕性和化學(xué)穩(wěn)定性。
沉積保護(hù)層:
化學(xué)鍍或電鍍:用于金屬保護(hù)層。
CVD或PVD:用于沉積氧化物或氮化物保護(hù)層。
涂層:對于有機(jī)保護(hù)層,通常通過旋涂、噴涂等方法應(yīng)用。
后處理:
可能包括熱處理以增強(qiáng)保護(hù)層的粘附性,或進(jìn)行表面處理以達(dá)到特定性能要求,如抗反射涂層。
關(guān)鍵點(diǎn)
界面管理:種子層與銅層、銅層與保護(hù)層之間的界面要管理好,以確保各層之間的良好結(jié)合。
材料兼容性:選擇種子層和保護(hù)層材料時(shí),需要考慮它們的化學(xué)和物理兼容性,以防止長期使用中出現(xiàn)分層或剝離。
質(zhì)量檢測:在每個(gè)步驟完成后,要進(jìn)行質(zhì)量檢測,包括厚度測量、附著力測試、耐腐蝕性實(shí)驗(yàn)等。
通過精確控制種子層和保護(hù)層的工藝,可以確保玻璃基板上的銅鍍層具有良好的電性能和長期的穩(wěn)定性。
銅互聯(lián)再布線層種子層的選擇
選擇種子層材料時(shí),需要考慮多個(gè)因素,包括與基板的結(jié)合力、與后續(xù)沉積金屬的兼容性、電導(dǎo)率、耐腐蝕性、工藝可行性以及成本。以下是一些常見的種子層材料及其特點(diǎn):
常用種子層材料
鈦 (Ti):
優(yōu)點(diǎn):
具有良好的粘附性,特別是在與玻璃或硅基板結(jié)合時(shí)。
可以形成氧化鈦層,進(jìn)一步增強(qiáng)與基板的結(jié)合。
耐腐蝕性較好。
應(yīng)用:廣泛用于半導(dǎo)體和微電子工業(yè)中的金屬化過程。
鉻 (Cr):
優(yōu)點(diǎn):
與各種基材的粘附力優(yōu)異,尤其在玻璃和陶瓷上。
良好的阻擋層特性,可以防止銅擴(kuò)散到基板中。
應(yīng)用:在需要高附著力的場景中常用,如薄膜頭制造。
鉭 (Ta):
優(yōu)點(diǎn):
氧化鉭(Ta?O?)層能提供極好的化學(xué)穩(wěn)定性和抗腐蝕性。
與銅兼容性好,適合在高溫下使用。
應(yīng)用:用于需要高可靠性和穩(wěn)定性的電子器件。
鎢 (W):
優(yōu)點(diǎn):
高熔點(diǎn)和良好的導(dǎo)電性,使其在高溫應(yīng)用中表現(xiàn)出色。
具有優(yōu)良的抗遷移特性,適合作為擴(kuò)散屏障。
應(yīng)用:常用于半導(dǎo)體中作為金屬互連的種子層。
鈷 (Co):
優(yōu)點(diǎn):
與銅的電化學(xué)性質(zhì)相近,有助于形成均勻的銅層。
低電阻率,適合需要高導(dǎo)電性的應(yīng)用。
應(yīng)用:在一些先進(jìn)的半導(dǎo)體工藝中作為種子層。
鎳 (Ni):
優(yōu)點(diǎn):
與銅有良好的電化學(xué)兼容性。
可以形成鎳硅化物,增強(qiáng)與硅基板的結(jié)合。
應(yīng)用:在某些特定需要鎳銅合金的電鍍應(yīng)用中。
選擇種子層材料的考慮因素
粘附性:材料與基板和后續(xù)層之間的結(jié)合力是首要考慮因素。
兼容性:與后續(xù)電鍍金屬(通常是銅)的化學(xué)和物理兼容性,以避免界面問題。
電導(dǎo)率:對于電子應(yīng)用,種子層應(yīng)具有足夠低的電阻率。
耐腐蝕性:在某些應(yīng)用中,種子層可能需要抵抗化學(xué)腐蝕。
工藝適用性:材料在特定鍍膜工藝下的表現(xiàn),包括濺射、化學(xué)鍍等方法。
成本:材料的成本效益分析,尤其是對于大規(guī)模生產(chǎn)。
環(huán)境影響:考慮材料的環(huán)保性,特別是在鍍層去除或處理過程中。
選擇種子層材料時(shí),必須進(jìn)行全面的評估,以確保其能滿足特定應(yīng)用的性能要求,同時(shí)考慮工藝的可行性和成本效益。
玻璃基板的化學(xué)活化處理要點(diǎn)
化學(xué)活化是玻璃基板真空鍍膜工藝中的重要步驟,旨在通過化學(xué)反應(yīng)增強(qiáng)基板表面的活性,從而改善后續(xù)金屬層與基板的結(jié)合力。具體到玻璃基板的化學(xué)活化,這里提供更詳細(xì)的步驟和考慮因素:
化學(xué)活化步驟
選擇活化劑:
硝酸 (HNO?):常用作玻璃表面的活化劑,因?yàn)樗苡行コAП砻娴奶蓟锘蚱渌袡C(jī)污染物,同時(shí)輕微蝕刻玻璃表面,提供更好的附著位點(diǎn)。
過氧化氫 (H?O?):有時(shí)單獨(dú)使用或與硝酸結(jié)合使用,提供氧化處理,有助于清潔和活化表面。
氫氟酸 (HF):對于特定的玻璃類型,氫氟酸可以微蝕刻玻璃表面,但需謹(jǐn)慎使用,因其對玻璃的腐蝕性強(qiáng)。
配制活化溶液:
濃度控制:例如,硝酸通常使用濃度在5-20%之間的稀溶液。過氧化氫可能以30%的濃度使用,但需根據(jù)具體情況稀釋。
溫度管理:溶液溫度應(yīng)控制在室溫到60°C之間,過高溫度可能導(dǎo)致玻璃表面過度腐蝕。
浸泡處理:
浸泡時(shí)間:通常為幾秒到幾分鐘,取決于活化劑的濃度和玻璃的類型。例如,硝酸浸泡可能只需10到30秒。
攪拌:確保溶液均勻接觸基板表面,可能需要輕微攪拌或振動(dòng),以增強(qiáng)活化效果。
反應(yīng)監(jiān)控:
觀察溶液對玻璃表面的影響,如氣泡生成情況或顏色變化,這通常表明活化過程正在進(jìn)行。
徹底清洗:
活化后,必須立即用高純度水或去離子水多次漂洗,以去除所有活化劑殘留物。通常需要至少三次水洗,每次確保水完全覆蓋基板。
干燥:
使用氮?dú)饣蚋稍锟諝獯蹈苫?,避免水斑和殘留物重新附著?/p>
關(guān)鍵考慮點(diǎn)
安全:處理酸性和強(qiáng)氧化劑時(shí),必須嚴(yán)格遵守安全規(guī)程,使用適當(dāng)?shù)姆雷o(hù)設(shè)備(如手套、護(hù)目鏡、防護(hù)服)。
活化效果評估:
使用顯微鏡或其他表面分析工具(如接觸角測量儀)評估活化效果。活化后的表面應(yīng)更親水,表明活性增加。
可以進(jìn)行附著力測試,如膠帶測試或劃痕測試,檢查活化后金屬層的粘附性。
環(huán)境影響:處理含有強(qiáng)酸或強(qiáng)的氧化劑的廢液時(shí),需遵循環(huán)保法規(guī)進(jìn)行中和和處理。
兼容性:確?;罨瘎┡c后續(xù)要沉積的材料(如鈀)在化學(xué)上是兼容的,不會導(dǎo)致不良反應(yīng)。
工藝控制:活化過程對時(shí)間和濃度的控制至關(guān)重要,因?yàn)檫^度活化可能導(dǎo)致玻璃表面損傷,而活化不足則不能達(dá)到理想的附著效果。
通過這些詳細(xì)的化學(xué)活化步驟,可以大大提升玻璃基板與后續(xù)金屬鍍層的結(jié)合力,從而提高鍍膜的整體質(zhì)量和耐久性。
璃基板RDL再布線層中介層材料與制作工藝
玻璃基板在電子封裝領(lǐng)域尤其是在高級封裝中的應(yīng)用越來越廣泛。RDL(再布線層)是高級封裝的關(guān)鍵組成部分,其制作需要中介層材料和工藝的支持,以滿足導(dǎo)電性、可靠性和熱膨脹系數(shù)等性能要求。以下是關(guān)于玻璃基板RDL中介層材料與制作工藝的介紹:
中介層材料要求
1. 熱膨脹系數(shù)(CTE)匹配
玻璃基板的CTE較低(約3~10 ppm/°C),中介層材料需要具有類似的CTE,以避免在溫度變化中發(fā)生翹曲或開裂。
2. 機(jī)械性能
材料需要具有較高的強(qiáng)度和韌性,能夠承受加工和使用中的應(yīng)力而不失效。
3. 電氣性能
高介電常數(shù)、低介電損耗,以滿足高速信號傳輸需求。
絕緣性良好,以防止信號串?dāng)_和短路。
4. 熱性能
需要具有較高的熱導(dǎo)率,以便在高功率器件中有效散熱。
5. 化學(xué)穩(wěn)定性與工藝兼容性
材料需要能夠耐受濕法或干法加工工藝,例如蝕刻、鍍銅或光刻等。
與玻璃基板和導(dǎo)電線路(如銅)具有良好的附著力。
常見中介層材料
1. 有機(jī)聚合物材料
聚酰亞胺(PI):耐高溫、化學(xué)穩(wěn)定性高、附著力好。
環(huán)氧樹脂:低成本,但耐熱性較聚酰亞胺差。
液晶聚合物(LCP):具有較低的介電常數(shù)和高頻性能。
2. 無機(jī)材料
二氧化硅(SiO?):常用作介電層,熱膨脹系數(shù)接近玻璃。
氮化硅(Si?N?):具有高機(jī)械強(qiáng)度和優(yōu)良的絕緣性能。
3. 有機(jī)-無機(jī)復(fù)合材料
有機(jī)聚合物中加入無機(jī)填料,如氧化鋁(Al?O?)、氧化鋯(ZrO?)等,以改善機(jī)械強(qiáng)度和熱膨脹性能。
制作工藝流程
1. 表面處理
清潔與粗化:玻璃基板表面清潔和粗化處理(如等離子處理或化學(xué)蝕刻)以提高附著力。
涂覆底層:施加粘結(jié)層材料(如氮化硅或鉻/鈦金屬層)。
2. 涂覆中介層材料
旋涂(Spin Coating):均勻涂覆有機(jī)聚合物材料。
沉積(CVD/PVD):物理或化學(xué)氣相沉積無機(jī)材料。
3. 光刻與圖案化
涂覆光刻膠(Photoresist)。
紫外曝光、顯影形成所需的再布線層圖案。
4. 蝕刻與清洗
濕法或干法蝕刻去除非必要材料。
清洗以確保圖案的精確性和表面潔凈度。
5. 導(dǎo)電層沉積
化學(xué)鍍銅或電鍍工藝沉積導(dǎo)電銅層。
平坦化(CMP)處理,以保證層間平整度。
6. 多層疊加
如果需要多層RDL,重復(fù)上述涂覆、圖案化和沉積工藝。
關(guān)鍵技術(shù)挑戰(zhàn)與解決方案
1. 玻璃與中介層材料附著力不足
采用表面改性技術(shù)(如等離子體處理)提高附著力。
2. 高溫環(huán)境下的熱失配問題
使用填料增強(qiáng)型復(fù)合材料以優(yōu)化CTE匹配。
3. 加工精度與可靠性
開發(fā)低應(yīng)力、高耐蝕性的中介層材料。
采用高精度光刻和蝕刻設(shè)備,減少缺陷率。
4. 信號完整性問題
選擇低介電常數(shù)材料,優(yōu)化層間厚度設(shè)計(jì)。
應(yīng)用展望
玻璃基板RDL技術(shù)在高性能芯片封裝、先進(jìn)互連和3D封裝領(lǐng)域具有重要應(yīng)用前景,特別是在5G通信、高性能計(jì)算(HPC)、人工智能(AI)等領(lǐng)域,將進(jìn)一步推動(dòng)中介層材料和制作工藝的優(yōu)化與創(chuàng)新。
-
半導(dǎo)體
+關(guān)注
關(guān)注
334文章
27459瀏覽量
219527 -
玻璃基板
+關(guān)注
關(guān)注
1文章
87瀏覽量
10326
原文標(biāo)題:技術(shù)前沿:TGV玻璃基板主流工藝詳解
文章出處:【微信號:深圳市賽姆烯金科技有限公司,微信公眾號:深圳市賽姆烯金科技有限公司】歡迎添加關(guān)注!文章轉(zhuǎn)載請注明出處。
發(fā)布評論請先 登錄
相關(guān)推薦
玻璃基板時(shí)代,TGV技術(shù)引領(lǐng)基板封裝
下一代英特爾玻璃基板封裝轉(zhuǎn)型概述
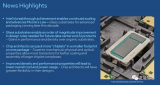
德國大型上市公司推出“TGV Foundry”,為擴(kuò)大半導(dǎo)體玻璃基板市場
LG進(jìn)軍半導(dǎo)體玻璃基板市場
臺積電角力玻璃基板:和英特爾、三星競爭,首批芯片最快有望 2025 年投產(chǎn)
韓國JNTC為三家芯片封裝企業(yè)供應(yīng)新型TGV玻璃基板
玻璃通孔(TGV)工藝技術(shù)的應(yīng)用
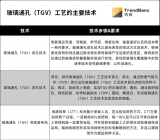
基板中互連的形成
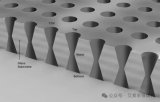
DNP:推進(jìn)玻璃芯板樣品驗(yàn)證,到2030年投20億美元用于大規(guī)模量產(chǎn)
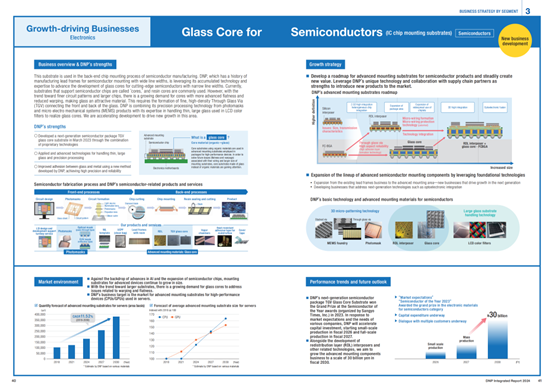
玻璃通孔(TGV)技術(shù)在傳感器制造和封裝中的應(yīng)用
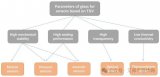
又一項(xiàng)目開工!聚焦TGV玻璃基板等產(chǎn)線!
一文了解玻璃通孔(TGV)技術(shù)
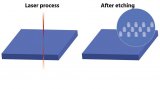
評論