漏印板印刷技術(shù)的最小間距,目前限制在150~200μm范圍之內(nèi)。對(duì)有超細(xì)間距和較寬的凸點(diǎn)尺寸范圍的增加的互連密度而言,電鍍技術(shù)是最受歡迎的。應(yīng)用于此電鍍技術(shù)工藝的間距可小到40μm。對(duì)高I/O和高功率芯片而言,各類半導(dǎo)體的國(guó)際半導(dǎo)體路線圖預(yù)測(cè),通常倒裝芯片技術(shù)使用的凸點(diǎn)間距從2002年的160μm減小到2010年的90μm和2016年的70μm。
電鍍技術(shù)工藝的凸點(diǎn)高度均勻度在±1μm范圍內(nèi)。這意味著從漏印板材料厚度和激光切割的精度方面的變化和從在漏印板開(kāi)口中殘存的主要的焊膏殘留物兩方面看,在smt貼片打樣或加工過(guò)程中,使用電鍍技術(shù)比使用漏印板印刷可達(dá)到更好的均勻性。這里典型的變化在±7μm范圍之內(nèi)。
根據(jù)諸如凸點(diǎn)高度均勻性失效標(biāo)準(zhǔn)的確定,電鍍技術(shù)的效率損失在10-6范圍之內(nèi)或者更少,這比通過(guò)漏印板印刷獲得的好得多。因此,當(dāng)效率損失使漏印板印刷對(duì)這些芯片無(wú)競(jìng)爭(zhēng)性時(shí),對(duì)高價(jià)值、大尺寸IC而言,電鍍技術(shù)也許是“低成本”技術(shù)。
電鍍技術(shù)的凸點(diǎn)下金屬化過(guò)程,是由在整個(gè)晶圓片表面上均勻地濺鍍Ti/W/Cu層和采用金屬板印刷術(shù)工藝過(guò)程來(lái)確定凸點(diǎn)焊盤構(gòu)成的。把額外的銅層進(jìn)行電鍍,在smt回流焊過(guò)程和形成金屬間化合物的熱應(yīng)力階段,通過(guò)焊料部分地完成電鍍。即從基于甲烷黃酸的溶液中用電化學(xué)方法把焊料金屬進(jìn)行淀積。因?yàn)殡婂児に嚨募庸r(shí)間依賴于凸點(diǎn)高度--與焊膏漏印板印刷工藝相反--電鍍工藝限制于較小的凸點(diǎn)高度剝?nèi)ル婂冄谀V?,用蝕刻工藝移去Ti/W/Cu凸點(diǎn)下金屬化(UBM)層。把在晶圓片上淀積的焊料進(jìn)行回流焊,以便形成球形的凸點(diǎn),接著進(jìn)行清洗步驟,以除去有機(jī)殘留物。
通過(guò)對(duì)幾種無(wú)鉛化焊料的應(yīng)用實(shí)施及深刻的研究,SnPb焊料較佳的替代品為SnAg3.5焊料。就眾焱電子小編的了解,此焊料具有某些特殊性能。由于高的標(biāo)準(zhǔn)電極潛在差異,銀比錫更易于淀積。因此需要針對(duì)銀離子的很強(qiáng)的形成洛合物劑的狀況,以防止其優(yōu)先沉淀。
根據(jù)SnPb雙相位圖顯示,焊料構(gòu)成方面的小偏差不會(huì)極大地影響熔點(diǎn)狀況。因而SnAg焊料的狀況則更具有關(guān)鍵性,甚至對(duì)低共晶焊料構(gòu)成加入少量的銀(3.5%),也會(huì)導(dǎo)致熔點(diǎn)方面極大的增加。再者,研究表明,對(duì)銀含量為4%的情況而言,大的電鍍形體的Ag3sn金屬間化合物的增長(zhǎng)較高,這對(duì)互連可靠性來(lái)說(shuō)是嚴(yán)重的問(wèn)題。就電鍍而言,需對(duì)用于低共晶SnAg3.5焊料電鍍的電鍍槽和合金組成進(jìn)行非常嚴(yán)格的控制。另一方而,當(dāng)凸點(diǎn)下金屬化過(guò)程的銅電鍍?cè)赟nAg焊料中部分溶解時(shí),已通過(guò)回流焊的凸點(diǎn)構(gòu)成了SnAgCu合金,并可受到回流溫度的影響。
與SnPb焊料相比,銅電鍍基底的消耗隨著SnAg焊料而增加。因此,不得不給電鍍銅提供合適的厚度。在smt貼裝工藝成本上,SnPb焊料和SnAg焊料之間不存在顯著的差異。
編輯:hfy
-
印刷技術(shù)
+關(guān)注
關(guān)注
0文章
16瀏覽量
9484 -
電鍍技術(shù)
+關(guān)注
關(guān)注
0文章
17瀏覽量
9232 -
SnPb
+關(guān)注
關(guān)注
0文章
4瀏覽量
6922
發(fā)布評(píng)論請(qǐng)先 登錄
相關(guān)推薦
PCB水平電鍍技術(shù)介紹
PCB水平電鍍技術(shù)介紹
【轉(zhuǎn)帖】一文讀懂BGA封裝技術(shù)的特點(diǎn)和工藝
高通MEMS封裝技術(shù)解析
封裝技術(shù)與加密技術(shù)的相關(guān)資料推薦
塑料電鍍技術(shù)
裝配、SMT相關(guān)術(shù)語(yǔ)解析
激光電鍍技術(shù)及其優(yōu)點(diǎn)
LED封裝技術(shù)簡(jiǎn)介與40種芯片的封裝技術(shù)解析
水平電鍍技術(shù)的原理及存在的優(yōu)勢(shì)介紹
簡(jiǎn)述產(chǎn)品裝配技術(shù)的發(fā)展、關(guān)鍵技術(shù)和未來(lái)趨勢(shì)
RFID技術(shù)在電鍍行業(yè)應(yīng)用的深遠(yuǎn)意義
pcb水平電鍍技術(shù)有何作用?
一文解析微系統(tǒng)封裝原理與技術(shù)
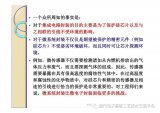
評(píng)論