摘要:文章是針對(duì)印制電路板生產(chǎn)過程中線路、阻焊的顯影工序所產(chǎn)生的廢顯影液進(jìn)行再生利用實(shí)踐及研究,其工藝過程是廢顯影液在超濾工藝過濾后通過參數(shù)調(diào)整、清洗等一系列的工藝流程,實(shí)現(xiàn)顯影液的循環(huán)再利用,減少廢水的排放。
0前言
印制電路板(PCB)生產(chǎn)過程中在線路和阻焊工序,需要經(jīng)過貼膜(或網(wǎng)?。?duì)位、曝光、顯影等加工步驟,將照相底版上的圖形轉(zhuǎn)移到在制PCB的表面上。其中的顯影步驟是使用低濃度的堿性顯影液將干膜或油墨未被曝光的部分通過化學(xué)反應(yīng)溶解于顯影液中,已經(jīng)曝光聚合的部分保留在電路板上完成圖形制作的過程。此制作環(huán)節(jié)會(huì)產(chǎn)生高濃度的顯影廢液,含有大量不同顏色的干膜或油墨殘?jiān)鞍逍嫉入s質(zhì)。其化學(xué)需氧量COD一般在10 000~20 000 mg/L,懸浮物800~1200 mg/L,pH值12~13。通常的處理方式是將顯影廢液排入工廠的廢水站與其它有機(jī)廢水合并進(jìn)行生化處理。根據(jù)國家廢水排放標(biāo)準(zhǔn),COD值要求<80 mg/L達(dá)標(biāo),傳統(tǒng)處理方法投資大、廢水處理量大、運(yùn)行成本高,已經(jīng)不再適合企業(yè)發(fā)展的需要。
行業(yè)內(nèi)推廣最新的處理方式是將廢顯影液通過超濾工藝過濾,然后經(jīng)過調(diào)整顯影液里的化學(xué)成分,再通過參數(shù)調(diào)整、清洗等一系列的工藝流程,實(shí)現(xiàn)顯影液的循環(huán)再利用,減少廢水的排放。如何在確保生產(chǎn)品質(zhì)穩(wěn)定的基礎(chǔ)上,提升回收再生的效率是這套系統(tǒng)運(yùn)行成功的關(guān)鍵。
1 顯影液循環(huán)再生利用系統(tǒng)
1.1 回收系統(tǒng)組成顯影液循環(huán)再生利用系統(tǒng)由五部分組成:(1)用于實(shí)現(xiàn)對(duì)回收液進(jìn)行收集的阻焊顯影液回收系統(tǒng);(2)與顯影液回收系統(tǒng)相連通,用于對(duì)藥水進(jìn)行過濾的超濾過濾系統(tǒng);(3)與超濾過濾系統(tǒng)相連通,用于實(shí)現(xiàn)對(duì)藥水進(jìn)行再生的再生系統(tǒng);(4)與再生系統(tǒng)和過濾系統(tǒng)相連通,用于實(shí)現(xiàn)對(duì)槽體進(jìn)行清洗的清洗系統(tǒng);(5)與所述再生系統(tǒng)相連通,用于實(shí)現(xiàn)藥液添加的添加系統(tǒng)。
1.2 回收系統(tǒng)工作方法廢顯影液過濾再生首先將廢顯影液通過顯影槽的出料口管道連通到回收站中央收集池;再通過揚(yáng)程泵抽到與回收站中央收集池連通的暫存槽暫存;然后送到過濾系統(tǒng)采用超濾膜超濾過濾,去除雜質(zhì)和污物;過濾后回收液再送至再生槽,與濃縮原液按比例混合;攪拌均勻調(diào)配成再生液,再生液pH要求12.5,碳酸根離子濃度按1.2%。達(dá)標(biāo)的再生液可以重新投入到生產(chǎn)線上正常使用。再生液添加方法包括再生槽加裝pH控制探頭以及自動(dòng)添加裝置,按pH值補(bǔ)加水和顯影濃縮液,pH控制器可設(shè)定12.5,分析化驗(yàn)要求碳酸根離子濃度按1.2%補(bǔ)加完成,補(bǔ)加完成后再生槽出口通過管道連接高壓泵,進(jìn)入加料槽進(jìn)料口,加料槽設(shè)置高液位、低液位,通過管道進(jìn)入車間的自動(dòng)添加缸入料口,自動(dòng)添加缸出料口通過管道連接pH控制器,通過管道連接顯影槽入料口。同時(shí)可以利過濾后的藥水對(duì)清洗槽進(jìn)行清洗,清洗完的顯影液再返回暫存槽進(jìn)行二次過濾,暫存槽清洗可以打開管道清洗后排入廢水站。具體回收系統(tǒng)工作運(yùn)行方法如圖1所示。
1.3 回收再生技術(shù)特點(diǎn) (1)待處理顯影液通過棉芯過濾器只可過濾5~10 mm以上的固體物,但是通過超濾膜過濾可以將大于0.1 mm的干膜膠體物或防焊膠體物全部過濾,并且能夠讓顯影化學(xué)物透過并不變質(zhì),透過液可被送到再生槽,調(diào)配成再生液,然后送到顯影設(shè)備中再次利用。(2)該顯影液循環(huán)再生利用系統(tǒng)打破了傳統(tǒng)的印制電路板顯影液的管理方式,不用每天排放,可以循環(huán)使用。(3)該顯影液循環(huán)再生利用系統(tǒng)完全收集顯影的廢水過濾后,污水再利用,可大幅減少廢水廢渣排放,有效利用了水資源,節(jié)能環(huán)保。(4)降低生產(chǎn)成本,提高生產(chǎn)效率,同時(shí)保證了顯影點(diǎn)的穩(wěn)定性,確保電路板的生產(chǎn)品質(zhì)。
2回收再生實(shí)踐 2.1 原有處理方式線路顯影線3條,阻焊顯影線2條,印制電路板產(chǎn)量40000平方米/月,顯影液用量300噸/月,顯影廢液排放到廢水處理站生化處理。
2.2 回收再生處理流程安裝300噸處理量顯影液廢液再生系統(tǒng)一套,通過收集、過濾、再生、清洗、回用等步驟,實(shí)現(xiàn)80%以上廢液回用,剩余廢液排放到廢水處理站生化處理。具體回收再生處理流程(見圖2)。
2.3 超濾過濾原理及效果超濾是一種加壓膜分離技術(shù),即在一定的壓力下使小分子溶質(zhì)和溶劑穿過一定孔徑的特制的薄膜,而使大分子溶質(zhì)不能透過,留在膜的一邊,從而使大分子物質(zhì)得到了部分的純化。超濾原理也是一種膜分離過程原理,超濾利用一種壓力活性膜,在外界推動(dòng)力(壓力)作用下截留水中膠體、顆粒和分子量相對(duì)較高的物質(zhì),而水和小的溶質(zhì)顆粒透過膜的分離過程。通過膜表面的微孔篩選可截留分子量為10 000~30 000的物質(zhì)。當(dāng)被處理水借助于外界壓力的作用以一定的流速通過膜表面時(shí),水分子和分子量小于300~500的溶質(zhì)透過膜,而大于膜孔的微粒、大分子等由于篩分作用被截留,從而使水得到凈化。其過濾原理如圖3所示。超濾膜在過濾方式上也分為內(nèi)壓和外壓兩種。內(nèi)壓式超濾膜被截留的污染物在超濾膜管內(nèi),可以被直沖洗水流全部沖走,而外壓式超濾膜的污染物存在于膜管之間,污染物無法全部沖洗干凈,日累月積會(huì)引起超濾膜堵塞,所以本顯影過濾系統(tǒng)選用的是內(nèi)壓式超濾膜。顯影液經(jīng)超濾回用設(shè)備過濾后,顯影液中的油墨雜質(zhì)被過濾,顯影液體變得清澈透明潔凈(見圖3)。
2.4 再生液配置方法及控制參數(shù)超濾后的顯影液碳酸根[CO32-]濃度偏低,顯影過濾后再生液經(jīng)化驗(yàn)后濃度下降0.3~0.5%,pH值下降1.0~1.5,再生藥水無法直接加入自動(dòng)添加缸中投入生產(chǎn)使用,需要在再生槽加裝pH控制探頭以及自動(dòng)添加裝置,按pH值補(bǔ)加水和顯影濃縮液(濃縮液為藥水供應(yīng)商提供的原液),pH值控制器可設(shè)定12.5,邊補(bǔ)加邊循環(huán)攪拌,通過調(diào)配后恢復(fù)達(dá)到pH:12~13、濃度1.1%~1.3%。
補(bǔ)加完成后再生槽出口通過管道連接高壓泵,抽入存儲(chǔ)槽備用。存儲(chǔ)的藥水可以通過管道進(jìn)入車間的自動(dòng)添加缸入料口,自動(dòng)添加缸控制系統(tǒng)連接pH控制器,自動(dòng)添加缸出料口通過管道連接顯影線的顯影槽入料口,當(dāng)pH值超出設(shè)定范圍時(shí)開始自動(dòng)添加。顯影液濃度對(duì)比及再生液工藝參數(shù)要求(見表1、表2)。
再生液碳酸根[CO32-]濃度化驗(yàn)方法如下。(1)試劑:0.1 mol/L 鹽酸(2)方法: ①取5 ml樣品,至250 mL錐形瓶中; ②加4~5滴指示劑甲基紅,用0.1 mol/L 鹽酸滴定; ③由黃色滴定成紅色為終點(diǎn)色。(3)計(jì)算:碳酸根(g/l)=F×V×13.85F——0.1 mol/L鹽酸溶液變量V——0.1 mol/L鹽酸溶液滴定體積(ml)配置方案:再生液按pH值12.5,濃度為1.2%配置。取200 mL超濾液,加入原液5 mL,測pH值12.7,濃度為2.6%,再加入100 mL水,測pH值12.6、濃度1.4%,再加入50 mL水,測pH值12.5,濃度為1.2%。通過化驗(yàn)結(jié)果得到再生槽的添加比例為:超濾液:原液:水=25 L:1 L:7 L。
2.5 設(shè)備回用能力在回用系統(tǒng)存儲(chǔ)槽上加裝流量計(jì)及刻度,設(shè)備運(yùn)行后經(jīng)跟進(jìn)統(tǒng)計(jì)再生液與廢顯影液的總量,表3為統(tǒng)計(jì)連續(xù)兩周(15天)數(shù)據(jù)。經(jīng)計(jì)算回用系統(tǒng)回用率在80%以上,廢液排放量低于20%,與設(shè)計(jì)要求一致?;赜寐?(再生液量÷總廢顯影液量)×100%=(128830÷157960)×100%=81.6%。
2.6 回用液生產(chǎn)品質(zhì)回用系統(tǒng)調(diào)試穩(wěn)定后上線使用,每4 h分析一次pH值和碳酸根離子濃度。經(jīng)跟進(jìn)統(tǒng)計(jì)連續(xù)7天再生液控制參數(shù)數(shù)據(jù),測量的化驗(yàn)pH值、濃度穩(wěn)定,pH值范圍:12.5±0.5,碳酸根離子濃度范圍:1.2±0.1%。設(shè)備運(yùn)行穩(wěn)定,產(chǎn)線使用回用藥水后未出現(xiàn)顯影不凈問題,生產(chǎn)整體品質(zhì)與之前使用原液配槽基本一致,未出現(xiàn)品質(zhì)波動(dòng)。
3回收效益
以其中一條顯影線,使用碳酸鉀顯影液為例,比較原有模式與在線顯影液回用模式獲得的經(jīng)濟(jì)效益。此顯影線顯影缸總體積大小1600 L,需要消耗的物料主要是顯影液、濾芯及保養(yǎng)時(shí)使用的清槽劑。具體收益比較(見表4)。
顯影線在不計(jì)算人工、水電、設(shè)備折舊的前提下,月度成本計(jì)算公式如下。顯影線成本=日常生產(chǎn)成本+保養(yǎng)成本+廢液及固廢處理成本=顯影液成本+清槽劑成本+濾芯成本+廢液處理成本+固廢處理成本
按顯影液單位成本2元/公斤,清槽劑單位成本2元/公斤,濾芯單位成本22元/支,廢液處理費(fèi)3元/噸,濾芯固廢處理費(fèi)用4000元/噸計(jì)算:原有模式成本=60×1000×2+3×1000×9+160×22+(60+12.8)×3+0.15×4000=151338.4元/月;回用模式成本=15×1000×2+1.5×1000×9+32×22+(15+6.4)×3+0.03×4000=44388.2元/月;回用模式節(jié)約成本=151338.4-44388.2=106950.2元/月
假設(shè)整套回收再生系統(tǒng)總投資250萬元,每月運(yùn)行成本約6萬元(含人工、水電),總計(jì)有5條規(guī)格相同的顯影線,按每條線每月節(jié)約成本10萬元計(jì)算,可以在6個(gè)月內(nèi)收回投資成本,其后每年可以節(jié)約成本5×10×12-6×12=528萬元。
4結(jié)論
通過導(dǎo)入超濾回收系統(tǒng)并結(jié)合公司實(shí)際情況進(jìn)行優(yōu)化設(shè)計(jì)和改進(jìn),建立了一整套完善的運(yùn)作管理體系,實(shí)現(xiàn)了顯影液的在線回收利用,回用液品質(zhì)良好,經(jīng)濟(jì)收益顯著。(1)通過使用在線顯影再生利用系統(tǒng)80%藥水可以清潔回用,可減少四分之三的污水排放;(2)通過實(shí)際生產(chǎn)品質(zhì)確認(rèn),使用在線顯影再生利用后與原有方式比較,未對(duì)品質(zhì)造成不良影響,符合品質(zhì)要求;(3)通過使用在線顯影再生利用系統(tǒng),每年可以為公司節(jié)約巨額成本。
原文標(biāo)題:【本刊獨(dú)家】通元科技:印制電路板顯影液循環(huán)再生利用系統(tǒng)的實(shí)踐研究
文章出處:【微信公眾號(hào):CPCA印制電路信息】歡迎添加關(guān)注!文章轉(zhuǎn)載請注明出處。
責(zé)任編輯:haq
-
pcb
+關(guān)注
關(guān)注
4319文章
23105瀏覽量
398138 -
印制電路板
+關(guān)注
關(guān)注
14文章
956瀏覽量
40794
原文標(biāo)題:【本刊獨(dú)家】通元科技:印制電路板顯影液循環(huán)再生利用系統(tǒng)的實(shí)踐研究
文章出處:【微信號(hào):pci-shanghai,微信公眾號(hào):CPCA印制電路信息】歡迎添加關(guān)注!文章轉(zhuǎn)載請注明出處。
發(fā)布評(píng)論請先 登錄
相關(guān)推薦
TüV南德與中汽數(shù)據(jù)解讀汽車行業(yè)循環(huán)再生規(guī)范,共促產(chǎn)業(yè)綠色轉(zhuǎn)型
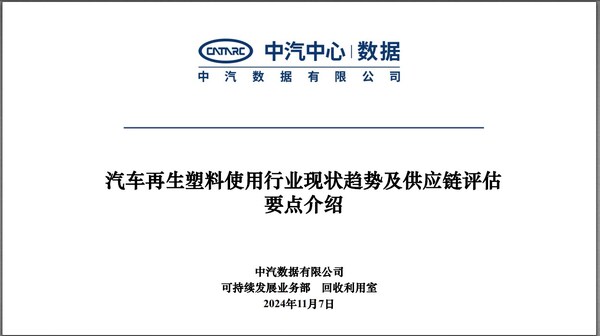
富士膠片開始銷售用于最先進(jìn)半導(dǎo)體生產(chǎn)的材料
利用位反轉(zhuǎn)尋址實(shí)現(xiàn)循環(huán)緩沖器
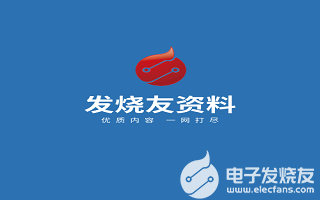
TE Connectivity 去“碳”路,去助力可再生能源電力系統(tǒng)
PCB行業(yè)典型DFM實(shí)踐 PCB先進(jìn)設(shè)計(jì)實(shí)踐讓效率倍增
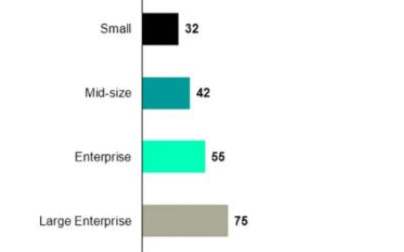
功率放大器在多組分微液滴交流電場下可控融合研究中的應(yīng)用
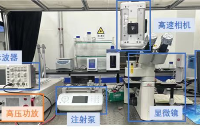
激光指向穩(wěn)定在光刻系統(tǒng)應(yīng)用中的關(guān)鍵作用及其優(yōu)化方案
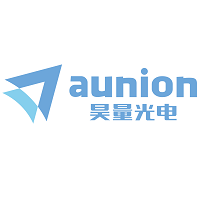
超聲波液位開關(guān)檢測液冷設(shè)備技術(shù)漏液情況
晶科能源入選世界經(jīng)濟(jì)論壇可再生能源價(jià)值鏈領(lǐng)先實(shí)踐案例
光刻膠旋轉(zhuǎn)涂膠的原因
如何利用家庭用具制備石墨烯懸浮液
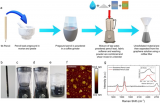
固態(tài)繼電器:推進(jìn)可再生能源系統(tǒng)
輕松get電路板pcb電鍍液技巧,助你制作出色電路板
天奇股份與長安成立合資公司,開展電池回收業(yè)務(wù)
堿性電解系統(tǒng)對(duì)可再生能源消納優(yōu)化策略
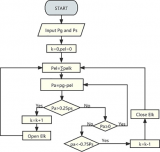
評(píng)論