一 前言
汽車技術的升級提升了性能,性能提升要求更安全穩(wěn)定高效制動;車速的加快造成交通事故的增多,對人身安全造成了巨大的威脅,汽車安全穩(wěn)定高效制動正變得越來越重要。普遍應用的液壓制動現(xiàn)是非常成熟的技術,隨著對制動性能要求的提高,防抱死制動系統(tǒng)、驅(qū)動防滑控制系統(tǒng)、電子穩(wěn)定性控制程序、主動避撞技術等功能逐漸融入到制動系統(tǒng)中,隨著新能源汽車的發(fā)展,制動系統(tǒng)的控制裝置逐漸會電子化,可以更加準確、更高效率地實現(xiàn)制動。隨著智能汽車的不斷發(fā)展和高級駕駛輔助系統(tǒng)的逐漸普及,對制動系統(tǒng)提出了新的要求,一方面既希望制動系統(tǒng)能夠?qū)崿F(xiàn)踏板力和車輪制動力之間的解耦,保持良好的踏板感覺來實現(xiàn)制動能量回收的需求,又希望實現(xiàn)高精度、更快的制動響應速度(300ms → 90ms)的汽車四輪制動力獨立調(diào)節(jié)的目的;另一方面希望制動系統(tǒng)具備主動制動功能,以適應緊急制動等智能輔助駕駛系統(tǒng)的需求。對傳統(tǒng)汽車制動行業(yè)而言,全新的挑戰(zhàn)和機會促使制動行業(yè)不斷變革。線控制動系統(tǒng)作為未來汽車制動系統(tǒng)的發(fā)展方向,不僅解決了傳統(tǒng)制動帶來的一系列問題,相較于傳統(tǒng)制動方式,線控制動技術有著顯著的優(yōu)勢,大大提高了車輛的安全性和舒適性,線控制動系統(tǒng)諸多優(yōu)勢使得線控制動技術將取代傳統(tǒng)的以液壓為主的制動系統(tǒng),當前正引領汽車線控技術的發(fā)展,更為汽車制動的快速發(fā)展帶來了新的契機。隨著自動駕駛時代的逼近推動了線控制動技術的進一步發(fā)展,線控制動(Brake-by-Wire)為智能網(wǎng)聯(lián)汽車實現(xiàn)自主停車提供了良好的硬件基礎,是實現(xiàn)高級自動駕駛的關鍵部件之一。線控制動產(chǎn)品正在不斷出現(xiàn)在智能電動汽車上,隨著線控制動的不斷發(fā)展與技術完善,已逐漸成為汽車新技術發(fā)展的主流。
二 概述
簡單介紹一下線控制動是怎么回事,分析線控制動技術類型、結(jié)構(gòu)和優(yōu)缺點及研究現(xiàn)狀,闡述其功能特點和工作原理。在剖析電子液壓制動系統(tǒng)組成架構(gòu)的基礎上歸納出電子液壓制動系統(tǒng)的液壓力控制架構(gòu),以控制變量和控制算法為突破口,從主缸液壓力控制和輪缸液壓力控制這兩個層面分別對國內(nèi)外的研究進展進行綜述,對能夠應用于電子液壓制動系統(tǒng)上的電磁閥特性進行分析,對其控制方式進行研究,提出對于電子液壓制動系統(tǒng)液壓力控制的發(fā)展展望;根據(jù)電動智能汽車對制動系統(tǒng)提出的新要求,設計了一款新型混合線控制動系統(tǒng)HBBW?;贖BBW開發(fā)了前后輪制動力精確跟隨控制算法,并進行了HiL試驗驗證。前輪EHB和后輪EMB系統(tǒng)均能達到設計的響應要求,較好跟隨目標壓力;通過整車制動力分配算法,能實現(xiàn)對前后車輪制動力的精確調(diào)節(jié),滿足整車制動力分配的需求;對一種線控制動系統(tǒng)踏板感覺模擬器進行計算分析和試驗驗證,確定了模擬器常閉電磁閥過流孔徑是影響踏板行程特性曲線偏離的主要因素. 重新設計了一種液控開閉閥,該閥由原踏板模擬器常閉電磁閥控制,所設計的液控開閉閥可提高踏板模擬器回路的通流能力. 利用 AMEsim 仿真模型完成參數(shù)選型并進行了裝車試驗,仿真及試驗結(jié)果均表明該方案可獲得良好的踏板感曲線精度,同時具備開發(fā)方便、降低電磁閥負荷的特點;汽車安全技術的研究與開發(fā)是當今世界汽車技術的重要發(fā)展方向,汽車制動系統(tǒng)對車輛的安全行駛起著至關重要的作用。采用線控技術構(gòu)建有關汽車安全性能的電子控制系統(tǒng),可極大地提高駕駛的安全性、可靠性和穩(wěn)定性。線控制動給汽車結(jié)構(gòu)和制動性能帶來根本性變革,相對傳統(tǒng)制動系統(tǒng)具有無法比擬的優(yōu)點,其研究與應用對汽車安全性、可操縱性、舒適性以及節(jié)能環(huán)保都將起到重要的作用。然后簡述了在當前新形勢下線控制動系統(tǒng)面臨的主要需求和未來發(fā)展趨勢。
三 定義
線控技術(X-by-Wire)”就是“電控技術”,從航空技術領域引入,其中,“X” 代表汽車中傳統(tǒng)上由機械或者液壓控制的各個功能部件,線控制動屬于線控,用制動(Brake)代替X就稱線控制動(Brake-by-Wire)。機械連接逐漸減少,制動踏板和制動器之間動力傳遞分離開來,取而代之的是電線連接;將原有的制動踏板用一個模擬發(fā)生器替代,通過制動踏板位置傳感器監(jiān)測駕駛員的制動意圖產(chǎn)生、傳遞制動信號,將制動踏板機械信號轉(zhuǎn)變?yōu)殡娍匦盘?,并將信號傳遞給控制系統(tǒng)和執(zhí)行機構(gòu),以電控模塊來實現(xiàn)制動力,并根據(jù)一定的算法模擬踩踏感覺反饋給駕駛員;電線傳遞能量,數(shù)據(jù)線傳遞信號,所以這種制動叫做線控制動。如果制動踏板僅僅只連接一個制動踏板位置傳感器,踏板與制動系統(tǒng)之間沒有任何剛性連接或液壓連接的,都可以視為線控制動系統(tǒng),如下圖。
大部分小型車都采用傳統(tǒng)的制動系統(tǒng)液壓制動,里面通過制動踏板提供能量,而線控制動系統(tǒng)有專門的能量供給方式,一般來說是通過輪邊的一些電機直接驅(qū)動進行這些工作。里面?zhèn)鹘y(tǒng)的制動系統(tǒng)液壓和氣壓管路沒有了,這是它們最大的區(qū)別,比較如下圖所示,
傳統(tǒng)制動系統(tǒng)與線控制動系統(tǒng)的區(qū)別
線控制動使用一個制動踏板傳感器,監(jiān)測踏板的位置;踏板的移動被傳遞給ECU,ECU與四個直流電動機相連,每個輪胎上有一個;根據(jù)制動踏板的踩踏情況,ECU命令電機進行制動。由于這些電機是相互獨立的,它們可以對每個輪胎施加不同的壓力,這有助于使用其它技術,如ABS,TCS,ESC等,ECU通過線控液壓制動系統(tǒng),使四個輪缸完成不同的任務,比如增壓,減壓或者保壓,從而完成車輛的制動,或者穩(wěn)定性控制;ECU還使用來自其他傳感器的數(shù)據(jù),如輪速傳感器和橫向加速度傳感器,以獲得對需要多少制動的完美概念。由于制動是汽車中非常重要的一部分,它的故障是相當具有破壞性的。因此,線控剎車系統(tǒng)也使用了一個備用剎車系統(tǒng),以確保汽車能夠一直剎車。這種冗余系統(tǒng)是L3以上自動駕駛功能必須要具備的。
EHB是Electronic Hydraulic Brake的簡稱,是從傳統(tǒng)的液壓制動系統(tǒng)發(fā)展來的,但與傳統(tǒng)制動方式有很大的不同。由于液壓管路發(fā)展了上百年,現(xiàn)階段已經(jīng)是非常成熟可靠的系統(tǒng),并且也能較好的控制成本,是在它的基礎上,用電子器件替代了一部分機械部件的功能,將傳統(tǒng)液壓制動技術的動力源替換為電子控制系統(tǒng),只用了一個伺服電機和一套控制器為EHB系統(tǒng)提供動力,取消了傳統(tǒng)制動系統(tǒng)中的真空供給部件和真空助力部件。制動踏板不再與制動輪缸有任何機械連接,采用的是電傳剎車踏板,即剎車踏板與制動系統(tǒng)并無剛性連接,也無液壓連接(如果有也只是作為備用系統(tǒng)),而是僅僅連接著一個制動踏板傳感器,用于給電腦(EHB ECU)輸入一個踏板位置信號。使用制動液作為動力傳遞媒介,控制單元與執(zhí)行機構(gòu)布置比較集中,并且使用制動液作為制動力傳遞的媒介,有液壓備份系統(tǒng),那么稱之為集中式的濕式的制動系統(tǒng),也稱電子液壓制動系統(tǒng)。
與傳統(tǒng)制動系統(tǒng)相比,最大的區(qū)別在于:首先用電子系統(tǒng)來提供動力源,它以電機為動力源,解決了傳統(tǒng)的真空助力器制動系統(tǒng)的真空依賴問題;其次它引入了電控單元和多種傳感器,用電子元件替代傳統(tǒng)制動系統(tǒng)中的部分機械元件,即用綜合制動模塊取代傳統(tǒng)制動系統(tǒng)中的助力器、壓力調(diào)節(jié)器和ABS模塊,使得制動系統(tǒng)實現(xiàn)電控化,可作為智能駕駛的關鍵執(zhí)行器。同時保留了成熟的液壓部分,可以在電子助力失效時提供備用制動,確保車輛安全。
EHB系統(tǒng)主要功能是提升老舊制動體系的性能,將電子系統(tǒng)和液壓系統(tǒng)相結(jié)合整合到一起,是一種介于傳統(tǒng)的制動系統(tǒng)與電子機械制動系統(tǒng)之間的制動系統(tǒng), 兼具這兩種系統(tǒng)的特點, 系統(tǒng)中既有效把握了傳統(tǒng)液壓控制系統(tǒng)的結(jié)構(gòu), 同時又應用了電子控制系統(tǒng)的主要內(nèi)容。新型的線控電子液壓制動系統(tǒng)應運而生,是一個先進的機電液一體電控化系統(tǒng),其控制單元及執(zhí)行機構(gòu)布置集中。傳統(tǒng)車用12V電源即可驅(qū)動EHB系統(tǒng),無需設計新的供能系統(tǒng)。
EHB系統(tǒng)雖實現(xiàn)了線控制動功能,但并不完全移除液壓系統(tǒng),備用系統(tǒng)中仍然包含復雜的制動液傳輸管路,使得EHB并不完全包含線控制動系統(tǒng)產(chǎn)品的優(yōu)點,EHB系統(tǒng)也因此被視為線控制動控制BBW技術的前期產(chǎn)物。
電子機械制動系統(tǒng)EMB是Electronic Mechanical Brake的簡稱,最早是應用在飛機上的,如美國的F-15戰(zhàn)斗機就采用了EMB制動器,后來才慢慢轉(zhuǎn)化運用到汽車上來。EMB與傳統(tǒng)的制動系統(tǒng)有著極大的差別,與常規(guī)的液壓制動系統(tǒng)截然不同,完全不同于傳統(tǒng)的真空助力液壓制動系統(tǒng),基于一種全新的設計理念,完全摒棄了傳統(tǒng)制動系統(tǒng)的制動液及液壓管路等部件,取消了使用一百多年的剎車液壓管路,完全拋棄了液壓裝置,使用電子機械系統(tǒng)替代,其能量源只需要電能,因此執(zhí)行和控制機構(gòu)需要完全的重新設計,EMB作為純機械系統(tǒng),執(zhí)行機構(gòu)通常直接安裝在各個輪邊,將電機集成在制動鉗上,踏板產(chǎn)生制動信號直接輸入到制動鉗,輸入與終端執(zhí)行之間的部件全部簡化。沒有制動液也沒有液壓管路,由電機驅(qū)動產(chǎn)生制動力,每個車輪上安裝一個可以獨立工作的電子機械制動器,如果四個輪胎需要制動的話,就需要四個電機,也稱為分布式、干式制動系統(tǒng)。采用電子控制,使用控制模塊控制伺服電機進行制動,通過伺服電機直接作用于輪缸,直接給剎車碟施加制動力。這有點像電子手剎,但是與電子手剎最大的不同是它需要能夠產(chǎn)生足夠大的制動力并且制動線性要高度可調(diào),響應要非常迅速。
汽車的線控制動系統(tǒng)涵蓋面廣,主要包括了控制裝置、傳動裝置等多項構(gòu)成,通過全面控制有關的制動系統(tǒng),并聯(lián)合先進的制動器,就能夠在不同的制動器中,單獨進行控制,完成獨立操作。而制動踏板和制動器之間沒有采用機械進行連接,而是用電線關聯(lián),通過電線將兩者間的能量、信號等進行傳送,不僅提升了傳輸效率,還能提高汽車的整體性能,有效保障了駕駛過程中的安全。
線控制動系統(tǒng)包含傳統(tǒng)制動技術,是基于動力學、運動學、電控等多學科融合技術,技術壁壘較高。掌控著自動駕駛的底盤安全性和穩(wěn)定控制,只有擁有足夠好的制動性能(包括響應速度快、平順性好等),才能為行駛安全提供良好保障。這一系統(tǒng)結(jié)合了汽車電子技術和網(wǎng)絡信息技術, 它的應用推動了汽車全自動化水平的提升, 同時在汽車的智能控制方面有重要的作用, 給其創(chuàng)造了良好的條件。
線控制動可以縮短制動距離,軟件定義踏板感,滿足智能駕駛需求,符合集成化、電子化趨勢。即使整車EEA變革,制動單元ECU、芯片對安全穩(wěn)定性能要求嚴格,將長期獨立存在。
(1)改人力為電信號作為輸入起源
在自動駕駛典型的感知-規(guī)劃-執(zhí)行設計范式中,線控制動屬于執(zhí)行層部件,為感知層開放了接口。上一代制動系統(tǒng)制動力的輸入源必須是駕駛員,而線控制動既可以由剎車踏板控制,也可以脫離人力,由ECU控制主動建壓。因此,線控制動作為線控底盤的一部分,是L3+級別自動駕駛的必備條件,部分L2-L2.5級別自動駕駛車型也裝配了線控制動。
(2)更快更精的剎車性能,軟件定義踏板感
電信號傳遞快于機械連接,為自動駕駛提供更高級別的安全守護。常規(guī)制動系統(tǒng)響應時間為300-500毫秒,布雷博的線控制動系統(tǒng)響應時間只有90毫秒,線控制動距離相應縮短。
四 組成
由于防抱死制動系統(tǒng)(ABS)、車身穩(wěn)定控制系統(tǒng)(ESP)等逐步產(chǎn)生,線控制動系統(tǒng)慢慢在傳統(tǒng)的制動系統(tǒng)上發(fā)展起來。
L2時代的線控制動可以分為燃油車、混動、純電三大類,燃油車基本都采用ESP(ESC)做線控制動;混動車基本都采用高壓蓄能器為核心的間接型EHB(電液壓制動);純電車基本都采用直接型EHB,以電機直接推動主缸活塞。
L3+級別自動駕駛為線控制動提供明確的市場需求,線控制動是自動駕駛的標配。線控制動屬于執(zhí)行層部件,既可以由剎車踏板控制,也可以脫離人力,由ECU控制主動建壓。功能相似的ESP車身穩(wěn)定系統(tǒng)只能作為緊急備用方案,要實現(xiàn)L3+級別自動駕駛必須開發(fā)一套新的電子助力裝置作為常用制動,并配合ESP、EPB、RBU等形式的電子安全冗余。
1.ESP
ESP(Electronic Stability Program)車身穩(wěn)定系統(tǒng)有主動剎車的訴求,因此線控制動系統(tǒng)的結(jié)構(gòu)在ESP中也有所體現(xiàn)。但即便經(jīng)過了幾十年發(fā)展,ESP仍不能作為常用剎車方案,只能作為緊急備用方案,無法兼容線控制動功能。博世ESP系統(tǒng)的最大減速度為0.4g,低于常規(guī)剎車0.6g-0.8g的要求。并且ESP反應速度較慢,所需剎車時間為ibooster的三倍,每次使用都會導致壽命急劇下滑,頻繁使用不超過一個月便會報廢,因此有必要重新開發(fā)一套電子助力裝置。
2.電子液壓制動系統(tǒng)(EHB) 典型EHB由制動踏板位移傳感器(電子踏板)、電子控制單元ECU、液壓執(zhí)行器機構(gòu)(液壓泵、備用閥和制動器)等部分組成。電子踏板是由制動踏板和踏板傳感器(踏板位移傳感器/角度傳感器 )組成。制動踏板位置傳感器用于檢測踏板行程/踏板轉(zhuǎn)角,然后將位移/轉(zhuǎn)角信號轉(zhuǎn)化成電信號傳給ECU,實現(xiàn)踏板行程/轉(zhuǎn)角和制動力按比例進行調(diào)控。如下圖所示。
電子液壓制動系統(tǒng)結(jié)構(gòu)示意圖
電子液壓制動系統(tǒng)(EHB)結(jié)構(gòu)圖
電子液壓制動系統(tǒng)的組成
如上圖所示,電子液壓制動系統(tǒng)共分成四大部分:制動踏板單元、液壓調(diào)節(jié)(驅(qū)動)單元、制動執(zhí)行單元、電子控制單元(控制系統(tǒng))。
(1)制動踏板單元包括制動踏板、制動液罐、制動主缸、踏板行程傳感器、制動踏板模擬器等,負責為駕駛員提供合適的制動踏板感覺,同時獲取駕駛員意圖。在普通制動情況下,制動踏板單元不再向車輪制動器提供制動能量,其主要用來利用踏板行程傳感器采集駕駛員制動意圖以及利用制動踏板感覺模擬器模擬駕駛員的制動感覺。
(2)液壓驅(qū)動單元包括「電動機 + 減速機構(gòu)」、「液壓泵 + 高壓蓄能器」等形式。液壓調(diào)節(jié)單元包括布置在發(fā)動機艙內(nèi)的液壓調(diào)節(jié)器、制動管路、車輪制動器以及安裝在蓄能器和每個車輪制動器處的壓力傳感器。液壓調(diào)節(jié)單元主要包括進液閥、出液閥、平衡閥、隔離閥、氣囊式蓄能器以及電機泵等。相比于電子穩(wěn)定性系統(tǒng)ESP的液壓調(diào)節(jié)單元,EHB在制動主缸與液壓調(diào)節(jié)器連接處增加有隔離閥,用于隔斷制動踏板單元與液壓調(diào)節(jié)單元之間的物理連接;同時使用高壓蓄能器儲存來自電機泵的高壓制動液并向車輪制動器提供制動能量,以實現(xiàn)在普通制動下的主動制動功能。電機泵只在蓄能器壓力降低到規(guī)定極限時,才驅(qū)動電動機使液壓泵工作。
由于電動汽車制動主缸最高建壓需求往往超過15MPa,因此在采用電動機作為液壓壓力動力源的電子液壓制動系統(tǒng)中,均需要加裝減速增扭機構(gòu),以增大電動機的最大輸出轉(zhuǎn)矩,減小電動機體積,節(jié)約成本。
1)「電動機+減速機構(gòu)」負責將電動機的力矩轉(zhuǎn)化成直線運動機構(gòu)上的推力從而推動主缸產(chǎn)生相應的液壓力;
2)「液壓泵+高壓蓄能器」通過高壓蓄能器的高壓能量來提供主缸液壓力或輪缸制動力以實現(xiàn)主動調(diào)節(jié)。
該系統(tǒng)通過制動踏板單元獲取制動駕駛意圖從而向整車控制器發(fā)送指令,以控制高壓蓄能器、電磁閥和泵產(chǎn)生相應的液壓力;
當高壓蓄能器內(nèi)壓力不足時,液壓泵將對高壓蓄能器增壓。
(3)制動執(zhí)行單元包括主缸,液壓管路,輪缸等。這些機構(gòu)跟傳統(tǒng)制動系統(tǒng)的結(jié)構(gòu)保持一致,將推動主缸的推力轉(zhuǎn)化成制動器的液壓力,最后通過摩擦力作用在制動盤上產(chǎn)生相應的制動力矩。
(4)控制系統(tǒng)包括電控單元(Electric Control Unit,ECU)、液壓力控制單元(Hydraulic Control Unit,HCU)、液壓力傳感器、踏板力傳感器以及踏板位移傳感器等;液壓力控制單元(HCU)是液壓力控制的核心單元。電子控制單元與液壓調(diào)節(jié)器集成在一起,主要通過CAN總線接收來自傳感器信號并向液壓調(diào)節(jié)器發(fā)出控制指令。
1)HCU 用以精確調(diào)節(jié)輪缸液壓力;HCU 的主要元件是電磁閥,輪缸液壓力控制的底層控制就是電磁閥控制。目前用于 HCU 的電磁閥主要有三類:開關閥、高速開關閥和線性閥。
①開關閥是 HCU 的核心執(zhí)行部件之一,利用快速的開啟和關閉動作來改變液體的流向和平均流量。開關閥的開關機理是通過閥口兩端壓力差產(chǎn)生的液壓力和液動力、被壓縮彈簧的回位力、電磁線圈產(chǎn)生的電磁力以及閥芯運動過程中所受的制動液粘性阻力、機械摩擦阻力的合力來驅(qū)動閥芯移動從而進行閥口的開關動作。
②高速開關閥與傳統(tǒng)開關閥的工作原理相同,都是在開、關兩種狀態(tài)之間切換來實現(xiàn)液流的通斷。不同之處在于高速開關閥響應速度較快。
③線性閥是解決高速開關閥低頻控制下存在缺點的一個有效途徑。線性閥的主要特征是節(jié)流面積可調(diào),需調(diào)控電磁力。其設計思路是控制閥口開度,壓力增益可控可調(diào)。同一種孔徑的產(chǎn)品覆蓋面更廣,通用性更強,制造成本更低;而且還能抑制噪聲,提高制動的舒適性。電磁閥控制本質(zhì)上是流量控制。
2)液壓力傳感器作為反饋單元將液壓力實時反饋到整車控制器里,用作控制算法的輸入量;
3)踏板力傳感器和踏板位移傳感器用來檢測駕駛員的踏板信號,從而獲得駕駛員意圖。
特種車用線控制動系統(tǒng)
是一種基于液壓傳遞的全解耦線控制動系統(tǒng)。主要由電機、減速増扭機構(gòu)(齒輪、絲桿、螺母)、制動主缸、前后殼體、踏板推桿、行程傳感器、液壓力傳感器、電機控制器等組成。項目成果所涉及到的新型踏板行程傳感器將踏板推桿的平動轉(zhuǎn)化為傳感器內(nèi)部器件的轉(zhuǎn)動,基于此,可以通過在推桿上設計不同曲率的溝槽,將傳感器設計為非線性、線性以及不同的物理精度。所涉及的全解耦電子助力器,制動踏板推桿和制動主缸活塞之間無機械鏈接,屬于智能制動執(zhí)行器,滿足特種自動駕駛車輛對制動系統(tǒng)主動制動的功能要求、取消了傳統(tǒng)制動系統(tǒng)對發(fā)動機真空度的依賴、具備配合電動車實現(xiàn)制動能量回收的功能。
全解耦線控制動系統(tǒng)執(zhí)行器與行程傳感器
解耦原理:踏板推桿與制動總泵推桿之間無連接,制動系統(tǒng)的動作依靠電信號或者行程傳感器信號進行控制實現(xiàn)。
工作原理:當駕駛員踩下制動踏板時,踏板推桿向前移動,推動行程傳感器內(nèi)部旋轉(zhuǎn)件轉(zhuǎn)動,傳感器記錄旋轉(zhuǎn)部件的轉(zhuǎn)角,根據(jù)推桿滑槽曲率計算出踏板推桿實際行程,識別駕駛員制動意圖。通過電信號傳遞給系統(tǒng)控制器,控制器控制執(zhí)行器電機動作,電機驅(qū)動絲桿和螺母,講轉(zhuǎn)動轉(zhuǎn)化為平動,推動制動缸活塞建立液壓制動力,作用在輪邊制動盤上,產(chǎn)生制動力。
3.電子機械制動系統(tǒng)(EMB) EMB系統(tǒng)主要由踏板模塊(傳感器)、控制模塊(ECU)、驅(qū)動執(zhí)行模塊(電子機械制動器)等組成,系統(tǒng)有4套獨立的制動系統(tǒng),分別位于四個輪轂的輪缸處,并且配有獨立的控制器,以便實現(xiàn)四輪制動力的獨立調(diào)節(jié)。EMB系統(tǒng)中,所有液壓裝置(包括主缸、液壓管路、助理裝置等)均被電子機械系統(tǒng)替代,液壓盤和鼓式制動器的調(diào)節(jié)器也被電機驅(qū)動裝置取代。其典型EMB系統(tǒng)如下圖示。
EMB的結(jié)構(gòu)圖
(1)電制動器:由電機驅(qū)動產(chǎn)生制動力
EMB系統(tǒng)的關鍵部件之一是輪邊執(zhí)行機構(gòu)系統(tǒng)(電子機械制動器),集成了轉(zhuǎn)角傳感器、 扭矩傳感器, 結(jié)構(gòu)上又有將電機轉(zhuǎn)動轉(zhuǎn)化為直線運動的機械機構(gòu),它通過ECU改變輸出電流的大小和方向?qū)崿F(xiàn)執(zhí)行電機的力矩和運動方向的改變,通過減速增矩,將電機軸的旋轉(zhuǎn)變換為制動鉗塊的開合;通過相應的機構(gòu)或控制算法補償由于摩擦片的磨損造成的制動間隙變化,同時,電機和驅(qū)動機構(gòu)等都裝在制動器上,其結(jié)構(gòu)設計必須十分緊湊,以滿足空間要求。輪邊工作環(huán)境惡劣,是EMB開發(fā)難度所在。當前的EMB實現(xiàn)并沒有標準形式。
(2)ECU
1)通過制動器踏板傳感器信號以及車速等車輛狀態(tài)信號,驅(qū)動和控制執(zhí)行機構(gòu)的電機來產(chǎn)生所需的制動力,控制制動器制動。
2)接收駐車制動信號,控制駐車制動;
3)接收車輪傳感器信號,識別車輪是否抱死、打滑等,控制車輪制動力,實現(xiàn)防抱死和驅(qū)動防滑功能;
(3)輪速傳感器:準確、可靠、及時的獲取車輪速度。
(4)電源:為整個制動系統(tǒng)提供能源,可與其它系統(tǒng)共有。
4.EHCB系統(tǒng)
是目前已知的最接近量產(chǎn)的EHB和EMB混合產(chǎn)品,由于EMB制動力不足,因此該制動系統(tǒng)前輪采用EHB,后輪采用EMB,將兩種制動系統(tǒng)結(jié)合應用可有效發(fā)揮兩種制動系統(tǒng)的優(yōu)勢。前輪采用EHB系統(tǒng)可實現(xiàn)前輪單輪制動力調(diào)節(jié),同時靠裝于前軸的EHB實現(xiàn)制動失效備份以滿足現(xiàn)行法規(guī)要求;后輪采用EMB可縮減制動管路的長度,消除壓力控制過程中由于管路過長帶來的不確定性,同時能夠方便地實現(xiàn)電子駐車制動(electrical park brake,EPB)。
混合線控制動系統(tǒng)制動力精確調(diào)節(jié)控制策略
鑒于電子液壓制動(electronic hydraulic brake,EHB)系統(tǒng)液壓管路復雜且難以集成駐車制動,而電子機械制動(electronic mechanical brake,EMB)很難滿足失效備份的需求,提出了一種前軸采用EHB,后軸采用EMB的混合線控制動系統(tǒng)(hybrid brake by wire system,HBBW),研究了EHB的雙閉環(huán)壓力跟隨PI控制算法和EMB的三閉環(huán)制動力跟隨PI控制算法,使其制動力能快速準確地跟隨目標值。在此基礎上,提出了混合制動系統(tǒng)的制動力精確調(diào)節(jié)PI控制策略和控制算法,提出將EHB和EMB的制動系統(tǒng)組合形成一種比較理想的混合線控制動系統(tǒng)(hybrid brake by wire system,HBBW),最后基于dSPACE Autobox和CarSim搭建了HBBW系統(tǒng)的硬件在環(huán)(hardware-in-the-loop,HiL)試驗平臺,研究了EHB和EMB的壓力跟隨PI控制算法,使其制動力能快速準確地跟隨目標制動力,進行了HiL測試與算法驗證。結(jié)果表明,混合線控制動系統(tǒng)可有效地協(xié)調(diào)工作,實現(xiàn)四輪制動力快速、精確調(diào)節(jié),從而提高車輛制動性能。 提出的HBBW系統(tǒng)總體布置方案如下圖所示,系統(tǒng)采用前輪EHB,后輪EMB的結(jié)構(gòu)布置。前輪EHB模塊由EHB控制器、車輪制動器、液壓控制單元(hydraulic control unit,HCU)、制動主缸、踏板感覺模擬器和儲液罐組成;后輪EMB模塊每個車輪上有一個,由單獨的EMB控制器EMB ECU和一個EMB執(zhí)行器組成。系統(tǒng)裝備有一個中央控制器HBBW ECU實現(xiàn)壓力控制。
混合線控制動系統(tǒng)總體布置方案 系統(tǒng)工作流程如下:(1)駕駛員踩下制動踏板,主缸中的制動液進入踏板感覺模擬器形成與傳統(tǒng)制動系統(tǒng)相同的踏板感覺;(2)HBBW ECU采集制動踏板位移傳感器和主缸壓力等信息識別駕駛員的制動意圖,根據(jù)前后輪理想制動力分配曲線給出前后輪制動力;(3)前輪制動由EHB實現(xiàn),EHB控制器集成于HBBW ECU中,它控制電動泵抽取儲液罐中的制動液,向高壓蓄能器注入制動液作為高壓壓力源,通過電磁閥控制制動液流入流出制動器實現(xiàn)壓力跟隨;(4)后輪制動由EMB實現(xiàn),HBBW ECU通過CAN向EMB ECU發(fā)出制動力控制指令,EMB ECU作為底層控制器驅(qū)動EMB執(zhí)行器實現(xiàn)后輪制動力控制;(5)在HBBW ECU中,還可集成 EBD/ABS/ESP等控制算法。 當系統(tǒng)失效時,啟動制動失效備份,如下圖所示。后輪EMB不再工作,前輪EHB恢復電磁閥初始狀態(tài),踏板感覺模擬器前端電磁閥和增減壓電磁閥關閉,兩隔離閥打開,電機不再工作。駕駛員通過制動踏板經(jīng)主缸直接作用于前輪輪缸形成制動力,實現(xiàn)制動。
EHB制動失效備份原理圖 該系統(tǒng)既能充分發(fā)揮兩種制動系統(tǒng)的優(yōu)勢,又能彌補各自的不足。為提高控制響應速度與精度時,在前軸裝EHB,實現(xiàn)制動失效備份以滿足現(xiàn)行法規(guī)要求;另外,由于后軸EMB所需的制動力矩相對較小,現(xiàn)有的12V車載電源系統(tǒng)滿足其功率需求。
-2 HBBW制動力調(diào)節(jié)控制算法
-2.1 HBBW前后輪制動力分配
HBBW在對前后輪進行制動力精確調(diào)節(jié)之前,需要識別駕駛員的制動行為,下圖為HBBW前后輪制動力分配框圖。駕駛員踩下制動踏板,位移傳感器和主缸壓力信號分別采集信號輸送給HBBW ECU,HBBW ECU通過對傳感器的信號采集分析識別出駕駛員的制動意圖,經(jīng)整車控制算法,根據(jù)汽車制動過程中的不同需求,如ABS,ESP和EBD等算法開啟和關閉給出前后輪的目標制動壓力。
HBBW前后輪制動力分配框圖 為能精確而快速地調(diào)節(jié)前后輪制動壓力,EHB和EMB應滿足: (1)EHB系統(tǒng)達到14MPa的輪缸壓力的增壓時間小于200ms,超調(diào)量小于1%,能較好地跟隨正弦調(diào)制壓力跟隨曲線,適應制動系統(tǒng)調(diào)壓功能; (2)EMB系統(tǒng)達到12kN的制動器制動力的增力時間小于500ms,超調(diào)量小于5%,能較好地跟隨正弦調(diào)制夾緊力跟隨曲線,適應制動系統(tǒng)調(diào)節(jié)夾緊力功能。 以整車EBD控制算法對HBBW制動力調(diào)節(jié)控制算法進行驗證,如下圖所示。首先根據(jù)制動踏板位移和主缸壓力等信息識別駕駛員的制動意圖,通過提前設定的主缸壓力與前輪輪缸壓力之間的關系曲線,給出前輪輪缸的目標壓力值p?(駕駛員目標壓力),通過EHB執(zhí)行器來調(diào)節(jié)前輪的制動壓力。而對于后輪的制動壓力則通過后輪的滑移率控制器來調(diào)節(jié)后輪與前輪之間的相對滑移率。后輪滑移率控制器根據(jù)前輪輪速和后輪輪速的差值,輸出目標制動器制動力給EMB控制系統(tǒng),調(diào)節(jié)后輪的制動力的大小,保證前后輪的角速度一致,達到車輪抱死時前后車輪同時抱死的目的,可表示為
混合線控制動系統(tǒng)EBD控制框圖 式中:為EMB目標制動力;
為前輪角速度;ωrw為后輪角速度;Kw-p和Kw-i為后輪滑移率PI控制器的參數(shù)。
-2.2 前輪EHB壓力調(diào)節(jié)控制算法
對于EHB系統(tǒng)輪缸壓力的控制,關鍵在于對線性增減壓閥的控制。所選的EHB系統(tǒng)前輪的增減壓閥均為常閉閥,下圖為EHB輪缸壓力跟隨控制算法框圖。為防止電磁閥過于頻繁動作,設定一個保壓壓力門限值ε(ε>0),控制過程如下:設p?為目標輪缸壓力,p為實際輪缸壓力,則當p-p?<-ε時,減壓閥關閉,控制增壓閥提升輪缸壓力;當-ε≤p-p?≤ε時,增減壓電磁閥均處于關閉狀態(tài);當p-p?≥ε時,增壓閥關閉,控制減壓電磁閥,降低輪缸壓力。在保證輪缸壓力跟隨中壓力誤差較小和減少電磁閥開關頻繁的前提下,通過試驗標定選取ε為0.05MPa。
EHB輪缸壓力跟隨控制框圖 對線性電磁閥的控制由電磁閥電流環(huán)PI控制器和輪缸壓力環(huán)PI控制器組成,其中輪缸壓力環(huán)PI控制器根據(jù)目標輪缸壓力和實際輪缸壓力的差值算得增減壓電磁閥的目標電流:
式中:為增壓閥目標電流;
為減壓閥目標電流;Kp-p1,Kp-p2,Kp-i1和?Kp-i2為壓力環(huán)PI控制器的參數(shù)。 電流PI控制器根據(jù)線性電磁閥的目標電流與實際線性電磁閥的電流差值算得調(diào)節(jié)電磁閥的線圈電壓,再換算成PWM控制線性電磁閥開度:
式中:PWM in為增壓閥控制信號;PWMout為減壓閥控制信號;Iin為實際增壓閥電流;Iout為實際減壓閥電流;KC-p1,KC-p2,KC-i1和KC-i2為電流環(huán)PI控制器的參數(shù)。
-2.3 后輪EMB制動力調(diào)節(jié)控制算法
對于EMB系統(tǒng)的輪缸壓力控制,關鍵在于對EMB執(zhí)行器電機的控制。本文中所選取的EMB執(zhí)行器電機為無刷直流電機(brushless direct current motor,BLDC)。 對BLDC的控制由電機的電流環(huán)PI控制器、轉(zhuǎn)速環(huán)PI控制器和夾緊力環(huán)PI控制器組成,如下圖所示。其中夾緊力環(huán)PI控制器根據(jù)目標制動力和實際制動力的差值算得電機的目標轉(zhuǎn)速,可表示為
式中:為電機目標角速度;Fcl為實際制動力;KF-p和KF-i為夾緊力環(huán)PI控制器的參數(shù)。
EMB制動力跟隨串聯(lián)三閉環(huán)控制框圖 電機轉(zhuǎn)速PI控制器根據(jù)電機的目標轉(zhuǎn)速與實際電機的轉(zhuǎn)速偏差計算得到電機的目標控制電流,可表示為
式中:i?為電機的目標控制電流;ωm為電機的實際角速度;KN-p和KN-i為轉(zhuǎn)速環(huán)PI控制器的參數(shù)。 電機電流PI控制器根據(jù)電機的控制電流與實際電機的電流差值算得電機的控制PWM信號:
式中:PWMm為電機的控制PWM信號;i為電機的實際電流;KC-p和KC-i表示電流環(huán)PI控制器的參數(shù)。PWMm控制BLDC在制動器上形成的制動力。
5 I-EHB集成式電子液壓制動系統(tǒng)
I-EHB系統(tǒng)是一種集成式電子液壓制動系統(tǒng),是以電機+減速機構(gòu)來代替,內(nèi)部集成電控模塊,整個系統(tǒng)結(jié)構(gòu)更加緊湊。下圖為Bosch 公司的iBooster系統(tǒng)。ibooster的響應時間為120-150毫秒,ibooster可配置同一平臺的不同車型,通過設定制動性能曲線,軟件定義“舒適型”、“運動型”多種踏板感,滿足智能駕駛的需求。
Bosch公司iBooster系統(tǒng)
典型帶有E-Booster的EHB系統(tǒng)如下圖所示。踏板位移和踏板力經(jīng)電子傳感器傳導給電子ECU,然后經(jīng)過不同的助力形式,如電動液壓泵高壓蓄能器或者直流電機等推動建立起液壓,液壓再分配給四個制動輪缸。
EHB 系統(tǒng)
(1)I-EHB系統(tǒng)主要組成結(jié)構(gòu)
1)意圖獲取模塊
意圖獲取模塊主要有制動踏板、踏板位移傳感器、踏板感覺模擬器等,制動踏板經(jīng)過踏板位移傳感器將駕駛員所踩的制動踏板位移信號發(fā)送給I-EHB的ECU。踏板感覺模擬器用來模擬真實狀態(tài)的腳感與路感。踏板和主缸之間完全解耦,腳感較輕,更便于能量回收。
2)分析控制模塊
分析控制模塊是整個線控制動的核心,主要為I-EHB的ECU。ECU 通過踏板獲取駕駛員的制動意圖后,根據(jù)相應的算法計算出最佳制動力,控制制動系統(tǒng)的執(zhí)行。ECU 由嵌入式芯片、信號采集及處理電路、通訊電路、電機驅(qū)動電路、冗余電路及I/O 口等組成。
3)液壓執(zhí)行模塊
分析控制模塊為線控制動的執(zhí)行部分,包括伺服電機、減速機構(gòu)、制動主缸等。伺服電機作為驅(qū)動電機,與減速機構(gòu)連接,可直接使用傳統(tǒng)車載12V電源,減速機構(gòu)可增強整個系統(tǒng)的扭矩,獲得更大制動力。伺服電機接收來自ECU的制動信號,通過減速機構(gòu)推動制動主缸建壓。
(2)I-EHB系統(tǒng)工作過程
I-EHB系統(tǒng)通過意圖獲取模塊、分析控制模塊、液壓執(zhí)行模塊等幾個模塊協(xié)調(diào)完成整個制動過程,I-EHB系統(tǒng)協(xié)調(diào)控制示意圖如下圖所示。
I-EHB 系統(tǒng)協(xié)調(diào)控制示意圖
在車輛正常工況下,I-EHB的ECU接收踏板位移傳感器從踏板采集的制動力位移信號,以及其他外部ECU發(fā)出的方向盤轉(zhuǎn)角、輪速、橫擺角速度等信號,來獲取駕駛員的駕駛意圖,利用算法計算得出車輪所需的最佳制動力。在制動踏板與主缸完全解耦條件下,踏板感覺模擬器可以根據(jù)駕駛員的制動動作輸出線性的腳感同時反饋車輛制動狀態(tài)。制動力轉(zhuǎn)化為電信號輸出給伺服電機,電機和減速機構(gòu)連接,通過減速機構(gòu)將電信號大小轉(zhuǎn)變?yōu)辇X條行程大小,推動制動主缸活塞,最終完成建壓。制動主缸液壓力信號將實時反饋給I-EHB的ECU,用于精確控制主缸壓力以及對制動主缸保壓。
當車輛處于緊急狀態(tài)下需要急?;蛘咧苿酉到y(tǒng)電子助力失效時,如下圖所示,I-EHB 提供備用機械制動系統(tǒng)。駕駛員快速緊急制動,迅速克服系統(tǒng)內(nèi)部的解耦腔,此時制動踏板推桿將直接作用于制動主缸,主缸液壓力大小直接由制動踏板提供,一定程度上保證緊急情況下的制動安全。
I-EHB 系統(tǒng)助力失效制動示意圖
(3)I-EHB系統(tǒng)控制方法
在傳統(tǒng)制動系統(tǒng)中,主缸液壓力完全來自制動踏板推進的深度,因此,制動時無法精確控制主缸液壓力。對于駕駛新手來說,駕駛經(jīng)驗不足不僅影響車輛制動感覺,更影響車輛在緊急狀況下整車制動的安全性。I-EHB系統(tǒng)由于采用了電控單元,同時制動踏板與主缸活塞之間完全解耦,使得主缸液壓力控制更加迅速與精確。對于I-EHB系統(tǒng)主缸液壓力的控制,實際上就是對伺服電機的控制,利用ECU根據(jù)相應的控制算法計算駕駛員需要的最佳制動力,將最佳制動力轉(zhuǎn)化為電機的電流信號或者命令力矩,從而完成主缸的建壓。
PID 控制策略圖
如上圖所示,對以電動機+減速機構(gòu)為動力源的I-EHB系統(tǒng)的控制算法,大多以閉環(huán)反饋控制為主。在閉環(huán)控制中,比例積分微分控制(PID 控制)是一種最常用的控制方法,同時可通過參數(shù)整定變化多種控制結(jié)構(gòu),獲得不同的控制效果。運用在I-EHB系統(tǒng)中的主要控制思路是通過液壓力傳感器將主缸液壓力實時反饋給ECU,將ECU計算出的期望主缸液壓力和輸出的實際主缸液壓力進行對比,然后將二者之間的偏差值利用ECU中設好的PID算法對其整定,輸出一個最合適的量給電機,對主缸液壓力進行補償。線控液壓制動10MPa主動建壓時間≤170ms,液壓控制精度≤0.1MPa。
功能安全滿足ISO 26262標準要求
(4)IEHB設計原理及設計計算(基本構(gòu)型)
(5)踏板模擬器設計
(6)IEHB樣件制作及硬件接口
(7)制動能量回收軟件策略設計和仿真
能量回收效率滿足:ECE 15城市工況下制動能量回收降低整車電耗23%。
(8)IEHB仿真和檢測設備
(9)整車集成與初步實車匹配
(10)IEHB 二代
集成了ABS、ESC等先進電子制動各項功能,同時可以擯棄真空助力器將制動主缸集成一體。采用液電一體化控制實現(xiàn)對各輪缸的制動力獨立且線性性控制。分布式驅(qū)動式制動系統(tǒng)方向為實現(xiàn)高集成度,采用集成制動主缸和踏板模擬器實現(xiàn)全解耦的方式。采用電機泵預增壓,高壓蓄能器供液的形式為制動系統(tǒng)提供制動液壓力,保證制動過程快速響應的目的。
二代踏板模擬器設計
采用三級彈簧帶有力量重疊區(qū),過渡力變化區(qū)域模擬傳統(tǒng)制動腳感,針對不同車型可以通過調(diào)節(jié)擋圈螺紋深度對二級彈簧的預壓力來微調(diào)踏板感的軟硬。
6.線控氣壓制動系統(tǒng)
五 原理
1.線控制動助力來源 如何做到常規(guī)的線控制動,這得從真空助力器說起。
單踏板的杠桿并不足以推動主缸活塞較大的行程,因為制動液(剎車油)是非常黏性的液體,與主缸缸壁之間的摩擦力很大,需要的推力很大,為此使用了真空助力器,真空助力器一般位于制動踏板與制動主缸之間,為便于安裝,通常與主缸合成一個組件,主缸的一部分深入到真空助力器殼體內(nèi)。真空助力器是一個直徑較大的腔體,內(nèi)部有一個中部裝有推桿的膜片(或活塞),將腔體隔成兩部分,一部分與大氣相通,另一部分通過管道與發(fā)動機進氣歧管相連。它利用發(fā)動機工作時吸入空氣這一原理,造成助力器的一側(cè)真空,真空源從發(fā)動機進氣歧管處獲得,相對于另一側(cè)正??諝鈮毫τ袎毫Σ睿眠@壓力差來加強制動推力。如果膜片兩邊有即使很小的壓力差,由于膜片的面積很大,仍可以產(chǎn)生很大的推力推動膜片向壓力小的一端運動。真空助力系統(tǒng)在制動時,同時控制助力器的真空度,使膜片移動,并通過聯(lián)動裝置利用膜片上的推桿協(xié)助人力去踩動和推動制動踏板。需要注意推力來自壓力差,而非真空。傳統(tǒng)剎車系統(tǒng)需要依靠真空助力器,通過真空和大氣壓的壓力差放大踏板輸入的壓力,否則單純依靠人力腳踩和杠桿、液壓的放大作用不足以形成車輪制動力。
對制動性能要求的不斷提高,傳統(tǒng)的液壓或者空氣制動系統(tǒng)在加入了大量的電子控制系統(tǒng)如ABS、ESP等后,結(jié)構(gòu)和管路布置越發(fā)復雜,液壓(空氣)回路泄露的隱患也加大,同時裝配和維修的難度也隨之提高;使用協(xié)調(diào)式回收策略,傳統(tǒng)真空助力器的制動液壓超過跳增值的區(qū)域,能量回收系統(tǒng)的制動液壓的變化會被駕駛員感知而影響踏板感,因此,只能實現(xiàn)小于0.2g減速度的能量回收。傳統(tǒng)制動系統(tǒng)是基于真空助力器的液壓制動系統(tǒng),其真空來源為發(fā)動機負壓,但是它體積大、響應慢,無法適應新型車輛的需求,不利于汽車輕量化;也無法實現(xiàn)主動制動和制動壓力的精確、快速控制,不能滿足智能汽車對制動系統(tǒng)電動化和智能化的要求。
為減少駕駛員的體力消耗,汽油乘用車采用真空助力式液壓制動(剎車)系統(tǒng),利用汽油機進氣管中的真空度產(chǎn)生助力,幫助駕駛員剎車。真空助力器會減少一部分發(fā)動機效率,所以近來有些油車上使用電子真空助力器,用電機制造真空。純電動車沒有裝配發(fā)動機,混合動力車發(fā)動機啟停都是常態(tài),電動車和混合動力車不能依賴內(nèi)燃機取得真空,需要用電子真空泵。對此,有兩種解決技術方案:
1)依然使用真空助力,采用電子(電動)真空泵EVP(Electronic Vacuum Pump)獲得真空源,采用電子(電動)真空泵產(chǎn)生真空度。
在電機技術不夠先進的1999年前,只得放棄這種電機直接推動主缸的思路,轉(zhuǎn)而使用高壓蓄能器。這套系統(tǒng)利用電機建立液壓,然后將高壓剎車油儲存在高壓蓄能器中,需要剎車時釋放。這套系統(tǒng)結(jié)構(gòu)復雜,液壓管路眾多,成本高昂,可靠性不高。由于成本過高,從2007年起,電子真空泵EVP開始在電動車或混動車上取代這種高壓蓄能器設計,EVP極為簡單,就是將油車的真空助力器換為電子真空泵獲得真空,缺點非常明顯,首先它幾乎沒有任何能量回收,使用疊加式回收策略,EVP與制動系統(tǒng)并聯(lián),能量回收率只有ibooster+ESP HEV協(xié)調(diào)式回收方案的5%左右,能量回收效率遠低于線控制動;其次,EVP因自身結(jié)構(gòu)以及轉(zhuǎn)速較高的原因,剎車時會發(fā)出刺耳的噪音,噪音小的葉片式真空泵則成本高;EVP方案壽命短,設備常見的使用壽命為600-1200h;EVP方案獲得的真空源并不穩(wěn)定,真空泵產(chǎn)生負壓的穩(wěn)定性受大氣環(huán)境影響,因此EVP無法在高原地區(qū)獲得足夠的真空度,有高原反應,該工況下剎車助力被削弱;最主要是EVP方案常規(guī)制動依然必須由人力首先踩下制動踏板再逐級放大,也就是說它并非線控制動,而是機械制動,滿足自動駕駛需求。優(yōu)點也很明顯,首先是EVP電子真空泵雖然對底盤改動小、價格低/成本很低,再者是設計異常簡單,油車的底盤幾乎不做絲毫改動就可以用來做混動車,這對中國企業(yè)來說非常重要,因缺乏自主設計底盤能力。
現(xiàn)有新能源汽車的制動系統(tǒng)主要是采用真空助力器和電動真空泵EVP結(jié)合提供負壓的過渡產(chǎn)品,這種形式的制動系統(tǒng)未能很好地實現(xiàn)踏板力與車輛制動力之間的解耦和制動能量回收的功能;電動真空泵和真空儲能機構(gòu)的體積和噪聲較大,且難以和其他底盤電子控制系統(tǒng)集成。作為線控制動的替代方案,但不是長久之計。
2)放棄真空助力器,轉(zhuǎn)用電子助力器,完全用電機助力來實現(xiàn),由線控制動系統(tǒng)直接建壓。新能源車型沒有穩(wěn)定真空源,線控制動對比電子真空泵優(yōu)勢明顯。目前電動汽車更傾向于應用電子(電動)助力器,如日本日立公司推出的e-ACT和博世公司推出的iBooster等,
基本發(fā)展路徑如下圖示。
線控制動正是從真空助力器延伸開來,用一個電機來代替真空助力器推動主缸活塞。由于汽車底盤空間狹小,電機的體積必須很小,同時要有一套高效的減速裝置,將電機的扭矩轉(zhuǎn)換為強大的直線推力,這其中的關鍵因素就是電機主軸。隨著電機技術的
發(fā)展,在2009年首次推出電液線控制動系統(tǒng)E-ACT。大部分日系混動或純電車都采用這種設計。用直流無刷超高速電機配合滾珠絲杠直接推動主缸活塞達到電液線控制動,這套方案對滾珠絲杠的加工精度要求很高。傳統(tǒng)的液壓制動系統(tǒng)反應時間大約400-600毫秒,電液線控制動大約為120-150毫秒,安全性能大幅度提高,百公里時速剎車大約最少可縮短9米以上的距離,同時用在混動和電動車上,可以回收幾乎99%的剎車摩擦能量。使用協(xié)調(diào)式回收策略,ibooster與ESP HEV協(xié)調(diào)最高可回收0.3g減速度,在制動頻繁的城市路況下,續(xù)航里程增加10%-20%;是目前公認最好的制動方式。為了保證系統(tǒng)的可靠性,這套制動系統(tǒng)一般都需要加入ESP(ESC)做系統(tǒng)備份。這類制動系統(tǒng)具備變助力比功能,能提供較好的駕駛感受、實現(xiàn)部分能量回收和主動制動功能。然而,該類制動系統(tǒng)仍然無法實現(xiàn)踏板力與車輛制動力之間的解耦及單輪制動力調(diào)節(jié),要實現(xiàn)上述功能,需要額外添加器件,增加系統(tǒng)的復雜度。2.工作原理
線控制動系統(tǒng)將原有的制動踏板用一個模擬發(fā)生器,用來接收駕駛員的制動意圖,產(chǎn)生、傳遞制動信號給控制器和執(zhí)行機構(gòu),并根據(jù)一定的算法模擬反饋給駕駛員,如下圖。
傳統(tǒng)液壓制動系統(tǒng)實現(xiàn)車輛制動功能是直接通過液壓裝置來傳遞和實施的,而線控制動系統(tǒng)則是利用物理信號傳遞制動信息,使用電子控制單元控制機電一體化裝置來實施制動。線控制動簡單理解是電開關版的蝶式剎車,不需要再經(jīng)過油壓轉(zhuǎn)換,直接讓電控單元驅(qū)動活塞,卡鉗夾緊制動片以達到剎車制動效果,從而直接實現(xiàn)“電”信號對制動系統(tǒng)更直接的管理。下面分別簡述EHB和EMB的工作原理和特性。
(1)EHB 系統(tǒng)
EHB原理:電機液一體化,電機取代真空助力器
汽車駕駛員的制動動作被踏板上的傳感器感轉(zhuǎn)化成電子信號,電子控制單元接受到信號后,命令液壓執(zhí)行機構(gòu)完成制動的操作。EHB能根據(jù)路面的附著情況和轉(zhuǎn)速為每個車輪分配最合理的制動力,從而可以更充分地利用車輪和地面之間的摩擦力,使制動距離更短,制動過程更安全。
電子液壓制動系統(tǒng)示意圖
當駕駛員踩下制動踏板時,制動(電子)踏板配有踏板感覺模擬器和電子傳感器,集成在制動踏板上的傳感器將制動踏板的行程及駕駛?cè)瞬认驴刂铺ぐ鍟r的速度,轉(zhuǎn)換為電信號傳遞給制動控制單元(ECU),ECU通過CAN 總線與外部系統(tǒng)交流,綜合其它電信號判斷車輛的運行工況,ECU可以通過傳感器信號判斷駕駛員的制動意圖,計算出每個車輪的最佳制動力,并通過智能接口輸出控制信號到液壓系統(tǒng),液壓系統(tǒng)中包含由電動油泵和高壓蓄能器組成的液壓供給部分和車輪制動壓力模塊,車輪制動壓力模塊獨立的控制和調(diào)節(jié)各個車輪制動器中的油壓大小,進液閥開啟,液壓供給部分的高壓油液進入車輪制動器,通過電機驅(qū)動液壓泵進行制動,使制動器工作對車輪產(chǎn)生制動力。當減小車輪制動強度或解除制動時,出液閥開啟,車輪制動器中的油壓降低,制動力也隨之減小,直至制動器完全退出工作(上圖 )。輪缸里面的制動液不是通過主缸過來的,是通過高壓蓄能器里面,通過液壓泵來提供一個壓力源,提供一個制動液源,來進入輪缸,達到需要的制動的制動力。EHB系統(tǒng)的車輪制動壓力模塊能根據(jù)汽車行駛工況要求,計算出各車輪需要的制動力并分別進行控制,所以,EHB系統(tǒng)能夠有效減少車輛制動距離,提高行駛安全性。此外,為了使駕駛員對于制動強度有直觀的感受,線控制動系統(tǒng)中通常采用踏板行程模擬器,踩制動踏板的行程越大,模擬器上的阻力也就越大,使駕駛員在使用線控制動系統(tǒng)時和使用傳動的液壓制動系統(tǒng)感受基本相同。
正常工作時,制動踏板與制動器之間的液壓連接斷開,是完全解耦的,備用閥(隔離閥/開關)處于關閉狀態(tài)。打開進油閥和關閉出油閥,制動液從蓄能器通過進油閥進入制動輪缸實現(xiàn)增壓;打開出油閥和關閉進油閥,制動液從制動輪缸通過出油閥返回制動液罐實現(xiàn)減壓;進油閥及出油閥均處于關閉狀態(tài)則實現(xiàn)保壓。當需要單獨控制某側(cè)制動輪缸壓力時需要關閉平衡閥,由其對應的進油閥和出油閥工作。
為防止EHB系統(tǒng)失效造成制動失靈,EHB系統(tǒng)仍然保留著傳統(tǒng)的液壓制動系統(tǒng),當電子系統(tǒng)發(fā)生故障時,EHB系統(tǒng)失效時,備用開關(閥)打開(上圖),制動踏板連接的制動主缸通過備用開關(閥)連接各個車輪制動器的制動輪缸,進入常規(guī)的液壓系統(tǒng)制動模式,EHB系統(tǒng)變?yōu)閭鹘y(tǒng)的液壓系統(tǒng),保證車輛制動的基本需要。這時假設液壓泵壞了,這個油進去了,但是備用閥打開之后,那么從制動踏板和主缸過來的制動液,還是可以進入相應的輪缸,達到一定常規(guī)制動的效果,所以這是一個安全性的保證。制動踏板輸入信號后驅(qū)動制動主缸中的制動液通過備用閥流入連接各個車輪制動器的制動輪缸,進入常規(guī)的液壓系統(tǒng)制動模式,是保證車輛制動的必要安全保障。
當EHB的供能裝置出現(xiàn)故障時隔離閥無法打開,駕駛員仍能通過踩下制動踏板將制動主缸內(nèi)的制動液經(jīng)隔離閥和制動管路送入制動輪缸,實現(xiàn)一定強度的制動。
備用系統(tǒng)增加了制動系統(tǒng)的安全性,使車輛在線控制制動系統(tǒng)失效時還可以進行制動。當制動器涉水后,EHB系統(tǒng)可以通過適當?shù)闹苿觿幼?,恢復制動器的干燥,保持制動器的工作性能。由于EHB采用了線控技術,在制動器和制動踏板之間沒有液壓或機械連接,因此,當制動強度過大,進行防抱死調(diào)節(jié)時,制動踏板上感受不到由于液壓管路油壓波動產(chǎn)生的反沖作用力,提高了駕駛員的操作舒適性。
(2)EMB系統(tǒng)
EMB原理:電機一體化,電機直接驅(qū)動制動器
EMB系統(tǒng)的主控制器(制動控制單元ECU)工作時通過接收踏板位移傳感器傳來的踏板行程的位移信號,ECU計算出踩制動踏板的速度信號并結(jié)合整車其他ECU發(fā)出的車速信號、方向盤轉(zhuǎn)角信號等相關信號,明確汽車行駛狀態(tài),分析各個車輪上的制動需求,計算出各個車輪的最佳制動力矩大小后輸出對應的控制信號,分析后向4個車輪制動模塊發(fā)出制動指令,控制四個獨立的控制器向?qū)碾姍C發(fā)出制動信號,分別控制各車輪上的電子機械制動器中工作電機的電流大小和轉(zhuǎn)角,通過電子機械制動器中的減速增矩以及運動方向轉(zhuǎn)換,將電機的轉(zhuǎn)動轉(zhuǎn)換為制動鉗塊的夾緊,產(chǎn)生足夠的制動摩擦力矩。電機通過減速機構(gòu)將電機扭矩轉(zhuǎn)化為所需的制動力,車輪制動模塊上的電機驅(qū)動制動摩擦材料塊,然后實現(xiàn)摩擦制動。每一個車輪都有一個制動模塊,可以單獨分別控制,每個模塊的驅(qū)動電機也都有單獨的電機控制器。車輛轉(zhuǎn)向時,每個車輪制動系統(tǒng)分配的制動力不一樣,4個模塊作用下,實現(xiàn)制動力分配,制動穩(wěn)定性控制等功能,從而達到平穩(wěn)轉(zhuǎn)向的目的。踩一下自動踏板,通過自動踏板傳感器得到駕駛員的駕駛意圖,通過ECU處理之后直接驅(qū)動車輪上面的制動模塊,這里是四個電機直接進行制動。制動力矩完全是通過安裝在4個輪胎上的由電機驅(qū)動的執(zhí)行機構(gòu)產(chǎn)生,驅(qū)動和控制執(zhí)行機構(gòu)電機來產(chǎn)生所需要的制動力。
電子機械制動系統(tǒng)
線控制動系統(tǒng)在原理上帶來革新的同時也產(chǎn)生了一個不可忽視的問題:線控制動系統(tǒng)的制動增益系數(shù)與傳統(tǒng)的液壓制動系統(tǒng)相比較低,由于制動電機的增多以及功率的加大,這就使得線控制動系統(tǒng)需要消耗過多的車載能源,再加上受到車載電氣系統(tǒng)的限制,12V電源無法滿足制動需求,12V電源成為限制EMB發(fā)展的重要因素,電子機械制動系統(tǒng)的應用一直得不到廣泛的推廣。EMB相對汽車的應用來說,太過超前,而且同時由于沒有備用的制動系統(tǒng),安全性還有待提升,安全冗余一直被業(yè)界質(zhì)疑。
(3)EHB與EBM差異
EHB和EMB在傳力路徑上有很大不同,工作原理和特性也有差別:
這兩種制動系統(tǒng)各有優(yōu)勢,也都有各自的缺點。
EHB制動系統(tǒng)仍然保留了制動液,仍包含復雜的制動液傳輸管路,系統(tǒng)液壓管路布置復雜且難以集成駐車制動;雖然EHB能完全獨立于制動踏板而進行制動,但是其物理線路沒有延伸到車輪制動器,仍需要制動液將制動能量從蓄能器傳遞到制動輪缸,連續(xù)制動時,由于高壓蓄能器壓力的衰減,維持響應速度與精度能力均不及EMB,使得EHB并不完全具備線控制動系統(tǒng)產(chǎn)品的優(yōu)點,EHB并非終極方案;這類制動系統(tǒng)具備變助力比功能,能提供較好的駕駛感受、實現(xiàn)部分能量回收和主動制動功能。然而,該類制動系統(tǒng)仍然無法實現(xiàn)踏板力與車輛制動力之間的解耦及單輪制動力調(diào)節(jié),要實現(xiàn)上述功能,需要額外添加器件,增加系統(tǒng)的復雜度。
從本質(zhì)而言,電子液壓制動系統(tǒng)EHB并不是真正意義上純粹的線控制動系統(tǒng),它需要液壓系統(tǒng)放大制動能量。但就目前而言,這種結(jié)構(gòu)相比于其他線控制動系統(tǒng)具有一定的優(yōu)勢,因為EHB是從傳統(tǒng)液壓制動系統(tǒng)進化而來,具有冗余系統(tǒng),它基于傳統(tǒng)液壓制動系統(tǒng),原有的液壓制動系統(tǒng)結(jié)構(gòu)得以保留,易于實現(xiàn)失效備份,可以使用人力在供能裝置失效的情況下作為備用制動選項,就是液壓管路的方式是有液壓后備的,一旦線控失效之后,制動液還會從正常的液壓管路進入輪缸,可以提供部分的制動效能,使車輛在線控制系統(tǒng)失效時還可以進行制動。具備可靠的機械備份,即車載電源失效時啟用純液壓助力。備用系統(tǒng)增加了制動系統(tǒng)的安全性,安全性上有一定的保證,安全穩(wěn)定才是剎車系統(tǒng)的第一要務,其高安全性在用戶的可接受性方面更具優(yōu)勢。且此類產(chǎn)品成熟度高,兼具液壓制動系統(tǒng)高制動增益系數(shù)和線控制動的優(yōu)點,可以實現(xiàn)新能源車所需要的協(xié)調(diào)式制動策略,得到汽車零部件生產(chǎn)廠商的重視。
目前行業(yè)內(nèi)研究的主要方向是EHB,很大的一部分原因是具有備用制動系統(tǒng),是現(xiàn)階段的首選方案,是當前主要推廣量產(chǎn)的方案,目前已實現(xiàn)應用。目前線控制動系統(tǒng)更多的應用形式是EHB,這是汽車電動化以及智能化發(fā)展所必需。EHB是制動系統(tǒng)革命性產(chǎn)品,是智能駕駛的關鍵執(zhí)行部件,對智能網(wǎng)聯(lián)汽車的發(fā)展具有重大推動作用,已成為行業(yè)公認的下一代汽車制動系統(tǒng)主流解決方案。
EMB可以將傳統(tǒng)制動系統(tǒng)中的液壓油或空氣等傳力介質(zhì)完全由電制動取代,直接將輸入與終端執(zhí)行之間的部件全部簡化,因此只有EMB是完全的線控制動,因結(jié)構(gòu)簡單、制動效果好、易于與其他電控功能集成在一起,與EHB相比,EMB是更優(yōu)的方案,它不以制動液為工作介質(zhì),控制響應更加迅速精確,逐漸成為汽車制動系統(tǒng)的研究熱點。雖然具有諸多優(yōu)點,但EMB沒有機械冗余,沒有液壓后備制動系統(tǒng)且缺乏技術支持,很難滿足失效備份的需求,一旦執(zhí)行機構(gòu)或者EMB系統(tǒng)出現(xiàn)問題的話,常規(guī)制動可能就沒有了,沒有保險措施,在安全性上面可能會有一些顧慮。必須具有很高的設備可靠性、總線協(xié)議和抗信號干擾能力,尤其是需要解決車載電源失效問題。此外,剎車片產(chǎn)生的高溫巨震環(huán)境對電機穩(wěn)定性、芯片半導體和永磁材料造成巨大考驗,短期內(nèi)難有突破。其制動力能力依賴于較大的驅(qū)動功率,必須配備42V電源系統(tǒng),更為關鍵的是,EMB系統(tǒng)不能滿足現(xiàn)行法規(guī)對制動系統(tǒng)失效備份的需求。雖然國內(nèi)外企業(yè)與高校均研發(fā)EMB原理樣機,目前EMB還處在研究階段,由于缺乏足夠的技術支持,但還不具備進入市場的條件。
EMB理論上完美,但由于技術條件較高,成本較高,冗余備份,電機性能等限制以及熱可靠性技術等還需完善,這些問題都阻礙了EMB系統(tǒng)在短期內(nèi)的量產(chǎn),應該說比較長的一段時間內(nèi)很難大批量應用,至少在國內(nèi)肯定是一個長時間的過程,目前市場上并沒有批量裝車的EMB產(chǎn)品。
因此綜上所述,線控化的EHB系統(tǒng)仍然是最為可行的制動系統(tǒng)方案。現(xiàn)在汽車上的線控制動還是集中在EHB,而且還沒有對傳統(tǒng)制動系統(tǒng)構(gòu)成威脅。EMB雖然有著比傳統(tǒng)的液壓制動器和EHB兩者都無法比擬的優(yōu)勢和廣闊的運用前景,雖然是未來制動系統(tǒng)的終極發(fā)展方向,必然是未來的趨勢,可能成為主流,但EMB技術在汽車上的應用并不成熟,短期內(nèi)難以量產(chǎn),未來5-10年線控技術的主流仍是EHB方案,仍以EHB為主,EHB為現(xiàn)有技術條件下的主要方案,是現(xiàn)在研究的主流方向或者說是在目前狀態(tài)下主要研究的一個產(chǎn)品。若材料方面無法突破,EHB占據(jù)主導地位的時間將更久。只有解決了一些制約其自身發(fā)展的關鍵因素,才能得到越來越廣發(fā)應用。目前來看EMB商業(yè)化之路的優(yōu)先級明顯低于EHB,但是從線控制動系統(tǒng)長遠發(fā)展來說,它是一個未來發(fā)展的方向,是線控制動最終形態(tài)。EHB系統(tǒng)僅僅只是一個先期的產(chǎn)品,EHB是傳統(tǒng)液壓制動到EMB的一個過渡產(chǎn)品,最終的產(chǎn)品一定是一個EMB系統(tǒng)。EMB的可靠性對其商業(yè)化有著至關重要的作用。EMB技術肯定會得到大力的發(fā)展,未來會向液壓制動系統(tǒng)發(fā)起強有力的挑戰(zhàn)。線控制動的發(fā)展之路還任重道遠。
EHB與EMB主要不同點:
1) EMB減少機械連接件和閥類元件,一方面使得結(jié)構(gòu)更加緊湊,減輕車重,提供更大的內(nèi)部空間,便于布置、裝配和維修;另一方面電信號傳遞更迅速、高效;
2) EMB需要對底盤進行更大范圍的改造,造價高;
3) EMB不存在液壓油泄露問題,電池更加安全;
4) EMB便于集成其他電控系統(tǒng),如ABS、ESP、自動駕駛、能量回收等;
5) EHB 可以打開液壓管路備用閥作為其中一道安全失效模式,EMB則沒有機械冗余。
(4)線控制動兩種技術路線:EHB與EMB
EHB(Electro-hydraulic Brake)保留傳統(tǒng)的液壓工作方式,博世ibooster和采埃孚EBB(Electronic Brake Booster)都是vacuum booster真空助力器的局部替代方案。ibooster制動信號的產(chǎn)生可以來自踏板,踏板行程傳感器測量到輸入推桿的位移后,將該位移信號發(fā)送到ECU,由ECU計算制動請求;也可以由ECU根據(jù)場景需要主動生成制動需求。ECU計算出電機應產(chǎn)生的扭矩,二級齒輪傳動裝置將該扭矩轉(zhuǎn)化為助力器閥體的伺服制動力,通過電機轉(zhuǎn)化為強大的直線推力,推動制動主缸推桿。
與EHB相比,EMB主要組件差異是系統(tǒng)內(nèi)沒有制動液。燃油車EHB主要適用智能駕駛的場景,新能源車EHB適用于智能駕駛、能量回收等多場景。
(5)線控制動EHB路線BOX之爭:One-Box vs. Two-Box
確定了EHB的技術路線,接下來就是具體的實現(xiàn)方法了,目前EHB的線控制動方案又出現(xiàn)了兩大流派: Two-Box 和One Box。但作為線控制動,無論是Two-Box還是One-Box,相比較傳統(tǒng)制動系統(tǒng),都有非常優(yōu)秀的性能體現(xiàn)。
Two-Box和One-Box又有各自的優(yōu)劣勢,要評價二者優(yōu)劣,必須對它們的性價比進行一次分析。 One-Box較Two-Box性能上更具優(yōu)勢,但Two-Box目前安全性更有保障,One-Box需要看踏板調(diào)教的安全性。One-Box的集成度更高,是未來的主流方案。 One-Box方案集成ESP,需以成熟ESP技術為基礎,Two-Box方案協(xié)調(diào)ESP,可通過外采ESP降低技術難度。
One-Box方案由于將ESP集成在EHB中,更需要以成熟的ESP量產(chǎn)經(jīng)驗為基礎,由于其在性能、成本等方面的優(yōu)勢,博世、大陸、采埃孚正在逐步加碼One-Box產(chǎn)品,有望成為市場主流。同時,EHB在新能源汽車的滲透率更高且增速更快,國產(chǎn)One-Box方案在價格上較主流Two-Box方案具有明顯優(yōu)勢,具備先發(fā)優(yōu)勢的自主供應商有望實現(xiàn)國產(chǎn)替代。
從對比來看,Two-Box相比較One-Box最大的優(yōu)勢在L3自動駕駛工況下的制動冗余需求,拋開這一點One-Box完勝。 L2級別的自動駕駛明確了是要駕駛員主導操作車輛的,而L3則是有限條件下的自動駕駛,也就是說它可以完全不需要駕駛員干預,但是有的時候又必須駕駛員干預。
駕駛員和車輛自主控制之間如何相互接管就成了一大問題,因為這之間并沒有一個明顯的界定,所以假設出了交通事故,是需要駕駛員和汽車共同承擔責任,而這也是相關法律法規(guī)最模糊的地方,基于這樣的模糊定義,現(xiàn)在的L3的定義被大范圍的詬病。
甚至不少品牌直接放棄了L3級別自動駕駛的研發(fā),比如福特、沃爾沃就表示會直接從L2到L4,電動車企蔚來也表示會跳過L3,直接進入L4。而以自動駕駛聞名的特斯拉自始至終都沒有給自己的產(chǎn)品定過級,只表示會進入L4時代。
之所以大部分廠商在向L3不遺余力,其實更多是為了避免被扣上“無創(chuàng)新”的帽子。實際上,法規(guī)、技術等層面上,L3的發(fā)展遠比想象的要復雜得多。
奧迪曾經(jīng)在L3領域投入數(shù)十億歐元的巨資研發(fā),這已經(jīng)接近A8的研發(fā)費用了。奧迪將L3級別自動駕駛的弱化,更像是在L3遇到瓶頸遲遲不能在量產(chǎn)車上實現(xiàn)之后,奧迪認清了L4才是正確方向。
一些大的供應商,比如BOSCH ,在它的WHA系統(tǒng)在實施車輛變道動作時,只允許車輛脫離控制20s,它是實現(xiàn)了L3的定義功能的,但是它又不允許用戶完全放開接管車輛,無限接近L3的功能但是不脫離L2的定義,是現(xiàn)階段最穩(wěn)妥也最常見的做法,所以有了越來越多的L2+和L2.5,至于L3,沒有哪個供應商能給到明確的時間。
所以現(xiàn)在行業(yè)里慢慢形成了共識,One Box是目前新能源車型線控制動較為理想的解決方案。
一句話總結(jié)核心原因:LV3自動駕駛遙遙無期,但能量回收的需求確實迫在眉睫。在滿足當前核心需求的前提下,肯定選擇性價比最高的方案。 但就目前市場出貨量來看,還是以BOSCH的iBoost+ESP的Two-Box 出貨量最大。 分析大眾集團大規(guī)模的采用了Two-Box 方案,其原因大概是因為大眾同一平臺應用車型眾多,為了兼顧高-中-低端車型的需求,用Two-Box最為經(jīng)濟,比如MQB平臺下的奧迪/斯柯達/大眾/西雅特都有車型應用,如果采用One-Box方案,那只有唯一的選擇,無論高中低端車型必須用One-Box,而采用Two-Box方案,相對來說靈活性更高一點,比如低端車采用傳統(tǒng)的助力器+ESP,而高端車采用iBoost+ESP這樣就避免的大規(guī)模更改的成本增加。
現(xiàn)在這些大的供應商也意識到在當前5-10年之內(nèi),L3以上的自動駕駛還將處于叫好不叫座的尷尬狀況,而能量回收、EVPHEV卻是不折不扣的大量涌現(xiàn)。沒有自動駕駛制動冗余這一緊箍咒之后,One-Box成了線控制動的最佳選擇。所以各供應商也都在積極的開發(fā)自己的One-Box產(chǎn)品。
EHB將采取one-box方案
定義one-box方案和two-box方案的標準在于ABS/ESP系統(tǒng)是否和電子助力器集成在一起。以ibooster為例,必須和ESP HEV配合才能與踏板解耦,采用協(xié)調(diào)式能量回收策略,否則未完全與踏板解耦,踏板力和電機共同作用產(chǎn)生主缸制動力,只能采用疊加式回收策略,制動效果和回收效率大打折扣。未來集成化的one-box方案必然會取代two-box。
相較于two box,one-box體積和重量大大縮小,成本更低,但由于技術問題量產(chǎn)時間更晚。博世第一代、第二代ibooster均采用two-box方案,最新一代IPB則采用one-box方案;采埃孚EBB屬于two-box方案,IPB屬于one-box方案;大陸MK C1和伯特利WCBS直接采用one-box方案。
4線控制動BBW技術研究
智能汽車對制動系統(tǒng)提出的主要需求包括:電動助力、主動制動、線控制動及失效備份等功能。
汽車線控制動技術主要由檢測的反饋系統(tǒng)、信號的處理單元、執(zhí)行器等多項結(jié)構(gòu)組成,所有環(huán)節(jié)相關聯(lián)系,相關作用,根據(jù)其本身獨立的功能工作,以推動系統(tǒng)能夠穩(wěn)定的運行,使以充分發(fā)揮。例如在檢測反饋系統(tǒng)中,是將各種傳感器中檢測的信號進行放大、轉(zhuǎn)換,顯示出反饋的信號。
(1)BBW制動力分配
傳統(tǒng)的液壓制動系統(tǒng)中制動主缸與制動輪缸之間通過液壓管路直接相連,這使得制動主缸的壓力與各車輪的制動壓力之間存在一個確定的關系,通常前輪制動壓力等于主缸壓力,后輪制動壓力與前輪制動壓力成一個確定的比例關系,同一車軸上左右車輪的制動壓力則是相等的。受此硬件條件的限制,液壓制動系統(tǒng)在設計制動力的分配時做了一定的折衷.這使得在制動過程中,制動壓力無法在前左右四個車輪之間進行動態(tài)的,合理的分配,從而在大多數(shù)情況下,各個車輪的附著條件無法得到充分的利用,不能有效的縮短制動距離,甚至可能發(fā)生后輪先于前輪抱死,后軸發(fā)生側(cè)滑,導致危險的事故。
BBW系統(tǒng)是由電機來提供制動力,由于其具有結(jié)構(gòu)簡單,質(zhì)量輕,響應迅速,易于采用模塊化結(jié)構(gòu),易于進行改進與增加功能等諸多特性,成為了一個研究的熱點。控制動系統(tǒng)中制動踏板與制動器之間僅通過電路相連,當駕駛員踩下制動踏板時,制動壓力可以在四個車輪之間進行靈活的分配。為了使各個車輪的附著條件均得到充分的利用。
線控制動系統(tǒng)制動力分配策略研究
本文提出了基于各車輪垂直載荷的線控制動系統(tǒng)制動力分配策略。為了驗證該分配策略的有效性,通過聯(lián)合MATLAB/Simulink與車輛動力學軟件Carsim。分別在直道與彎道制動的情況下對線控制動車輛與液壓制動車輛進行了對比仿真。
-1 控制動系統(tǒng)的結(jié)構(gòu)和工作原理
線控制動系統(tǒng)的基本組成如下圖所示.它主要包括制動踏板模塊、中央控制器、車輪制動模塊、通訊網(wǎng)絡、電源模塊等部分。
當駕駛員踩下制動踏板時,制動踏板模塊通過壓力傳感器和角位移傳感器辨識駕駛員的制動意圖.中央控制器根據(jù)駕駛員的制動意圖,并結(jié)合整車縱向加速度傳感器、整車側(cè)向加速度傳感器以及輪速傳感器等傳感器的信息,按照一定的分配策略,計算各個車輪制動力的大小,井將計算結(jié)果通過通訊網(wǎng)絡傳人各車輪制動模塊,車輪制動模塊控制電機來實施制動。電源模塊用于給系統(tǒng)的各個部分提供能量。 控制動系統(tǒng)的制動力分配策略 -2.1 最優(yōu)的制動力分配 動力分配進行了研究,并將牽引系數(shù)(Ⅱ卵-tioncoemcient)定義為制動力與車軸動態(tài)載荷的比值,如式(1)所示;
其中蘆。為第i車軸的牽引系數(shù),n為第j車軸的制動力,如為第i車軸的動態(tài)載荷。在任何程度的減速情況下,施加合適的制動力使前后車軸的牽引系數(shù)相同,直到兩個車軸同時達到附著極限,這就是最優(yōu)的制動力分配。此時,等式(2)是成立的: ? 其中pⅣ和p。分別為前后車軸的牽引系數(shù),a為整車的減速度(以重力加速度g為單位)。車輛在彎道上制動時,同一車軸上左右車輪之間的垂直載荷并不相同。類比于直道制動的情況,若要使制動力分配最優(yōu),須施加合適的制動力使四個車輪的牽引系數(shù)相同.直到四個車輪同時達到附著極限,如式(3)所示。
-2.2 制動過程中縱向及側(cè)向載荷的轉(zhuǎn)移 由以上分析可知,要合理的分配制動力,必須實時的估計制動過程中各個車輪上的垂直載荷。當車輛在直道制動時.可以利用整車參數(shù)和縱向減速度,通過式(4)來估計前后車軸之問的載荷轉(zhuǎn)移:
其中4B為前后車軸之間的載荷轉(zhuǎn)移,m為懸掛質(zhì)量m和m。分別為前后車軸的非懸掛質(zhì)量,‘和‘分別為前后車輪的轉(zhuǎn)動慣量h。為懸掛質(zhì)量重心高度,h為非懸掛質(zhì)量重心高度£為軸距,r為車輪半徑.a(chǎn)為整車縱向減速度。載荷在左右車輪之問的轉(zhuǎn)移可以通過整車參數(shù)和側(cè)向加速度來估計1。將連接前、后懸架側(cè)傾中心的直線定義為側(cè)傾軸線,當整車存在側(cè)向加速度時,側(cè)傾軸線的力矩大小為:
-2.3 直道上制動時的制動力分配策略
當車輛即將停下時,由于懸架的振動,使各車輪的垂直載荷發(fā)生較大的波動,由此將導致后輪的制動壓力也存在較大的波動。因此,當車速低于3km/h時,使線控制動系統(tǒng)的制動力的分配方式與液壓制動系統(tǒng)相同。 -2.4 彎道上制動時的制動力分配策略 彎道上制動時先根據(jù)前后車軸總的垂直載荷來分配前后車軸總的制動壓力,其數(shù)值大小與3.3中所算手導的各車軸總的制動壓力大小相等。然后再將總的制動壓力在左右輪之間進行分配,使左右輪壓力之比等于垂直載荷之比,最終各個車輪之間的制動壓力將滿足式(3)所示的最優(yōu)關系。同樣為了避免車輛即將停下時制動壓力的大幅波動,當車速低于3kra/h時,使線控制動系統(tǒng)制動力分配方式與液壓制動系統(tǒng)相同。 (2)EHB液壓力控制 傳統(tǒng)制動系統(tǒng)由于制動踏板與主缸活塞推桿之間的機械連接未解耦和真空助力器的非線性使主缸液壓力難以精確控制。 對于EHB系統(tǒng),液壓力控制的平穩(wěn)、精確、快速是汽車對于制動系統(tǒng)的基本要求。汽車的電動化和智能化對液壓力控制算法的控制精度、適應性和魯棒性要求進一步提高。液壓力控制算法對整車的制動舒適性和操縱穩(wěn)定性影響也有待進一步討論。
從主缸液壓力控制和輪缸液壓力控制這兩大層面對EHB系統(tǒng)液壓力控制方面的國內(nèi)外發(fā)展現(xiàn)狀進行深入研究。
1. 液壓力控制架構(gòu)
1.1 電子液壓制動系統(tǒng)的液壓力控制架構(gòu)
液壓力控制是EHB的基本功能,也是車輛穩(wěn)定性控制系統(tǒng)和再生制動系統(tǒng)等的關鍵技術。因此,液壓力控制的性能優(yōu)劣是整車性能的重要一環(huán)。液壓力控制層是整車控制系統(tǒng)的最底層,所以整車控制效果的優(yōu)劣與液壓力控制密切相關。如果沒有液壓力控制模塊或者液壓力控制模塊不能有效對液壓力施加控制,那么整車控制系統(tǒng)的控制性能會受到很大影響。與此同時,液壓力控制方法是伴隨著整車控制系統(tǒng)的變化而不斷發(fā)展的。
國外知名整車和零部件公司等均提出了電子液壓制動系統(tǒng)方案及其液壓力控制方法。
電子液壓制動系統(tǒng)液壓力控制架構(gòu)
輪缸液壓力控制層面又分為輪缸液壓力上層控制和電磁閥底層控制。前者用于計算出電磁閥的控制指令;后者用于確定電磁閥的控制方法。EHB系統(tǒng)的液壓力控制架構(gòu)如上圖所示。 2. 主缸液壓力控制電磁閥控制
在ESC中,電動機液壓泵的能力和HCU的限制對控制效果有很大影響,此時如果能夠?qū)χ鞲滓簤毫_控制,會較大改善控制效果和提高車輛穩(wěn)定性。
傳統(tǒng)制動系統(tǒng)不能滿足要求,而EHB系統(tǒng)能夠精確控制主缸液壓力,即利用一定的控制算法計算出電動機或電磁閥的控制指令,穩(wěn)定、準確、快速地跟蹤目標主缸液壓力,從而滿足制動系統(tǒng)的新要求。其中,
液壓驅(qū)動單元屬于「電動機+減速機構(gòu)」形式的EHB系統(tǒng)對主缸液壓力控制的過程實際上是對電動機的控制過程,控制器輸出為電動機的命令電流或命令力矩;
液壓驅(qū)動單元屬于「液壓泵+高壓蓄能器」形式的EHB系統(tǒng)對主缸液壓力控制的過程是對電磁閥的控制過程,控制器輸出為電磁閥的控制指令。
現(xiàn)有的主缸液壓力控制方案如下表所示。
電子液壓制動系統(tǒng)主缸液壓力控制方案
2.1控制變量
對于液壓驅(qū)動單元為「電動機+減速機構(gòu)」形式的EHB系統(tǒng),主缸液壓力控制效果的直接判據(jù)是主缸液壓力。因此,直接以主缸液壓力作為控制變量,其優(yōu)點是觀測容易,而且對制動系統(tǒng)的改造不大而易于實現(xiàn),但由于液壓系統(tǒng)PV特性在低壓工作點處存在死區(qū),所以低壓范圍不能實現(xiàn)精確控制。間接以主缸活塞推桿位移為控制變量,解決了上述以主缸液壓力作為控制變量存在的問題,但主缸活塞推桿位移傳感器不易布置且成本較高。對此,MK C1和IBC在電動機內(nèi)部安裝轉(zhuǎn)角傳感器,以電動機轉(zhuǎn)動角度為控制變量,實際上能夠間接得到主缸活塞推桿位移,從而對主缸液壓力進行控制。
對比以上幾種單控制變量的控制系統(tǒng),在液壓閉環(huán)控制時,存在「殘留液壓力」問題,此時主缸活塞將不再動作而「滯留」在非零壓處。雖然企業(yè)中對于「殘留液壓力」的要求有一定容許量,但是如果主缸活塞一直「滯留」,那么制動系統(tǒng)將變得越來越「硬」,從而影響正常工作。相比于液壓閉環(huán)控制,位移閉環(huán)控制沒有主缸活塞「滯留」問題,但也存在不足:如果位移控制指令由一較大目標值變?yōu)榱?,此時主缸活塞回位時由于運動慣性可能出現(xiàn)超調(diào),從而導致與殼體或其他部件撞擊,產(chǎn)生工作噪聲,并影響零件壽命。
還指出以主缸液壓力或主缸活塞推桿位移為控制變量的單控制變量控制系統(tǒng)面對系統(tǒng)參數(shù)變化和外界擾動時的魯棒性和適應性不高。為了提高系統(tǒng)性能,設計了以主缸液壓力和主缸活塞推桿位移為雙控制變量的控制系統(tǒng)。其中,采用位移控制器能夠快速建壓并消除「殘留液壓力」的問題;采用液壓控制器能夠確保目標壓力的精確跟蹤控制。
設計了以主缸液壓力和電動機電流為雙控制變量的控制系統(tǒng)。其中,電流環(huán)還有一個重要作用就是保持電動機電流在動態(tài)過程中不超過允許值。因而在突然施加控制作用時不希望有超調(diào)或超調(diào)量越小越好。而壓力環(huán)的作用是保證穩(wěn)態(tài)響應無靜差。
對于液壓驅(qū)動單元為「液壓泵+高壓蓄能器」形式的EHB系統(tǒng),控制變量只有主缸液壓力。另外,如所述的傳統(tǒng)EHB系統(tǒng),由于常規(guī)制動時主缸與輪缸之間的液壓回路被電磁閥斷開,而主缸液壓回路與踏板模擬器液壓回路連通,起模擬踏板感覺的作用,所以傳統(tǒng)EHB系統(tǒng)中不存在主缸液壓力控制問題。
2.2 控制算法
針對液壓驅(qū)動單元為「電動機+減速機構(gòu)」形式的EHB系統(tǒng)進行主缸液壓力控制,大多數(shù)的控制算法是閉環(huán)反饋控制。如ibooster 系統(tǒng)和e-ACT 系統(tǒng)采用液壓閉環(huán)反饋。這種控制算法的思路是將被控對象輸出的實際值與期望的目標值進行對比,然后將二者的偏差經(jīng)過控制器的處理后輸送給執(zhí)行器。而如何利用好二者偏差進行控制器的設計是這種控制算法設計的重中之重。
研究中多以PID控制算法對主缸液壓力進行反饋控制。在具體應用PID控制器時,需要對其控制參數(shù)進行整定,以產(chǎn)生適當?shù)妮敵隽縼砜刂齐妱訖C。提出一種集成式I-EHB液壓力分段比例一積分PI控制方法,利用基于系統(tǒng)改進的田口方法求出分段PI控制器的最優(yōu)控制參數(shù)。所設計的魯棒性液壓力控制方法魯棒性強,響應迅速,在500次試驗內(nèi)均保持穩(wěn)健。
為了在執(zhí)行機構(gòu)全工作范圍內(nèi)取得良好的液壓控制效果,采用基于增益調(diào)度的PI控制算法進行液壓力控制。以指令液壓為調(diào)度變量,液壓控制器在不同的局部控制器之間切換,局部控制器采用PI控制。
反饋控制按實際值和目標值的偏差進行調(diào)節(jié),而不需要考慮干擾類型。但是反饋控制存在信號傳遞周期長、實時性差的缺點。引入前饋和反饋控制的方法。前饋控制是基于不變性原理發(fā)展起來的一種特殊控制規(guī)律,能夠按擾動進行調(diào)節(jié),控制實時性強,但只能克服特定干擾,所以經(jīng)常與反饋控制一起使用。基于其開發(fā)的電子伺服制動系統(tǒng)ESB采用前饋和反饋控制算法對主缸液壓力進行控制,能夠?qū)崿F(xiàn)高精度的制動壓力控制,保持車輛實際減速度跟蹤恒定。將該系統(tǒng)應用于坡道停轉(zhuǎn)、自適應巡航和坡道起步等工況,試驗結(jié)果表明該系統(tǒng)的實時性更強,操縱性能得到明顯改善。
基于試驗分析了集成式電子液壓制動系統(tǒng)I-EHB的開環(huán)特性,發(fā)現(xiàn)系統(tǒng)增減壓時,主缸液壓力產(chǎn)生明顯的爬行現(xiàn)象,影響了系統(tǒng)的響應速度和精度,并指出是由于減速機構(gòu)存在較大的摩擦力引起的。當采用PID控制器對系統(tǒng)進行閉環(huán)控制時,發(fā)現(xiàn)在跟蹤目標液壓力的同時在目標值上下不斷振蕩,有可能會使系統(tǒng)失穩(wěn),而且跟蹤誤差較大。因此提出了利用顫振信號進行摩擦補償。摩擦爬行現(xiàn)象消失,系統(tǒng)的線性度提高。
將切換函數(shù)轉(zhuǎn)換成飽和函數(shù)來最大限度地削弱系統(tǒng)抖振,使控制器發(fā)揮最佳性能,并增強在多種工況下的適應性。LSP的IBS采用基于液壓模型預測的方法對目標主缸活塞推桿位移進行修正,結(jié)果表明相比于傳統(tǒng)EHB系統(tǒng),IBS的液壓波動明顯減小,有利于提高制動舒適性。
目前應用到基于雙控制變量的控制系統(tǒng)主要有兩種控制算法:切換控制和串級控制。切換控制是一種多個控制器并聯(lián),但同一時刻只有一個控制器在工作,在控制部分要有邏輯開關實現(xiàn)不同控制器的平滑切換。
設計了主缸活塞推桿位移一主缸液壓力切換控制器,并提出在保證系統(tǒng)穩(wěn)定的基礎上控制器設計的關鍵點在于兩種控制器的切換時機。
串級控制是一種串聯(lián)控制形式,能夠增強系統(tǒng)的魯棒性,但首先要考慮所設計的控制系統(tǒng)的穩(wěn)定性。其次,由于兩種控制器的各方面性能有所不同,需要協(xié)調(diào)一致,因此內(nèi)外環(huán)控制器不能獨立設計,需要根據(jù)控制器的性能要求同時設計內(nèi)外環(huán)控制器的參數(shù)。設計了內(nèi)環(huán)是位移環(huán)、外環(huán)是液壓環(huán)的串級控制器,并進行了控制系統(tǒng)穩(wěn)定性的分析。
采用抗回繞控制器,能夠保證系統(tǒng)平衡點全局漸近穩(wěn)定。
針對液壓驅(qū)動單元為「液壓泵+高壓蓄能器」形式的EHB系統(tǒng)進行主缸液壓力控制,
大多數(shù)采用反饋控制方法.
受高壓蓄能器重量、體積、安全性等因素影響,所述的EHB系統(tǒng)取消了高壓蓄能器,由電動機帶動柱塞泵直接提供高壓油。
通過將目標液壓和實際液壓的差值輸入PID控制器調(diào)節(jié)電動機的轉(zhuǎn)速,實現(xiàn)主缸液壓力跟蹤控制。
3. 輪缸液壓力控制
輪缸液壓力控制的工作原理是接收由上層算法(制動防抱死控制算法、車輛穩(wěn)定性控制算法、電液復合制動分配算法等)計算得到的輪缸目標壓力,根據(jù)當前車輪所處的實際工作位置,結(jié)合電磁閥的工作特性以及包含制動管路和制動輪缸在內(nèi)的EHB系統(tǒng)的壓力特性,得到電磁閥的實際控制指令。同時不斷監(jiān)測當前輪缸實際壓力和目標壓力,以便及時調(diào)整電磁閥的控制指令和工作狀態(tài),使輪缸實際壓力盡快地達到目標壓力。不涉及傳統(tǒng)EHB系統(tǒng)中電動機液壓泵的控制問題。
提出基于輪速反饋的液壓力控制方法,能夠補償車輛制動力輸出和車輛載荷擾動的變化量。
基于法規(guī)對制動系統(tǒng)的雙回路要求,設計了兩種液壓驅(qū)動單元的控制回路,并對比了單回路控制和雙回路控制的控制方法,試驗結(jié)果表明雙回路控制的控制效果更好。大多數(shù)是采用基于雙回路控制方法的輪缸液壓力控制。
國內(nèi)外多是以輪缸液壓力為控制變量設計控制系統(tǒng)。下表所示是以輪缸液壓力為控制變量的輪缸液壓力控制方案。
電子液壓制動系統(tǒng)輪缸液壓力控制方案
程序邏輯(if-else)控制器可根據(jù)輪缸壓力傳感器的反饋信號獲得輪缸的實際壓力,與目標壓力相比較,通過分別控制前后輪缸的進液閥和回液閥的開閉來對輪缸壓力進行調(diào)節(jié)。該控制系統(tǒng)相比于傳統(tǒng)制動系統(tǒng)的性能更好。
由于采用程序邏輯(if-else)使得輪缸實際壓力有較大波動,所以改用普遍使用、可靠性高的PID控制算法來設計輪缸壓力控制器。一般將輪缸目標制動壓力與輪缸實際制動壓力的差值作為PID控制器的輸入,通過試驗調(diào)節(jié)控制器的控制參數(shù),輸出為增減壓電磁閥的占空比控制信號,使輪缸實際壓力跟隨目標壓力。
由于汽車制動系統(tǒng)是一個復雜的非線性系統(tǒng),采用傳統(tǒng)PID控制算法進行輪缸壓力控制時,系統(tǒng)響應及穩(wěn)定性等并不理想,不能滿足制動系統(tǒng)的要求?;诖罅抗こ虒嵺`衍生出許多改進型PID控制方法,對控制系統(tǒng)的控制效果有較大改善。如進行控制器設計時,通過分段PID控制算法調(diào)節(jié)占空比來控制EHB系統(tǒng)中的高速開關閥,從而實現(xiàn)輪缸壓力的跟隨。由于用于對比例閥進行調(diào)節(jié)的PWM占空比和線圈電流近似呈線性關系,提出基于查表前饋的增量式PID控制算法,實現(xiàn)了對溢流閥線圈電流的精確控制,從而間接地調(diào)節(jié)輪缸壓力。由于EHB系統(tǒng)單片機性能的限制,采用遞歸PI控制方法控制輪缸液壓力,累積上一步輸出的電磁閥控制信號。
以上所涉及的PID控制器皆為定參數(shù),僅能夠在一定工況下或某些工作點處實現(xiàn)較好的控制效果。但其固定的控制參數(shù)對復雜路面和工況的適應性不高,所以設計了能夠在線調(diào)節(jié)參數(shù)的PID控制器,能夠改善控制效果。
由于EHB系統(tǒng)具有較強的非線性特性,采用模糊PID控制算法實現(xiàn)了EHB系統(tǒng)的輪缸液壓力控制,與傳統(tǒng)PID控制算法相比,模糊PID控制算法能夠準確地實現(xiàn)輪缸液壓力控制,但是建立壓力的快速性不如傳統(tǒng)PID控制算法。因此采用分段模糊PI控制算法對輪缸液壓力進行控制。僅當實際壓力與目標壓力偏差較小時,采用模糊PI控制算法來實現(xiàn)制動壓力的精確調(diào)節(jié);偏差較大時仍采用傳統(tǒng)PI控制算法。
對于不同壓力區(qū)間PI控制器的最優(yōu)參數(shù)選取也不同,將EHB系統(tǒng)的工作區(qū)間分為低、中、高壓,通過模糊邏輯求出最優(yōu)PI參數(shù)。然而模糊控制算法存在不連續(xù)性,會帶來控制信號的不連續(xù)等問題,從而影響控制系統(tǒng)的性能。因此增加自整定方法來調(diào)整控制器的控制參數(shù),但必須考慮控制參數(shù)的收斂性。利用模糊PI自整定算法對輪缸壓力進行控制。結(jié)果表明,模糊PI自整定算法在EHB系統(tǒng)的整個工作區(qū)間都具有良好的控制效果。
為了彌補反饋控制的不足,引入基于查表法的前饋控制算法采用前饋+反饋控制的算法,提高了輪缸液壓力控制系統(tǒng)的響應速度。
除了采用PID控制算法設計輪缸液壓力控制器外,還提供了另外一種思路:即采用數(shù)表插值法來進行輪缸液壓力控制,對數(shù)表插值法進行了改進。首先分析了輪缸制動間隙對壓力調(diào)節(jié)的影響,發(fā)現(xiàn)制動問隙使得制動初始階段制動力的上升過程存在遲滯現(xiàn)象,且輪缸壓力變化的非線性化趨勢明顯。然后提出一種分段控制的方法,即將目標壓力大于1.2MPa 的區(qū)間采用數(shù)表插值法計算占空比,而小于1.2MPa的區(qū)間采用階梯法來計算占空比。試驗結(jié)果表明,考慮了遲滯特性的分段階梯查表法比采用單一數(shù)表法進行輪缸壓力調(diào)節(jié)的控制精度有所提高。
輪詢調(diào)度算法作為一個經(jīng)典的調(diào)度算法由于其實現(xiàn)相對簡單,調(diào)度公平性比較好在計算機系統(tǒng)、網(wǎng)絡等方面有著廣泛應用。其工作原理如下:算法將控制器的處理時間分為時間片,分配給每一個進程。當被算法選中的進程進行完所分配的時間片后,無論該進程是否已經(jīng)完成所要求的任務,算法都會暫時停止該進程,同時調(diào)度當前隊列中的下一個進程。而被算法暫時停止的進程會被排到隊列的末尾,等待下一次調(diào)度的執(zhí)行。這樣就可以保證隊列中的所有進程在一個給定的時間段內(nèi)均能得到執(zhí)行,但會導致對優(yōu)先級高的進程響應不及時的問題。采用輪詢調(diào)度算法調(diào)節(jié)輪缸液壓力。試驗結(jié)果證明系統(tǒng)的響應時間和控制精度對于車輛應用的可行性,但是還有進一步優(yōu)化的空間。
Bang-Bang控制是一種非線性極值控制,其控制器的輸出只有最大和最小這兩種極限狀態(tài)。針對EHB系統(tǒng)的強非線性設計了Bang-Bang控制器來控制輪缸壓力。發(fā)現(xiàn)當存在系統(tǒng)內(nèi)部參數(shù)攝動和外界隨機干擾的情況下,Bang-Bang 控制系統(tǒng)的振蕩比較厲害,穩(wěn)定性較差。認為EHB系統(tǒng)實現(xiàn)對制動壓力的控制關鍵在于確定合適的PWM占空比。為了快速使實際壓力趨近于目標壓力,當實際壓力與目標壓力偏差較大時,采用Bang-Bang控制來調(diào)節(jié)占空比。
模糊控制算法可用來對輪缸壓力進行控制。實車測試表明,對于 25km/h以內(nèi)的速度信號跟蹤,實際車速變化量在2.5 km/h上下波動,即車內(nèi)乘員感受不到這一微小變化。但指出模糊控制系統(tǒng)在模型參數(shù)變化和外界隨機干擾的適應性不是很好,表現(xiàn)為系統(tǒng)響應超調(diào)量大,在保壓過程中出現(xiàn)大幅度的振蕩。
通過試驗發(fā)現(xiàn)若采用單一的Bang-Bang控制對EHB制動壓力進行跟蹤控制,輪缸的制動壓力會很快達到目標值,但制動壓力會在目標壓力附近反復波動,穩(wěn)態(tài)誤差較大:若采用模糊PI控制對EHB制動壓力進行跟蹤控制,輪缸制動壓力的響應曲線在超調(diào)量和穩(wěn)定性等方面都有較好的結(jié)果,但模糊PI的調(diào)節(jié)時間較長。為了使輪缸制動壓力能夠快速逼近目標壓力,同時還能使實際壓力精確地跟蹤目標壓力,設計了基于 Bang-Bang模糊PI控制算法的輪缸壓力控制器,能夠明顯改善系統(tǒng)性能。
采用魯棒 H∞ 控制算法設計了輪缸液壓力控制器,來提高系統(tǒng)的魯棒性,結(jié)果表明控制系統(tǒng)響應迅速、穩(wěn)態(tài)誤差較小,但是超調(diào)量較大、波動較劇烈。因此需要優(yōu)化魯棒控制器的設計,提高系統(tǒng)性能,減少超調(diào)量。遺傳算法是一種根據(jù)自然法則淘汰適應度差的解最后得到最優(yōu)解的方法。采用遺傳算法對魯棒控制器的權函數(shù)進行優(yōu)化。優(yōu)化后系統(tǒng)的超調(diào)量減少了約50%,超調(diào)后能迅速回到平衡狀態(tài),避免了波動和振蕩,而穩(wěn)態(tài)誤差和響應時間幾乎沒有變化。當控制系統(tǒng)在模型參數(shù)變化和外界隨機干擾的情況下,系統(tǒng)的超調(diào)量保持在較小值,整個過程比較平穩(wěn)。但是系統(tǒng)不確定性的存在,按照理想模型計算出的最優(yōu)解在實際工程中往往不能保持最優(yōu),有時甚至會引起控制品質(zhì)的嚴重下降。所以,工程中的控制系統(tǒng)不僅要「最優(yōu)」,還必須具有在不確定性影響下保持「最優(yōu)」的能力,即魯棒性和魯棒穩(wěn)定性。
鑒于EHB系統(tǒng)存在強非線性的特點,采用神經(jīng)網(wǎng)絡方法設計輪缸液壓力控制器,并提高控制系統(tǒng)的適應性。使用試驗獲得的數(shù)據(jù)樣本集對BP神經(jīng)網(wǎng)絡進行訓練,以目標增壓速率、輪缸壓力、閥前后壓差為輸入通過離線訓練完成的線性閥神經(jīng)網(wǎng)絡模型獲得控制電流,再通過反饋修正控制模塊確定控制信號的占空比。結(jié)果表明,系統(tǒng)各項性能均有顯著提高。
通過系統(tǒng)辨識獲得了EHB系統(tǒng)的預測模型,在廣義預測控制理論的基礎上設計了輪缸壓力控制器。結(jié)果表明,在系統(tǒng)參數(shù)時變的情況下應用該算法是有效的,并且該控制算法較一般的PID控制算法進一步提高了汽車的制動性能。在采用最小二乘法對模型參數(shù)進行辨識的基礎上,借鑒了多模型預測控制思想進行輪缸壓力控制器的設計,并指出模型參數(shù)變化對多模型控制器性能的影響不大。
自抗擾控制ADRC是一種不依賴系統(tǒng)模型的控制技術。它繼承了PID算法中基于誤差消除誤差的思路。不同之處在于,它能夠?qū)崟r估計并實時補償系統(tǒng)運行時受到的包括內(nèi)擾和外擾等各種干擾作用的總和,基于誤差反饋的非線性組合能夠?qū)崿F(xiàn)理想的控制性能。將自抗擾控制技術應用于EHB系統(tǒng)的輪缸液壓力控制,完成了自抗擾控制器設計和參數(shù)調(diào)整。實車試驗結(jié)果表明該系統(tǒng)能夠取得理想的控制效果。
液壓力控制算法的優(yōu)劣成為EHB系統(tǒng)能否實現(xiàn)精確快速液壓力調(diào)節(jié)的關鍵,也是能否與整車良好匹配的關鍵。
4. 電磁閥特性分析與控制
4.1開關閥
開關閥是通過主動控制電磁線圈產(chǎn)生的電磁力來開關閥口,其開關動作可以根據(jù)高低電平的互相轉(zhuǎn)換來實現(xiàn)?;陂y口開閉動作對EHB系統(tǒng)的開關閥進行控制,發(fā)現(xiàn)汽車低速行駛時能夠滿足駕駛需求。在對電磁閥的性能試驗研究的基礎上對在線控制的車身電子穩(wěn)定系統(tǒng)ESP的液壓模型和反模型進行了研究,由ESP上層車身姿態(tài)控制器優(yōu)化得到的預期壓力和當前輪缸實際壓力根據(jù)系統(tǒng)反模型求出各開關閥的開關指令。在研究原有ABS結(jié)構(gòu)的基礎上提出了一種新型可控主動EHB,利用電磁閥的開關控制實現(xiàn)了制動防抱死控制功能。
發(fā)現(xiàn)在對ABS和EHB的液壓力控制中使用開關控制存在很大缺陷,制動壓力波動與滑移率波動相互影響。制動壓力波動影響舒適性和輪胎磨損等問題;滑移率波動影響制動安全性和穩(wěn)定性。分析指出波動是由于電磁閥只有開、關兩種狀態(tài),實現(xiàn)流量的連續(xù)控制難度很大。
從閥芯的機械運動機理、電磁閥驅(qū)動電流變化和線圈磁通的關系等角度提出了電磁閥驅(qū)動電流的確定方法,能夠更精確地控制電磁閥的開關動作。
4.2 高速開關閥
通過控制高速開關閥的開啟頻率或開啟時問可以近似調(diào)節(jié)通過閥的流量,即采用不同寬度的脈沖信號來控制閥的開關,可以使通過閥的平均流量Q_AVG與占空比成正比 。設Qmax 為閥全開時的流量,則閥的平均流量為:
通過電磁閥的流量與脈沖寬度成正比,與調(diào)制周期成反比。因此存在兩種方式調(diào)節(jié)流量,一種是脈寬調(diào)制(PWM),調(diào)節(jié)脈沖寬度;一種是脈頻調(diào)制(PFM),調(diào)節(jié)調(diào)制周期。由于高速開關閥的臨界頻率有限,因此PWM方式更適合高速開關閥。在其提出的EHB上基于PWM方式控制高速開關閥,在基本制動工況、防抱死制動工況中進行試驗,結(jié)果表明能夠主動控制輪缸壓力。
近年來優(yōu)化了PWM控制方法。提出一種電磁閥控制方法,通過測量電磁線圈中的感應電流,確定閥芯的當前位置,與期望的閥芯位置進行對比,根據(jù)偏差確定PWM方式的占空比?;谄x度的概念采用PWM控制方法研究制動壓力增長速率對ABS控制效果的影響。通過制動試驗臺分析,使偏離度最小化的占空比能使制動壓力增長速率達到最優(yōu)。結(jié)果表明該方法顯著提高了ABS控制效果。
PWM脈沖的頻率和寬度的選擇對輪缸壓力的調(diào)節(jié)效果有重要影響。調(diào)制頻率一般在 10~100Hz。調(diào)整PWM控制的占空比,使閥芯的平均開度保持在設定值,從而控制輪缸壓力。在10~100Hz這一低頻范圍內(nèi)的PWM控制,通過高速開關閥的完全開和關,實現(xiàn)增壓.保壓的不斷循環(huán),從而減慢制動壓力的增長速度,防止車輪迅速抱死 。介紹了PWM控制參數(shù)中占空比的選擇和頻率的選擇對ESC液壓回路整體壓力建立的影響。利用硬件在環(huán)測試臺對ABS系統(tǒng)電磁閥的不同周期和占空比下的輪缸壓力平均增長速率進行了研究。結(jié)果發(fā)現(xiàn)低頻范圍內(nèi)PWM控制的缺點有:
壓力變化不是線性的,精確控制需要積累大量試驗數(shù)據(jù);
由于電磁閥是完全開閉,這就導致噪聲和液壓力波動的問題。
通過有效調(diào)節(jié)控制脈沖的頻率和寬度,高速開關閥能夠近似線性地控制流量瞵引。利用實際主缸壓力、實際輪缸壓力和目標輪缸壓力這三個壓力之間的關系計算線圈中的初始電流和電流變化量,實現(xiàn)利用高頻信號控制電磁閥。
高速開關閥的響應速度越快,對流量的控制就越精細和平穩(wěn)。對高速開關閥的控制機理進行詳細分析,得出結(jié)論:在確定高速開關閥PWM的控制參數(shù)時,應當綜合考慮控制信號的頻率、占空比與高速開關閥的響應速度以及線性工作區(qū)間之間的關系。控制信號頻率越低,對于具有確定開、閉響應時間的高速開關閥,其占空比工作范圍越寬,但控制效果越差。
但采用PWM控制電磁閥時,發(fā)現(xiàn)利用占空比對輪缸壓力變化速率進行調(diào)節(jié)的有效區(qū)間很小,所以需要采用其他電液比例控制方法。采用PWM控制進油閥、開關控制出油閥的方式對轎車穩(wěn)定性控制系統(tǒng)的輪缸壓力進行控制。發(fā)現(xiàn)對于減壓閥PWM控制時不同占空比下得到的減壓梯度過于接近,很難實現(xiàn)減壓精確調(diào)節(jié)。為了獲得理想的減壓速率,對減壓閥采用PFM方法進行控制,結(jié)果表明減壓速率隨頻率變化明顯,通過PFM方式能夠有效控制減壓速率。
4.3 線性閥
采用線性閥能夠獨立平滑地控制四個輪缸的液壓力,并實現(xiàn)基本制動功能和ABS、ESC、TCS 等功能,以及最大程度地回收制動能量。提出了新型的EHB 架構(gòu),其ESC采用4個比例伺服閥,實現(xiàn)了更快、更精確的液壓力控制,并縮小制動距離。指出,由于用于對比例閥進行調(diào)節(jié)的 PWM 占空比和線圈電流近似呈線性關系,故采用控制算法實現(xiàn)了對溢流閥線圈電流的精確控制,從而間接地調(diào)節(jié)輪缸壓力。
線性閥的結(jié)構(gòu)比開關閥更為精密,調(diào)節(jié)壓力變化速率時能夠控制閥芯懸停在一定位置,所以線性閥的控制方式與開關閥有本質(zhì)區(qū)別。由于電磁線圈通電后溫度上升,線圈電阻會發(fā)生改變,因此線圈電流和PWM控制占空比的關系發(fā)生變化,造成閥芯的懸停位置發(fā)生變化。為精確控制輪缸壓力,使閥芯位置能夠懸停在原位置,在控制線圈電流的過程中,需要考慮溫度對線圈電阻的影響。指出線性閥的控制主要分為兩部分:控制電流生成模塊和反饋修正控制模塊??刂齐娏魃赡K是根據(jù)當前輪缸壓力、目標壓力變化率和閥口兩端壓差通過一定的控制算法得到線性閥的控制電流。反饋修正控制模塊是根據(jù)目標控制電流、閥口兩端的電源電壓和當前線圈電阻值得到線性閥的PWM 控制占空比。
(3)耦合/解耦
線控制動系統(tǒng)可實現(xiàn)制動踏板與制動輪缸的解耦。
(4)踏板模擬
需要采用特定裝置來模擬制動踏板感覺,保證給駕駛員傳遞制動反饋信息。踏板模擬器作為關鍵部件之一,需要更真實地模擬傳統(tǒng)制動踏板特性,因為駕駛員在長期的制動操作中,已形成使用這種帶真空助力形式的制動踏板的習慣。傳統(tǒng)的制動系統(tǒng)中,駕駛員在踩踏制動時,能夠感受到真空助力器以及液壓系統(tǒng)的反饋, 整車在不同制動壓力的驅(qū)動下,建立起相應的減速度,給駕駛員建立起制動踏板感。踏板踩踏速度、踏板力、踏板行程以及對應壓力和減速度的建立都影響制動踏板感覺。傳統(tǒng)的制動踏板感覺是基于制動樣件選型來調(diào)整, 每個企業(yè)也都有基于樣件的踏板感覺DNA。目前制動踏板感覺評價, 主要是通過主觀評價評分和客觀數(shù)據(jù)測試兩種方式。
國內(nèi)外廠商和科研機構(gòu)對線控制動系統(tǒng)踏板模擬器進行了大量的分析研究,提出了多種類型的踏板模擬器設計思路,根據(jù)踏板力模擬方式可分為主動式和被動式。主動式踏板模擬器可以對踏板行程?踏板力特性進行實時調(diào)整,一般設計有獨立的信號反饋、控制系統(tǒng)及執(zhí)行機構(gòu),結(jié)構(gòu)復雜,多處于研究階段。設計的電子輔助制動系統(tǒng)進行了主動式踏板力補償分析,對踏板感覺進行了優(yōu)化;提出了一種踏板感覺可控的踏板模擬器,并通過實例仿真分析了踏板特性的影響參數(shù);設計了利用高壓蓄能器和氣體彈簧共同調(diào)節(jié)模擬器內(nèi)壓力的制動踏板感覺模擬器。提出了一種基于磁流變液可控流變特性阻尼可調(diào)的制動踏板感覺模擬器。被動式踏板模擬器踏板行程?踏板力特性多通過特殊的機械結(jié)構(gòu)實現(xiàn),一般不能實時調(diào)整和補償,結(jié)構(gòu)簡單易于實現(xiàn)。常見的形式有采用彈簧和橡膠體組合模擬傳統(tǒng)非線性踏板感覺,采用兩段或多段彈簧組合用分段線性模擬非線性踏板感覺,以及采用節(jié)流機構(gòu)利用非線性液阻模擬非線性踏板感覺等。
踏板模擬器系統(tǒng)中各部件參數(shù)均可對踏板感覺即踏板行程?踏板力特性產(chǎn)生影響。分析了制動主缸活塞摩擦特性對制動踏板感覺的影響;在制動踏板感覺試驗研究中,提出了影響制動踏板感覺的因素;設計了一種組合彈簧式踏板感覺模擬器,仿真分析了活塞阻尼系數(shù)、推桿回位彈簧預緊力、電磁閥最大通流面積和助力比等參數(shù)對踏板力?行程曲線的影響。以上研究多通過理論和仿真的方法驗證模擬器設計,或是結(jié)合仿真與試驗進行踏板感覺模擬影響因素分析,并未針對實際產(chǎn)品進行設計改進及驗證。特別地,將模擬器常閉電磁閥作為先導控制功能的閥控踏板模擬器研究未見報道。
BBW系統(tǒng)取消了踏板和主缸之間的機械連接,踏板力需要用通過模擬器或算法模擬的方式提供給駕駛員,踏板力模擬的好壞決定了BBW系統(tǒng)品質(zhì)的優(yōu)劣。目前主要的研究集中在實驗方法,一般是通過對大量的實驗數(shù)據(jù)進行分析歸納,得到踏板力與踏板行程和車輛狀態(tài)之間的關系,通過彈簧或作動器對踏板力進行模擬。 線控制動踏板感覺從基于樣件調(diào)整到從零開始設計模擬。完全的設計模擬,可調(diào)整范圍就相對寬泛,不會受限于樣件選型,可以靈活設計調(diào)整踏板感覺曲線。一方面可以去模擬傳統(tǒng)制動系統(tǒng)的踏板感覺, 另一方面也可以讓消費者適應新的踏板感覺。甚至可以將制動踏板和油門踏板集成, 完全通過電子化的設計以及能量回收的配合來建立新的踏板感覺。是否需要沿用傳統(tǒng)車的制動踏板感覺標準和開發(fā)模式,這是線控制動的全新選擇。
線控制動系統(tǒng)踏板感覺模擬器設計與改進
設計開發(fā)一種線控制動(EHB)系統(tǒng)樣機,選取不同過流孔徑的踏板模擬器常閉電磁閥進行踏板行程?踏板力對比試驗. 結(jié)果表明:當將單個電磁閥直接接入踏板感覺模擬器回路時,隨著制動力加載速度的提高,會產(chǎn)生實際制動踏板行程?踏板力關系曲線偏離目標曲線的問題,并且電磁閥孔徑越小,偏離越大,借助于數(shù)學推導得出電磁閥過流孔徑與踏板速度響應之間的理論關系。設計一種液壓先導閥加入到踏板模擬器回路中,以提高系統(tǒng)通流能力和踏板速度響應,液壓先導閥由原回路中的電磁閥控制。對改進的踏板模擬器回路進行仿真及試驗,結(jié)果均表明:改進過的回路可較好地實現(xiàn)踏板行程?踏板力曲線精度,曲線受踏板力加載速度變化影響小,同時可使模擬器常閉電磁閥工作功耗更低,提高了系統(tǒng)的可靠性.
自行設計的一種線控制動系統(tǒng)樣機進行踏板行程?踏板力特性試驗分析,針對因模擬器常閉電磁閥過流孔徑偏小而造成的踏板行程? 踏板力曲線隨踏板速度偏移的問題,提出一種改進設計方案并通過仿真及試驗驗證其可行性.
1 制動系統(tǒng)踏板力特性分析
1.1 傳統(tǒng)制動系統(tǒng)踏板力特性
傳統(tǒng)液壓制動系統(tǒng)踏板行程與踏板力的關系曲線如下圖所示,圖中S為踏板行程,F(xiàn)為踏板力.a-b段:主要消除踏板的自由行程,踏板位移較大,踏板壓力沒有明顯增加;b-c段:真空助力裝置起作用,踏板壓力隨踏板位移增加而變大;c-d段:真空助力比達到最大值并恒定,踏板壓力隨踏板位移變化較大. 在實際制動過程中,中小強度制動時,達到最大制動壓力所需的踏板位移較大,即特性曲線斜率較小,踏板壓力隨踏板位移變化均勻,制動穩(wěn)定舒適;緊急制動時,達到最大制動壓力所需的踏板位移較小,即特性曲線斜率較大,踏板壓力隨踏板位移變化急劇增加,制動響應迅速.
傳統(tǒng)液壓制動系統(tǒng)踏板行程?力特性曲線
Pedal stroke-force curve of traditional hydraulic brake system
1.2 線控制動系統(tǒng)踏板感覺模擬器設計
設計開發(fā)一種線控制動系統(tǒng)(wire brake system,WBS)踏板感覺模擬器,原理如圖 2 所示.
常規(guī)制動工況下,駕駛員踩下制動踏板,控制器通過讀取踏板角度信號確認車輛制動需求,常開型制動主缸隔離電磁閥上電關閉,模擬器常閉電磁閥上電打開,制動主缸油液通過模擬器常閉電磁閥進入模擬器主缸,并由制動主缸和模擬器主缸共同作用反饋合適的制動腳感. 線控制動系統(tǒng)的制動力源由電動柱塞泵提供,并由高壓蓄能器儲壓,以減少油泵工作次數(shù)并提高系統(tǒng)壓力速度響應. 控制器通過判斷踏板角度傳感器等信號,控制電磁閥開度及柱塞泵工作,按照控制邏輯控制線控制動系統(tǒng)輸出相應制動力,此時制動踏板和制動力是完全解耦的;如果線控制動系統(tǒng)發(fā)生故障,進入備用制動狀態(tài),控制器控制制動主缸隔離電磁閥斷電打開,模擬器常閉電磁閥斷電關閉,模擬器停止工作. 此時制動油液通過制動主缸和制動主缸隔離電磁閥直接進入備用制動回路,提供車輛備用制動力。
如圖 2 所示,在模擬器主缸中設置 2 段彈簧,分別模擬圖 1 中b-c段和c-d段的踏板力特性. 不考慮空行程及制動過程中流體壓力損失,制動主缸活塞及模擬器主缸活塞運動方程滿足:
2 試驗分析與改進設計
2.1 試驗條件及主要參數(shù)
試驗在萬向 WBS 試驗臺架上展開,不考慮油溫變化導致的油液黏度變化(室溫條件下進行),臺架測試原理如圖 4 所示.
測試方法:模擬器常閉電磁閥通電,踏板力加載速率 15~25 N/s.
記錄數(shù)據(jù):記錄踏板轉(zhuǎn)角傳感器數(shù)據(jù)、踏板力傳感器數(shù)據(jù),每組試驗記錄 3 次.
由于空間布置、功率、發(fā)熱量等實際要求,模
2.2 試驗結(jié)果分析
2.2.1 踏板力加載速度為 15 N/s 的試驗結(jié)果試驗中踏板力加載速度為 15 N/s,試驗結(jié)果如圖 5 所示. 試驗中裝配過流孔徑分別為Φ0.7、Φ1.0 mm 模擬器常閉電磁閥的樣機第一段彈簧曲線均出現(xiàn)了偏移,踏板力偏大;而直接短接開閉電磁閥通路(孔徑Φ2.8 mm)與目標值貼近較好;裝配Φ0.7 mm 孔徑開閉電磁閥的樣機曲線在第一段出現(xiàn)了明顯了非線性特征。
2.2.2 踏板力加載速度為 25 N/s 的試驗結(jié)果試驗中踏板力加載速度為 15 N/s,試驗結(jié)果如圖 6 所示. 隨著踏板加載速度加快:裝配過流孔徑分別為Φ0.7、Φ1.0 mm 模擬器常閉電磁閥的樣機第一段彈簧曲線偏移和非線性特性愈加明顯,并且隨著電磁閥過流孔徑變小,偏移量和非線性化愈加明顯;直接短接開閉電磁閥通路(孔徑Φ2.8 mm)與目標值貼近較好,受踏板力加載速度影響小.
試驗結(jié)果表明:模擬器常閉電磁閥過流孔徑參數(shù)對踏板模擬器S-F試驗結(jié)果影響顯著,隨著制動力加載速度提高,其液壓阻尼力變大,踏板感變硬,影響制動舒適性;在緊急制動時,踏板不能及時踩下,導致控制器接收到的制動力請求不足,極大影響行車安全性.
2.2.3 踏板特性影響因素理論分析由試驗分析可知,當前模擬器開閉電磁閥過流孔所產(chǎn)生的液壓損失不能忽略,應考慮過流孔徑影響,建立如圖 7 所示的踏板模擬器簡化分析液路圖.
考慮管徑突變及小孔節(jié)流產(chǎn)生的壓力損失,根據(jù)伯努利定理和流量連續(xù)性方程,制動主缸油壓pc與模擬器主缸油壓ps的壓力損失關系為
式中:ρ為制動液密度,Dt為模擬器常閉電磁閥前管路內(nèi)徑,Cv為模擬器常閉電磁閥流量系數(shù),Dv為模擬器常閉電磁閥阻尼孔直徑,Dn為模擬器常閉電磁閥后管路內(nèi)徑,ke為Dt負相關系數(shù),ke'為Dn負相關系數(shù).
將當前設計參數(shù)代入式(4),并根據(jù)試驗結(jié)果確定常量C的取值,用作圖法可得到電磁閥阻尼孔徑對踏板速度響應的影響曲線,如圖 8 所示. 為提高踏板感模擬曲線精度,應提高實際系統(tǒng)到達理論無阻尼踏板速度的響應時間. 從圖中可以看出,模擬器電磁閥阻尼孔徑對速度響應具有高階影響系數(shù),增大電磁閥的阻尼孔徑,即提高其過流面積,能顯著提高踏板速度響應.
2.3 改進設計及仿真分析
2.3.1 改進方案設計
重新開發(fā)的滿足要求的大過流孔徑電磁閥理論上可消除上述試驗問題. 但考慮到電磁閥產(chǎn)品開發(fā)周期較長,性能及可靠性短期內(nèi)難以完成驗證,同時需要與控制器、閥體重新匹配,是一個系統(tǒng)性問題,因此,考慮將當前電磁閥作為先導控制閥使用,充分利用當前開發(fā)成果。改進設計方案原理如圖9和10所示。
常規(guī)制動工況:模擬器常閉電磁閥通電打開,踩下制動踏板后制動油液通過電磁閥進入液控開閉閥控制口,油液首先通過回流排氣孔進入模擬器主缸排氣并推動模擬器主缸形成初始踏板力,當制動踏板力繼續(xù)加大足以克服液控開關閥彈簧回復力時,主閥芯閥口打開,制動油液進入模擬器主缸. 松開踏板后,制動油液可通過主閥芯閥口和回流排氣孔回制動主缸. 特別地,當踏板力超過一定小行程(足以克服液控開閉閥彈簧回復力打開主閥口)時,可關閉模擬器開閉電磁閥,因出油口壓力與液控開關閥控制口連通,仍然能保證主閥口打開,這可在實際中降低模擬器開閉電磁閥通電
工作時間,有利于控制電磁閥發(fā)熱量并提高可靠性.
2.3.2仿真分析優(yōu)化
建立原設計及改進設計仿真模型如圖 11 所示. 根據(jù)空間布置限制及工程設計經(jīng)驗確定液控開閉閥通徑為Φ10 mm。
踏板模擬原設計仿真模型踏板行程-踏板力仿真結(jié)果如圖12所示。模型中模擬器常閉電磁閥過流孔徑選定為Φ1.0mm. 仿真結(jié)果表明:踏板力加載速度越快,曲線非線性特性越明顯,這主要是由于電磁閥過流孔徑過小,與之前試驗結(jié)果趨勢相同。如圖 13所示為
所設計的液控開閉閥主閥口初始密封量對踏板加載S-F特性曲線的影響:初始密封量過大會造成初段踏板力變大,并引起S-F特性曲線前段突變;如圖14所示為回流排氣孔徑對踏板回程(踏板力為 0)踏板行程的影響:在踏板回程后段,回流排氣孔徑過小,會造成后段踏板回程不夠順滑,但基本不影響踏板回程速度。
同時利用 AMEsim-Optimus 優(yōu)化模塊對所設計的液控開關閥進行參數(shù)尋優(yōu),并根據(jù)工程實際設定取值范圍. 優(yōu)化后該閥回復彈簧剛度選定為 0.3N/mm,預緊力為 0.3 N,回流排氣孔直徑為Φ2.8 mm。
對參數(shù)優(yōu)化后的改進仿真模型施加相同的踏板力,仿真結(jié)果曲線如圖 15 所示. 仿真結(jié)果表明:改進設計仿真結(jié)果與目標曲線吻合度良好,受踏板力加載速度影響小,這主要是因為液控開閉閥有較強的通流能力,并可根據(jù)踏板力大小調(diào)節(jié)主閥口開度. 改進設計相比原設計,在不同踏板力加載時間下,踏板速度響應均有明顯改善,如圖 16 所示. 在踏板改進設計仿真模型中施加如圖 17 所示周期性踏板力,sole 表示電磁閥的開閉狀態(tài):0 表示斷電,1 表示通電. 在 A 段周期內(nèi),模擬器常閉電磁閥上電
打開,踏板模擬器正常工作;在 B 段周期內(nèi),模擬器常閉電磁閥斷電關閉,模擬器停止工作,踏板僅輸出固定空行程;在 C 段周期內(nèi),模擬器常閉電磁閥在前 1 s 內(nèi)上電打開后關閉,踏板模擬器可依然保持正常工作. 這一特性可縮短開閉電磁閥工作時間,從而降低電磁閥負荷及發(fā)熱量,提高了系統(tǒng)可靠性.
3 改進方案試驗驗證
對采用改進方案設計的線控制動系統(tǒng)樣機進行實車試驗測試,試驗情況如圖 18、19 所示. 試驗結(jié)果表明,該優(yōu)化設計較好地實現(xiàn)了踏板行程? 踏板力特性曲線跟隨.
改進前、后的踏板模擬器踏板行程?力特性進行了記錄和對比如表 1 和 2 所示. 表中:Fori為改進前對應踏板位置的踏板力,F(xiàn)imp為為改進后對應踏板位置的踏板力,Eori為改進前對應踏板位置的踏板力誤差或誤差百分比,Eimp改進后對應踏板位置的踏板力誤差或誤差百分比,Rori為改進前對應踏板位置的踏板力評價結(jié)果,Rimp為改進后對應踏板位置的踏板力評價結(jié)果:NG 為不合格,OK 為合格.
(5)主動制動
上層策略根據(jù)當前車輛狀態(tài)和駕駛員操作,向BBW系統(tǒng)發(fā)出制動請求,BBW系統(tǒng)則需要準確、快速地響應這個請求。主動制動旨在提高車輛的穩(wěn)定性和安全性,高級駕駛輔助系統(tǒng)(ADAS)、緊急制動系統(tǒng) (AEB)及自動駕駛等都使用到了這一功能。目前,所有關于主動制動的研究基本分為基于經(jīng)驗設計的方法和基于動力學模型計算的方法。幾乎所有常見的控制算法都可以其中找到應用,如PID算法、最優(yōu)控制、魯棒控制、滑??刂啤⒛:刂?、神經(jīng)網(wǎng)絡控制、模型預測控制。
(6)制動能量回收
傳統(tǒng)燃油車的制動系統(tǒng)由制動踏板、真空助力部件(EVP)和防滑控制部件(ESP、ABS)等組成,沒有制動能量回收功能,如果在電動汽車上使用會浪費掉大量的制動能量。線控制動系統(tǒng)(E-Booster)利用線控制動系統(tǒng)控制器和線控制動系統(tǒng)執(zhí)行器(主要是伺服電機系統(tǒng))代替了真空助力部件,將有效地解決傳統(tǒng)制動系統(tǒng)制動能量無法回收的痛點。
純電動汽車或混合動力汽車在回饋制動過程中,主缸制動液暫時儲存在蓄能器內(nèi),此時液壓制動不介入,控制器根據(jù)踏板行程信號向電機發(fā)送相應的制動扭矩請求,實現(xiàn)主缸與輪缸的解耦,利用電機制動實現(xiàn)能量回收。若再生制動力不足以產(chǎn)生駕駛員所期望的制動減速度,低壓蓄能器內(nèi)的液壓制動液將被推至制動輪缸內(nèi),此時系統(tǒng)工作于機電復合制動模式,并在整個制動過程中傳遞一致的制動踏板感覺,實現(xiàn)制動力的深度解耦。為了保證回收效率,將對電機制動與機械制動力矩進行解耦,實現(xiàn)機電復合制動的雙向協(xié)調(diào)控制,如下圖所示。
制動能量回收控制原理
從功能上看,電動汽車要實現(xiàn)制動能量回收,制動系統(tǒng)須由電動機回饋制動和另一種制動形式共同作用。由于電動機制動的特性以及回收能量最大化的需求,液壓制動系統(tǒng)的制動力必須實時可調(diào)。
與制動力通過液壓制動力及回饋制動力協(xié)調(diào)控統(tǒng)制動系統(tǒng)相比,線控制動系統(tǒng)取消了真空助力制動,可滿足電動汽車及混合動力汽車的再生制動器,具有結(jié)構(gòu)簡單、制動響應快、控制精度高等系統(tǒng)需求,具有很好的發(fā)展前景。
因此線控制動是必然的發(fā)展方向。
制動能量回收系統(tǒng)的協(xié)調(diào)分配電制動力矩和制動力矩是關鍵技術之一,控制策略的研究基本圍繞這一點展開。
在駕駛員制動時,線控制動系統(tǒng)控制器依據(jù)動力總成的工作狀態(tài)和駕駛員的制動需求控制電機實施電制動,電機制動力不足部分通過液壓制動進行補充。 制動過程中踏板行程模擬器會將踏板力和輪缸壓力進行解耦,使電機電制動部分的能量得到回收,提升整車的續(xù)航能力,還改善了駕駛員制動過程的舒適性。此外,線控制動系統(tǒng)通過其控制器與智能駕駛(ADAS)零件進行交互,可以實現(xiàn)響應智能駕駛部件的制動需求。
(7)制動控制
是自動駕駛執(zhí)行系統(tǒng)的重要部分,目前ADAS與制動系統(tǒng)高度關聯(lián)的功能模塊包括ESP(車身穩(wěn)定系統(tǒng))/AP(自動泊車)/ACC(自適應巡航)/AEB(自動緊急制動)等。電動汽車上與線控制動系統(tǒng)直接關聯(lián)的零件有整車控制器(VCU)、電機控制器(MCU)、智能駕駛部件(ADAS)和防滑控制部件(ABS、ESC)等。
線控制動系統(tǒng)與各個模塊的高度關聯(lián)
(8)線控制動功能安全
2.3. 安全冗余
是永恒的發(fā)展任務,電信號傳遞更快、更可拓展,但是不如機械連接穩(wěn)定。制動系統(tǒng)和自動駕駛對線控制動提出了兩個層次的冗余要求:
1)制動系統(tǒng)本身必須具備可靠的安全失效模式。在L3+級別自動駕駛尚未放量的當下,線控制動需求來源主要是新能源車型,安全穩(wěn)定才是剎車系統(tǒng)的第一要務。EHB采用可靠的機械備份,即車載電源失效時啟用純液壓助力,這也是EHB容易被市場接受的關鍵因素。
2)自動駕駛必須具備電子冗余,不能單純依靠機械冗余,否則要求駕駛員在段時間內(nèi)接管車輛就會陷入責任劃分的泥潭。因此,自動駕駛車型使用線控制動至少需要電子冗余+機械冗余的雙安全失效模式才能滿足法規(guī)要求。ESP并非可靠的安全失效模式,本田CR-V發(fā)生過ibooster和ESP同時故障的案例。博世最新一代IPB新增RBU冗余制動單元、伯特利WCBS+雙控EPB則是對應L3+級別自動駕駛的電子冗余方案。
高可靠性實時容錯控制系統(tǒng)結(jié)構(gòu)設計
BBW系統(tǒng)的應用一直受到安全可靠性的較大影響, 因為任何一個電子信號的失效都可能會帶來一個災難性的后果, 而且在BBW系統(tǒng)之中, 不再擁有獨立的備用制動系統(tǒng), 這就對其設計的安全性有了更高的要求, 使其必須安全、實用并且是可維護的。雖然可以通過可靠性分析、事件樹分析、故障樹分析、危險分析等方法提高BBW系統(tǒng)在設計階段的安全性, 并且通過有效的質(zhì)量控制手段保證生產(chǎn)質(zhì)量, 但是還是不能有效的防止某些故障的出現(xiàn)。
因此為了保證系統(tǒng)的安全性, 需要提升系統(tǒng)的容錯功能, 最合適的辦法就是對系統(tǒng)的元件、單元和子系統(tǒng), 甚至是軟件進行冗余設計, 通過這樣的方式能夠是實現(xiàn)有效的系統(tǒng)容錯結(jié)構(gòu)設計, 提高系統(tǒng)的安全可靠性, 但是同時也會提高系統(tǒng)的成本, 因此設計時實現(xiàn)高安全性、成本、空間和重量等多方面因素的均衡。 (9)車載網(wǎng)絡通訊技術 BBW系統(tǒng)是一個安全關鍵性分布式實時控制系統(tǒng), 對于安全性和可靠性有著非常高的要求, 因此要求車載網(wǎng)絡協(xié)議必須要具備高速率、可靠和支持容錯等方面的性能, 而且消息的傳輸時間的實時和確定性也是其必備的條件, 只有這樣才能夠準確的完成實時性要求很高的控制任務, 諸如嚴格時序和參數(shù)定時刷新等,線控系統(tǒng)對車載通訊網(wǎng)絡提出了新的性能需求。針對這樣要求, 需要進行嵌入式實時控制系統(tǒng)的網(wǎng)絡設計。嵌入式實時控制系統(tǒng)存在兩種模式, 分別是事件觸發(fā)和實踐觸發(fā),目前基于事件觸發(fā)的總線系統(tǒng)將會不能滿足新的需求,尤其是系統(tǒng)對通信的高速率、可靠性、容錯支持以及滿足消息傳輸實時和確定性的要求。當前的研究結(jié)果表明, 基于時間觸發(fā)的確定性通信網(wǎng)絡協(xié)議在安全關鍵性實時控制方面的應用更具優(yōu)勢?;跁r間觸發(fā)的確定性的通信網(wǎng)絡協(xié)議是滿足安全關鍵性實時控制的最佳選擇。目前有TTCAN,Byteflight,F(xiàn)lexRay,TTP/C 等通信網(wǎng)絡標準。在BBW系統(tǒng)中應用最多的是 FlexRay,TTP/C 兩個網(wǎng)絡協(xié)議。TTP/C 是專門為安全關鍵實時控制系統(tǒng)而設計的通信協(xié)議,基于TDMA (Time Division MultipleAccess)的訪問方式,能夠支持多種容錯策略,提供容錯的時間同步以及廣泛的錯誤檢測機制。FlexRay是專為車內(nèi)局域網(wǎng)設計的一種具備故障容錯的高速車載總線系統(tǒng),基于時間觸發(fā)的機制,具有高帶寬、容錯性好等特點,在實時性、可靠性以及靈活性等方面優(yōu)勢明顯。FlexRay有兩個信道, 最高速率都可以達到10Mbps,能更好的實現(xiàn)冗余,使得消息具有容錯能力。Flex Ray協(xié)議具備同步時基、確定性、容錯等特性。 目前看,車載通信網(wǎng)絡技術的應用商業(yè)化還在雛形,CAN通信仍占主導。但是隨著智能汽車的發(fā)展,車載通訊網(wǎng)絡的變革也將很快出現(xiàn)。 (10) 傳感器技術 制動系統(tǒng)傳感器如踏板力、行程、扭矩、溫度、 電機轉(zhuǎn)角位移等傳感器, 這些傳感器對制動系統(tǒng)的控制執(zhí)行有著至關重要的作用。傳感器不僅包含制動系統(tǒng)傳感器,同時還包括整車速度,轉(zhuǎn)速以環(huán)境感知傳感器。 未來的制動系統(tǒng)一定是智能主動制動系統(tǒng),能夠依據(jù)精確、 分辨率高傳感器信息來感知、 控制決策、動態(tài)執(zhí)行。因此成本低、可靠性好、精度高、體積小的傳感器是發(fā)展線控制動系統(tǒng)的關鍵技術之一。多功能化、智能化、集成化的傳感器并和計算機芯片集成是未來發(fā)展趨勢。 (11)車用電源系統(tǒng)
BBW制動系統(tǒng)對于電源得需求較傳統(tǒng)制動系統(tǒng)較高, 需要42V的驅(qū)動力才能夠滿足驅(qū)動力要求, 有效的預防緊急制動情況下出現(xiàn)電量不足的問題;而且42V電源通過進行良好絕緣處理, 能夠有效的防止出現(xiàn)線路接觸不良的問題, 有效的提高控制系統(tǒng)的安全性。
智能汽車線控制動系統(tǒng)開發(fā)
在TBS和ESC協(xié)調(diào)控制下,TBooster保證踏板感,而ESC將進行液量分配與制動力的分配,同時展示了協(xié)同控制系統(tǒng)邏輯圖。
面向下一代智能汽車的線控制動系統(tǒng)解決方案:T-Booster與ESC深度耦合制動系統(tǒng)
-1.T-Booster系統(tǒng)
為此研發(fā)了一款不依賴于真空源的主被動一體化電動助力制動系統(tǒng)(T-Booster),為新能源汽車、ADAS、自動駕駛技術等提供模塊化、可擴展的制動系統(tǒng)解決方案,其外觀如下圖所示。
T-Booster三維模型
T-Booster利用電機及傳動機構(gòu)代替真空助力器來實現(xiàn)制動助力功能,通過電機來推動制動主缸活塞,可迅速建立所需的制動壓力并對其進行精確調(diào)節(jié),實現(xiàn)主動制動功能。與典型的ESC系統(tǒng)相比,T-Booster建立制動壓力的速度更快,系統(tǒng)工作壽命更長,滿足連續(xù)下長坡等需要制動系統(tǒng)長時間工作的工況。
1.1電動助力性能
下圖為人工駕駛的緊急制動工況下主缸液壓的響應特性及制動推桿的行程曲線,在主缸內(nèi)建立10MPa壓力耗時150ms。
主缸壓力-推桿行程曲線
下圖為不同助力比對應的主缸壓力—踏板力特性,可根據(jù)不同車型及駕駛員主觀意愿調(diào)整助力比,以調(diào)整制動踏板腳感。
T-Booster助力特性
T-Booster可以通過助力控制提供接近于真空助力制動系統(tǒng)的踏板感覺,下圖為與原車真空助力制動系統(tǒng)的對比。
主缸壓力-踏板力曲線
主缸壓力-推桿行程曲線
1.2主動制動性能
T-Booster的瞬態(tài)響應特性影響著車輛的制動安全性能,下圖為T-Booster主動增壓的制動主缸壓力響應曲線。主缸壓力從0建立至10MPa所需要的時間大約為0.2s,壓力穩(wěn)態(tài)跟蹤誤差小于0.1MPa。
主缸壓力階躍信號響應曲線
主缸壓力階梯信號響應曲線
1.3線控制動性能
T-Booster控制器接收目標主缸壓力后,解算并發(fā)送電機控制命令,實現(xiàn)目標制動壓力的跟隨控制。下圖為線控制動過程中的推桿行程獲取以及制動壓力的跟隨控制效果。在整個制動過程中,主缸實際壓力始終較好的跟隨理想制動壓力變化。
推桿行程估計
制動壓力跟隨控制
-2T-Booster與ESC耦合制動系統(tǒng)
2.1耦合制動系統(tǒng)
T-Booster與ESC深度耦合的線控制動系統(tǒng)具備更高的響應速度和控制精度,匹配費用與博世相比大幅下降。當T-Booster系統(tǒng)發(fā)生故障或車載電源不能滿負載運行時,ESC系統(tǒng)可以迅速提供制動實現(xiàn)第一道安全失效備份;當車載電源失效時,T-Booster系統(tǒng)依然可以通過純機械方式建立制動壓力,實現(xiàn)第二道安全失效備份。
下圖為耦合制動系統(tǒng)的結(jié)構(gòu)圖,T-Booster可以單獨實現(xiàn)電動助力制動及主動制動功能,T-Booster和ESC結(jié)合可以實現(xiàn)線控制動、制動能量回收及雙安全備份制動功能。
T-Booster與ESC耦合制動系統(tǒng)結(jié)構(gòu)圖
2.2制動能量回收
下圖為T-Booster與ESC耦合制動系統(tǒng)制動能量回收試驗曲線。圖中紫色線是踏板力,當踏板力較小時,單獨由電機進行回饋制動。當踏板力大于一定程度時,表示駕駛員期望制動力矩較大,電機再生制動力矩無法滿足需求,此時液壓制動介入。
制動能量回收試驗曲線
六、分類
由于技術發(fā)展程度的局限,目前出現(xiàn)的線控制動系統(tǒng)是電子制動系統(tǒng),根據(jù)乘用車線控制動系統(tǒng)的實現(xiàn)形式不同,根據(jù)實現(xiàn)的難易程度分成了兩條技術路線,目前線控制動系統(tǒng)可分為電子液壓制動EHB系統(tǒng)和電子機械制動EMB系統(tǒng)兩類。
(1)電子液壓制動系統(tǒng)EHB
1)EHB從結(jié)構(gòu)上分:
整體式:總泵踏板單元、主動增壓模塊、壓力調(diào)節(jié)模塊集成在一個部件內(nèi)。
分體式:總泵踏板單元和主動增壓模塊集成在一個模塊中,分泵壓力調(diào)節(jié)作為另一個單獨模塊。
2)EHB系統(tǒng)目前主要有兩種:一種由液壓泵和高壓蓄能器提供動力源(P-EHB),P-EHB系統(tǒng)ECU獲取制動信號后,向電動液壓泵發(fā)出相應的電信號,將足夠的制動液泵入高壓蓄能器,利用高速開關閥實現(xiàn)車輛的制動;另一種由電機和減速機構(gòu)為動力源(I-EHB),同時集成電控模塊。I-EHB系統(tǒng)主缸液壓力由電機通過減速機構(gòu)提供,電機接收來自控制器的制動信號,經(jīng)過減速機構(gòu)直接推動主缸活塞對制動主缸進行建壓。相較于P-EHB,I-EHB結(jié)構(gòu)更加緊湊、響應快速,更易于集成諸如EPB、ESP等多種主動安全功能,解耦單元使得整套系統(tǒng)靈活制定制動方案,不僅節(jié)約了成本,更可縮短車輛的開發(fā)周期。
3)三種典型的EHB系統(tǒng),第一個是博世的SBC系統(tǒng),它是一個最典型的EHB系統(tǒng),常規(guī)制動時備用閥打開,通過控制增壓泵與減壓閥的通斷狀態(tài)來完成輪缸制動液的增壓和卸壓工作。常規(guī)制動失效后,控制器會打開備用閥,啟用備用的制動系統(tǒng),通過踩踏制動踏板,可以對兩前輪進行制動;第二個是豐田的ECB系統(tǒng),整體結(jié)構(gòu)上原理上跟SBC是類似的,應該說所有的EHB系統(tǒng)基本上原理都是類似的,但是豐田這里有一種全新的設計,因為前制動器的缸徑一般都比后制動器的缸徑大,那么它在制動完成之后,液壓開始降壓回流的時候,這時前輪回油管路油的流速和后輪的流速是不一樣的,兩個回油管路的結(jié)合處,因為流速的不一樣,豐田認為會產(chǎn)生一種脈沖,這種脈沖會隨著后制動器的回油管路逐漸傳遞,造成很大的噪音?;谶@個考慮,在后制動器回油管路上增加一個脈沖的抑制裝置,叫做阻尼設備;第三個是清華大學的DEHB系統(tǒng),這個系統(tǒng)主要針對分布式驅(qū)動,主要有一個全新的設計,增加了一個保壓閥的設計,在每個輪缸的管路上都增加了保壓閥,達到一定的壓力之后,它可以保持這個壓力,這個時候電機就不用持續(xù)工作了,可以減少電機的工作負荷。
4)按照踏板的解耦形式又可以分為全解偶和半解耦方式。
5)目前EHB有著不同的實現(xiàn)形式,按照ESC、ABS系統(tǒng)等功能是否和電子助力器集成的一體化形式,分為 One-Box形式和Two-Box兩種技術類型。One-Box為EHB集成了ABS/ESP,只有一個ECU,新一代IPB則為one-box方案;而Two-Box需要協(xié)調(diào)EHB ECU和ESP ECU的關系。以two-box方案的ibooster為例,必須和ESP hev配合才能與踏板解耦,采用協(xié)調(diào)式能量回收策略。
6)EHB根據(jù)技術方向還分為三類:
①電動伺服:電機驅(qū)動主缸提供制動液壓力源,代表產(chǎn)品Bosch Ibooster, NSK
②電液伺服:采用電機+泵提供制動壓力源,代表產(chǎn)品Continental MK C1, 日立
③電機+高壓蓄能器電液伺服:ADVICS ECB
以上關鍵部件包括:電機、電磁閥、油泵、電液控制單元、蓄能器,這些部件集成在一起,形成了機電液集成程度非常高的EHB產(chǎn)品。
(2)電子機械制動系統(tǒng)EMB
1)電子機械制動器按其結(jié)構(gòu)特點和工作原理可以分為無自增力制動器、自增力制動器兩大類。
①無自增力制動器:
電動機通過減速增矩的機械執(zhí)行機構(gòu)產(chǎn)生夾緊力作用到制動盤上,制動力矩與制動盤和摩擦片之間的壓力、摩擦系數(shù)成線性正相關,控制驅(qū)動電機軸轉(zhuǎn)角大小即可實現(xiàn)對于制動轉(zhuǎn)矩的控制,控制系統(tǒng)相對簡單,制動器的工作性能穩(wěn)定,但對于電機的功率要求較高,因而尺寸較大,如下圖所示。
無自增力制動器
無自增力制動器結(jié)構(gòu)圖
②自增力制動器:
在制動盤與制動鉗塊之間增加一個楔塊,制動工作時,制動盤的摩擦力使楔塊進一步楔入制動盤和制動鉗塊,增大夾緊力,產(chǎn)生更強的制動效能,從而產(chǎn)生自增力效果,故又稱為電子楔塊制動(EWB,Electronic Wedge Brake),這一類制動器中,電機驅(qū)動楔塊移動,與摩擦片接觸后,自增力機構(gòu)作用使壓力增加,產(chǎn)生更強的制動效能,因此電機的功率較小,裝置的體積和重量也較小,但 EWB 的制動效能取決于楔塊的工作狀況,因此對楔塊的工藝及精度要求很高,不易加工。而且其制動穩(wěn)定性相對較差,難于控制。如下圖所示。
自增力制動器
自增力制動器結(jié)構(gòu)圖
2)按照制動器執(zhí)行結(jié)構(gòu)的盤式或者鼓式之分,EMB又可以分為機電盤式制動器 (Electro-Mechanical Disk Brake) 和機電鼓式制動器 (Electro-Mechanical Drum Brake)。目前更多的機構(gòu)選擇的是機電盤式制動器。
3)EMB從執(zhí)行機構(gòu)的差別上可以分成兩類,第一類是電動機驅(qū)動執(zhí)行機構(gòu)然后作用到制動盤上;第二類是在前者的基礎上增加一個自增力機構(gòu)。第一類的典型代表是Continental Teves公司研發(fā)的制動器,German Aerospace Center的E-Brake屬于后者。兩類EMB各有優(yōu)缺點,前者結(jié)構(gòu)和控制都比較簡單,制動過程更穩(wěn)定;但由于電動機提供全部的制動推力,要求電動機必須輸出很大的功率,這就造成了電動機體積、質(zhì)量、能耗都比較大。后者由于增加了自增力機構(gòu),可以利用汽車的動能增加制動力度,所以驅(qū)動電動機的功率可以大幅降低,其能耗比前者減少83%,體積和質(zhì)量也比前者??;不過由于多了自增力機構(gòu),制動控制的難度變大,制動穩(wěn)定性也變差了。
七、優(yōu)缺點1.傳統(tǒng)制動系統(tǒng)已難以滿足當今汽車智能化、電動化對制動系統(tǒng)提出的新需求,線控制動相比傳統(tǒng)的液壓系統(tǒng)有明顯的優(yōu)勢,將使得線控制動技術取代傳統(tǒng)的以液壓為主的制動系統(tǒng),成為未來制動系統(tǒng)的主要發(fā)展方向。 汽車線控制動技術具備獨特的特征與優(yōu)點,主要優(yōu)勢和隱患體現(xiàn)在以下幾個方面: ①該技術能夠降低對駕駛?cè)藛T精力的消耗,在提高其駕駛舒適度的同時,增加了安全性。 ②此項技術能夠為汽車行業(yè)的發(fā)展帶來新的方向,提供了更廣闊的設計空間,不僅能夠促使設計方向更加個性化,還能提升性能,吸引更多的顧客。 ③此項技術能夠大量減少維護所消耗的費用,也減少了維護所用的設施。但在現(xiàn)階段,電子設備還具有一定的安全隱患,比如當電路失效后,很有可能導致油門的控制失靈、或是無法安全制動等,因此,今后的發(fā)展和研究要重點關注其安全性能,從而更好地提升車輛行駛的可靠性。
如下幾個傳統(tǒng)制動系統(tǒng)的痛點,恰恰是線控制動的優(yōu)勢,
①不受真空度的限制,所以不會因為海拔高度升高而制動變硬的情況; ②踏板感可調(diào),可以根據(jù)主機廠踏板感DNA調(diào)節(jié)出對應的踏板感覺; ③主動制動響應較快、對于ACC/AEB工況的適應性更強; ④具有很好的制動冗余(Two-Box)滿足L3制動駕駛的需求 ⑤能量回收優(yōu)于ESP Hev方案 與傳統(tǒng)的制動系統(tǒng)相比, 線控系統(tǒng)具有十分明顯的優(yōu)勢, 具有以下優(yōu)點:
①系統(tǒng)結(jié)構(gòu)簡單更簡潔了,整車質(zhì)量低。
②線控制動系統(tǒng)具有精確的制動力調(diào)節(jié)能力,是電動汽車摩擦與回饋耦合制動系統(tǒng)的理想選擇。
③便于擴展和增加其它電控制功能?;诰€控制動系統(tǒng),不僅可以實現(xiàn)更高品質(zhì)的ABS/ESC/EPB等高級安全功能控制,而且可以滿足先進汽車智能系統(tǒng)對自適應巡航、自動緊急制動、自動泊車、自動駕駛等的要求。
④導線取代了液壓管路,不存在由于管路冗長帶來的制動滯后問題。(EMB) ⑤無制動液,易于維護。由于沒有使用制動液, 而且結(jié)構(gòu)也比較簡單, 因此其維護工作比較簡單, 而且系統(tǒng)的耐久性也比較好, 從環(huán)保角度看也比較優(yōu)秀。(EMB) ⑥與傳統(tǒng)真空助力制動系統(tǒng)相比,線控電子液壓制動系統(tǒng)具有高性能主動制動、大幅提高制動能量回收率、制動感覺可調(diào)、集成度高、擴展性強等諸多優(yōu)勢(EHB) ⑦可以使用具有容錯功能的車用網(wǎng)絡通訊協(xié)議。
⑧使車輛制動控制的魯棒性得到了增強。系統(tǒng)中車輛每個輪子上都會配備獨立的制動控制器, 因此能夠通過更好的算法來完成制動力控制, 從而保證制動控制系統(tǒng)能夠應對較為復雜工況條件。
這些優(yōu)勢使得線控取代液壓成為了未來的趨勢,但在技術方面存在的諸多問題,也導致了線控發(fā)展的緩慢。其中有幾個也是線控制動系統(tǒng)最大的目前沒有辦法完全實施量產(chǎn)化的最大的制約因數(shù)。
2.電子液壓制動系統(tǒng)EHB有許多優(yōu)勢,
①傳統(tǒng)的制動系統(tǒng)在長期使用后,由于各部件的磨損和變形,會導致制動性能的衰退。而EHB會利用算法彌補部件的磨損和變形,使制動性能長期處于良好狀態(tài)。
②EHB可以根據(jù)各個車輪的轉(zhuǎn)速和附著力為其分配最合適的制動力,十分方便實現(xiàn)四輪制動分別控制,這就做到了制動的高度靈活性和高效性。
③EHB不但能夠提供高效的常規(guī)制動功能,還能發(fā)揮包括ABS在內(nèi)的更多輔助功能。
④EHB無發(fā)動機提供真空助力,體積更小、重量更輕,EHB內(nèi)部沒有運行真空助力器所需要的真空生成裝置,結(jié)構(gòu)更簡單緊湊,發(fā)動機艙內(nèi)的可用空間將增加。
⑤EHB的一切均為電氣控制,能夠?qū)崿F(xiàn)制動器的電動驅(qū)動,響應也更加迅速,與標準的真空助力器系統(tǒng)相比,反應速度更快,產(chǎn)生的摩擦力也更大,提供的性能更為穩(wěn)定,EHB在緊急情況下的制動力更強,并且產(chǎn)生的制動速度也更快,并可在應對道路緊急情況時縮短響應時間,提升駕駛員與乘客的安全保障。EHB具備高性能主動制動、高效率制動能量回收、制動感覺可調(diào)、高集成度、高安全性、擴展性強等諸多優(yōu)勢,可完美取代真空助力器、電子真空泵、真空罐等傳統(tǒng)制動系統(tǒng)部件。
⑥EHB通過軟件容易集成ABS、TCS、ESC等輔助功能,兼容性強,可以進一步提高行車的安全性及舒適性。
⑦EHB系統(tǒng)仍保留了傳統(tǒng)的液壓管路部分,是電子和液壓相結(jié)合的產(chǎn)物。與傳統(tǒng)的液壓或氣壓制動系統(tǒng)相比,EHB系統(tǒng)增加了制動系統(tǒng)的安全性,使車輛在線控制動系統(tǒng)失效時還可以進行制動,由于具有冗余系統(tǒng),安全性在用戶的可接受性方面更具優(yōu)勢;EHB在高級駕駛輔助系統(tǒng)方面也有優(yōu)勢,并且踏板解耦,能夠主動制動以及能量回收,使電動汽車EV在制動能量回收(即將制動系統(tǒng)的能量帶回電池)方面具有顯著優(yōu)勢;EHB為整車控制提供了更迅速更精確的執(zhí)行器,但其對液壓力控制的精度和控制算法的魯棒性要求也進一步提高;與傳統(tǒng)制動系統(tǒng)相比,EHB系統(tǒng)主動控制在制動工況中的所占比重越來越高。
⑧EHB是在傳統(tǒng)的液壓制動器基礎上發(fā)展來的,此類型產(chǎn)品成熟度高,相對來說開發(fā)、驗證難度不大。
3.EHB缺點: 備用系統(tǒng)中仍然包含復雜的制動液傳輸管路,液壓系統(tǒng)結(jié)構(gòu)復雜,使得EHB并不完全具備線控制動系統(tǒng)的優(yōu)點;容易發(fā)生液體泄漏,有一定的泄露風險,存在安全隱患;成本和維護費用較高;由于EHB以液壓為制動能量源,液壓的產(chǎn)生和電控化相對來說比較困難,不容易做到和其他電控系統(tǒng)的整合;液壓系統(tǒng)的復雜性對輕量化不利;應用過程中需要使用制動液, 而且存在控制時延長和結(jié)構(gòu)復雜等方面的問題,從而給汽車的安全運行造成不利的影響。 現(xiàn)代的汽車電子化程度越來越高,新能源汽車和自動駕駛汽車的發(fā)展又進一步加快了這種趨勢。在汽車越來越像電子產(chǎn)品的今天,EHB的優(yōu)點并沒有遠遠蓋過它的缺點,所以,EHB的大面積普及并不被看好。
EHB面臨的主要挑戰(zhàn):
①目前已經(jīng)出現(xiàn)的 EHB 系統(tǒng),無論是干式還是濕式系統(tǒng),由于均需要液壓系統(tǒng)參與,因此不能算是純粹的線控系統(tǒng);
②由于仍保留液壓結(jié)構(gòu),雖然利用電機驅(qū)動,但響應時間不夠迅速,作為智能輔助駕駛系統(tǒng)的底層執(zhí)行器,仍有提升的空間;
③主動制動力有提升空間;
④集成度不夠高,雖然相比于濕式EHB的3 boxes(ESP、Booster、高壓蓄能器),iBooster 等系統(tǒng)的 two boxes(ESP、Booster 或者EHB、踏板感覺模擬器)的方案大大提升了集成度,縮減了體積,但是仍有向1 box 進步的可能,MK-C1和IBS等系統(tǒng)已經(jīng)開始采用one box方案;
⑤對電動汽車而言,EHB有一定的漏液短路隱患。
4.EMB的優(yōu)點:
(1)執(zhí)行機構(gòu)和制動踏板之間無機械或液壓連接,集成度極高,是完全解耦的制動系統(tǒng),由于取消了主缸、液壓管路等復雜的零部件結(jié)構(gòu),制動更迅速,制動力的傳遞效率得到提升,踏板信號與執(zhí)行器之間完全靠電子信號傳輸,縮短了制動器的反應時間,反應靈敏,反應時間在100ms以內(nèi),EMB系統(tǒng)響應時間迅速,僅為90ms,比iBooster快了30ms,制動響應速度大大提高、更加迅速,執(zhí)行速度快,有效減少、大幅度縮短制動距離,安全優(yōu)勢極為突出。制動系統(tǒng)的相應時延關系到汽車的運行安全, 在傳統(tǒng)的機械和液壓制動系統(tǒng)中, 由于存在運動慣性和間隙等結(jié)構(gòu)問題, 制動命令發(fā)出后, 會延遲一定時間后才能夠完成執(zhí)行操作, 給汽車的行駛安全帶來了安全隱患, EMB中沒有液壓驅(qū)動部分,工作穩(wěn)定性和可靠性更好,使用電信號控制電機驅(qū)動,使制動系統(tǒng)的響應時間縮短,通過應用EMB系統(tǒng)能夠極大地減少制動控制的時延,極大地縮減制動相應的時間,從而給緊急情況的處理帶來更多的時間。
(2)整個系統(tǒng)中不需要助力器,省去液壓管路,不存在漏液問題,取消了制動系統(tǒng)的液壓備份部分,EMB系統(tǒng)結(jié)構(gòu)顯得更簡潔了,結(jié)構(gòu)更簡單,體積更小,讓出布置空間,減少空間,由于是獨立的制動系統(tǒng),布局上更加靈活,布置靈活;EMB結(jié)構(gòu)精簡,簡化了制動系統(tǒng)的結(jié)構(gòu),結(jié)構(gòu)極為簡單緊湊,制動系統(tǒng)的布置、裝配和維修都非常方便,易于裝配和維護,便于安裝調(diào)試,更為顯著的優(yōu)點是隨著制動液的取消,使汽車底盤使用、工作及維修環(huán)境得到很大程度地改善;同時由于減少了一些制動零部件,大大減輕了系統(tǒng)的重量,能夠降低整車質(zhì)量,提高汽車燃油經(jīng)濟性;沒有液壓系統(tǒng),無需制動液,不存在液壓泄露問題,降低了環(huán)境污染,環(huán)保。
(3)ABS模式下無回彈震動,可以消除噪音。
(4)EMB完全實現(xiàn)了電子化,制動平臺開放度更高,通過ECU直接控制,易于實現(xiàn)ABS、TCS、ESP、ACC等功能,可以很容易地與汽車的其他電控系統(tǒng)整合到一起,能夠發(fā)揮更多重的功能:制動、ABS、EBD、ESP、自動駕駛、優(yōu)化能量回收,可完美配合再生制動等,便于集成電子駐車制動、防抱死、制動力分配等附加功能,直接在控制器添加代碼即可;能夠?qū)崿F(xiàn)和其它控制功能的集成,X.By.Wire技術能夠提供硬件和功能的集成平臺, 從而能夠?qū)崿F(xiàn)制動、油門和轉(zhuǎn)向等獨立控制系統(tǒng)的集成, 使這些控制系統(tǒng)都集成到統(tǒng)一的平臺上, 通過計算機進行調(diào)控, 這樣能夠?qū)崿F(xiàn)控制系統(tǒng)的無縫連接。與ABS、TCS、ESC等模塊配合實現(xiàn)車輛底盤的集成控制,是真正的線控制動系統(tǒng),便于底盤域控制及智能駕駛技術發(fā)展。傳感器信號的共享以及制動系統(tǒng)和其它模塊功能的集成,便于對汽車的所有行駛工況進行全面的綜合控制,通過這樣的集成能夠極大的提升汽車的操作性和安全性, 而且還使汽車的設計更加的智能和靈活;EMB系統(tǒng)能夠?qū)崿F(xiàn)每個車輪制動力的獨立控制, 這樣能夠使輪胎的地面附著力達到最佳, 這樣可以實現(xiàn)不增加硬件的情況下, 依靠軟件來實現(xiàn)防抱死控制和電子制動力分配等功能。
5.EMB的缺點:
EMB使用本身工作環(huán)境惡劣,電子元器件易受干擾,系統(tǒng)工作的安全性和可靠性還有待提高;EMB要求助力電機的性能優(yōu)越、反應迅速、體積小巧,在電機設計上難度很大,成本很高。
(1)由于完全采取線控的方式,無液壓備用制動系統(tǒng),取消了機械連接,沒有機械冗余,沒有失效備份,因而對系統(tǒng)的工作可靠性和容錯要求更高, 或需要備份系統(tǒng)或存在對應的后備執(zhí)行系統(tǒng)來保證可靠性。因此必須具有很高的設備可靠性,制動系統(tǒng)必須配備可靠的冗余方案。雖然在現(xiàn)階段,可通過其他技術來提升整體系統(tǒng)的安全性,但還是需要保留一個基本的后備系統(tǒng),若在電子控制單元中,發(fā)生故障時,便能及時開始啟動;如果電路出現(xiàn)短路、斷路,或者電源出現(xiàn)問題,制動系統(tǒng)怎樣繼續(xù)發(fā)揮功能?制動踏板模擬器不能正常工作又該如何處置?是容錯的要求,因此需要在系統(tǒng)的可靠性上著重加強,還要設置意外情況下的保險功能。包括穩(wěn)定的電源系統(tǒng)、更高的總線通信容錯能力和電子電路的抗干擾能力。由于去除了備用制動系統(tǒng),EMB系統(tǒng)需要有很高的可靠性,關于容錯的要求則是:容錯的情況會根據(jù)場合的改變而變化,且在控制器等中存在備份。還需要可靠性更高的總線協(xié)議和強抗信號干擾能力,尤其是需要解決車載電源失效問題。一般來說是需要有容錯功能的總線協(xié)議,目前整車環(huán)境還沒有普遍采用這樣的總線協(xié)議;需要更好的抗干擾能力,地面車輛運行會遇到各種干擾信號,目前來說電動汽車在EMC方面問題還是很多的,這方面的問題有一些也是比較難以解決的。 (2)制動力不足的挑戰(zhàn)。EMB取消了原有液壓系統(tǒng),將電機直接集成在制動鉗上,必須布置在輪轂中,執(zhí)行機構(gòu)安裝在制動鉗上,因輪轂處布置體積決定制動電機不可能太大,制動電機的設計受限,電機功率限制,制動力不足;空間非常有限,只能采用小型永磁式制動電機。目前的小電機提供的剎車力不足,小電機無法滿足普通轎車制動功率1-2kW的要求。純靠永磁電機產(chǎn)生的制動力有限,要想大規(guī)模普及到前后車輪上還需要永磁體性能得到突破。 (3)工作環(huán)境惡劣,工作溫度高的挑戰(zhàn)。特別是高溫,剎車溫度達幾百攝氏度,制動系統(tǒng)在長時間或高強度工作時會產(chǎn)生高溫,所以關鍵部件的抗高溫性能和散熱性能非常重要;剎車片產(chǎn)生的高溫巨震環(huán)境對電機穩(wěn)定性、芯片半導體和永磁材料造成巨大考驗;且布置空間有限,無法裝散熱裝置,加劇了這一挑戰(zhàn)。制動器需要能夠耐高溫,質(zhì)量輕,成本低。是關于執(zhí)行器的要求:首先,需要具備良好的高溫性能,能夠承受住執(zhí)行器周邊的較高溫度,其次,需要開發(fā)一些質(zhì)量輕且價格實惠的制動器,且尺寸滿足車輛設計的需求。因?qū)儆诨上虏考駝痈?,制約現(xiàn)有EMB零部件的設計。如:因空間限制,制動電機只能采用永磁式,而最好的磁王釹鐵硼(N35牌號)工作上限80℃,310℃磁性消失,制動電機無法工作。另如:EMB部分半導體需工作在剎車片附近,不能承受幾百度的高溫,且因體積限制難以配置冷卻系統(tǒng)。制動器需要具有更好的耐高溫性能,同時需質(zhì)量輕價格低。
(4)EMB需要用非常精密的電子電路才能運行,但在車輛的行駛途中,會接收到來自不同種類的干擾信息,要面對外部的各種電磁場和地球磁場,這就需要電子電路有更好的抗干擾能力,抵制車輛運行中遇到的各種干擾信號。關于抗干擾的處理最常見的是“對稱式”、“非對稱式”兩種,兩者各有各的優(yōu)勢。除此之外,線控制動系統(tǒng)的軟件和硬件要進一步完善,從而滿足不同車輛的有效需求。只有進行全面化考慮,才能創(chuàng)建其科學化的總線系統(tǒng),進而獲取良好的控制系統(tǒng)。
(5)驅(qū)動電源問題,首先,是執(zhí)行器能量需求,制動能量需求比較大,需1-2kw電機:傳統(tǒng)的鼓式制動的功率要求是100W,而盤式制動則需要1000W,執(zhí)行制動動作的電動機會消耗不少的電能,目前的12V車載電源可能無法勝任,如果車輛電氣系統(tǒng)的整體電壓維持在12V,是很難保障能夠滿足其運作需求的,因此,執(zhí)行器對于能量的需求非常關鍵。應該為其建立起足夠電壓的系統(tǒng)(一般是保持在42伏特),未來需要成熟可靠的42V或48V電源高壓系統(tǒng)提高電機功率來保證系統(tǒng)的能源供應,同時還需要應對高壓所隱藏的安全隱患。42V電壓系統(tǒng)從目前發(fā)展的趨勢看也是一種發(fā)展的方向,但是目前來說暫時沒有大批量的出現(xiàn)。
(6)需要針對底盤開發(fā)對應的系統(tǒng),難以模塊化設計,導致開發(fā)成本極高。由于EMB是全新的技術,又需要大量傳感器和控制芯片的支持,導致成本比現(xiàn)在主流制動系統(tǒng)高,因此降低成本增強競爭力是EMB能否走向市場的決定因素。市場上還沒有成熟的EMB產(chǎn)品,制動系統(tǒng)功能安全等級要求高,產(chǎn)品周期長,投放到市場還需要各種驗證。
七 需求挑戰(zhàn)趨勢
當前線控制動系統(tǒng)面臨的主要需求是節(jié)能減排,在節(jié)能與新能源汽車產(chǎn)業(yè)發(fā)展規(guī)劃中提出了不管是乘用車和商用車都提出了燃料消耗量降低的目標要求,包括新能源汽車發(fā)展的要求。汽車智能輔助駕駛技術的發(fā)展需要EHB系統(tǒng)作為一個執(zhí)行機構(gòu)來做配合,這是EHB系統(tǒng)目前面臨的一些新的需求,第一個因為電動汽車目前來說普遍的都具有能量回收功能,它需要一個制動能量回收功能,目前整車企業(yè)整車廠一般來說主要在做一個帶檔滑行回收的,這是一個開盤回收的過程;第二個就是智能駕駛,目前來說主要在ESC上實現(xiàn),但其實無法支撐智能輔助駕駛需要的一個快速降壓還有精度高的要求,那么EHB系統(tǒng)是可以達到這樣的要求;然后是適用于分布式驅(qū)動的汽車,主要是指輪轂電機驅(qū)動的汽車。這里又衍生出來一個制動能量回收效率的問題,它又衍生出舒適度和噪音、安全性、耐久性的問題。純粹的線控制動系統(tǒng)—電子機械制動系統(tǒng)EMB成為研究熱點,該系統(tǒng)響應時間更快,平臺開放度更高,同時不會有漏液隱患,這對電動汽車具有重要意義。
在汽車電動化和智能化技術的大潮下,汽車制動系統(tǒng)將產(chǎn)生新的發(fā)展趨勢。
1.擺脫真空源
首先要求制動系統(tǒng)不再使用真空源助力,需要采用新的助力源,因此各種電動助力制動系統(tǒng)開始出現(xiàn)。
2.體積、質(zhì)量更小、集成度更高
帶有高壓蓄能器的濕式EHB系統(tǒng)過于復雜、體積和質(zhì)量均很大,并且響應時間略長,成本高、維修費用昂貴,新型制動系統(tǒng)向去掉高壓蓄能器的方向發(fā)展。
3.系統(tǒng)更開放,可與其他底盤控制子系統(tǒng)配合
為了提高整車的綜合行駛性能,要求制動系統(tǒng)是一個更加開放的平臺,能夠和其他底盤控制子系統(tǒng)集成。
4.再生制動與踏板解耦
為了解決電動汽車和混合動力汽車的續(xù)航里程問題,出現(xiàn)了制動能量回收技術,為了與再生制動協(xié)調(diào)工作,要求制動系統(tǒng)在保證高的制動能量回收效率的同時具有解耦能力,液壓制動系統(tǒng)應能根據(jù)駕駛員的制動需求合理分配再生制動力和液壓制動力。
5.適用于智能駕駛輔助系統(tǒng)
隨著汽車智能化技術的發(fā)展,制動系統(tǒng)的另一個發(fā)展趨勢就是應能夠與ESC、ACC等汽車智能輔助駕駛匹配,能夠作為智能駕駛輔助系統(tǒng)的重要底層執(zhí)行器。這就要求制動系統(tǒng)擁有更強的主動制動能力以及更快的響應速度和更精確的制動壓力控制。
6.人機共駕
隨著執(zhí)行控制層面人機共駕技術的發(fā)展,要求制動系統(tǒng)具有能夠個性化定制踏板感覺和制動特性的能力,車輛匹配各種不同的駕駛風格和駕駛模式。
7.具備更平順的“軟”停車功能、更好的
NVH性能這要求制動系統(tǒng)響應必須足夠精確、迅速和舒適。例如當車輛開啟ACC自適應巡航時,博世的iBooster可以確保車輛在制動直到停駛過程中的制動舒適性,在此過程中幾乎不產(chǎn)生任何振動和噪聲。
8.系統(tǒng)線控
汽車底盤電動化,而線控制動是底盤線控化的最大障礙,目前市場上沒有成熟可靠的量產(chǎn)解決方案。域控制等都離不開線控制動系統(tǒng)。
隨著汽車技術向低碳化、智能化發(fā)展,制動系統(tǒng)未來的研究方向?qū)⒀刂@八大趨勢進行,即未來的制動系統(tǒng)將向更節(jié)能、更開放、更精確、更快速、更智能、更安全、更舒適的方向發(fā)展。
制動行業(yè)正在變革, 未來將是線控制動系統(tǒng)蓬勃發(fā)展的時期,線控制動是電動化、智能化的必然選擇,電動化和智能化趨勢共同指向一個方向:汽車制動系統(tǒng)將與踏板解耦,向電子化、線控化轉(zhuǎn)變。
審核編輯:郭婷
-
傳感器
+關注
關注
2552文章
51288瀏覽量
755108 -
智能汽車
+關注
關注
30文章
2877瀏覽量
107401 -
自動駕駛
+關注
關注
784文章
13895瀏覽量
166689
原文標題:T-Booster與ESC耦合制動系統(tǒng)
文章出處:【微信號:阿寶1990,微信公眾號:阿寶1990】歡迎添加關注!文章轉(zhuǎn)載請注明出處。
發(fā)布評論請先 登錄
相關推薦
PLC的未來發(fā)展趨勢的三個方向
您看好電動汽車的未來發(fā)展趨勢嗎?
未來觸控產(chǎn)品發(fā)展趨勢1
未來觸控產(chǎn)品發(fā)展趨勢3
Multicom發(fā)展趨勢如何?它面臨哪些挑戰(zhàn)?
嵌入式開發(fā)工具面臨的挑戰(zhàn)是什么?未來的發(fā)展趨勢呢?
新形勢下如何裝表接電
新形勢下智能制造發(fā)展趨勢
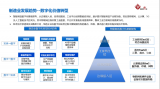
評論