摘要:鋰電池技術(shù)的逐漸成熟使之應(yīng)用在各個行業(yè)中,其產(chǎn)品廣泛應(yīng)用在電網(wǎng)儲能、智能家電、通訊儲能、新能源汽車等領(lǐng)域。其中鋰電池的熱管理技術(shù)是電池組延長壽命、運行安全的重要保障。鋰電池?zé)峁芾硐到y(tǒng)對電池的安全和穩(wěn)定性起著至關(guān)重要的作用,本文對現(xiàn)有的散熱技術(shù)進行了廣泛的介紹和闡述。首先總結(jié)了電池?zé)崃康漠a(chǎn)生、傳熱和熱量分布,其次討論了電池散熱系統(tǒng)中風(fēng)冷、液冷、熱管和相變材料等四種方式的工作原理和特點,最后結(jié)合電池散熱系統(tǒng)的發(fā)展需求,提出未來的散熱系統(tǒng)發(fā)展方向和可實行的技術(shù)。 關(guān)鍵詞:鋰離子電池;熱管理;傳熱系數(shù);相變材料
1 引言
INDUSTRIALINTERNET
隨著經(jīng)濟的快速發(fā)展,新能源技術(shù)的不斷開 發(fā),電動汽車逐漸成為交通工具的主流趨勢之一。鋰離子電池作為電動汽車的主要動力源,對電動汽車的安全性、行駛里程、使用性能和壽命起著至關(guān)重要的作用。鋰離子電池具有工作電壓高、體積小、能量高、無記憶效應(yīng)、循環(huán)壽命長等優(yōu)點,已經(jīng)成為了目前電動汽車中使用最廣泛的電池之一。
為滿足電動汽車高電壓和大容量的需求,電池單體采用最常見的串并聯(lián)相結(jié)合的方式進行使用。在電動汽車運行過程或充電過程中,電池處于充放電的環(huán)境,此時的電池溫度會發(fā)生很大的變化。若不及時散熱,熱量在電池模塊內(nèi)持續(xù)積累, 會導(dǎo)致電池模塊熱量不斷上升和不均勻擴散。鋰電池內(nèi)部化學(xué)成分耐熱性較差,因此在高溫下會加速反應(yīng),導(dǎo)致鋰離子電池內(nèi)部結(jié)構(gòu)產(chǎn)生質(zhì)變,最終造成嚴重的安全后果。同時,鋰電池也不適合在低溫環(huán)境下工作,低溫下的鋰電池活性會下降。因此, 需要一個高效的電池?zé)峁芾硐到y(tǒng)(Battery thermal management system,BTMS)來保持適當?shù)碾姵毓ぷ鳒囟确秶?,以防止溫度過高或過低所帶來的不利影響。一般來說,電池溫度每升高 10℃,內(nèi)部化學(xué)反應(yīng)速率增大一倍,其壽命減少一半。通過對容量為 1.8 A·h 的索尼 18650 鋰電池的循環(huán)性能進行研究,結(jié)果表明,在 25 ℃和 45 ℃工作溫度下鋰電池進行 800 次充放電循環(huán)后,電池容量分別下降 31% 和 36%;當工作溫度為 50 ℃時,500 次充放電循環(huán)后電池容量下降 60%。對于鋰電池,工作溫度超過 50 ℃,電池的使用壽命就會隨之下降。電池的容量和功率可以用來表征電池性能的優(yōu)劣,高溫下由于鋰電池內(nèi)部的活性物質(zhì)發(fā)生死區(qū)和析鋰現(xiàn)象,導(dǎo)致電池的容量減少,而電池功率也因阻抗增加而降低。表 1 總結(jié)了鋰離子電池容量的衰減和溫度的關(guān)系,鋰電池最佳工作溫度范圍是 25 ℃~40 ℃。
表 1 鋰離子電池容量在不同溫度條件下的衰減總結(jié)
隨著電動汽車的發(fā)展和動力系統(tǒng)功率的不斷提 升,電池組的密度也比以往增加更多,快速充電的需求導(dǎo)致電池在大電流充放電時產(chǎn)生更多的熱量。在這種趨勢下設(shè)計出合理的電池?zé)峁芾硐到y(tǒng)成為焦點,需要在高溫下進行快速散熱、低溫條件下能夠進行加熱或保溫,以提升電動汽車的整體性能。
電池?zé)峁芾硐到y(tǒng)可分為電池散熱系統(tǒng)和電池加熱系統(tǒng),本文重點講述電動汽車鋰電池的散熱系統(tǒng)。
目前較成熟的散熱系統(tǒng)根據(jù)傳熱介質(zhì)可分為四部分,分別為風(fēng)冷、液冷、相變材料冷卻 (Phase-change material,PCM)和熱管冷卻。電池散熱系統(tǒng)分類如圖 1 所示。
圖 1 電池冷卻系統(tǒng)分類
在電池散熱系統(tǒng)方面,國內(nèi)外學(xué)者已經(jīng)進行了 相關(guān)整理和綜述,主要側(cè)重點為橫向?qū)Ρ龋?縱向?qū)Ρ壬婕暗妮^少。本文對電動汽車鋰離子電池散熱管理的研究進展進行了分析及梳理,總結(jié)了各研究學(xué)者在鋰電池散熱管理中所做出的努力以及優(yōu)勢,旨在未來進一步優(yōu)化 BTMS,并提出前沿的技術(shù)進行指導(dǎo)。
本文第 2 節(jié)論述了鋰電池的產(chǎn)熱原理及模型, 第 3 節(jié)詳細介紹鋰電池不同散熱系統(tǒng)的性能和優(yōu)缺點。最后在第 4 節(jié)進行總結(jié)并對未來的散熱技術(shù)發(fā)展方向做出了展望。
2 鋰電池產(chǎn)熱原理及模型
INDUSTRIALINTERNET
2.1 電池產(chǎn)熱原理分析
以鋰離子電池為例,其產(chǎn)熱來源主要有三種形式,分別為極化熱( ) Qp、內(nèi)阻焦耳熱(Qj)和化學(xué) 反應(yīng)熱( Qr)。(1) 極化熱電池極化主要包括活性極化和濃差極化,在充放電過程中取正值。極化熱公式為
式中, JiLi為鋰離子交換的電流密度,ηi為過電勢, I 為電池充放電電流大小, Rp為電池極化內(nèi)阻。(2) 內(nèi)阻焦耳熱內(nèi)阻焦耳熱是電池充放電過程中最主要的熱量來源。該值始終為正值,充放電過程中都產(chǎn)生熱量, 公式如下所示
式中, R?為電池內(nèi)阻之和。(3) 化學(xué)反應(yīng)熱化學(xué)反應(yīng)熱為鋰電池內(nèi)部因鋰離子的活動而產(chǎn) 生的熱量,在放電時熱量取正值,充電時取負值。反應(yīng)熱公式為
式中,H 為焓(J),S 為熵(J/K),G 為吉布斯自由能 (J),ΔΔ Δ G H TS = ? ,T 為熱力學(xué)溫度(K),n為電子數(shù), F 為法拉第常數(shù)。因此鋰電池總產(chǎn)熱量可以表示為
則電池平均產(chǎn)熱速率可用V 來代替
式中,Q 為電池工作時間總的產(chǎn)熱量(J),t 為電池工作時間(s)。
2.2 電池?zé)釘?shù)學(xué)模型
分析電池?zé)崮P头椒ㄓ泻芏?,可通過物理機制 建立電熱模型、電化學(xué)模型和熱失控模型,也可通過不同維度建立電池一維對稱、二維或三維模型。電熱模型最初是由美國國家可再生能源實驗室 的 Steve Burch 提出,后由 Johnson改進,模型的散熱量計算為
式中, Reff為有效熱阻,即
式中,h為表面換熱系數(shù),由電池的溫度決定,即
式(6)中電池周圍的溫度Tair為
利用 Li-ion 電池的熱濫用三維模型來模擬電池 熱模型,模型的熱源為
式中,qjoul和qcombustion分別表示焦耳熱與反應(yīng)熱, abuse q 為熱濫用發(fā)生后額外的產(chǎn)熱量,qsei為 SEI 分解反應(yīng)產(chǎn)熱,qne為負極活性材料反應(yīng)熱,qpe為 正極活性材料反應(yīng)熱,qele為電解液分解反應(yīng)熱,qnb為正負極之間的反應(yīng)熱。均由以下公式計算可得
式中,i = sei ne , 時, x = c ,Wc為特定體積的比碳 含量;i = pe 時, x = p ,Wp為特定體積的正活性 成分;i = ele , x = e ,We為特定體積的電解質(zhì)含 量;Ri,Ai,Ea,sei,Ea,pe,Ea,ete為反應(yīng)參數(shù),Hi為比熱釋放量, csei為 SEI 中穩(wěn)定的鋰離子無量綱數(shù)量, cneg為碳中鋰離子無量綱數(shù)量, tsei為 SEI 中鋰離子的數(shù)量,α 為轉(zhuǎn)換度, ele c 為電解質(zhì)的無量綱濃度。
3 鋰電池散熱系統(tǒng)
INDUSTRIALINTERNET
散熱系統(tǒng)能夠使電動汽車以最佳狀態(tài)運行,為 確保鋰電池的安全性、使用壽命和性能,需要對電池的溫度進行實時監(jiān)測和及時降溫以避免動力電池的熱失控。以下將對電池散熱的幾種不同方式進行詳細介紹。
3.1 空氣冷卻系統(tǒng)
空氣冷卻又叫風(fēng)冷,是目前使用最廣泛的電池 散熱方式,可與整車的行駛特性設(shè)計相結(jié)合。可通過車速形成的自然風(fēng)將熱量帶走,也可通過風(fēng)扇運轉(zhuǎn)產(chǎn)生強制氣流。自然對流具有簡單易行,低成本, 散熱過程多以自然對流為主等優(yōu)點,缺點為風(fēng)力不可控。強制對流相比自然對流更可靠,更易于維護, 因此成為常見的電池冷卻方式。強制對流的缺點是電池內(nèi)的溫度分布不均勻,由于空氣本身的特性, 冷卻效果有一定的局限性。3.1.1 電池排列方式為提高電池溫度分布的均勻性與冷卻效率,電 池組內(nèi)單體電池排列方式的研究是必不可少的。常見的電池排列方式有順排、叉排和梯形排列三種,如圖 2 所示。順排方式為單體電池在電池箱內(nèi)呈整齊有序的 排放,如圖 2a 所示。外部冷空氣從電池縫隙穿過,優(yōu)點為氣流阻力較小,缺點為不易受到擾動而產(chǎn)生湍流漩渦,與電池接觸面較小,對流換熱較小,因此散熱效率不高,一般不采用。
圖 2 常見的電池排列方式
叉排方式是將相鄰的兩個電池彼此錯開排列, 如圖 2b 所示。外部冷空氣通過上一層電池后直接穿過下一層電池的表面,然后繞過該電池表面流向電池兩側(cè)的間隙。增加了冷空氣與電池接觸的面積, 提了電池表面的對流換熱系數(shù),進而提高了散熱效率,缺點為流動阻力損失較大。梯形排列方式在氣流尾部減少電池的個數(shù),縮小冷空氣流通方向的截面積,從而增加換熱系數(shù), 如圖 2c 所示。采用梯形排列方式能夠平衡上下游電池的散熱效果,可使電池組中的單體電池溫度分布呈現(xiàn)出較好的一致性。但是在使用 32(4×8)個鋰電池進行強制風(fēng)冷試驗研究中,將電池組分別采用順排、交錯和交叉三種方式進行排列,交錯和交叉方式如圖 3 所示。采用三種典型排列方式的鋰電池組在 20 ℃工作環(huán)境下進行試驗,放電速率為 2C。風(fēng)洞設(shè)置在 4 列電池側(cè),當進氣速度從 0.6 m·s ?1增加到 1 m·s?1時, 順排、交錯和交叉排列的電池組最大溫升分別降低了 10 ℃、7 ℃和 7 ℃。隨著進氣速度的增加,三種排列方式的電池組溫度呈負指數(shù)形式減少。該結(jié)果與文獻截然不同,在電池組中順排方式表現(xiàn)出更好的冷卻性能,其次是交錯排列,最后是交叉排列。通過上述兩個風(fēng)冷熱管理散熱性能的試驗結(jié)果 對比可知,電池組的排列順序、進出風(fēng)口的位置以及風(fēng)速的大小等因素都會影響電池的散熱效果。電池組個數(shù)較少時,風(fēng)速的提高和電池組的排列順序?qū)ι岬男阅芎蜏囟确植嫉木鶆蛐杂绊懽兓淮蟆.旊姵亟M個數(shù)較多、電池包密度較大時,三種排列方式的上下游風(fēng)壓的不同會導(dǎo)致每種方式的散熱效果呈現(xiàn)出不一致性,甚至?xí)蝻L(fēng)速的增加加劇風(fēng)冷系統(tǒng)能量的二次消耗,與提高電池組效率和散熱性能相矛盾。電動汽車中電池個數(shù)往往成千上萬,數(shù)量遠遠比試驗的多。因此當儲能系統(tǒng)中電池個數(shù)較少時, 可采用圖 2 中梯形排列方式;當儲能系統(tǒng)電池個數(shù)較多時,可采用圖 3 中的順排方式。
圖 3 交錯、交叉陣列的電池組
3.1.2 串行通風(fēng)與并行通風(fēng)單體電池間的溫度差異與其在電池組內(nèi)的位置有很大關(guān)系,一般情況下,下邊緣位置相對于 中心位置散熱較好,溫度較低。因此在布置散熱設(shè)計時,應(yīng)盡量保證單體電池的溫度均勻性。根據(jù)通風(fēng)方式,可分為串行通風(fēng)和并行通風(fēng),如圖 4 所示。
圖 4 串行通風(fēng)和并行通風(fēng)方式
在串行通風(fēng)的電池模塊中,使用由 8 塊 26650 動力電池(2.3 A·h,3.3 V)進行 4 個串聯(lián)和 2 排并聯(lián)組成的電池組模型,電池模塊的電壓為 14.8 V,容量為 4.6 A·h。該試驗平臺包含充放電裝置,溫度、風(fēng)速、壓力檢測器,風(fēng)洞裝置等,風(fēng)洞裝置能 夠有效控制風(fēng)速大小,風(fēng)速的大小范圍為 0.5 m·s?1~30 m·s?1。試驗借助 ANSYS/FLUENT 軟件對該模塊進行二維數(shù)值模擬研究,CFD 模型示意圖和網(wǎng)格劃分結(jié)果如圖 5 所示,網(wǎng)格采用四邊形非結(jié)構(gòu)網(wǎng)格,但該數(shù)值模型未考慮到流體參數(shù)和流場在 z 軸的變化。
圖 5 CFD 模型示意圖和網(wǎng)格劃分
CHEN 等進行了各種關(guān)于提高空氣模塊冷卻效率的研究。使用計算流體動力學(xué)方法的數(shù)值解決方案以及優(yōu)化算法來改進由棱柱形電池組成的風(fēng)冷電池組,如圖 6 所示。電池間距分布、氣流速率、入口和出口的寬度、增壓室長度和位置是數(shù)值函數(shù)中要優(yōu)化的目標。電池系統(tǒng)由 8 個方形電池組成, 在 5C 放電倍率下進行測試。試驗結(jié)果表明,當入口和出口位于增壓室的中間時可以實現(xiàn)電池的高效冷卻。與 Z 型熱管理模型相比,電池間的最高溫度和最大溫差分別降低了 4.3 ℃和 6.0 ℃。
圖 6 風(fēng)冷電池組模塊
基于風(fēng)冷熱管理的優(yōu)點包括:運行過程中的安 全性與可靠性、所需材料簡單且易于實現(xiàn)、產(chǎn)生有害氣體時能夠及時有效通風(fēng);與液體和相變材料相比,空氣作為冷卻介質(zhì)的降溫能力明顯不足,且僅適用于低密度電池。表 2 對風(fēng)冷系統(tǒng)中的一些重要參數(shù)進行了總結(jié)。表 2 風(fēng)冷系統(tǒng)的進展總結(jié)
龐大的電池組產(chǎn)生的熱量使得主動式風(fēng)冷系統(tǒng) 隨之增加體積,從而影響電動汽車的性能和乘客的舒適度。為解決風(fēng)冷系統(tǒng)面臨的問題并提高其性能, 眾多學(xué)者開始研究將其他冷卻介質(zhì)加入到風(fēng)冷系統(tǒng)中。
3.2 液體冷卻系統(tǒng)
與基于風(fēng)冷的電池?zé)峁芾硐到y(tǒng)相比,基于液 體的熱管理具有更高的傳熱系數(shù)和比熱容,對提高電池組能量密度和熱管理能力有著更顯著的效果。表 3 為水在不同溫度下的導(dǎo)熱系數(shù)。根據(jù)電池與冷卻液接觸的方式,液冷系統(tǒng)可分為直接接觸式和間接接觸式兩種。根據(jù)電池液冷散熱的結(jié)構(gòu)又可分為主、被動兩種方式,被動式系統(tǒng)中, 冷卻液與外界空氣進行熱量交換,將電池?zé)崃克统?;主動式系統(tǒng)中,電池?zé)崃客ㄟ^液-液交換的方式送出。
表 3 不同溫度下水的導(dǎo)熱系數(shù)
3.2.1 直接接觸式冷卻冷卻液直接與電池或電池模塊表面接觸為直接 接觸式液冷,相較于風(fēng)冷能夠更好地進行電池散熱。冷卻液的特點為導(dǎo)熱率高且絕緣,但由于使用的冷卻液體流動性不強,因此散熱效果也會受到一定的影響。兩相冷卻技術(shù)在直接接觸式液冷系統(tǒng)中是一種 較前沿的冷卻技術(shù)。選擇 3M 公司濃度為 99.5% 的 Novec7000 電子氟化液作為冷卻劑,冷卻劑液體在常壓下沸點為 34 ℃。通過試驗發(fā)現(xiàn),即使在放電倍率為 5C 的條件下,冷卻劑也可將電池組的溫度保持在 35 ℃左右。同時試驗結(jié)果還證明了,在沸點以下的冷卻液的冷卻效果超過了基于空氣的熱管理系統(tǒng),當冷卻液的溫度達到沸點時,沸騰過程可進一步將電池的溫度趨于一致。在冷卻液沸騰過程中會受到大氣壓的影響,因此有必要研究如何通過控制冷卻液周圍的壓力來主動控制沸騰強度。3.2.2 間接接觸式冷卻間接接觸式冷卻系統(tǒng)是通過裝有冷卻液的翅片 或熱沉等物質(zhì)與電池接觸帶走熱量,從而達到使電池降溫的目的。對于圓柱形電池,可設(shè)置成環(huán)形夾套式結(jié)構(gòu),其液體的流速不受限制,因此可使用導(dǎo)熱率高的液體材料。間接接觸式冷卻系統(tǒng)總體結(jié)構(gòu)如圖 7 所示,液管設(shè)置在電池周圍通過液體流動進 行熱量傳遞。
圖 7 間接接觸式冷卻系統(tǒng)原理圖
(1) 單進式冷板與圓柱形電池相比,方形電池形狀整齊,表面平整,在相鄰電池單體之間可以通過插入板式散熱組件,在冷板上焊接各種形狀的管道,使液體從管道內(nèi)流過,對電池進行冷卻。也可采用扁平管式結(jié)構(gòu),將壓平的管道置于相鄰電池之間。冷板式液冷系統(tǒng)中,冷卻液與電池間接接觸, 能夠有效避免短路風(fēng)險,提高電池組運行的安全性。冷板中的流道根據(jù)進出口形式可分為單進單出、單進多出、多進單出和多進多出式流道,冷卻液為水或其他冷卻液與水的混合物。如圖 8 所示,為單進單出式流道示意圖,其中冷卻液進出口可同側(cè)進出,也可異側(cè)進出。單進單出式流道結(jié)構(gòu)冷板的主要優(yōu)點為安裝方便,結(jié)構(gòu)簡單,缺點為因電池尺寸的限制而導(dǎo)致管內(nèi)冷卻液流動阻力較大,增加了電池消耗,且當流速較低時,進出口的溫差較大,增 加了電池溫度的不一致性。
圖 8 單進單出式通道冷板
(2) 多進式冷板多進式通道冷板液冷系統(tǒng)中,冷卻液進出口均 為兩個及以上,如圖 9 所示。當電池尺寸較大或者電池密度較高時,采用單進式通道,冷卻液流速越大,電池溫差越小,但同時壓力耗能也就越大。為減小液體流動時的阻力,研究者們采用了多進多出式通道冷板。多進多出式冷板的優(yōu)點為冷卻速度快, 效率高,缺點為進出口的設(shè)置越多,復(fù)雜程度就越 大,同時漏液的可能性就越大。
圖 9 雙進雙出式通道示意圖
在方形鋰離子電池冷卻系統(tǒng)中添加冷板式微型 通道,如圖 10 所示。冷板為鋁制材料,具有高 導(dǎo)熱系數(shù)等優(yōu)點,冷卻液采用液態(tài)水,電池使用 5C 倍率恒流放電進行模擬試驗。模擬結(jié)果表明,在冷卻板上增加的冷卻通道越多,放電結(jié)束后的電池最高溫度越低;同時在進口流量為 5×10?6kg·s?1時, 電池最高溫度下降至 58.40 ℃,局部減小為 9.02 ℃,當流量增加到 5×10?4kg·s?1時,鋰離子 電池內(nèi)部的溫差逐漸減小。
圖 10 冷板系統(tǒng)模型示意圖
由于僅采用液態(tài)水來作為冷卻液材料,當環(huán)境溫度極其惡劣時難以保證電池的正常使用,需要考慮其他的替代方法或者結(jié)合主動制冷以降低通道口的進液溫度。(3) 蛇形通道冷板在單進單出流道的冷板結(jié)構(gòu)簡單的基礎(chǔ)上,眾多學(xué)者研究出了單進單出式的蛇形流道冷板,如圖 11 所示。流道在冷板上呈現(xiàn)出蛇形曲折回旋,能夠避免冷卻液在進口端溫度低,出口端溫度高而導(dǎo)致電池組溫度不一致的問題。
圖 11 蛇形流道分布示意圖
對于蛇形通道結(jié)構(gòu),可以根據(jù)產(chǎn)熱特性、熱量 傳遞和熱量分布的實際情況來進行合理的設(shè)計。同時 JARRETT還對圖 12 的八種不同通道形狀進行了數(shù)值分析,發(fā)現(xiàn)冷卻液進出口的寬度、流道的形狀和分布等都會對電池的溫度造成很大的影響。即使在電池溫差較小時,電池不同部位的溫度分布也可能因為不同的通道結(jié)構(gòu)而呈現(xiàn)差異。所以在不同的蛇形流道結(jié)構(gòu)設(shè)計上,同樣要考慮電池的降溫以及其溫度分布的均勻性。
圖 12 不同結(jié)構(gòu)的蛇形冷板
(4) 超薄翅片微型通道冷板在傳統(tǒng)的直通冷板中,冷卻液沿著入口端流動 到出口端,對流傳熱系數(shù)逐漸降低,導(dǎo)致最高溫度持續(xù)升高,溫度梯度變大。針對此問題,JIN 等設(shè)計了一種超薄內(nèi)斜翅片微型通道冷板,當流量和負載分別為 0.1 L·min?1、220 W 和 0.9 L·min?1、1240 W 時,該系統(tǒng)能夠使電池兩邊冷板的溫度降低到 50 ℃以下。斜翅片冷板模型如圖 13 所示。該模型由兩塊板組成,每塊板包含相同數(shù)量的斜翅片,如圖 13a所示,冷板中的流道呈 U 形結(jié)構(gòu),如圖 13b 所示。
圖 13 斜翅片冷板結(jié)構(gòu)
冷板中的斜翅片可使電池內(nèi)部的熱量加速擴散 到流動中心,使兩端的對流換熱系數(shù)高于中心的對流換熱系數(shù),從而使斜翅片微型通道冷板具有更好的對流傳熱系數(shù),且冷卻液的流動比直通道下的更加均勻。3.2.3 夾套結(jié)構(gòu)液冷在電池外套上一層環(huán)形腔體,使電池與外殼間構(gòu)成流體通道,稱為夾套式液冷系統(tǒng)。夾套式 液冷系統(tǒng)能夠滿足多種情況下的電池散熱情況, 甚至可在低溫環(huán)境下對電池組進行加熱。電池組 夾套式液冷系統(tǒng)結(jié)構(gòu)由電池組、套管式換熱器和管道等組成。利用夾套式液冷系統(tǒng)通過有限體積法對電池進 行數(shù)值分析,使用的電池組模塊為 5×5 的圓柱 形鋰離子電池。分析對比電池組在 0.5C、1C、2C、 3C、4C 和 5C 不同放電倍率下的熱分布。在未添加 冷卻系統(tǒng)時,在 5C 放電倍率下仿真時間進行到 720 s 內(nèi)電池組達到的最高溫度為 61.449 ℃,電池組內(nèi)的最大溫差為 37.626 ℃,如圖 14 所示。加入夾套式冷卻系統(tǒng)后,5C 放電倍率下的最高平均溫度 為 27.862 ℃,電池組內(nèi)的最大溫差為 2.894 ℃。
\
圖 14 不同放電倍率下夾套式冷卻系統(tǒng)電池溫度曲線
3.2.4 其他液冷系統(tǒng)液冷散熱系統(tǒng)能夠有效降低電池的工作溫度和 局部溫差,但同時也存在系統(tǒng)結(jié)構(gòu)復(fù)雜,或發(fā)生漏液等不良情況。為此 TANG 等對液冷系統(tǒng)和熱泵空調(diào)系統(tǒng)(Heat pump air conditioning system,HPACS) 進行了耦合設(shè)計,建立了基于液冷與熱泵空調(diào)系統(tǒng) 的自動校準模型。通過模型試驗表明,設(shè)計的液冷 系統(tǒng)在環(huán)境溫度為 42 ℃時,入口處的溫度可降低 至 19.8 ℃,此時系統(tǒng)性能參數(shù)為 2.36。由于空氣的傳熱系數(shù)相對較低使得風(fēng)冷系統(tǒng)不 適用于大部分的高性能電動汽車,為克服空氣冷卻的缺點,可應(yīng)用二次回路液冷系統(tǒng)。二次回路液冷系統(tǒng)示意圖如圖 15 所示。該系統(tǒng)由兩個循環(huán)組成,虛線標示的制冷劑回路與實線標示的液體冷卻劑回路由冷水機連接,液體冷卻劑的流量和流速由冷負荷和周圍環(huán)境來決定并通過三通膨脹閥控制。當電池需要低冷卻性能或環(huán)境溫度低于液體冷卻劑溫度時,液體冷卻劑就會流向外部的散熱器;當電池需要高冷卻性能或環(huán)境溫度高于冷卻劑溫度時,冷卻劑就會流向冷凝器與制冷劑進行熱交換。優(yōu)點為在極端氣候條件下還可保持電池適當?shù)臏囟炔M足充放電要求,缺點為該系統(tǒng)結(jié)構(gòu)復(fù)雜,隨之產(chǎn)生更多重量、增加維護工作量和液體泄漏等風(fēng)險。
圖 15 二次回路液冷系統(tǒng)
液冷散熱系統(tǒng)效果良好,能夠有效降低電池的 工作溫度和局部溫差,同時也存在系統(tǒng)結(jié)構(gòu)復(fù)雜,質(zhì)量相對大,存在漏液以及常常需要維護等不利影響。但在對電池工作條件要求相對嚴格、熱管理優(yōu) 先的電動汽車熱管理系統(tǒng)中,液冷系統(tǒng)電池散熱方式具有比風(fēng)冷更明顯的優(yōu)勢,表 4 在上述文獻和調(diào) 研的基礎(chǔ)上對散熱性能進行了總結(jié)。表 4 液體冷卻系統(tǒng)總結(jié)
3.3 熱管冷卻系統(tǒng)
熱管(Heating pipe,HP)是利用管內(nèi)介質(zhì)相變進 行吸熱和放熱的高效換熱元件,廣泛應(yīng)用于工業(yè)等眾多領(lǐng)域。常用的熱管有三部分組成:封閉式金屬管、吸液芯和端蓋,將熱管內(nèi)抽成真空,充入適當?shù)睦鋮s液體,使管內(nèi)壁的吸液芯毛細多孔材料內(nèi)充滿冷卻液后加以密封。工作原理圖如圖 16 所示,熱管的吸熱端為蒸發(fā)端,散熱端為冷凝端。當熱管的加熱端受熱時,工作介質(zhì)受熱蒸發(fā)并在管內(nèi)流體的受力下流向冷凝端,然后蒸汽在冷凝端散熱重新變?yōu)橐后w,冷凝端的液體受重力或多孔材料的毛細力作用下流回蒸發(fā)端,以達到散熱的目的。如此循環(huán),將電池產(chǎn)生的熱量傳遞到外界空氣,從而實現(xiàn)小溫差大熱流的傳輸,使電池溫度降低。
圖 16 熱管工作原理
熱管由于具有良好的熱流密度可變性、導(dǎo)熱性、 密度可變性、熱流方向可逆性、優(yōu)良的恒溫?zé)嵝院铜h(huán)境適應(yīng)性等特點,已成為電子設(shè)備重要的散熱技術(shù)之一。此外,熱管需要在一定的條件下才能正常工作,從熱管的蒸發(fā)端到冷凝端的汽相與液相之間的靜壓差都應(yīng)與該處的毛細壓差保持線性關(guān)系。
式中,ΔPc為熱管內(nèi)部液體流動時的推動力;ΔPv為熱管內(nèi)蒸發(fā)端到冷凝端的蒸汽壓降;ΔP1為冷凝端回到蒸發(fā)端的壓降;ΔPg為由重力勢能引起的流體壓降,由熱管環(huán)境所決定,數(shù)值可正可負。熱管相比于其他冷卻系統(tǒng)具有更強的傳熱能 力,但并不意味著可以無限增大其熱負荷,熱管的 熱效率受眾多因素制約。影響熱管的傳熱的極限如 圖 17 所示,當熱管達到極限時,傳熱量將不再 繼續(xù)增加,傳熱極限取決于熱管的形狀、內(nèi)部吸芯液的結(jié)構(gòu)、工作介質(zhì)和周圍環(huán)境。
圖 17 影響熱管傳熱的各種極限
3.3.1 扁平熱管扁平熱管(Flat heat pipe,F(xiàn)HP)與普通熱管相比,可以更充分的接觸電池表面,能夠更快速、均勻的傳遞熱量。扁平熱管系統(tǒng)如圖 18 所示,使用可再現(xiàn)電池模塊產(chǎn)生的熱量進行 FHP 的冷卻系統(tǒng)的試驗,研究了 FHP 冷卻系統(tǒng)的熱性能,并與各種傾斜位置和多種冷卻條件下的傳統(tǒng)散熱器進行了比較。試驗結(jié)果表明,帶有熱管的普通散熱器通過自然對流熱阻降低了 30%,在風(fēng)速較小的情況下,熱阻降低了 20%,從而使電池溫度保持在 50 ℃以下。根據(jù)電動汽車中為電池組分配的空間,可將扁平熱管進行垂直或水平放置。
圖 18 扁平熱管散熱系統(tǒng)
3.3.2 重力型熱管重力型熱管又稱為熱虹吸管,結(jié)構(gòu)如圖 19 所示,從傳熱角度可由冷凝端、絕熱端和蒸發(fā)端三部 分組成。液體工質(zhì)在蒸發(fā)端受熱后汽化進入冷凝端, 在冷凝端釋放潛熱并在管壁上形成液膜,液態(tài)工質(zhì)在重力的作用下沿管壁回到蒸發(fā)端,如此循環(huán)。由于重力熱管具有方向性,蒸發(fā)端需設(shè)置在冷凝端的下方, 利用液體工質(zhì)自身重力回到蒸發(fā)端,因此重力型熱感結(jié)構(gòu)簡單、制造方便、成本便宜且穩(wěn)定性較好。
圖 19 重力型熱管
3.3.3 燒結(jié)熱管針對在微重力下熱管內(nèi)冷卻液難回到蒸發(fā)端的 問題,學(xué)者們采用了具有吸液芯結(jié)構(gòu)的燒結(jié)熱管。燒結(jié)熱管能夠在毛細力的作用下將冷卻液從冷凝端送到蒸發(fā)端,同時吸液芯結(jié)構(gòu)在循環(huán)中的速度更快, 有利于熱量的傳遞和擴散,提高了熱管的傳熱效率。近年來,燒結(jié)熱管所遇到的問題為其結(jié)構(gòu)和材料難以滿足高熱流密度環(huán)境下的散熱,尤其在傳熱過程中由于真空腔厚度的增加導(dǎo)致局部燒干的情況。因此合理的布置熱管結(jié)構(gòu),選取適當?shù)墓べ|(zhì)提高熱管的傳熱率是今后的研究熱點。在進行基于扁平式燒結(jié)熱管的方形電池散熱試驗,研究了燒結(jié)熱管對電池的散熱特性和電池組的溫度分布一致性。通過研究發(fā)現(xiàn),在電池溫升和局部溫差的控制中,必須同時考慮熱管的有效散熱能力和均熱能力;電池局部溫差隨熱管傾斜角的減小而增大,當熱管垂直安裝時,電池局部溫差受 路面坡度影響較小,傳熱熱阻可忽略不計;在周期性散熱的工況下,扁平式燒結(jié)熱管仍能保持良好的散熱能力和熱量均勻性。3.3.4 環(huán)路熱管環(huán)路熱管由20 世紀蘇聯(lián)科學(xué)家MAYDANIK 首次提出,結(jié)構(gòu)如圖 20 所示。回路系統(tǒng)通常由蒸發(fā)器、冷凝器和補償室組成。環(huán)路熱管具有反重力性能好、傳熱能力強和布置方便等特點。
圖 20 環(huán)路熱管結(jié)構(gòu)圖
常見的環(huán)路熱管有兩種結(jié)構(gòu)形式,分別為圓柱 型和平板型。圓柱型的特點為蒸發(fā)受熱均勻,且毛細芯能夠得到充分的濕潤。與圓柱型熱管相比,平板型接觸的電池面積更大,散熱更加均勻,傳熱能力更為優(yōu)秀。3.3.5 脈動熱管脈動熱管又稱振蕩熱管,結(jié)構(gòu)如圖 21 所示。脈動熱管可分為閉合型和開放型,開放型為單向流動,閉合型則兩端形成回路,且中間可加一個或多個單向閥進行衍生。
圖 21 脈動熱管基本結(jié)構(gòu)
與傳統(tǒng)的熱管相比,脈動熱管具有體積小、結(jié)構(gòu)簡單、傳熱性能良好、適應(yīng)性強、可對形狀進行任意彎曲等優(yōu)點。綜上文獻分析,總結(jié)基于熱管的電池?zé)峁芾硐到y(tǒng)的顯著優(yōu)點為在不消耗任何功率的情況下降低最大溫升,同時具有更高的導(dǎo)熱性、安靜無噪音、重量輕、 結(jié)構(gòu)靈活、輕維護和循環(huán)使用壽命長等優(yōu)點。缺點為熱管的容量小、接觸面積小,對大型電池組需要使用更多的熱管進行散熱,以及無法對電池組進行加熱。
3.4 相變材料冷卻系統(tǒng)
相變材料(Phase change materials,PCM)的物理 狀態(tài)隨溫度而變化,相變過程中溫度變化范圍小, 但吸收或釋放的潛熱大。相變材料具有體積變化小、潛熱大、穩(wěn)定性好等優(yōu)點。常見的 PCM 材料可分為有機材料、無機材料 和共晶材料,有機材料包括石蠟(PA)和石蠟化合物,如硬脂酸和長鏈烷烴等;無機材料包括水合鹽和金屬等材料;共晶材料是兩種或多種具有特定原子比的有機和無機化合物的混合,具有較高的潛熱和較高的熔點。3.4.1 有機相變材料常見的有機相變材料包括石蠟、脂肪酸、醇、 酯、二酯和其他有機化合物。有機材料中由于石蠟具有高潛熱、穩(wěn)定性好、 耐腐蝕和低成本的優(yōu)點,被廣泛應(yīng)用與電池?zé)峁芾硐到y(tǒng)中。由于易燃性和泄露風(fēng)險使得熱管理系統(tǒng)中不會使用純石蠟作為相變材料。針對這一問題,學(xué)者們提出一種有效方法,就是將膨脹石墨(EG)、金屬泡沫銅、納米流體和石墨氈等導(dǎo)熱材料引入到純有機相變材料中。將有機材料正二十烷 PCM 與銅納米顆粒、翅片和泡沫金屬混合,形成具有更高熱導(dǎo)性的復(fù)合 PCM,結(jié)構(gòu)如圖 22 所示。
圖 22 納米顆粒、翅片與金屬泡沫的電池?zé)峁芾砟P?/strong>
試驗結(jié)構(gòu)表明,納米顆粒的加入對電池散熱特 性影響很小,而翅片的添加使得電池溫度顯著下降, 高導(dǎo)熱性和三維結(jié)構(gòu)的金屬泡沫在降低電池溫度方面相對最有效。利用 PA、EG、聚磷酸銨(APP)、紅磷(RP)和環(huán) 氧樹脂(ER)組成的新型復(fù)合 PCM,可增強熱物理和阻燃性能。PCM 電池?zé)峁芾砟P腿鐖D 23 所示, 其中圓柱形電池放置在孔中且被 PCM 材料包裹。試驗結(jié)果表明,當 PCM 材料中 APP 和 RP 比例為 2.3:1 時,電池模塊能表現(xiàn)出更優(yōu)良的阻燃性。
圖 23 具有阻燃復(fù)合 PCM 材料的鋰電池模塊
3.4.2 無機相變材料與有機材料相比,無機材料因其易腐蝕、易脫 水和過冷特性導(dǎo)致在電池?zé)峁芾碇惺褂煤苌?。近年來,也有不少學(xué)者開始對其進行研究。典型的無機材料有水合鹽和金屬相變材料。為解決無機材料易脫水問題,LING 等設(shè)計出一種新型多尺度封裝 的無機 PCM,優(yōu)點為具有高穩(wěn)定性,結(jié)構(gòu)如圖 24 所示??紤]到安全性和低成本,使用了一種不易燃的三水乙酸鈉-尿素?zé)o機相變材料。EG 的添加能提高 PCM 的導(dǎo)熱性,有機硅膠的封裝可提高復(fù)合 PCM 的長期穩(wěn)定性。
圖 24 多尺度封裝的無機 PCM
3.4.3 共晶材料共晶材料是有機和無機的混合物,因此具有更高的潛熱和尖銳的熔點等特性。共晶材料的特點為不同化合物的層狀結(jié)構(gòu),在熔化和凝固過程中不會出現(xiàn)偏析現(xiàn)象,可阻止成分發(fā)生變化。通過物理結(jié)合六水硝酸鎂和硝酸鋰制備的共晶混合物中添加膨脹石墨,制備一種復(fù)合共晶材料。通過試驗測得共晶混合物的相變溫度為 72.46 ℃,潛熱為 170.32 kJ/kg,在容器選擇上使用鋁制或不銹鋼為最佳材料。所制備的共晶相變材料具有良好的吸熱能力,可為電池儲能領(lǐng)域散熱器的候選材料。3.4.4 與 PCM 耦合冷卻PCM 依賴于自身高潛熱的能力,然而當溫度超過自身的熔點后 PCM 冷卻性能就會顯著下降。因此將 PCM 與常用冷卻方法耦合起來構(gòu)成混合系統(tǒng),確保長期使用。表 5 總結(jié)了近些年 PCM 與其他冷卻系統(tǒng)耦合的方案。圖 25a 在鋁制框架中添加石蠟材料,空氣通過框架的間隙流動來冷卻和固化石蠟。圖 25b 將復(fù)合 PCM 的一側(cè)連接電池,另一 側(cè)連接到帶有風(fēng)冷系統(tǒng)的散熱器。在高溫環(huán)境和高放電倍率下,電池模塊溫度仍能保持在 60 ℃以下, 具有良好的熱性能。表 5 PCM 耦合冷卻系統(tǒng)綜合比較
圖 25 PCM 與風(fēng)冷系統(tǒng)結(jié)合的熱管理
與風(fēng)冷相比,液冷能夠表現(xiàn)出更優(yōu)秀的熱性能 和能源效率。圖 26a 為集成 PCM 與液冷系統(tǒng)結(jié)合的熱管理。當環(huán)境溫度為 40 ℃,放電倍率為 3C 下,液體冷卻系統(tǒng)管理下的電池組的最高溫度和電池間的梯度分別為 47.6 ℃和 4.5 ℃。圖 26b 在 PCM 系統(tǒng)中結(jié)合了可控液冷策略,可根據(jù) PCM 的溫度和環(huán)境溫度來調(diào)節(jié)冷卻液的流速和入口溫度,避免 了電池組在不同環(huán)境溫度下出現(xiàn)的過熱問題。PCM 與熱管耦合以降低電池組的溫度,在電池 組的熱管理系統(tǒng)中通過填充PCM可減低約33.6%的溫差,將熱管嵌入到 PCM 中可進一步下降 28.9%。圖 27 為 PCM 與脈動熱管耦合的熱管理系統(tǒng),脈動熱管夾在電池之間,將 PCM 填充至電池和熱管的縫隙中,由于 PCM 耦合熱管系統(tǒng)既有 PCM 的固液相變蓄熱,又有脈動熱管工質(zhì)的液汽傳熱,因此在各種工況下,PCM 耦合熱管的系統(tǒng)具有更好的散熱性能。
圖 26 PCM 與液體結(jié)合的熱管理系統(tǒng)
圖 27 PCM 耦合脈動熱管的熱管理系統(tǒng)
表 5 總結(jié)了近些年其他冷卻系統(tǒng)與 PCM 耦合的方案。
4 總結(jié)與展望
INDUSTRIALINTERNET
儲能電池作為電動汽車的核心,散熱問題是電 池?zé)峁芾硐到y(tǒng)的關(guān)鍵技術(shù)之一?;陔姵厣岬难芯楷F(xiàn)狀和研究趨勢,未來的熱管理系統(tǒng)可從以下方面展開。
(1) 風(fēng)冷方式的散熱結(jié)構(gòu)簡單,設(shè)計輕巧便捷, 但冷卻效率較低,很多情況不適于電動汽車的電池散熱。氣流通道和電池排布的優(yōu)化是未來的研究方向。
(2) 相比于風(fēng)冷,液冷具有更高的散熱效率, 能使電池組溫度保持在正常溫度范圍內(nèi),且使單體電池呈現(xiàn)出更好的溫度均勻性。由于需要額外的冷卻劑循環(huán)器件,增加了電路的復(fù)雜性、整車的重量與能耗,且有漏液的風(fēng)險。通道形狀和數(shù)量優(yōu)化是重點研究方向。納米流體作為冷卻劑的性能還需進 一步研究。
(3) 熱管作為一種導(dǎo)熱工具,具有更高的導(dǎo)熱率,但由于蒸發(fā)器和冷凝器部分的接觸面積小和體積較大等原因,在實際應(yīng)用中難以集成。額外能源消耗的削減和系統(tǒng)結(jié)構(gòu)的簡化是未來的發(fā)展趨勢。
(4) 大多數(shù)的 PCM 導(dǎo)熱系數(shù)較低,直接影響到 電池的散熱效率。因此尋找高導(dǎo)熱率的 PCM 一直是研究重點。如果在連續(xù)的高倍率充放電循環(huán)中僅使用 PCM 來控制電池溫度,可能無法達到理想的效果。因此,需要額外的冷卻系統(tǒng)來進行輔助,以協(xié)助散熱。PCM 與其他冷卻系統(tǒng)的結(jié)合是電池?zé)峁芾硐到y(tǒng)的發(fā)展趨勢之一。
目前 PCM 材料正慢慢向直冷靠近,相變材料 使用制冷劑 R134a。通過制冷劑的相變過程將熱量帶走。典型的例子有 BWM i3,散熱效果比液冷高出 3-4 倍,且避免了乙二醇液體在電池內(nèi)部流動造成的氧化腐蝕。當然直冷方式只能進行散熱,需要安裝加熱器來進行加熱。
未來,對高功率、高能量密度和高充電效率電 池的需求將持續(xù)增長,隨之而來的是對更高效、更穩(wěn)定、更經(jīng)濟、更緊湊的電池?zé)峁芾硐到y(tǒng)的需求。從低能耗和結(jié)構(gòu)角度來看,PCM 的散熱系統(tǒng)更具有潛力,需要進一步研究來提高商業(yè)應(yīng)用性。首先, 尋找高導(dǎo)熱率的 PCM 來代替;其次,設(shè)計以 PCM 為主體,其他散熱系統(tǒng)為輔助的協(xié)同機制,以保證電池?zé)峁芾硐到y(tǒng)的耐久性。
來源:電氣工程學(xué)報
作者:于仲安 陳可怡 張軍令 胡澤洲
江西理工大學(xué)電氣工程與自動化學(xué)院
-
電池
+關(guān)注
關(guān)注
84文章
10868瀏覽量
133196
發(fā)布評論請先 登錄
相關(guān)推薦
動力電池測試中的直流負載挑戰(zhàn)與應(yīng)對策略
石墨烯鉛蓄電池研究進展、優(yōu)勢、挑戰(zhàn)及未來方向
AI大模型的最新研究進展
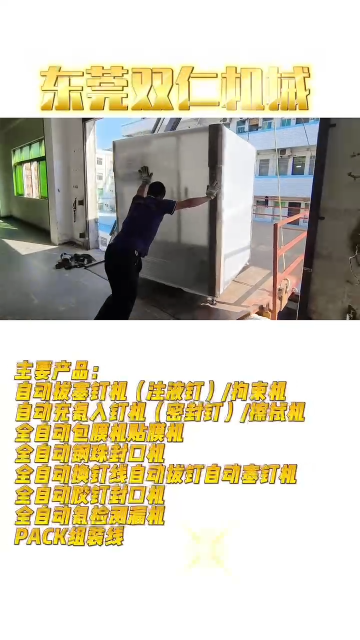
動力電池阻抗分析
新能源汽車電池三大散熱方案
新能源汽車動力電池散熱,導(dǎo)熱結(jié)構(gòu)膠粉體是關(guān)鍵!
【干貨】新能源汽車動力電池詳解
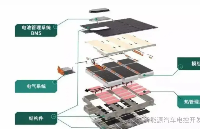
溫度是如何對動力電池的性能造成影響?
導(dǎo)熱紙(膜)的研究進展 | 晟鵬技術(shù)突破導(dǎo)熱芳綸紙
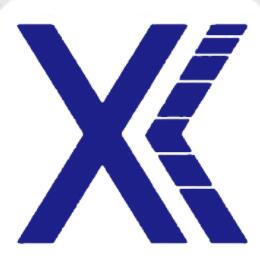
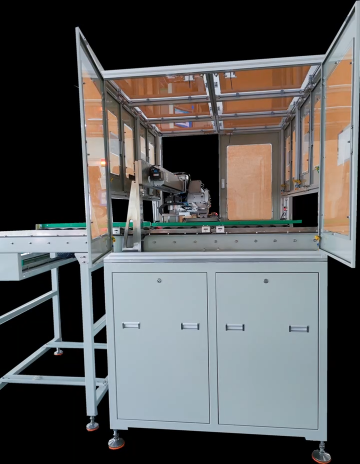
評論