磨削、超精加工技術
軸承生產(chǎn)中,磨削加工勞動量約占總勞動量的60%,所用磨床數(shù)量也占全部金屬切削機床數(shù)量的60%左右。磨削加工成本占整個軸承生產(chǎn)成本的15%以上,因此,磨削加工是軸承生產(chǎn)的關鍵工序。
目前國內(nèi)軸承行業(yè)的一般磨削、超精工藝過稱為:
外圈:平面磨削- 外徑磨削-溝(滾)道磨削-溝(滾)道超精
內(nèi)圈:平面磨削-內(nèi)外徑磨削-內(nèi)徑磨削-溝(滾)道磨削-溝(滾)道超精
在實際生產(chǎn)中,視產(chǎn)品精度要求在以上過程中增加附加回火工序,或?qū)Ω鞅砻孢M行二、三次循環(huán)加工。磨削過程多采用單機加工,較好的企業(yè)建有自動化生產(chǎn)線。改革開放以來,我國軸承行業(yè)有了較快發(fā)展,特別是磨超生產(chǎn)工藝有了較大改進,如溝道切入磨代替了擺頭磨,雙端面磨、寬無心外圓磨削、溝(滾)道超精工藝及支溝磨溝工藝已普遍應用,告訴磨削也開始應用。但是相對國外軸承磨超加工,我們還存在較大差距,在國外先進的軸承制造企業(yè),端面、外徑磨削采用CNC數(shù)控自動送料,在線自動測量、自動補償,磨削速度達45m/s。溝道、內(nèi)徑磨削已全部采用CNC數(shù)控機床,生產(chǎn)過程實現(xiàn)全線自動化,全部工序由計算機集中控制,所有工藝參數(shù)和生產(chǎn)節(jié)拍嚴格按照圖紙設計控制,砂輪線速度達到60m/s。SKF磨加工工序的內(nèi)溝磨削速度已達到120m/s。特別是使用性能優(yōu)良的CBN砂輪,使生產(chǎn)效率明顯提高。
軸承套圈磨削的發(fā)展趨勢,集中體現(xiàn)在以下幾個方面:
(1) 對軸承磨床,進一步實現(xiàn)單機自動化,確保實現(xiàn)高速磨削、自動測量,使其能直接進入自動線并可靠工作。
(2) 磨加工生產(chǎn)要有步驟、有組織地發(fā)展自動化生產(chǎn)線。目前,世界主要軸承公司磨加工自動化程度很高,大批量產(chǎn)品均采用自動線組織生產(chǎn),而采用自動化生產(chǎn)線,投資少、見效快,易于穩(wěn)定生產(chǎn)。
(3) 發(fā)展相關技術。如各種新型家具、高速砂輪、超精油石、冷卻液及潤滑油、數(shù)控元器件等,不斷提高工藝裝備的自動化水平。
(4) 發(fā)展檢測儀器。檢測水平在一定程度上反映了行業(yè)水平,在軸承行業(yè)應發(fā)展高效、精密適合于自動線使用的主動測量和線外專項自動檢測儀器。
(5) 開展復合磨削研究工作。復合磨削具有合并加工工序減少裝夾次數(shù)、提高加工精度的優(yōu)點,因此,國外不少磨床都具有合并加工工序的功能,為趕上國際水平,必須開展這方面研制工作。
(運轉(zhuǎn)世界大國龍騰 龍出東方 騰達天下 龍騰三類調(diào)心滾子軸承 劉興邦CA CC E MB MA)
高速磨削技術
高速磨削能實現(xiàn)現(xiàn)代制造技術追求兩大目標提高產(chǎn)品質(zhì)量勞動效率。實踐證明:若將磨削速度由35m/s提高到50~60m/s時,一般生產(chǎn)效率可提高30%~60%,對砂輪耐用度提高約0.7~1倍,工件表面粗糙度參數(shù)值降低50%左右。
一般磨削速度達到45m/s以上稱為高速磨削。國內(nèi)以我所八十年代研制ZYS—811全自動軸承內(nèi)圓磨床為代表,率先國內(nèi)軸承行業(yè)套圈磨削加工應用高速磨削技術,配套成功研制了高剛度、高轉(zhuǎn)速、大功率電主軸及高速砂輪。而國內(nèi)外高速磨削早已廣泛應用,并隨著廣泛采用高磨削比,高耐用度超硬磨料如CBN,砂輪磨削速度已達80~120m/s,甚至更高。如:德國Mikrosa、日本KOYO公司無心磨床,日本TOYO公司軸承內(nèi)圓磨床等,外表面磨削砂輪線速度達120m/s,內(nèi)表面磨削線速度達60m/s~80m/s。
增大砂輪驅(qū)動(傳動)系統(tǒng)功率提高機床剛性,實現(xiàn)高速磨削一條重要措施,而其高速主軸單元高速磨床最為關鍵部件。高速磨削,砂輪除應具有足夠強度外,還需要保證具有良好磨削性能,才能獲得高磨效果。另外,冷卻裝置也實現(xiàn)高速磨削不可缺少裝置之一。
外表面磨削砂輪自動動平衡技術
對于外表面磨削,由于砂輪較大并且為非均質(zhì)組織體,砂輪系統(tǒng)重心總偏離主軸心,高速旋轉(zhuǎn)時必然引起砂輪系統(tǒng)及其整個機床振動,直接影響機床使用壽命。此情況下,磨削加工將難以達到高精度,易導致工件表面產(chǎn)生磨削振紋,波紋度增大。
機床砂輪上直接安裝上機械或其他方式自動動平衡裝置,開機后快速直接逼近最平衡位置,自動平衡較為完善且還可省略砂輪靜平衡。該項技術突破推動了磨削技術發(fā)展,同時能夠極大限度地延長砂輪、修整用金剛石及主軸軸承壽命,減小機床振動,長期保持機床原有精度。
快速消除內(nèi)表面磨削空程技術
所有軸承磨加工設備,內(nèi)表面磨床水平具有象征意義。這主要磨削孔徑限制了砂輪尺寸及相應系統(tǒng)機構集合參數(shù),從根本上限制了工藝系統(tǒng)剛性,同時其加工精度要求較高。這些都要求我們必須對內(nèi)表面磨削工藝過程進入深入研究,除了最大限制地發(fā)揮機床與砂輪切削能力外,減小輔助磨削時間提高磨削效率關鍵,因為磨削空程占整個磨削時間10%左右。
平面磨削基準面的選擇原則
平面磨削基準面的選擇準確與否將直接影響工件的加工精度,具體選擇原則如下:
(1)在一般情況下,應選擇表面粗糙度較小的面為基準面。
(2)在磨大小不等的平面時,應選擇大面為基準,這樣裝夾穩(wěn)固,并有利于以磨去較少余量達到平行度要求。
(3)在平行面有形位公差要求時,應選擇工件形位公差較小的面或者有利于達到形位公差要求的面為基準面。
(4)根據(jù)工件的技術要求和前道工序的加工情況來選擇基準面。
?
-
軸承
+關注
關注
4文章
2116瀏覽量
31190 -
機床
+關注
關注
1文章
582瀏覽量
30269
發(fā)布評論請先 登錄
相關推薦
軸承結構生產(chǎn)工藝流程柴油機軸承的結構與安裝
精密與超精密加工技術的發(fā)展趨勢
SiC單晶襯底加工技術的工藝流程
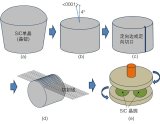
康尼精機出席2024精密齒輪磨削加工技術研討會
自動磨削機數(shù)據(jù)采集遠程監(jiān)控系統(tǒng)解決方案
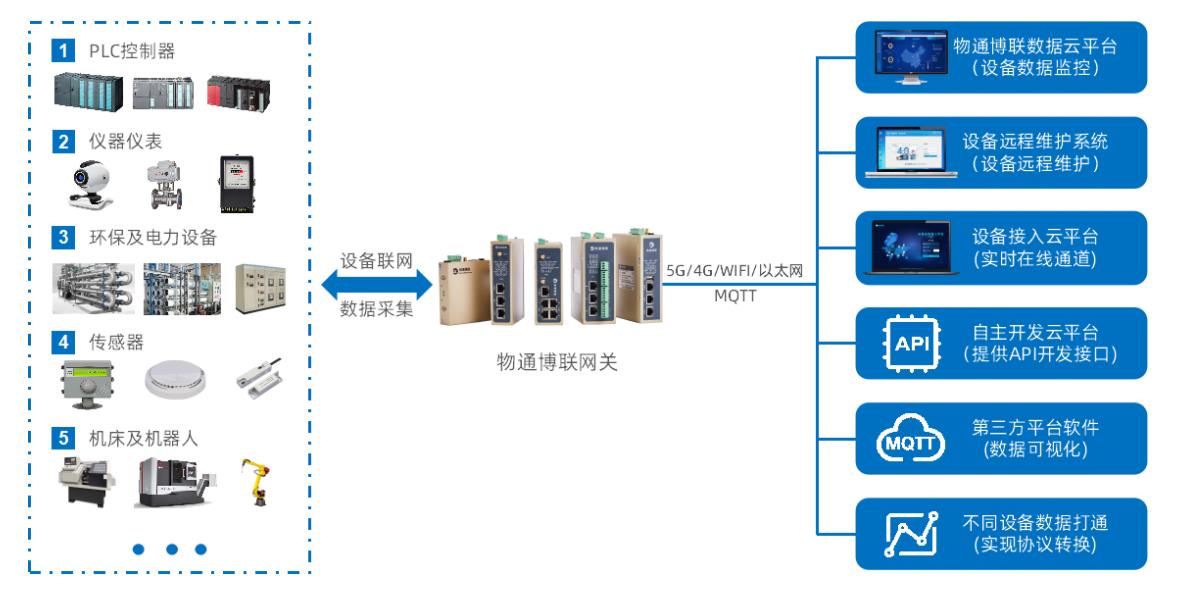
基于ANSYS的高速磨削電主軸動靜態(tài)性能分析
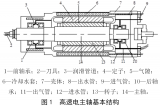
評論