共讀好書
曹建武 羅寧勝
摘要:
碳化硅 ( SiC ) 器件的新特性和移動應(yīng)用的功率密度要求給功率器件的封裝技術(shù)提出了新的挑戰(zhàn)?,F(xiàn)有功率器件的封裝技術(shù)主要是在硅基的絕緣柵雙極晶體管( Insulated Gate Bipolar Transistor ,IGBT) 和金屬氧化物半導(dǎo)體場效應(yīng)晶體管 ( Metal Oxide Semiconductor FieldEffect Transistor ,MOSFET ) 等基礎(chǔ)上發(fā)展起來的,并一直都在演進(jìn),但這些漸進(jìn)改良尚不足以充分發(fā)揮 SiC 器件的性能,因而封裝技術(shù)需要革命性的進(jìn)步。在簡述現(xiàn)有封裝技術(shù)及其演進(jìn)的基礎(chǔ)上,主要從功率模塊的角度討論了封裝技術(shù)的發(fā)展方向。同時討論了功率模塊的新型疊層結(jié)構(gòu)以及封裝技術(shù)的離散化、高溫化趨勢,并對 SiC 器件封裝技術(shù)的發(fā)展方向做出了綜合評估。
1 引言
碳化硅(SiC)器件的本質(zhì)特性決定了其低內(nèi)阻、高耐壓、高頻率和高結(jié)溫等優(yōu)異指標(biāo),在移動應(yīng)用功率密度不斷提升的壓力之下,SiC 器件對封裝技術(shù)提出了全新的要求,也帶來了全新的挑戰(zhàn)。
在寬禁帶(Wide Band Gap,WBG)半導(dǎo)體發(fā)展的早期階段,SiC 等器件的封裝繼承和沿用了現(xiàn)有的封裝技術(shù),這些技術(shù)主要是在硅基的絕緣柵雙極晶體管(InsulatedGate Bipolar Transistor,IGBT) 和金屬氧化物半導(dǎo)體場效應(yīng)晶體管(Metal Oxide Semiconductor Field Effect Transistor,MOSFET)等功率半導(dǎo)體的基礎(chǔ)上發(fā)展而來的。過去功率半導(dǎo)體的表面金屬化主要基于鋁質(zhì)材料,且一直都在漸進(jìn)改良中,例如從鋁基連接逐漸轉(zhuǎn)向銅基或銀基連接,包括邦定、焊接等。最新的發(fā)展嘗試了各種銅燒結(jié)和銀燒結(jié),有時也稱納米銀燒結(jié)或納米銀等技術(shù),取得了優(yōu)異的測試指標(biāo),特別是銀燒結(jié)被認(rèn)為是未來封裝技術(shù)的主要發(fā)展方向之一。
為了充分發(fā)揮 SiC 等新型器件的優(yōu)勢,部分銅基同質(zhì)連接和高壓銀燒結(jié)技術(shù)的研究已經(jīng)獲得了令人滿意的性能。未來發(fā)展聚焦于低壓或無壓銀燒結(jié);銅燒結(jié)和銀燒結(jié)都能提供極佳的導(dǎo)熱性能和循環(huán)壽命,但銅燒結(jié)的工藝更為復(fù)雜,費(fèi)時較多產(chǎn)出低效,且設(shè)備昂貴,制造成本偏高,因而低壓或無壓銀燒結(jié)日益受到重視。部分工程師在連接的疊層微觀構(gòu)型等方面進(jìn)行了探索,近年來出現(xiàn)多種嵌入式基板和無基板嵌入式封裝等概念。也有一些工程師轉(zhuǎn)向了某種非傳統(tǒng)的異形封裝架構(gòu),暫稱之為離散型封裝。此外,封裝技術(shù)的高溫化也是一個明顯的發(fā)展趨勢。
本文首先討論了 SiC 器件的新特性和移動應(yīng)用對功率密度的指標(biāo)要求,以及這些特性和要求給封裝技術(shù)帶來的新壓力和新挑戰(zhàn);在綜述現(xiàn)有封裝技術(shù)及其漸進(jìn)改良的基礎(chǔ)上,對銅基同質(zhì)連接等特別是銀燒結(jié)技術(shù)的發(fā)展?fàn)顩r進(jìn)行了介紹;進(jìn)而討論了封裝技術(shù)的疊層結(jié)構(gòu)創(chuàng)新和離散化、高溫化趨勢;最后對封裝技術(shù)的發(fā)展方向進(jìn)行了綜合評估。
2 現(xiàn)有技術(shù)及其面臨的主要挑戰(zhàn)
2.1 SiC 功率器件的本質(zhì)特性
寬禁帶半導(dǎo)體的本質(zhì)特性主要表現(xiàn)在電場強(qiáng)度(Electric FieldIntensity)、 導(dǎo) 熱 系 數(shù) (Thermal Conductivity)、熔點(Melting Point)、電子遷移速度(Electron Velocity)和禁帶寬度(Energy Gap)5 個方面,不同半導(dǎo)體材料的本質(zhì)特性見圖 1。
SiC 的本質(zhì)特性在多個方面都很優(yōu)秀,其低導(dǎo)通內(nèi)阻、高耐壓、高開關(guān)頻率和高耐受結(jié)溫能力是這些本質(zhì)特性的外在表現(xiàn)。SiC 器件特別適合功率電子的移動應(yīng)用,例如多電和全電飛機(jī)、電動船舶及新能源汽車等領(lǐng)域。在電動汽車的電力牽引驅(qū)動系統(tǒng)(Electric Traction Drive System,ETDS) 應(yīng)用上特別受重視,被視為 IGBT 等原有功率器件的換代技術(shù)。
2021 年末標(biāo)志性的 SiC 器件單芯片內(nèi)阻已經(jīng)低至 13 mΩ(歐美)/17 mΩ(中國),正在挑戰(zhàn) 8~10 mΩ(歐美)/10~12 mΩ(中國)的量產(chǎn)目標(biāo)。SiC 半導(dǎo)體制造水平越來越高,芯片的內(nèi)阻持續(xù)降低,從而為更高功率密度 SiC 模塊的實現(xiàn)奠定了基礎(chǔ)。為了配合高功率SiC 模塊的應(yīng)用,CISSOID 開發(fā)了相匹配的耐高溫門級驅(qū)動方案,并推出了系列三相全橋 SiC MOSFET 智能功率模塊(Intelligent Power Module,IPM),其中一款單臂 6 顆芯片并聯(lián)時,額定內(nèi)阻僅為 2.53 mΩ,額定指標(biāo) 1200 V 550 A RMS /400 kW [4] 。隨著 SiC 芯片技術(shù)的進(jìn)步,未來 CISSOID 有機(jī)會推出額定內(nèi)阻 2.00 mΩ 的IPM,即保持現(xiàn)有模塊的造型和尺寸不變,在理想的散熱條件下,單個 IPM的驅(qū)動功率將會高達(dá)1200V800A RMS /600 kW,功率密度可再提高 50%。
SiC 器件的開關(guān)速度更高,開關(guān)損耗更低(大約為IGBT 的 1/3),因而可以適應(yīng)更高的脈寬調(diào)制(Pulse Width Modulation,PWM)開關(guān)頻率。過去基于 IGBT、MOSFET 器件構(gòu)建的功率驅(qū)動電路開關(guān)頻率多為6~10 kHz,一般不超過 15 kHz。而基于 SiC 器件的同等功率實現(xiàn),開關(guān)頻率常常都在 12~30 kHz(電機(jī)驅(qū)動)或 50~100 kHz(電源逆變)。歐洲電力電子中心(EuropeanCenter for Power Electronics,ECPE)探索項目在 2015 年已經(jīng)實現(xiàn)了 250 kHz 的 SiC 開關(guān)頻率 [5] ;2021 年有些面向電源類應(yīng)用的 SiC 功率模塊,PWM開關(guān)頻率已經(jīng)高達(dá) 400 kHz [6] ,有些 SiC 門級驅(qū)動芯片的開關(guān)頻率已經(jīng)高達(dá) 430 kHz [7] 。針對高壓大功率AC/DC 或 DC/DC 應(yīng) 用 , 已 有 研 究 機(jī) 構(gòu) 嘗 試 在CISSOID 的 IPM 上進(jìn)行 200 kHz 開關(guān)頻率的測試;針對電機(jī)拖動類應(yīng)用,也有客戶開始在 CISSOID 的 IPM上嘗試30~40 kHz 的開關(guān)頻率。
SiC 器件耐壓高、內(nèi)阻小,芯片尺寸相對于 IGBT可以做得很小。目前一顆額定指標(biāo)為 1200 V、150 A(約 12 mΩ)的第四代 IGBT芯片,面積約為 140 mm 2(11.31 mm×12.56mm)[8] ;而一顆額定指標(biāo)同為 1200 V、150A(13mΩ)的 SiC 器件,面積僅為 30mm 2 (4.36mm×7.26mm)左右 [9] ,后者面積較前者幾乎減小至五分之一。
在高壓大電流和高開關(guān)頻率的應(yīng)用中,大電流意味著導(dǎo)通損耗的增加;開關(guān)頻率的提高也會帶來開關(guān)
損耗的增加;SiC 芯片面積的顯著縮小使得單位面積散熱需求急劇增加 [10-12] 。在同等負(fù)載功率的情況下,兼顧結(jié)溫、瞬態(tài)熱阻、短路耐量等因素,SiC 器件封裝的單位體積導(dǎo)熱能力需要提高 3~7 倍才能滿足總體的散熱要求,這對封裝技術(shù)提出了前所未有的挑戰(zhàn)。
2.2 來自移動應(yīng)用的指標(biāo)壓力
從 2014 年開始,美國能源部 (Departmentof Energy,DoE)在 DoE 2025 序列資助了多個 WBG 基礎(chǔ)研究項目,橡樹嶺國家實驗室(Oak Ridge National Laboratory,ORNL)、 麻 省 理 工 學(xué) 院(Massachusetts Instituteof Technology,MIT) 等學(xué)術(shù)機(jī)構(gòu)及企業(yè)參與研發(fā)[13-15] 。DoE 還與其他單位一起資助了USDRIVE 等新能源汽車探索,指向 WBG 器件的具體系統(tǒng)應(yīng)用實現(xiàn),其中對電動汽車類 ETDS 提出了苛刻的功率密度要求(見圖 2)。
美國國家可再生能源實驗室、伊利諾斯理工大學(xué)等 研 究 機(jī) 構(gòu) 及 福 特 、 通 用 等 汽 車 企 業(yè) 參 加 了USDRIVE 的挑戰(zhàn)性研究項目 [13-15] 。主要難題在于ETDS的功率密度,相對于 2020 年的水平,USDRIVE 要求2025 年牽引電機(jī)及其驅(qū)動的功率密度分別提高到50 kW/L 和 100 kW/L,相對于 2020 年的探索實現(xiàn)(非工業(yè)實現(xiàn)),要求 2025 年分別提高 8.8 倍(機(jī)械)和 7.5倍(電氣);同時要求 ETDS 的成本下降到 2025 年的6$/kW [14] ,實現(xiàn)與內(nèi)燃機(jī)驅(qū)動系統(tǒng)的可比性。
在環(huán)保要求更高的歐洲,業(yè)界也面臨著類似壓力。ECPE 作為歐洲功率電子領(lǐng)域的代表性平臺,依托本地多個大學(xué)、研究機(jī)構(gòu)和企業(yè),在基礎(chǔ)材料、封裝技術(shù)等多個層面做了大量的研究,均指向了各類創(chuàng)新性的高密度封裝 [19] 。
2.3 現(xiàn)有封裝技術(shù)面臨的關(guān)鍵挑戰(zhàn)
SiC 器件對封裝技術(shù)特別是高功率密度模塊的封裝提出了新的要求。這些要求包括但不限于:(1)為了耐受更高的結(jié)溫,所有結(jié)合面的熔點要從 200 ℃提高到 400 ℃以上; (2)封裝的總體散熱能力提高 3~7 倍,以便在更小的體積下耐受相當(dāng)?shù)暮纳⒐β?;?) 連接的剪切力(die Shear)值要從 30 MPa 提高到 60 MPa 以上,從而可以耐受寬幅熱沖擊和熱電聯(lián)合功率循環(huán),保證可靠性和壽命; (4)連接面的電阻值要小,以便耐受較高的電流;(5)要求更小的封裝體積,有助于進(jìn)一步提高功率密度并降低雜散電感,適應(yīng)更高的開關(guān)頻率 [20-27] 。
以 ETDS 為例,要實現(xiàn) 8 倍左右的功率目標(biāo)值且散熱能力還要提高 3~7 倍,業(yè)界必須從新興材料、新型連接工藝和疊層構(gòu)造形式等方向去尋找答案。
3 現(xiàn)有封裝技術(shù)及其漸進(jìn)改良
3.1 現(xiàn)有的封裝技術(shù)
現(xiàn)有封裝技術(shù)的核心可以歸納為焊接和邦定技術(shù),筆者泛稱為連接或結(jié)合。對于功率模塊,與芯片(die/dice)直接相關(guān)的連接稱為芯片近端連接,其他泛稱為芯片遠(yuǎn)端連接。關(guān)于連接,多數(shù)文獻(xiàn)混用為Attach、Contact、Connection或 Join、Joining 等,也有人用 Bonding 來泛指所有的連接(結(jié)合)。焊接是用于芯片底部與基板(Substrate)的連接(die Attach),或基板與散熱底板的連接(系統(tǒng)連接)。焊接的主要方法有傳統(tǒng)的SAC 焊接(SnAgCu Soldering),近年發(fā)展出了各種釬焊(Brazing)和擴(kuò)散焊等。邦定(Bonding)是用于芯片頂部到基板或基板到模塊外框引線的連接,材質(zhì)常用金銀銅鋁,型制有線形或帶狀,方法有超聲或熱壓等。過去功率芯片的表面金屬化材料通常是 Al 或Al 摻雜少量 Si、Cu,經(jīng)過焊接與基板表面(通常是 Cu)形成的金屬間化合物構(gòu)成 die Attach 的結(jié)合層?;鍍擅娴慕饘俪?Cu,通過焊接與散熱底板連接,散熱底板的材質(zhì)通常為鋁碳化硅(AlSiC)或表面鍍 Ni 的 Cu。
這些連接器件的性能在早期 IGBT 中可以滿足多數(shù)應(yīng)用的要求,近年來則日益落后于半導(dǎo)體技術(shù)的發(fā)展,主要表現(xiàn)在兩個方面:(1)由于半導(dǎo)體芯片單位面積電流密度的提高,原有連接的導(dǎo)熱能力嚴(yán)重不足;(2)由于半導(dǎo)體芯片最高耐受結(jié)溫的提高,芯片近端和遠(yuǎn)端連接在寬幅度熱沖擊或熱電聯(lián)合功率循環(huán)測試中劣化太快,壽命不足。各類連接的熔點、導(dǎo)熱能力取決于表面材料及形成結(jié)合的工藝過程,連接的剪切力取決于表面材料及結(jié)合層的熱膨脹系數(shù)(Coefficient of Thermal Expansion, CTE)。SiC 基礎(chǔ)材料的 CTE 為(4.3~5.4)×10-6 /℃,金銀銅鋁的CTE 依次為 14×10 -6 /℃、20×10 -6 /℃、18×10 -6 /℃、23×10 -6 /℃ [2, 27-28] ,金銀銅的 CTE更接近半導(dǎo)體,且剛度較低,拉伸延展性更好,商業(yè)中應(yīng)用的封裝技術(shù)主要使用銀和銅。
3.2 基礎(chǔ)材料和工藝的發(fā)展
至今為止,絕大多數(shù)基板的表面金屬都是銅,外框引線端子也多為銅(有時鍍鎳等)。功率模塊常用的是直接覆銅陶瓷基板(Direct Copper Bonding,DCB,或Direct Bond Copper,DBC)、氮化鋁有源金屬釬焊覆銅陶瓷基板(AlN Active Metal Brazing,AMB),還有摻雜了二氧化鋯(ZrO 2 )增韌的 Al 2 O 3 陶瓷基板等,基板與散熱底板的連接(系統(tǒng)連接)泛稱為 DCB Attach,它們的表面金屬化材料都是銅。近年來在 USDRIVE 項目的支 持 下 ,ORNL 等 開 發(fā) 了 嵌 入 石 墨(Graphite Embedded)的陶瓷基板,額定熱阻下降 17%,瞬態(tài)熱阻降低 40%,電流能力提高 10% [14] ,其表面金屬還是銅。
在 DCB Attach 工藝中,AlSiC散熱底板的 CTE 為(7~9)×10 -6 /℃,熱電聯(lián)合功率循環(huán)周次是銅質(zhì)散熱底板的 10 倍,但其導(dǎo)熱能力只有銅質(zhì)散熱底板的 30%,壽命雖長但散熱效果較差,因而近期的很多研究回歸到銅散熱底板。過去功率器件的表面金屬多為鋁,芯片頂部的粗線邦定多用鋁線(也有些網(wǎng)狀編織銅帶的嘗試)。近年來芯片近端連接的發(fā)展方向主要是用銅替代鋁,與鋁相比,銅的導(dǎo)熱性能約高 80%,電流能力約高 37% [24] ;銅的 CTE 較低且更為柔軟,延展性強(qiáng),因而在解決了 DCB Attach 的壽命問題之后,銅基同質(zhì)連接的熱沖擊和熱電聯(lián)合循環(huán)測試周次可以比傳統(tǒng)的銅鋁連接高 6~15 倍 [27-28] 。銅基同質(zhì)連接工藝普適性強(qiáng),除了用于傳統(tǒng)的邦定和焊接外,還用于銅夾封裝(Copper Clip Package,CCPAK)和印刷電路板(Printed Circuit Board,PCB)的各種厚銅工藝及焊接、燒結(jié)等。銅與半導(dǎo)體材料表面的結(jié)合有鋁質(zhì)金屬化鍍銅、銅質(zhì)燒結(jié)緩沖層邦定、二次燒結(jié)等 [10,19,24,26] 。
然而裸露的銅很容易被氧化;銅與硅、SiC 等半導(dǎo)體材料結(jié)合的附著力也偏弱;銅基連接工藝過程繁瑣費(fèi)時,量產(chǎn)產(chǎn)量低,制造設(shè)備昂貴。另外,功率器件的連接需要具備較大的電流能力,因而常用粗壯的線型或帶狀邦定材料,這樣又會導(dǎo)致在熱脹冷縮時產(chǎn)生較大的機(jī)械應(yīng)力,容易損壞芯片、降低壽命。近期關(guān)于銅基同質(zhì)連接的研究都是圍繞著相關(guān)材料的改良(例如在銅料摻雜其他形成合金及焊料成分改善)和制造工藝(焊接方法等)展開的 [10,23-24,26,29] 。
連接的工藝實現(xiàn)和基礎(chǔ)材料的開發(fā)是同步改良的。例如,傳統(tǒng)錫銀銅焊接的 CTE 約為 30×10 -6 /℃,剪切力為 20~30 MPa,導(dǎo)熱系數(shù)為 30~58 W/ (cm·℃)[2,29],因而在連接工藝方面出現(xiàn)了固液相互擴(kuò)散和瞬時液相燒結(jié) / 焊接等工藝,與之配合研發(fā)了特制的焊料,新型焊接工藝的主要連接指標(biāo)均有一定的改善 [30-32] 。此外,大量研究表明,在一定壓力下進(jìn)行的銅燒結(jié)和銀燒結(jié)的剪切力是焊接的3~5 倍,熱導(dǎo)率為 3~9 倍,電阻率僅為焊接的 1/6 左右,各方面都有相當(dāng)大的進(jìn)步。
作為連接和結(jié)合輔料的粘性導(dǎo)電環(huán)氧樹脂或摻雜微米銀聚合物近年來也獲得了極大的進(jìn)步,過去老式的環(huán)氧樹脂導(dǎo)熱能力只有 1~7 W/mK,現(xiàn)在已經(jīng)提高到 20~100 W/mK [2,29,33] ;除導(dǎo)熱外,這些輔料還可以幫助減小連接電阻,減緩熱脹冷縮帶來的機(jī)械應(yīng)力等 [33] ;與之類似,作為模塊封裝填料的絕緣導(dǎo)熱有機(jī)硅膠、熱固性樹脂等材料的導(dǎo)熱能力也提高了。最后,外殼模料的發(fā)展對于封裝的整體散熱也有貢獻(xiàn)。這些輔料的選擇和工藝過程對封裝整體性能也有重要影響 [10,33-38] 。
3.3 銅基同質(zhì)連接的研究
很多學(xué)術(shù)機(jī)構(gòu)和企業(yè)參加了銅基同質(zhì)連接的研究,例如歐洲弗里德里希亞歷山大大學(xué)等研究了重型銅線邦定,卡爾斯魯厄理工學(xué)院研究了粗銅線與厚膜銅基板的邦定;有些企業(yè)開發(fā)了激光邦定技術(shù)來提高銅銅結(jié)合的連接強(qiáng)度,還有些企業(yè)開發(fā)了鋁硅包裹銅帶用于功率邦定;有些企業(yè)開發(fā)了鋁基金屬化芯片表面雙面鍍銅的工藝來支持銅基同質(zhì)連接;多個企業(yè)開發(fā)了用于重銅邦定的 PCB 基板和焊膏以及操作工藝,可用于 die Attach、邦定、擴(kuò)散焊和銅燒結(jié)。部分工藝設(shè)備制造企業(yè)在這些研究的基礎(chǔ)上進(jìn)行局部創(chuàng)新,推出了兼容銀燒結(jié)和重銅邦定的制造設(shè)備 [19] 。
NAKAKO 等 人 在 PCIM2018 (Conference of Power Convention and IntelligentMotion,PCIM)報告了銅燒結(jié)循環(huán)壽命的研究 [39] 。他們使用了 3 種不同的銅漿料,環(huán)境氣體配置有氫氣、氮?dú)夂图姿?,設(shè)置 225~300 ℃的不同溫度等級,在銅、DCB 或 AMB 基材上進(jìn)行了燒結(jié)試驗,試驗表明銅燒結(jié)可以用于 49~169 mm 2的芯片。該研究還使用了 25 mm 2 的硅基芯片分別進(jìn)行銅燒結(jié)(無壓,300 ℃)、銀燒結(jié)(20 MPa,300℃)、高鉛焊接,然后進(jìn)行了-40~+200 ℃的寬幅熱沖擊測試對比。在 5000 次循環(huán)之后,三種連接都出現(xiàn)了某種程度的劣化,銅燒結(jié)的邊緣出現(xiàn)了細(xì)微的裂縫,銀燒結(jié)的邊緣則出現(xiàn)了較大的裂縫,但二者的中間位置幾乎沒有劣化;高鉛焊接的邊緣和中間均出現(xiàn)了明顯的裂縫。該試驗還進(jìn)行了 5 MPa、10 MPa 等不同壓力條件組合的測試,獲得了 60~80 MPa 的剪切力。
NAGAO 等人在 PCIM 2018報告了高結(jié)溫半導(dǎo)體銅燒結(jié)研究的情況 [40] 。他們使用一種新型的銅漿料(來源未披露),在 300 ℃和氮?dú)庵?,?1 MPa 的低壓對 Si(3 mm×3 mm)和 SiC(3 mm×4.4 mm)芯片進(jìn)行銅燒結(jié),獲得的剪切力均值分別為 32.7MPa (Si )和 17.2MPa(SiC),報告認(rèn)為這個結(jié)果好于傳統(tǒng)的高溫 Pb20Sn 焊接(一種高鉛的鉛錫焊料)。
WANG 和 LU 在 CIPS 2020 (International Conference onIntegrated Power Electronics Systems)聯(lián)合 做 了 題 為 《Sintered Copper die Attach:Process,Properties,and Reliability 》 [41] 的研究報告。研究者使用微米級的低成本市售銅膏,用銅燒結(jié)進(jìn)行了 dieAttach測試。該測試使用了 3 mm×3 mm、5mm×5 mm 的IGBT 芯 片 、DCB、AlN AMB 基 板 , 在 0~5 MPa、230~300 ℃等條件組合下進(jìn)行燒結(jié)操作。測試表明,在5 MPa、270~300 ℃,不同基板上進(jìn)行 30 min 的銅燒結(jié),芯片的剪切力最高可達(dá) 65 MPa。在經(jīng)過 2000 次的-55~125℃熱沖擊循環(huán)(參照 JESD22-A106B.01 測試標(biāo)準(zhǔn))之后,剩余剪切力也還有 58 MPa。考慮到目前各類焊接工藝的 die Attach 剪切力都在 20~30 MPa 左右,該報告的結(jié)果是相當(dāng)積極的。
3.4 封裝技術(shù)的現(xiàn)狀
某些基于第五代 IGBT 芯片的功率模塊封裝技術(shù)是漸進(jìn)改良的典型案例,反映了封裝技術(shù)的現(xiàn)狀 [30-31] 。該技術(shù)集合了封裝技術(shù)的經(jīng)典方法和漸進(jìn)改良成果,其中部分也嘗試了銅燒結(jié)和銀燒結(jié)等工藝,主要包括:
1)芯片頂部連接,核心是銅銅(Cu-Cu)邦定,通過對芯片頂部進(jìn)行銅質(zhì)金屬化(基板表面也為銅),邦定線由鋁線改為銅線,獲得了最佳的表面同質(zhì)結(jié)合及CTE 匹配,改善了連接壽命和芯片表面的散熱狀況;
2)芯片底部連接,依據(jù)底部金屬化的不同,分別采用銅錫(Cu-Sn)或鎳錫(Ni-Sn)混合焊料進(jìn)行擴(kuò)散焊(不同配比試驗,有時也摻入了納米銀粉),在結(jié)合面產(chǎn)生了 5 μm 以上的金屬化合物層,測試表明對面積高達(dá) 185mm 2 的 IGBT 芯片都可以有效操作,該封裝技術(shù)也嘗試了高壓銀燒結(jié)來進(jìn)行dieAttach (壓力5~30MPa);
3)系統(tǒng)連接,DCB Attach 等,通過調(diào)節(jié)焊料中的錫銀銅比例,并調(diào)節(jié)工藝過程(溫度曲線),實現(xiàn)了高效改進(jìn)型焊接,獲得最佳的結(jié)合面彈性模量。
由此,該組合式漸進(jìn)改良的封裝技術(shù)獲得了性能的綜合性改善:首先,該技術(shù)將各個連接的熔點都提高到了 400 ℃以上,可以支持 200 ℃以上的最高工作結(jié)溫,可用于 SiC 模塊的封裝;其次,使用該技術(shù)的功率模塊在各種壽命測試中表現(xiàn)優(yōu)異,在熱沖擊和熱電聯(lián)合功率循環(huán)(類似于 AQG 324 的 PCSEC [42] )測試中表現(xiàn)優(yōu)異,經(jīng)過 200 萬次循環(huán)后芯片頂部邦定幾乎沒有劣化,底部焊接則僅因 DCB 銅皮劣化而受到影響 [30] ;模塊總體熱阻顯著降低,導(dǎo)熱性能提高 15%左右。該封裝技術(shù)是一個顯著進(jìn)步,但對于 SiC 器件要求的3~7 倍的散熱能力還是不足的。
其他廠家也開發(fā)了主要基于銅基同質(zhì)連接的不同工藝,具體實現(xiàn)各有特色。例如直接端子鍵合把銅質(zhì)引線端子直接鍵合到芯片頂部 [19] ,芯片頂部系統(tǒng)混用了銅燒結(jié)和銅銅邦定 [19] ,與 DTS 概念接近的邦定緩沖層(Bonding Buffering)技術(shù)揭示了銅基同質(zhì)連接的核心要點:通過在芯片表面生成大約 50 μm 的緩沖層,解決了銅與半導(dǎo)體表面結(jié)合強(qiáng)度不足的問題,且導(dǎo)電和導(dǎo)熱能力優(yōu)異,有報道說該技術(shù)實現(xiàn)的芯片頂部連接,電流耐受能力提高至原有工業(yè)標(biāo)準(zhǔn)的 15倍 [22-25] 。還有一些企業(yè)轉(zhuǎn)向了銀銅三維多層燒結(jié)的無邦定連接,目前細(xì)節(jié)沒有得到足夠的披露,但是廠家宣稱其電流能力、導(dǎo)熱能力和熱循環(huán)周次均得以提高10 倍 [19] 。國內(nèi)的領(lǐng)先企業(yè)也開發(fā)了類似的先進(jìn)混合封裝技術(shù),取得了優(yōu)異的測試結(jié)果,部分已在產(chǎn)品上批量應(yīng)用 [27] 。
由此可見,目前功率器件封裝技術(shù)的核心工藝已從鋁基轉(zhuǎn)向銅基,在前期研究和實際產(chǎn)品應(yīng)用上都取得了顯著進(jìn)展,除了基于原有技術(shù)的邦定和焊接等連接型式,銅燒結(jié)也有不小的進(jìn)步。但從導(dǎo)電導(dǎo)熱性能、剪切力、熔點等指標(biāo)來看,這些漸進(jìn)改良的效果還不夠,因而近年來業(yè)界的前沿研究大都轉(zhuǎn)向了銀燒結(jié)。
4 銀燒結(jié)技術(shù)
4.1 銀燒結(jié)技術(shù)的背景
銀是目前唯一一種在 200 ℃下有自動還原的去氧化自潔功能的金屬材料,對于銀銀(Ag-Ag)、金銀(Au-Ag)或銀銅(Ag-Cu)界面,銀燒結(jié)后形成的結(jié)合面非常穩(wěn)定,工藝實現(xiàn)相對簡單,生產(chǎn)速度更快。從現(xiàn)有的研究成果來看,銀燒結(jié)形成的結(jié)合面同時具備高電導(dǎo)、高熱導(dǎo)、高可靠性、高剪切力等特點,因而已被視為封裝技術(shù)未來的核心發(fā)展方向之一。卡爾斯魯厄理工學(xué)院的研究報告 [50] 指出,die Attach 銀燒結(jié)之后的結(jié)合面熔點分別為 961 ℃(銀)和 1085 ℃(銅),足以耐受高達(dá) 225 ℃的工作溫度,銀燒結(jié)的導(dǎo)熱能力是傳統(tǒng)焊接的 5~7 倍,融合界面更為柔軟,具有更大的剪切力值,銀燒結(jié)壓力與 die Attach 剪切力的大致關(guān)系參見圖 3,因而其熱電聯(lián)合功率循環(huán)壽命是傳統(tǒng)焊接的 10 倍。總而言之,僅就熱力學(xué)性能而言,銀燒結(jié)正好可以滿足 SiC 器件對封裝技術(shù)所要求的 3~7 倍的散熱能力 [27,35,43-47] 。
目前國內(nèi)模塊封裝常用的釬焊焊料為錫銀銅焊料組合(SnAgCu,SAC),其熔點僅有 220 ℃左右,而現(xiàn)在多數(shù) SiC 器件的最高額定結(jié)溫都是 175 ℃,很快就會普及到 200 ℃,因而要求芯片底部連接結(jié)合面的熔點要達(dá)到 300 ℃,最好超過 400 ℃。由于銀燒結(jié)形成的結(jié)合面更為柔軟,在芯片底部連接時,高溫高壓銀燒結(jié)的熱沖擊測試或熱電聯(lián)合功率循環(huán)周次,可以達(dá)到傳統(tǒng)釬焊的 10 倍或以上 [24,27] 。不僅如此,銀燒結(jié)連接在電氣和熱力學(xué)性能上也非常理想,大致而言,其燒結(jié)面的電阻率可以降低至 8×10 -6 Ω·cm 2[8] ,熱導(dǎo)率提高到150~300 W/ (m·K),導(dǎo)熱性能是傳統(tǒng)焊接的 3~10倍 [2,27,35] 。圖 3 中給出的數(shù)值是一個大致的數(shù)量級描述。銀燒結(jié)相關(guān)的研究和實踐還處于早期階段,尚未有一個公認(rèn)的、規(guī)范化的測試規(guī)程,所以不同研究的測定條件是有差異的,報道的測試數(shù)值也各不相同。
銀燒結(jié)的優(yōu)異性能吸引了大量的研究者涉足其間,但其并非新生事物。早在 1970—1983年,銀燒結(jié)就被用于金屬和陶瓷之間的鍵合,同期也有一些銅燒結(jié)、金燒結(jié)的研究,還有使用鐵和陶瓷(Al 2 O 3 )在100 MPa~1 GMPa 壓力下進(jìn)行燒結(jié)的報道。1990 年前后,德國開始使用微米級的銀粉膏料來進(jìn)行高壓燒結(jié),2000 年前后,納米級的金粉和銀粉(納米銀)也開始被用于各種試驗。這些實驗表明在適當(dāng)?shù)膲毫l件下,各種燒結(jié)都能實現(xiàn)極佳的連接強(qiáng)度和導(dǎo)電導(dǎo)熱性能,近期中高壓銀燒結(jié)也開始進(jìn)入量產(chǎn)應(yīng)用;近年來更多的試驗表明,較為便宜的亞微米到微米級的混合銀粉漿料可以在較低溫度(220 ℃左右)進(jìn)行有效的燒結(jié)(配合以各種輔料、制造工藝),但還是需要足夠的壓力才能保證剪切力、導(dǎo)通電阻及導(dǎo)熱能力等指標(biāo)滿足應(yīng)用的需要 [20] 。目前已有一些報道展示了低壓甚至無壓銀燒結(jié)試驗的測試情況,效果暫時還不夠理想,有待進(jìn)一步探索。
歐洲很多研究機(jī)構(gòu)介入了銀燒結(jié)相關(guān)的探索。在德國佛勞恩霍夫研究促進(jìn)協(xié)會(Fraunhofer)體系中,材料和系統(tǒng)所(Fraunhofer Institute for Microstructure of Materials and Systems,IMWS)長期致力于廣域的半導(dǎo)體封裝基礎(chǔ)研究并開發(fā)了對應(yīng)的 CAM(Computer Aided Manufacturing) 系 統(tǒng) ;可 靠 性 和 微 集 成 所(Fraunhofer Institute for Reliability and Microintegration,IZM)同時在進(jìn)行大面積銀燒結(jié)和擴(kuò)散焊的研究和驗證;硅技術(shù)所(FraunhoferInstitute for Silicon Technology,ISIT)也從事封裝技術(shù)和可靠性研究,并與美國元件企業(yè) VISHAY 一起建立了研究型試生 產(chǎn)線;法國 IMS (Laboratoire de l'Intégration du Matériau au Système)開放平臺進(jìn)行了 3D 組裝相關(guān)的低 壓 銀 燒 結(jié) 研 究 , 法 國 PRIMES(Plateforme d'Innovation Mécatronique de Puissance et Management del'énergie) 開放平臺則進(jìn)行了模塊結(jié)構(gòu)創(chuàng)新方面的開 發(fā) 。 University of Breme、Chemnitz University of Technology、DelftUniversity of Technology 等高校也都參與了各種銅燒結(jié)、銀燒結(jié)研究。歐洲其他國家的研究機(jī)構(gòu)相對分散,大都依托于 ECPE 與德法的對口單位合作 [19] 。
2014 年 SIOW 在期刊 Electronic Materials [44] 、2018年 LIU 等人在 Micromachines [45] 匯總了銀燒結(jié)的總體情況,兩個報道均可作為近年來銀燒結(jié)技術(shù)發(fā)展的索引。在 PCIM 2018,TAKESUE 等報道了無壓銀燒結(jié)在機(jī)械和可靠性方面的測試情況 [48] ,OTTO 等人報道了在引線框架上進(jìn)行銀燒結(jié)和擴(kuò)散焊的對比研究 [32] ,DRESEL 等人報道了在高溫 PCB 上進(jìn)行銀燒結(jié)的研究情況 [49] ;在 CIPS 2020,SUGANUMA 報告了有壓銀燒結(jié)及銅燒結(jié)的測試情況 [20] ,SUBBIAH 等人(佛萊堡大學(xué)) 報道了在若干非 DCB 基板進(jìn)行銀燒結(jié)的試驗 [46] ,而 BLANK 等人(卡爾斯魯厄理工學(xué)院)則對無壓銀燒結(jié)進(jìn)行了總結(jié) [50] ;2021 年 CALABRETTA 等人在 Applied Science 報道了銀燒結(jié)工藝優(yōu)化和建模的研究成果 [47] 。這些研究報道反映了近年來銀燒結(jié)技術(shù)的前沿發(fā)展,以下筆者對相關(guān)研究作一些詳細(xì)介紹。
4.2 銀燒結(jié)技術(shù)的相關(guān)研究
4.2.1 大阪大學(xué)的研究
大阪大學(xué) SUGANUMA 在CIPS 2020 報 告 了《 WBG Power Semiconductor Packaging withAdvanced Interconnection Technologies 》 [20] ,作為 CIPS 2020 的特邀報告,論文詳細(xì)說明了銀燒結(jié)結(jié)合面的形成機(jī)制:柔軟的合金融合介面(見圖 4)。報告總結(jié)了銀燒結(jié)技術(shù)的歷史和現(xiàn)狀,給出細(xì)節(jié)數(shù)據(jù),團(tuán)隊用相對便宜的微米和亞微米混合顆粒銀膏在 200 ℃低溫下進(jìn)行 die Attach,獲得優(yōu)異的電氣和熱傳導(dǎo)性能。報告指出,在180 ℃進(jìn)行 10 min 的無壓銀燒結(jié)可在 DCB 上形成剪切力值約為 30~40 MPa 的結(jié)合,結(jié)合面的電阻值、熱導(dǎo)率等關(guān)鍵指標(biāo)也很理想;用 GaN 芯片在鍍鎳的陶瓷覆鋁(Direct Bonding Aluminum,DBA)基板上進(jìn)行銀燒結(jié),在-40~250 ℃區(qū)間進(jìn)行 500 次熱沖擊試驗后,殘余剪切力幾乎沒有變化(保持在約 33 MPa 的水平)。
對于用銀料濺射形成的 GaN 芯片金屬表面,在250 ℃與微米銀膏燒結(jié)后的銀珠分布非常均勻,可以有效結(jié)合兩個表面;對于 Au-Ag 燒結(jié),過去低壓燒結(jié)的效果不良困擾了業(yè)界多年,近年已被研究清楚,空氣環(huán)境、無壓、180 ℃、10 min 燒結(jié)的結(jié)合面細(xì)節(jié)見圖4。另外,作者也曾經(jīng)做過數(shù)年的銅燒結(jié)研究,在250~300 ℃的氮?dú)猸h(huán)境中,用 0.4 MPa 的壓力進(jìn)行的銅燒結(jié)也可獲得 30~40MPa 的 die Attach 剪切力數(shù)據(jù)。
大阪大學(xué)的報告指出,傳統(tǒng)焊接技術(shù)已不能滿足WBG 器件對導(dǎo)熱能力及熱電聯(lián)合循環(huán)壽命的苛刻要求,高壓銀燒結(jié)目前雖然還比較昂貴,但是已經(jīng)開始了商業(yè)化應(yīng)用進(jìn)程。由于燒結(jié)的結(jié)合面是融合性的,與焊接結(jié)合面的剛性相比要柔軟很多,因為能夠更好地消化熱脹冷縮的機(jī)械應(yīng)力,所以獲得了極為理想的可靠性和壽命。
4.2.2 佛萊堡大學(xué)的研究
佛萊堡大學(xué) SUBBIAH 等人在CIPS 2020 報告了《 Comparison of Silver Sintered Assemblieson Non-DCB Substrates 》 [46] ,對3 種非 DCB 基板(IS550H 高溫 PCB、隔離金屬基板和銅質(zhì)引線框架) 進(jìn)行了銀燒結(jié)測試,測試使用了 2 mm×2 mm的小型芯片及市售銀膏(LTS338-28 [37] ),在230 ℃、10~20 MPa 壓力下進(jìn)行,初始和剩余剪切力見圖 5。
該研究指出,用銀燒結(jié)技術(shù)把功率芯片等直接連接到高溫 PCB 上是可行的。僅從剪切力的數(shù)據(jù)來看,這個試驗并不完美,因為在高壓銀燒結(jié)(最高 20 MPa)時獲得的最佳剪切力初值只有 35 MPa,低于 3.3 節(jié)天津大學(xué)的中壓 5 MPa 銅燒結(jié)數(shù)據(jù) [41] ,所以筆者認(rèn)為這個試驗還需要進(jìn)一步的嘗試,例如參考 4.2.3 節(jié)卡爾斯魯厄理工學(xué)院(Karlsruhe Institute of Technology,KIT)的測試,使用不同的芯片底部金屬化層及 PCB 的表面處理來進(jìn)行比對。不過該試驗偏向離散式封裝(參見5.2 節(jié)),報告提及了在 PCB 上可以集成更多的離散元件并通過銅質(zhì)過孔互聯(lián)等,并稱該 PCB 基材可以在200 ℃高溫環(huán)境下長期可靠地工作,因而該研究也有其獨(dú)特的意義。
4.2.3 卡爾斯魯厄理工學(xué)院和日立化學(xué)的研究
卡爾斯魯厄理工學(xué)院 BLANK 等人和日立化學(xué)ISHIKAWA 在 CIPS 2020 聯(lián)合發(fā)表了 《 Is Pressureless Sintering Ready for Power Electronic Modules?》 報告 [50] ,報道了無壓納米銀及納米銅 die Attach 燒結(jié)的測試情況。測試使用 3 種不同尺寸的 die,分別為2.3 mm×2.3 mm、3.2 mm×1.6 mm、4.0mm×4.0 mm,較小的 2 款芯片獲得成功,第 3 個較大的芯片遇到問題,燒結(jié)后呈現(xiàn)大量的空洞區(qū)(見圖 6)。
研究者使用了 100 nm 的納米銅膏、20 nm 的納米銀膏等材料,在 275 ℃進(jìn)行了無壓燒結(jié)對比試驗,銀燒結(jié)測試的襯底使用了常規(guī)的 DCB 基板及化學(xué)鍍鎳沉金(Electroless Nickel ImmersionGold,ENIG)和化學(xué)鍍鎳鍍鈀及沉金(ElectrolessNickel Electroless Palladium Immersion Gold,ENEPIG)這 2 種 PCB 基材,銅燒結(jié)測試則使用了 DCB 基板及銅質(zhì)引線框架。
2.3 mm×2.3 mm 的 die使用了純銀進(jìn)行底部金屬化,3.2 mm×1.6 mm 使用了厚膜銀鈀合金(Thick Film Silver Palladium,AgPd),而 4.0 mm×4.0 mm 的 die 底部表面為鎳鈀銅合金,并在燒結(jié)前進(jìn)行了表面預(yù)處理。此外,測試還使用了 80 μm 和 120 μm 兩種銀膏(銅膏)印刷厚度進(jìn)行了燒結(jié)試驗,具體燒結(jié)時間曲線的配置也有調(diào)整和變化。試驗表明,對 2.3 mm×2.3 mm的芯片,納米銀燒結(jié)在 ENIG 和 ENEPIG 產(chǎn)生的剪切力均值分別為 82 MPa 和 100 MPa,較為理想;3.2 mm×1.6 mm(AgPd 底部)的芯片,在 ENIG 上的剪切力均值為 70 MPa,但在 DCB 上表現(xiàn)不佳,不超過30 MPa;至于銅燒結(jié),這兩個小型芯片在一定的工藝條件下獲得的最好結(jié)果是在銅質(zhì)引線框架上,剪切力均值為 65 MPa,與天津大學(xué)的測試結(jié)果一致 [41] 。4.0 mm×4.0 mm 芯片的銀燒結(jié)試驗沒有獲得成功,空洞面積太大(圖 6),報告者認(rèn)為該芯片面積較大,在進(jìn)行無壓銀燒結(jié)時焊膏揮發(fā)存在一定困難,還需要繼續(xù)研究。
4.2.4 卡塔尼亞大學(xué)的研究
CALABRETTA 等人在卡塔尼亞大學(xué)及合作企業(yè)研究了 SiC 芯片銀燒結(jié)工藝優(yōu)化并建模,在 Applied Sciences 發(fā)表《 Silver Sintering for Silicon Carbide Die Attach:ProcessOptimizationandStructuralModeling》 [47] ,報告了使用 BOSCHMAN 的市售設(shè)備在 AMB 基板上進(jìn)行 SiC 芯片銀燒結(jié)的詳細(xì)過程。該文還報告了10~30 MPa 的有壓銀燒結(jié)最佳壓力值的測定方法,并結(jié)合 3000 次寬幅熱沖擊試驗(-65 ~+150 ℃)的中間和最終測試數(shù)據(jù),劣化情況見圖 7。
他們還基于中間測試結(jié)果等數(shù)據(jù),對銀燒結(jié)的材料(顆粒)、壓力、溫度等之間的關(guān)系進(jìn)行了研究,嘗試了用有限元方法對結(jié)合面進(jìn)行分析,并通過燒結(jié)粘附特性和相關(guān)斷裂形式進(jìn)行了內(nèi)聚區(qū)建模。
4.3 銀燒結(jié)技術(shù)的材料、工藝和設(shè)備
銀燒結(jié)的兩個表面,芯片底部金屬化層和基板、散熱底板表面的金屬化層的材質(zhì)也得到了廣泛的研究。例如,因戈爾施塔特技術(shù)應(yīng)用大學(xué)等研究了銀漿料與改性銅合金之間的連接;弗勞恩霍夫集成系統(tǒng)和設(shè)備技術(shù)研究所(Fraunhofer Institute for Integrated Systems and DeviceTechnology,IISB)則研究了銀銀直接鍵合的效果;阿莎芬堡應(yīng)用技術(shù)大學(xué)研發(fā)了 Micro Copper Sinter 材料;F&K、DODUCO 等企業(yè)也致力于界面友好的鍍層材料研究并應(yīng)用于產(chǎn)品設(shè)計 [19] 。
在企業(yè)界,領(lǐng)先的基礎(chǔ)材料公司 HERAEUS、日立化學(xué)等開發(fā)了適用于銀燒結(jié)的各種漿料 [28-29,50] ,目前市場上已有十余家銀燒結(jié)漿料的商業(yè)供應(yīng)。以顆粒度論,有納米、亞微米和微米級別;以燒結(jié)壓力論,有高壓銀膏、低壓銀膏、無壓銀膏;市面也有金漿料、銅膏料的供應(yīng)。已有一些中國廠家涉足了銀燒結(jié)材料,并與國內(nèi)大學(xué)一起進(jìn)行了對比驗證。
在不同壓力、溫度(曲線)和環(huán)境(氣體)條件下,對不同芯片、基板的表面材質(zhì)進(jìn)行銀燒結(jié)時,其功效有所不同,這方面的研究也很廣泛。銀燒結(jié)工藝研究的參與者有前述的 Fraunhofer 研究協(xié)會體系 IZM、IMWS、ISIT 等多個研究所,大學(xué)則有 University of Applied Science Kempten、Universityof Breme、Ferdinand Braun Institut Berlin、卡爾斯魯厄理工學(xué)院等?;鶢柭?lián)合應(yīng)用大學(xué)(University of Applied Sciences Kiel,UASK)進(jìn)行了低溫銀燒結(jié)工藝生產(chǎn)線的開發(fā);IMWS 和 UASK 還進(jìn)行了基于銀燒結(jié)的高密度高溫微組裝研究,具體有厚銅 PCB 制造工藝、帶有嵌入式元件的混合 PCBA (Printed Circuit Board Assembly)等。參與工藝研究的企業(yè)則有HERAEUS、F&K、HESSE 和 DODUCO 等,在測試驗證和建模方面,前述多個大學(xué)、研究機(jī)構(gòu)及企業(yè),與 MENTOR等熱力學(xué)和電氣模擬軟件廠家合作,同步開展了各種新型工藝的建模及驗證 [19] 。
焊接設(shè)備廠商 PINK、BOSCHMAN和 ASM 等開發(fā)了從實驗室應(yīng)用到量產(chǎn)車間使用的自動化銀燒結(jié)設(shè)備,ZESTRON 開發(fā)了用于銀燒結(jié)前后進(jìn)行清洗處理的生產(chǎn)設(shè)備。銀燒結(jié)技術(shù)目前還在發(fā)展中,現(xiàn)有的工藝和設(shè)備既是對前期研究成果的階段性總結(jié),又是后段持續(xù)演進(jìn)的起點 [19] 。
4.4 銀燒結(jié)技術(shù)總結(jié)
如前所述,納米或微米級的銀粉顆粒材料是一種優(yōu)異的封裝材料,銀燒結(jié)形成的結(jié)合面同時具備理想的導(dǎo)電和導(dǎo)熱性能。就工藝過程而言,主要特征表現(xiàn)在兩點:(1)銀是目前唯一可見的當(dāng)溫度在 200 ℃以上時表面氧化層可以自潔并恢復(fù)到純銀狀態(tài)的金屬材料,而近年絕大多數(shù)銀燒結(jié)工藝是在 250 ℃左右進(jìn)行的,因而可以省略很多燒結(jié)前的預(yù)處理過程;(2)銀燒結(jié)的結(jié)合面是融合的,在燒結(jié)面形成了柔軟的合金層,可以耐受更大周次的熱電聯(lián)合功率循環(huán),因而可靠性更高,壽命更長。當(dāng)然,純粹的銀粉無法直接進(jìn)行燒結(jié)操作,通常以銀膏或銀漿形式出現(xiàn),混合有某種化合物或聚合物。除了銀粉本身的純度,銀粉在介質(zhì)中的分布均勻度、介質(zhì)在燒結(jié)后的殘留狀況也都存在工藝問題;有些研究使用了金粉或銅粉(金膏或銅膏)來代替銀膏進(jìn)行燒結(jié)試驗 [20,41] 。
銀燒結(jié)目前的研究涉及到 die Attach、DCB Attach等,效果取決于被燒結(jié)的兩個界面的材料及具體銀漿料的特征,還有環(huán)境氣體、溫度曲線(升溫、停留時間、降溫等)、壓力等要素。銀燒結(jié)的具體方法有熱壓、原位成型、火花等離子、激光燒結(jié)、電流燒結(jié)等 [45] 。從現(xiàn)有的研究報道來看,在一定壓力下進(jìn)行的各種銀燒結(jié)都可以獲得理想的剪切力值,銀燒結(jié)的壓力越大、溫度越高,高溫持續(xù)時間越長,燒結(jié)的效果越好。但是高溫高壓燒結(jié)的制造成本偏高,長時間燒結(jié)的產(chǎn)能偏低,而且燒結(jié)壓力太高可能對芯片本身帶來潛在的機(jī)械損害,進(jìn)而影響到熱沖擊或熱電聯(lián)合循環(huán)的壽命周次 [33,45,48] 。
當(dāng)然目前可見的研究報道,使用的芯片面積都還較小,面積更大芯片(或 DCB)的燒結(jié)報道較少,具體工藝條件和過程還需要進(jìn)一步研究和驗證。die Attach或 DCB Attach 的低壓或無壓銀燒結(jié)試驗都還在發(fā)展中,多數(shù)研究是在 200~300 ℃的溫度范圍內(nèi)進(jìn)行的,而這正是大多數(shù)普通的表面安裝技術(shù)(SurfaceMount Technology,SMT)回流焊爐(ReflowOven)的工作區(qū)間。因此,如果未來無壓銀燒結(jié)或低壓銀燒結(jié)技術(shù)可以取得理想的進(jìn)展,就意味著其制造效率可以顯著提升,制造成本將會大大降低,進(jìn)入商業(yè)化量產(chǎn)應(yīng)用的門檻就非常低了。筆者認(rèn)為,未來銀燒結(jié)的技術(shù)突破將主要集中在以下幾個方向:(1)低溫低壓銀燒結(jié)材料的研究; (2)較大面積芯片的銀燒結(jié)工藝研究、中間介質(zhì)的清除等;(3)在前二者基礎(chǔ)上發(fā)展出來的全自動化銀燒結(jié)制造設(shè)備。
5 封裝技術(shù)的其他發(fā)展
5.1 演進(jìn)中的模塊疊層構(gòu)型
基板是功率模塊的芯片載體之一。常見的基板與芯片、散熱底板的連接模式在 IGBT 時代就已經(jīng)成為了一種定式。近年來在基板的疊層構(gòu)型方面也出現(xiàn)了新的趨勢,為了提高組裝密度,研究人員開始使用雙面散熱結(jié)構(gòu),過去單一的芯片底部散熱帶走了大約60%的內(nèi)耗,但是在芯片頂部的淺近層面,還有 40%的熱量未能及時排出,導(dǎo)致芯片結(jié)溫偏高。在 SiC 器件中,導(dǎo)通電阻伴隨結(jié)溫升高而增加,其短路耐量只有IGBT 的一半左右,約為 2.5 μs 左右 [3-4] ,因而節(jié)溫更容易快速越限。所以改善現(xiàn)有各個結(jié)合面的熱阻,或同時減少結(jié)合面的數(shù)目,也是業(yè)界努力的主要方向之一。近年來出現(xiàn)的嵌入式基板概念把芯片及基板都埋入某種載體中,芯片和嵌入基板都使用了雙面銀燒結(jié)進(jìn)行連接,由此來實現(xiàn)雙面散熱,嵌入式基板、雙面空冷散熱的剖面構(gòu)造見圖 8。更為激進(jìn)的無基板封裝概念則取消了嵌入基板,芯片通過載體的金屬化層直接連接到散熱體上[42] 。圖中的頂部和底部嵌入基板與散熱器的結(jié)合面都使用了熱界面材料,可改善導(dǎo)熱并減緩機(jī)械應(yīng)力。
圖 8 中還出現(xiàn)了Spacer/Spacer Attach 的概念。Spacer 為芯片頂部燒結(jié)連接的一個銅質(zhì)中間件 [2,26,42] ,通過邦定或二次燒結(jié)與其他層面進(jìn)行連接(SpacerAttach)。與低壓和無壓銀燒結(jié)的情況類似,這些嵌入疊層結(jié)構(gòu)還處于發(fā)展早期,各個報道的細(xì)節(jié)披露尚不充分。
5.2 模塊封裝的離散化趨勢
為了減小 ETDS 的體積和重量,部分工程師轉(zhuǎn)向了接近于組裝概念的各種 3D 綜合集成。各種形式的發(fā)展分別肇始于混合厚膜電路、微組裝或多芯片封裝等傳統(tǒng)高密度工藝,或這些工藝的混合運(yùn)用,現(xiàn)在也有一些其他創(chuàng)新的微觀構(gòu)造型式。過去的 ETDS 常用IGBT 模塊來構(gòu)建,而電動車企 TESLA 幾年前就用SiC 分立器件實現(xiàn)了全 SiC 版的 ETDS,通過將電氣驅(qū)動與電機(jī)機(jī)體進(jìn)行某種程度的融合,顯著提高了ETDS 的性價比。圖 9 展示了TESLA 的實際產(chǎn)品設(shè)計:非典型模塊和散熱器的剖面構(gòu)造 [12] 。
近年來更多研究機(jī)構(gòu)和企業(yè)介入了這種離散化的研究??査刽敹蚶砉W(xué)院在進(jìn)行激光加工及銀燒結(jié)等混合制造工藝研究的同時,還嘗試用銅燒結(jié)把門級驅(qū)動直接結(jié)合到功率模塊中去;瑞典的零部件供應(yīng)商與車企 VOLVO 一起進(jìn)行了高密度混合封裝的設(shè)計研究;University ofApplied Sciences Kiel 進(jìn)行了封裝與模組設(shè)計一體化的嘗試。多個商業(yè)公司開發(fā)了p2Pack(die Embedded PCB Package)、ECP(Embedded Component Package)、OCM (Open Constructure Module)等多種離散型的封裝架構(gòu),有些架構(gòu)允許在PCB表面安裝控制系統(tǒng)零件,而在 PCB 內(nèi)層嵌入了引線框架,其間的空腔用以容納功率器件、門級驅(qū)動及其他分立元器件等 [19] 。
5.3 封裝的高溫化趨勢
為了獲得系統(tǒng)設(shè)計所要求的更高功率密度,今天很多工程師不得不把更多的元器件塞入到極為狹小的空間中,造成了單位體積中需要排出熱量的急劇增加,進(jìn)而要求封裝技術(shù)顯著提高導(dǎo)熱散熱能力。另外,為了適應(yīng)較高環(huán)境溫度的應(yīng)用場景,例如沒有液冷條件的移動功率應(yīng)用,半導(dǎo)體器件本身就要面對更高結(jié)溫的工作條件。因此,除了設(shè)法提高導(dǎo)熱散熱能力,功率器件及其驅(qū)動器件的封裝不可避免地走向了高溫化。知名技術(shù)市場趨勢研究公司 YOLE 早在 2012 年就明確指出,多年來功率電子器件的結(jié)溫一直在持續(xù)提高 [33] ,YOLE 對功率器件結(jié)溫的預(yù)測見圖 10。
從圖 10 可以看出,從 1980 年到 2015 年,硅基功率半導(dǎo)體的最高結(jié)溫從 100 ℃提高到了 150 ℃;然后由于 WBG 半導(dǎo)體的出現(xiàn),自 2015 年起,結(jié)溫的上升趨勢進(jìn)一步加速并分化為 2 個分支走向。現(xiàn)在 SiC 器件的結(jié)溫普遍到了 175 ℃,到 2025 年將會普及到200 ℃,而到2030 年則會提高到 225 ℃左右 [33] 。SiC 器件本身的最高耐受節(jié)溫可以輕易超越 500 ℃,目前常見的 SiC 器件標(biāo)稱結(jié)溫 175 ℃(少數(shù)標(biāo)稱 200 ℃)是由于現(xiàn)有封裝技術(shù)的限制所致。
有許多面向未來的應(yīng)用已推動功率半導(dǎo)體最高結(jié)溫的上升。如 2019 年 ORNL 在項目報告中把門級驅(qū)動的工作環(huán)境溫度提升到 150 ℃作為一項挑戰(zhàn),原因是為了進(jìn)一步提高功率密度,ORNL 正在嘗試把逆變器集成到電機(jī)端蓋或者電機(jī)筒體上 [13,16-18] 。歐洲中小功率的電動助力轉(zhuǎn)向已經(jīng)實現(xiàn)了完全的機(jī)電融合,為了減小尺寸和重量,柏林技術(shù)大學(xué)、卡爾斯魯厄理工學(xué)院、ZF 公司、YASA 公司等都在努力把ETDS 融合到牽引電機(jī)上去 [19] ,所有類似的努力都導(dǎo)致電力牽引驅(qū)動越來越靠近作為熱源的電機(jī),而且電機(jī)的軸溫也伴隨著轉(zhuǎn)速在持續(xù)提高,因此不僅需要功率器件提高最高耐受結(jié)溫,也需要與之匹配的高溫門級驅(qū)動方案。
針對結(jié)溫持續(xù)上升的應(yīng)用需求并配合 SiC 器件的普及,CISSOID 公司推出了耐高溫的 SiC 門級驅(qū)動芯片和方案(CMT 系列 175 ℃結(jié)溫,CHT 系列 225 ℃結(jié)溫)。CISSOID 長期從事高溫半導(dǎo)體器件的設(shè)計制造,其核心技術(shù)包括兩個主要方面:第一,高溫芯片技術(shù),基于耐高溫的芯片結(jié)構(gòu)設(shè)計及先進(jìn)的絕緣體上硅(Silicon on Insulator,SoI)制造工藝;其二,高溫封裝技術(shù),其金屬陶瓷封裝的高溫器件系列最高耐受結(jié)溫可達(dá) 225 ℃以上 [33] 。且與絕大多數(shù)硅基器件約 1000 h 的高溫壽命不同,CISSOID 的高溫器件可在 175 ℃結(jié)溫條件下長期穩(wěn)定連續(xù)運(yùn)行達(dá) 15 年之久。SiC 等半導(dǎo)體的高功率密度和高溫應(yīng)用越來越受到重視,這些應(yīng)用的領(lǐng)域包括但不限于航空應(yīng)用、電動汽車動力總成深度集成、移動儲能等,將會給整個功率電子產(chǎn)業(yè)帶來深刻影響,并推動封裝技術(shù)的持續(xù)進(jìn)步。
6 結(jié)論
為了應(yīng)對 SiC 等新型功率半導(dǎo)體帶來的挑戰(zhàn),封裝技術(shù)的發(fā)展路線是多徑的。封裝技術(shù)的發(fā)展是一個綜合的系統(tǒng)工程,牽涉到基礎(chǔ)材料、構(gòu)型設(shè)計、制造工藝及制造裝備,還有測試、驗證及建模等細(xì)分領(lǐng)域,有些是基于現(xiàn)有技術(shù)和工藝的漸進(jìn)改良,有些則是另辟蹊徑的超越創(chuàng)新,很多研究工作在細(xì)分專業(yè)的邊緣展開。封裝技術(shù)的發(fā)展為充分發(fā)揮 SiC 等新型半導(dǎo)體的性能優(yōu)勢奠定了基礎(chǔ)。
業(yè)界正從基礎(chǔ)材料、連接工藝、構(gòu)造形式等方面展開探索。漸進(jìn)改良的、混合型的銅基同質(zhì)連接等基本滿足了目前的需求;要充分發(fā)揮 SiC 等 WBG 器件的性能優(yōu)勢,封裝技術(shù)的前沿研究正在尋求革命性的發(fā)展。鑒于銀燒結(jié)界面極為優(yōu)異的導(dǎo)電導(dǎo)熱能力、剪切力及寬幅度熱沖擊和功率循環(huán)周次能力,今天多數(shù)的研究指向了銀燒結(jié)技術(shù),特別是低壓和無壓銀燒結(jié)的材料和工藝。
模塊封裝的疊層結(jié)構(gòu)創(chuàng)新以及封裝的離散化、高溫化也是新型封裝技術(shù)的發(fā)展方向,決定了SiC 等器件高功率密度和高溫應(yīng)用的實現(xiàn)。單一層面的技術(shù)改良難以滿足日趨苛刻的應(yīng)用要求,對于 SiC 器件而言,封裝技術(shù)的未來發(fā)展方向在于銀燒結(jié)工藝、新型疊層結(jié)構(gòu),以及離散化、高溫化等方面的深度融合。未來5~10 年,作為核心連接技術(shù)的銀燒結(jié)將會得到充分的發(fā)展,其性價比也會逐漸為各種主流應(yīng)用所接受。
審核編輯 黃宇
-
封裝
+關(guān)注
關(guān)注
128文章
8535瀏覽量
144833 -
功率密度
+關(guān)注
關(guān)注
0文章
92瀏覽量
17080 -
碳化硅
+關(guān)注
關(guān)注
25文章
3024瀏覽量
50089
發(fā)布評論請先 登錄
碳化硅功率器件有哪些特點
碳化硅功率器件的種類和優(yōu)勢
先進(jìn)碳化硅功率半導(dǎo)體封裝:技術(shù)突破與行業(yè)變革
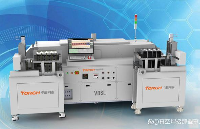
國內(nèi)碳化硅功率器件設(shè)計公司的倒閉潮是市場集中化的必然結(jié)果
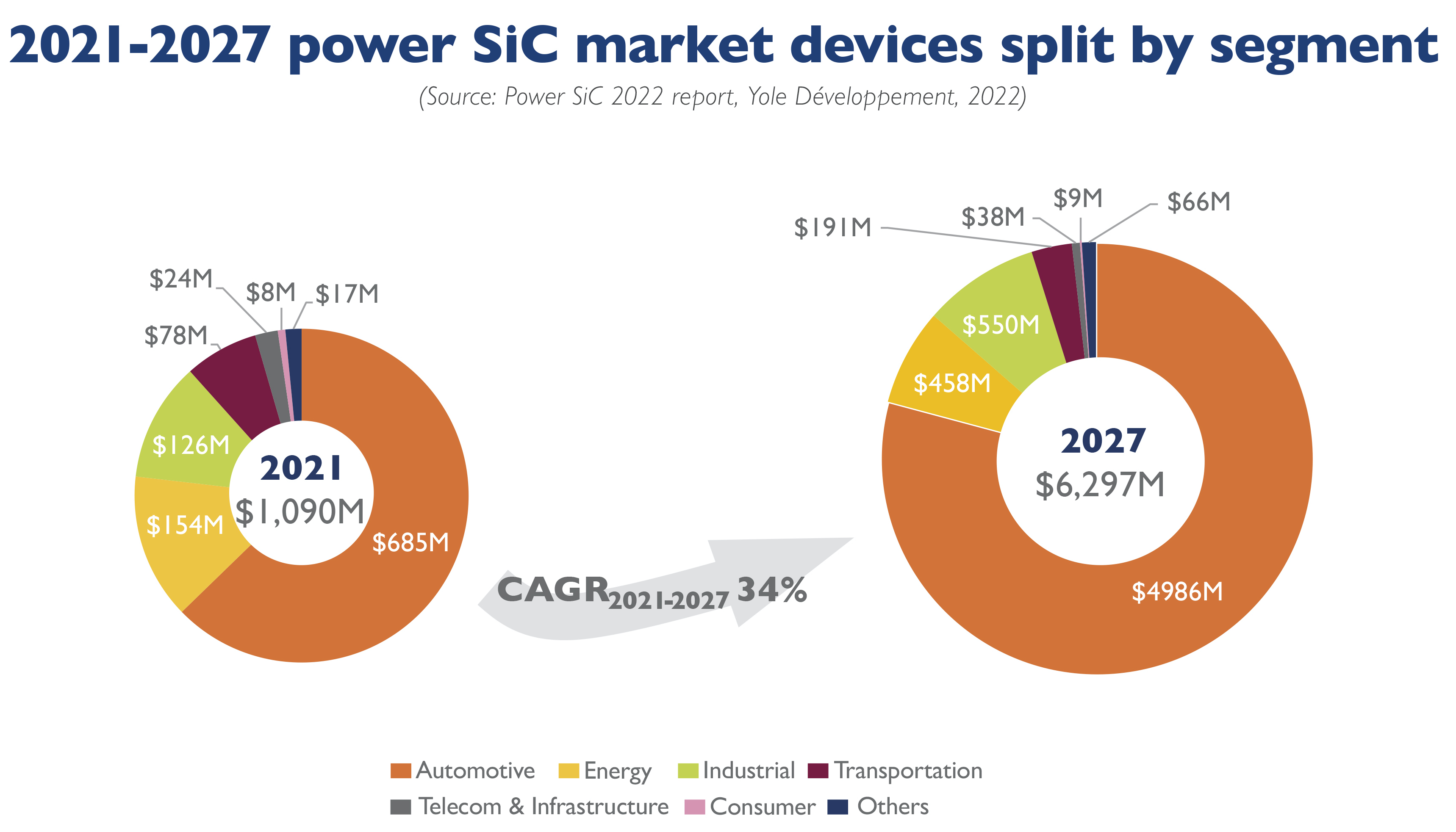
碳化硅功率器件的封裝技術(shù)解析
什么是MOSFET柵極氧化層?如何測試SiC碳化硅MOSFET的柵氧可靠性?
碳化硅功率器件的工作原理和應(yīng)用
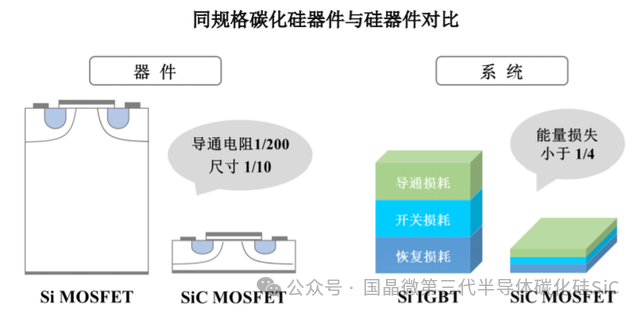
碳化硅功率器件的優(yōu)勢和應(yīng)用領(lǐng)域
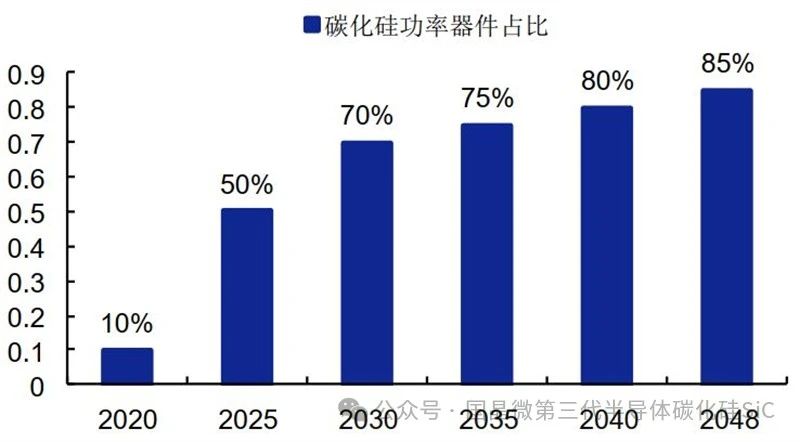
碳化硅功率器件的原理簡述
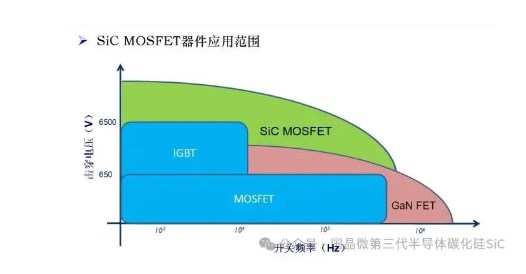
碳化硅功率器件的優(yōu)點和應(yīng)用
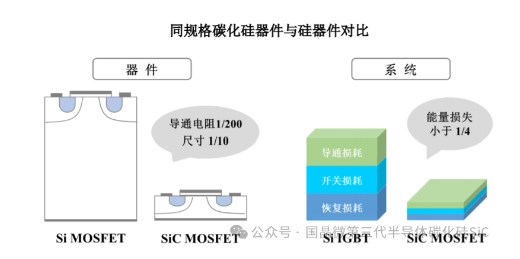
碳化硅功率器件的技術(shù)優(yōu)勢
碳化硅功率器件有哪些優(yōu)勢

探究電驅(qū)動系統(tǒng)中碳化硅功率器件封裝的三大核心技術(shù)
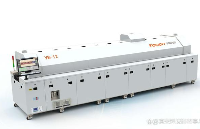
碳化硅器件的應(yīng)用領(lǐng)域和技術(shù)挑戰(zhàn)
碳化硅功率器件的優(yōu)勢和分類
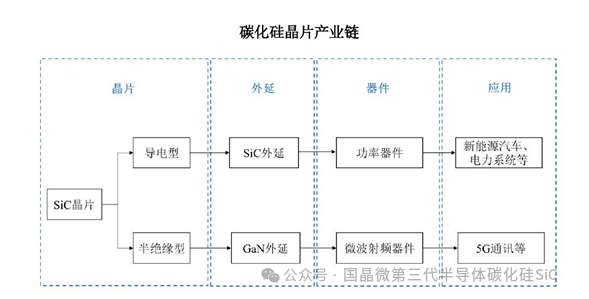
評論