一、超聲波焊接原理:超聲波線束焊接是目前汽車線束焊接的一種常用工藝,原理是通過高頻的振動(dòng)是焊接材料表面重新組合。超聲波焊接能耗低,無污染,焊接牢固且內(nèi)阻低,不改變焊接件的化學(xué)性質(zhì)。焊接導(dǎo)電性能優(yōu)良。
二、與傳統(tǒng)的壓接點(diǎn)焊相比,超聲波線束焊的優(yōu)點(diǎn)如下:
1、焊接時(shí)間短,效率大大提高,快速而節(jié)能;
2、焊接材料不熔融、不脆弱導(dǎo)體特性;
3、焊接后導(dǎo)電性能優(yōu)越,強(qiáng)度高,電阻系極低或近乎零;
4、不需要任何助焊劑、氣體、焊料;
5、焊接無火花、煙塵,環(huán)保安全;
6、焊接過程穩(wěn)定,在線檢測(cè)控制。
3.
三、超聲波線束焊接在汽車線束生產(chǎn)過程中的應(yīng)用
汽車線束是汽車電路的網(wǎng)絡(luò)主體,汽車正常工作的神經(jīng)元。沒有線束也就不存在汽車電路。傳統(tǒng)的汽車線束是指由銅材沖制而成的接觸件端子(連接器)與電線電纜壓接后,外面再塑壓絕緣體或外加金屬殼體等,以線束捆扎形成連接電路的組件。
隨著汽車電子產(chǎn)品和各種通訊設(shè)備進(jìn)入汽車,對(duì)汽車線束傳輸?shù)碾?a target="_blank">信號(hào)的要求也日益苛刻。為應(yīng)對(duì)這些高精度電壓和信號(hào)傳輸?shù)囊?,傳統(tǒng)的線束制造工藝上采用了一些特殊材料,比如雙絞線、屏蔽線、鍍金端子等。然而,在多數(shù)的電子控制設(shè)備和一些特殊信號(hào)上仍然顯得無濟(jì)于事,例如CAN控制器信號(hào)傳輸線路、安全氣囊信號(hào)傳輸線路以及一些音頻信號(hào)傳輸線路?,F(xiàn)有的端子導(dǎo)線對(duì)壓接工藝盡管采用了以上特殊材料,但在上述信號(hào)傳輸線路中,信號(hào)偶爾還是出現(xiàn)失真或較大衰減。
1 端子壓接工藝的研究
采用傳統(tǒng)壓接工藝壓接的汽車線纜,經(jīng)解剖放大發(fā)現(xiàn)在銅絲與銅絲之間、銅絲與端子壁之間形成空洞[1]。傳統(tǒng)汽車線束生產(chǎn)工藝采用銅材沖制而成的接觸件端子(連接器)與導(dǎo)線壓接,僅對(duì)電線銅絲進(jìn)行簡(jiǎn)單擠壓,使銅絲產(chǎn)生物理變形,這樣就有可能出現(xiàn)銅絲變形不足,在端子與導(dǎo)線進(jìn)行壓接后,必然形成上述空洞,這些空洞的存在,是不可避免的。而這些空洞的存在,必然導(dǎo)致壓接部位電阻系數(shù)增加,導(dǎo)電性下降,從而影響電流和信號(hào)的傳輸質(zhì)量,進(jìn)而影響其他電器及電子設(shè)備的正常工作。同時(shí),線束制作過程中因壓接引起的質(zhì)量缺陷[2],必將導(dǎo)致使用耐久性降低,并且易發(fā)熱產(chǎn)生高溫,形成線束燒損質(zhì)量隱患點(diǎn)。
2 超聲波壓接和端子壓接工藝對(duì)比分析
超聲波壓接是通過電晶體功能設(shè)備將工頻50/60 Hz的電頻轉(zhuǎn)變成20 kHz或40 kHz的高頻電能,供應(yīng)給轉(zhuǎn)換器,轉(zhuǎn)換器將電能轉(zhuǎn)換成高頻機(jī)械振動(dòng)能,調(diào)壓裝置將高頻機(jī)械能傳至超聲波焊接機(jī)的焊頭。振動(dòng)通過焊頭傳遞到需要焊接的兩個(gè)金屬表面,兩個(gè)金屬表面相互摩擦形成熱能使金屬熔化,在短暫的壓力下可以使熔化物在粘合面固化時(shí)產(chǎn)生強(qiáng)分子鍵, 終形成金屬分子層之間的熔合,整個(gè)周期通常是不到一秒種便完成,但是其焊接強(qiáng)度卻接近于一塊連著的材料。而傳統(tǒng)的端子壓接是通過金屬端子的U型部位對(duì)電線銅絲進(jìn)行簡(jiǎn)單物理擠壓,利用相鄰銅絲之間的表面摩擦力來保證電線與端子之間的連接。
事實(shí)上,無論是經(jīng)超聲波壓接的導(dǎo)線還是端子和導(dǎo)線,在壓接處呈矩形狀,無松散的芯線和斷頭或裂開的芯線;而且,導(dǎo)線沒有彎曲,而是在自熔合處呈直線引出。超聲波焊接是通過相鄰金屬表面熔化,形成金屬分子層之間的熔合,相當(dāng)于將相鄰金屬熔為一個(gè)整體,相比端子壓接后相鄰銅絲仍為獨(dú)立金屬個(gè)體而言,焊接部位的密實(shí)度更好,不會(huì)出現(xiàn)空洞。導(dǎo)電性好,電阻系數(shù)極低或近乎于零,有效提高了使用耐久性,不易發(fā)熱,無質(zhì)量隱患。如圖1所示,為超聲波壓接截面[1]。
3 超聲波壓接和端子壓接的試驗(yàn)數(shù)據(jù)分析
在進(jìn)行壓接處外觀對(duì)比和截面分析基礎(chǔ)上,筆者對(duì)兩種壓接工藝的導(dǎo)線進(jìn)行了拉脫力和導(dǎo)電性能測(cè)試。測(cè)試分別選取了0.75mm2、4.0 mm2、16.0 mm2導(dǎo)線進(jìn)行試驗(yàn)。試驗(yàn)方法和標(biāo)準(zhǔn)依據(jù)《QC/T29106-2004汽車用低壓電線束技術(shù)條件》的要求進(jìn)行,試驗(yàn)結(jié)果見表1[2]和表2[2]。
從表1可以看出,超聲波壓接和端子壓接在拉脫力性能上,均可以滿足使用要求,但由于壓接工藝本身差異,端子壓接截面往往出現(xiàn)空洞,芯線外漏、絕緣層破損等質(zhì)量缺陷。
從表2可以看出,超聲波壓接比端子壓接的電壓降在同樣條件下要低得多,因而對(duì)導(dǎo)電性能和信號(hào)傳輸性能比端子壓接要優(yōu)越得多。至少可以有以下3個(gè)方面的優(yōu)點(diǎn)。
第一,解決端子壓接形成的空洞,提高導(dǎo)電性能和整個(gè)電氣系統(tǒng)的穩(wěn)定性能[3]。
第二,減低因接觸電阻引起的熱量堆積[4],防止了線束局部溫度升高和線束燒毀的質(zhì)量隱患。
第三,防止了線束中導(dǎo)線受外界水分、灰塵、油氣等不良因素影響而造成銅絲銹蝕、氧化,從而引起導(dǎo)電性能下降和信號(hào)傳輸失真。
基于上述研究,筆者認(rèn)為對(duì)信號(hào)要求很高或電流較大的線路,在其端子與導(dǎo)線、導(dǎo)線與導(dǎo)線間的壓接,采用超聲波壓接,對(duì)提高信號(hào)傳輸質(zhì)量或電流輸送能力是非常有效的,而且也可以提高汽車電氣系統(tǒng)的穩(wěn)定性。
審核編輯 :李倩
-
超聲波
+關(guān)注
關(guān)注
63文章
3028瀏覽量
138506 -
焊接
+關(guān)注
關(guān)注
38文章
3202瀏覽量
59946 -
汽車線束
+關(guān)注
關(guān)注
4文章
166瀏覽量
15552
原文標(biāo)題:超聲波焊接在汽車線束生產(chǎn)中的應(yīng)用
文章出處:【微信號(hào):線束專家,微信公眾號(hào):線束專家】歡迎添加關(guān)注!文章轉(zhuǎn)載請(qǐng)注明出處。
發(fā)布評(píng)論請(qǐng)先 登錄
相關(guān)推薦
超聲波焊接原理和應(yīng)用
超聲波塑料焊接的優(yōu)點(diǎn)
超聲波焊接存在的缺點(diǎn)
超聲波焊接的原理及方法
影響超聲波焊接的因素
關(guān)于超聲波焊接中的導(dǎo)熔線設(shè)計(jì)
超聲波焊接在數(shù)字電子中的應(yīng)用
汽車線束的傳統(tǒng)超聲波焊接應(yīng)用
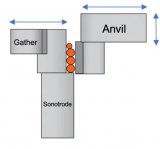
線束焊接機(jī)超聲波焊接發(fā)生器驅(qū)動(dòng)電源
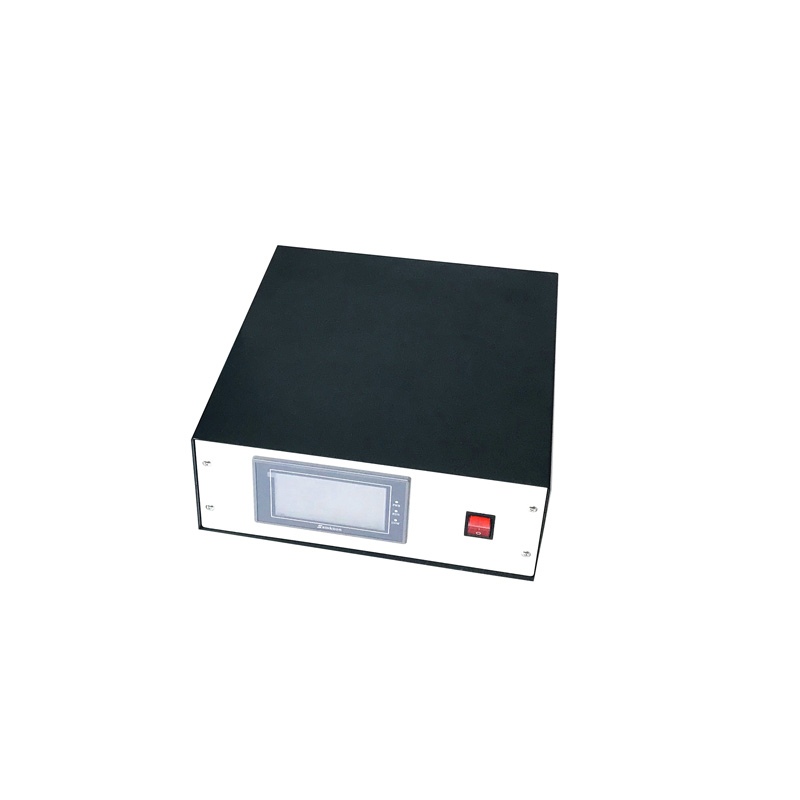
線束端子超聲波焊接發(fā)生器驅(qū)動(dòng)電源

評(píng)論