對于電驅系統(tǒng)的仿真分析,傳統(tǒng)方法是將不同的結構分割,然后再分領域的進行設計仿真分析。不同的仿真分析之間相互獨立,系統(tǒng)級集成往往在后期階段完成?;蛘卟捎枚辔锢韴雎?lián)合仿真的方法,創(chuàng)建二維或者三維模型,采用有限元方法進行仿真分析,這些模型相對精度較高,但是其求解過程往往需要消耗大量的時間和計算資源。
圖1 傳統(tǒng)集成分析流程:順序仿真 (上圖) 和 三維多物理場仿真 (下圖)
隨著開發(fā)周期壓縮的壓力和產(chǎn)品集成度的提高,采用集成化的方式進行系統(tǒng)級的設計仿真,同時兼顧電機和控制器的性能的方式應運而生。即在系統(tǒng)級采用一維模型,設計空間或者實時仿真。在部件級采用一維、二維和三維模型的混合模型。
圖2 集成化的系統(tǒng)仿真
在其中,一維系統(tǒng)仿真往往都會采用Simcenter Amesim來搭建,不同層級的零部件模型會通過聯(lián)合仿真或者模型降階的方法與系統(tǒng)模型聯(lián)合,最終形成一個包含各個層級維度的系統(tǒng)模型。Simcenter 中的工具及其直接和間接連接提供了一個獨特的平臺,可用于探索傳統(tǒng)設計方法的替代方案。同時Simcenter將整個過程做的更加自動化、接口更加方便,以同時方便設計工程師和仿真工程師來使用。下面我們將舉幾個典型的案例予以說明。
動力性能迭代驗證
獲得電機的詳細設計參數(shù)后,工程師利用Simcenter Amesim將這些參數(shù)導入整車及電驅動系統(tǒng)的詳細模型中,完成對電機詳細設計的整車級迭代驗證。驗證內容包括初始設計階段所述動力性和經(jīng)濟性的各項指標。該階段所用到的電驅動系統(tǒng)模型較初始階段的功能模型顆粒度更為精細,具體表現(xiàn)為電驅動系統(tǒng)模型對控制器和電機本體進行區(qū)分,電機本體外特性不再采用用戶定義的方式,而是根據(jù)電機設計部門給出的詳細參數(shù)計算得到。同樣的,控制器功率單元的效率也能夠根據(jù)器件手冊中的半導體工作特性計算得到。綜上所述,電驅動系統(tǒng)的詳細動力性能在這一階段得到了驗證。
圖3 加載電機詳細電磁性能的整車級指標驗證
散熱性能分析及熱管理策略
電機內部溫升過高不僅會縮短電機內部絕緣材料的壽命,而且會降低電機的運行效率,使得發(fā)熱量增加,造成電機溫度進一步上升,形成惡性循環(huán),嚴重影響電機壽命和運行安全性。據(jù)統(tǒng)計,30%~40%的永磁電機失效是由電機溫升過高引起的。因此,采用高效的散熱系統(tǒng)抑制電機溫升是電機向高效率、高穩(wěn)定性和高可靠性方向發(fā)展的關鍵。
相較于風冷散熱,液冷散熱具有更高的換熱效率,可以達到前者的50倍,適用于電機發(fā)熱量大,熱流密度高的散熱場合。因此,車用電機的多采用水冷或油冷這兩種液冷散熱方式。水冷散熱系統(tǒng)的流道結構是影響其冷卻效率的關鍵因素,工程師通過優(yōu)化流道結構參數(shù)提高水冷散熱的冷卻效率。通過通過增加流道數(shù)量、在冷卻流道中添加擾流結構和增加冷卻水流量等方式可以有效提高冷卻效率,但同時也導致壓力損失明顯增大。因此,在實際應用中需要綜合考慮水道換熱能力和壓力損失以設計合適的水道結構。直接油冷散熱系統(tǒng)的冷卻油與電機內部發(fā)熱部件直接接觸,具有極高的散熱效率,是解決高功率密度電機散熱難題的有效方案,目前正在被越來越多的電驅動系統(tǒng)供應商所采納。但直接油冷循環(huán)系統(tǒng)的設計復雜度比水冷循環(huán)的設計更加復雜,需要較為詳細的仿真驗證與評估過程才能使系統(tǒng)散熱效率達到最佳。
無論是水冷散熱還是油冷散熱系統(tǒng),都涉及到液冷循環(huán)回路的流量和壓力計算,以及冷卻工質和電機本體間的換熱計算。通常采用的方法是通過CFD和熱網(wǎng)絡法相結合的方式,利用CFD精細化的網(wǎng)格劃分計算得到電機液冷循環(huán)系統(tǒng)在典型工況下的穩(wěn)定流動狀態(tài)以及換熱效果,然后通過離散化處理,在多學科系統(tǒng)仿真環(huán)境中得到電機本體、減速器、以及液冷循環(huán)系統(tǒng)的熱網(wǎng)絡模型,進而加載動態(tài)工況完成進一步的散熱設計驗證。
采用Simcenter Amesim可以幫助工程師快速地從電機設計工具如Simcenter SPEED、MotorCAD導入當前設計所對應地電機本體熱網(wǎng)絡模型,同時,用戶可以在Simcenter Amesim環(huán)境下對該熱網(wǎng)絡模型進行任意調整已完成電機本體、減速器、液冷循環(huán)系統(tǒng)的集成,從而在保持仿真精度的同時,大大提升仿真閉環(huán)動態(tài)工況下的仿真計算速度。
圖4 電機熱網(wǎng)絡法的仿真評估的自動化實現(xiàn)流程
圖5 液冷循環(huán)系統(tǒng)的流量分配仿真評估
控制器功率模塊散熱設計
控制器功率模塊為電機控制器的核心部件,電機驅動系統(tǒng)的大容量控制需求,使功率模塊向高頻化、大功率化以及高度集成化方向發(fā)展。IGBT/SiC是目前車用電機控制器功率模塊普遍采用的半導體技術,同時也是電機控制器的主要熱源,在處理波動的功率流工作過程中,IGBT/SiC產(chǎn)生的功率損耗導致其結溫的升高與波動,導致芯片性能衰減,甚至造成鍵合線斷裂等失效形式。因此,進行結溫估算研究對于提高電驅動系統(tǒng)可靠性,實現(xiàn)精準熱控制及部件保護具有重要意義。
目前常用的結溫估算模型例如Foster熱網(wǎng)絡法,需要通過熱阻測試儀,例如:T3STER,或基于CFD的專業(yè)電子散熱仿真工具,例如:Simcenter FloTherm,測量或計算得到功率模塊的降階熱網(wǎng)絡模型。該熱網(wǎng)絡模型可以直接導入Simcenter Amesim中與電驅動系統(tǒng)其他部件模型集成,并應用于動態(tài)閉環(huán)工況的仿真。工程師采用上述方法能夠大大縮減仿真計算耗時,從而加快功率模塊散熱的設計研發(fā)速度。
圖6 功率驅動模塊的降階熱模型與Simcenter Amesim中整車及液冷系統(tǒng)集成
NVH性能集成驗證
車用永磁同步電動機具有結構緊湊、功率密度高、氣隙磁通高以及轉矩慣性比高等優(yōu)點,電機輸出轉矩平滑度是衡量驅動系統(tǒng)性能的重要指標,而電機電流中的高次諧波是影響電機輸出轉矩平滑度的主要因素。造成電機電流諧波因素主要有兩方面原因:
1)電機本體方面,如齒槽效應、繞組分布形式、磁路磁飽和效應、轉子磁極結構等引起的電機氣隙磁場畸變;
2)逆變器方面,如開關器件的死區(qū)時間、管壓降等非線性特性。
同時,減速器齒輪的剛度和慣量也會引起電驅動系統(tǒng)輸出軸上的扭矩波動。因此,在設計電驅動系統(tǒng)的時需要對各因素引起的輸出扭矩波動進行綜合考慮和優(yōu)化。
圖7 系統(tǒng)仿真中的NVH性能評估與優(yōu)化
采用Simcenter Amesim多物理系統(tǒng)仿真平臺搭建的電驅動系統(tǒng)及整車駕駛性模型,可以精確復現(xiàn)電驅動系統(tǒng)各部件引起的扭矩波動。首先工程師將電機電磁仿真所獲得磁鏈及鐵損參數(shù)Map文件導入Simcenter Amesim,該參數(shù)文件用于精確計算電機轉子在不同角度與電流幅值相位下的電磁扭矩。同時Simcenter Amesim中搭建的詳細的驅動電路模型可以體現(xiàn)由PWM脈寬調制所產(chǎn)生相電流高階諧波。工程師通過仿真可以對電驅動系統(tǒng)輸出扭矩波動的各階分量進行跟蹤分析,同時開發(fā)用于抑制波動的軟件控制策略,如諧波注入功能。
審核編輯:湯梓紅
-
控制器
+關注
關注
114文章
17072瀏覽量
183905 -
電機
+關注
關注
143文章
9281瀏覽量
149156 -
仿真分析
+關注
關注
3文章
106瀏覽量
33925 -
電驅系統(tǒng)
+關注
關注
0文章
121瀏覽量
2732
原文標題:電驅動系統(tǒng)性能集成化分析
文章出處:【微信號:BasiCAE,微信公眾號:貝思科爾】歡迎添加關注!文章轉載請注明出處。
發(fā)布評論請先 登錄
集成化的Speaker Box設計
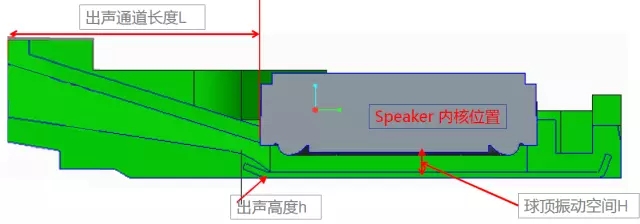
集成化信息化信號采集處理系統(tǒng)有哪些
分光光度計系統(tǒng)集成化設計及研究
集成化建筑設計系統(tǒng)
ADI高度集成化的設計大大簡化控制系統(tǒng)設計
電驅動系統(tǒng)集成包括哪些
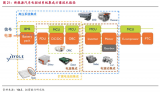
電驅動產(chǎn)品系統(tǒng)集成化趨勢明顯,威邁斯IPO提前布局把握機遇
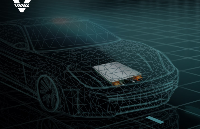
評論