功耗和散熱是嵌入式電機控制系統(tǒng)開發(fā)人員面臨的持續(xù)挑戰(zhàn),因為隨著執(zhí)行器在汽車中的部署越來越多、減少發(fā)動機二氧化碳排放的驅動力以及車輛重量的增加,集成度和性能密度不斷提高。
本文以步進電機執(zhí)行器IC為例,對電機控制軟件和硬件環(huán)境提出了許多改進,旨在應對這些挑戰(zhàn)。
在車輛中,電機和執(zhí)行器的應用范圍很廣,從前格柵百葉窗和自適應大燈到車門后視鏡調節(jié)器。電機控制IC顧名思義,控制電動機的性能。這些器件正在不斷發(fā)展,以集成所有必要的功能,例如穩(wěn)壓器、振蕩器、看門狗、閃存、EEPROM、ADC、相電流控制和電機驅動器。這種高集成度可在單個芯片內實現(xiàn)緊湊而智能的執(zhí)行器設計。然而,缺點是集成度和性能密度的所有這些增加都會產生熱量。在空間非常寶貴的嵌入式電機控制系統(tǒng)中,工程師在功耗和熱管理方面正在達到極限。但這一挑戰(zhàn)并非不可戰(zhàn)勝;具體措施可以幫助解決電源散熱問題。
建立熱預算
為了確定熱預算,我們研究了基于TDK-Micronas HVC 4xyzF SDB-I v4.1評估板的步進電機執(zhí)行器,該評估板使用高度集成的電機控制IC(圖1)。該板在結構和尺寸方面與現(xiàn)實生活中的應用相似。
圖1:步進電機執(zhí)行器框圖
操作執(zhí)行器的基本要求是:
最大可能環(huán)境溫度 (TA) 由 IC 中的預期功耗 (PV_IC)、結和環(huán)境之間的熱阻 (RthJA) 以及允許的最高結溫 (TJ) 計算得出。在這里,應考慮IC在電路板上的環(huán)境溫度,即沒有任何外殼,盡管可能存在一個。作為最壞的情況,將應用最大值:
最大 T A =最大 TJ-PV_IC最大值xRth JA最大值
IC中轉換的總功耗由電機驅動器(PMotorDriver)的功耗以及IC的CPU和外圍模塊(PDDP)的功耗組成。
PV_IC最大值=P電機驅動器最大值+P 最大 DDP
電機驅動器損耗由相電流 (IPhase_RMS) 和集成半橋的輸出電阻計算得出。對于兩個電機相位中的每一個,都要考慮高端(RDS(ON)hs)和低邊晶體管(RDS(ON)ls)的電阻。一個PWM調制晶體管的開關損耗是近似值。
psw=1/2 x U x Ix(tr+t f)xfPWM
20 kHz PWM頻率下的開關損耗、開關速度的標準設置和三個PWM調制晶體管由13%的附加功率損耗加法器表示。為簡單起見,我們沒有單獨考慮隨心所欲的損失。作為最壞情況的考慮,電機連續(xù)運行,即有效相電流連續(xù)流動。因此,電機驅動器損耗的計算公式為:
P電機驅動器最大值= 2 x(2 x(IPhase_rmsRDSONhs max.+RDSONls max.))x1.13
CPU和外設的損耗由IC的電流消耗(IDDP)和給定的工作電壓(VBAT)決定。為簡化起見,忽略可能存在的任何極性保護處的壓降,這表示額外的安全裕度。
借助以下數(shù)據(jù)表最大參數(shù),計算最大功耗:
P最大 DDP=IDDP最大值x 最大 V 蝙蝠
P最大 DDP=0.035Ax16V=0.56W
這使我們能夠計算最大電機損耗:
P電機驅動器最大值= 2 x(2 x(IPhase_rmsRDSONhs max.+RDSONls max.))x1.13
P電機驅動器最大值= 2 x(0.25 2 A 2 x(2.8 Ω + 2.8 Ω))x 1.13 =0.791瓦
反過來,我們可以計算IC中轉換的總功耗:
PV_IC最大值=P電機驅動器最大值+P 最大 DDP
PV_IC最大值=0.791 W+0.56W=1.351W
執(zhí)行器的簡化熱模型(圖2)表明,這僅限于初級熱阻,這應該足以考慮穩(wěn)態(tài)。
圖 2:TDK HVC 4xyzF SDB-I v4.1 評估板的簡化熱模型
起點是類似于圓形評估板的電路板,由 FR4 材料制成;它厚1.6毫米,直徑40毫米。它有兩個信號層,一個 35 μm 銅層、一個 3 x 3 熱通孔陣列和一個位于 ePad 下方底部的銅表面,其面積約為 0.75 cm2。
該電路板的最大RthJA約為32 K/W。因此, 我們可以計算電路板的最大可能環(huán)境溫度。
最大 T A =最大 TJ-PV_IC最大值xRth JA最大值
最大 T A =150°C-(1.351瓦× 32K/瓦) =106.8°C
通常, 電路板和電機緊密地放置在外殼中。因此,要計算外殼內的溫度,還必須考慮電機的功耗。我們使用的塑料外殼,測量的熱阻(RthAH)為11 K/W。
電機損耗(PMotor)僅通過銅損來描述,銅損構成了大部分損耗,以保持簡單。假設電機相位的電阻 RPhase 為 12 Ω。因此,我們可以計算電機的功耗。
PV_電機= 2x(IPhase_rms 2 xRPh酶)
PV_電機= 2 x(0.2502一個阿拉伯數(shù)字x12Ω)= 1.5 W
有了這些信息,我們就可以計算外殼中的總功耗(Ptot)。
Ptot=PV_ICmax.+PV_電機=1.351 W+1.5 W=2.851 W
因此,執(zhí)行器外殼上的溫度梯度(ΔT)由下式決定:
?TAH=PtotWxRTHAHK/W
?TAH= 2.851Wx11K/W=31,36千米
如果將此溫度梯度添加到執(zhí)行器的最大指定環(huán)境溫度(85°C)中,則內部外殼溫度為116.4°C。
之前計算的電路板的最高允許環(huán)境溫度(106.8°C)與現(xiàn)在已確定的外殼內部溫度(116.4°C)之間存在10 K的差距。因此,需要采取適當行動來彌合這一差距。
僅在需要時使用
降低功耗的最有效方法是完全不讓它發(fā)生。因此,所有外設模塊應僅在需要時處于活動狀態(tài)。到目前為止,評估板中最重要的功耗是ADC(8 mA)、BEMF比較器(1.3 mA)和增強型PWM(1.1 mA)。
當電機運行時,即使在停留期間,BEMFC和EPWM也必須處于活動狀態(tài),以產生保持力。相比之下,ADC并不總是必需的,由于它是最大的功耗,因此可以通過“按需”操作實現(xiàn)顯著的節(jié)省。
在我們的步進電機應用中,ADC測量反電動勢電壓,以識別過載和與之相關的步進損失。假設速度為每秒1000個完整步,則ADC每秒或每毫秒激活1000次。轉換時間為1 μs,每個事件使用8次順序轉換,并考慮預熱和同步時間,使ADC總活動時間為每整步20 μs。
因此,平均活動時間(TA)可以按如下方式計算。
T A=T開/T周期=20 μs/1000 μs= 0.02
由此,我們可以計算出ADC的平均電流消耗(IADC_av)。
IADCav.= 8 mA×0.02=0.16mA
因此,模塊的電流消耗可以降低7.84 mA,相當于功耗降低7.84 mA×16 V = 125.4 mW。
優(yōu)化時鐘速度
在嵌入式執(zhí)行器中,軟件通常是事件控制的,其中動作由中斷觸發(fā)。CPU 主要參與后臺任務和等待新事件。這些事件可以是內部事件(如定時器中斷)或外部事件(如過壓或欠壓中斷)。
在非時間關鍵型后臺任務期間動態(tài)減慢 CPU 時鐘速度可降低電流消耗。一旦出現(xiàn)中斷,CPU可以自動切換到最大時鐘速度,并且可以以最大速度處理中斷服務例程。在中斷服務例程結束時,軟件切換回較低的時鐘速度。
對于典型的步進電機軟件,CPU 平均花費 40% 的時間執(zhí)行中斷服務例程。這意味著 60% 的時間都花在處理后臺任務上;在此期間減慢時鐘速度將顯著降低電流消耗。
一個很好的折衷方案是為后臺任務選擇 5 MHz 的 CPU 時鐘速度。最大時鐘速度的四分之一(20 MHz)可節(jié)省38%的電流(圖4)。因此,總電流消耗(不含電機驅動器)降低了60%,×38%=22.8%。
圖 4:TDK HVC 4223F MCU 標準化為 20 MHz 的電流消耗。該行表示當前節(jié)省。
HVC 4223F MCU 在所有外圍模塊關閉的情況下(其中 fYS = fCPU = 20 MHz)的典型電流消耗為 15 mA。因此,可以節(jié)省15 mA×22.8% = 3.42 mA。這種節(jié)省相當于功耗降低3.42mA×16V = 54.72 mW。
降低開關損耗
電機驅動器中的開關損耗由電壓、電流和開關時間引起。由于外部要求決定了電壓和電流,因此只能改變開關時間。在這里,我們可以分三個階段設置開關速度。在最快的設置下,與最慢的設置相比,切換時間可以減少一半以上。計算出將開關損耗加法器從電機驅動器損耗的13%降低到5%。
P電機驅動器最大值= 2 x(2 x(IPhase_rmsRDSONhs max.+RDSONls max.))x1.05
P電機驅動器最大值= 2 × (0.2502A2×(2.8 Ω + 2.8 Ω))×1.05 =0.735W
由于最初的功耗計算為0.791 W,這相當于功耗降低了56 mW。但是,請注意,必須仔細考慮電磁兼容性,因為這種分期技術可能會影響個別情況。
印刷電路板優(yōu)化
QFN 封裝底部的 ePad垂直獲取主熱流。熱量必須從芯片下方傳導, 通過電路板到 PCB 的底層。因此,必須使底層的銅表面盡可能大,以保證水平分布和有效散熱。
由于標準過孔存在焊料流出的風險,我們建議用樹脂填充并用銅覆蓋它們。我們還建議通過數(shù)組使用 4×4 或 5×5。再多也只會導致熱阻略有降低(圖 6)。如果對機械穩(wěn)定性的要求允許, 還可以減小電路板的厚度, 因為垂直方向的熱阻與電路板厚度成正比。
圖 6:通過 2×2 標準化過孔的 Rth
通過最大化連接到ePad的接地層,可以進一步改善散熱。通過布局優(yōu)化,銅表面可以翻倍至約1.5 cm2,從而將熱阻降低2 K/W.與熱阻為32 K/W的原始兩層電路板相比,這些優(yōu)化將其降低到26 K/W。
如果成本不是問題,您可以使用四層電路板,通過將 ePad 連接到額外的內層接地層,將熱阻降低到 20 K/W。
將外層的銅層厚度加倍至 70 μm 也更便宜,但效果較差, 這使得該電路板上的銅層厚度減少了 1 到 2 K/W.但是,如果您決定采用此選項,請在早期階段這樣做,因為較厚的銅層會影響信號層的布局。這是因為當銅厚度加倍時,最小軌道寬度和距離必須幾乎翻倍。
最大凈空
通過優(yōu)化軟件,IC的功耗可降低238.1 mW。電路板上的優(yōu)化措施將熱阻 (RthJA) 降低了 6 K/W。有了這些新數(shù)字, 我們可以重新計算電路板允許的最高環(huán)境溫度。
最大 T A =150°C-(1.351 W-0.2381W) ×(32-6)K/W=121.0°C
通過簡單且具有成本效益的措施,與電路板最初允許的最高環(huán)境溫度 106.8°C 相比,可以實現(xiàn) 14.2 K 的改進。
功耗降低后沿外殼的溫度梯度的新計算結果為:
?TAH=2.851寬-0.2381寬 x 11K/W=28.74千米
與初始溫度梯度 31.36 K 相比,這相當于提高了 2.62 K。加上執(zhí)行器所需的最高環(huán)境溫度 (85°C),新的內部外殼溫度為 113.7°C。 這縮小了差距,具有 7.3 K 的舒適動態(tài)余量。
結論
對軟件和電路板進行經濟高效的優(yōu)化可以提高應用的熱預算,并為嵌入式電機控制系統(tǒng)的開發(fā)人員提供充足的余量。重要的是,這些改進可以在任何嵌入式電機控制系統(tǒng)上實現(xiàn)。
TDK-Micronas HVC 柔性伺服驅動器系列能夠以經濟高效的方式開發(fā)高性能和緊湊型嵌入式電機控制系統(tǒng)。它們由 32 位 CPU (ARM Cortex-M3) 提供支持,解決了功耗散熱挑戰(zhàn)。除了我們在計算中使用的兩相雙極步進電機外,集成了所有必要功能的微控制器同樣適用于最多三相的無刷直流 (BLDC) 電機和有刷直流 (BDC) 電機。
審核編輯:郭婷
-
嵌入式
+關注
關注
5082文章
19123瀏覽量
305146 -
控制系統(tǒng)
+關注
關注
41文章
6618瀏覽量
110605 -
電機
+關注
關注
142文章
9020瀏覽量
145481
發(fā)布評論請先 登錄
相關推薦
飛凌嵌入式獲批建設「河北省嵌入式計算機控制系統(tǒng)技術創(chuàng)新中心」
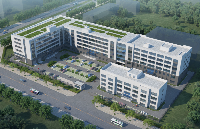
LDO在嵌入式系統(tǒng)中的應用 常見LDO故障及解決方法
mmc卡在嵌入式系統(tǒng)中的使用
嵌入式系統(tǒng)與物聯(lián)網的結合
【「嵌入式Hypervisor:架構、原理與應用」閱讀體驗】+第7-8章學習心得
嵌入式主板是什么意思?嵌入式主板全面解析
嵌入式系統(tǒng)的未來趨勢有哪些?
嵌入式系統(tǒng)怎么學?
了解嵌入式驅動器中的電源模塊
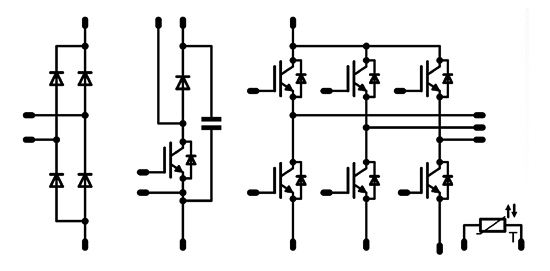
評論